Strategize for Service Excellence in Heavy Equipment
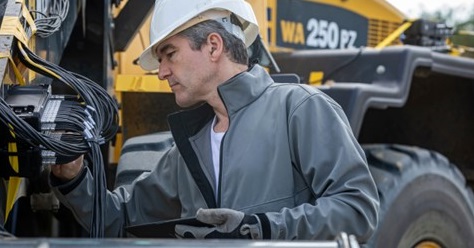
Learn how you can drive service excellence in heavy equipment with IBM Maximo and Siemens Teamcenter for end-to-end service lifecycle management.
To take service excellence to the next level, you may ask yourself:
- Do I have a solid strategy in place to support my heavy equipment service business?
- Do I have control over fielded heavy equipment with access to the current configuration data?
- Are my technicians equipped with the right information to ensure optimal heavy equipment performance and sustainability?
Effective service lifecycle management solutions should leverage product lifecycle management (PLM) capabilities to support integrated service BOM, service planning and forecasting, visually rich service instructions and management of serialized assets. It should also support an open ecosystem of connected systems that can work together to deliver quality service.
Siemens and IBM have partnered to deliver an end-to-end service lifecycle management solution. Learn about the value of integrated IBM Maximo Application Suite and Teamcenter for service by registering for this upcoming webinar Driving service excellence in heavy equipment, May 22, 2024 at 11:00 AM EDT

In this webinar, you’ll hear from Siemens Teamcenter product manager Brian Johnsen and IBM worldwide business advisor Tom Woginrich on how to improve service in the heavy equipment industry with a focus on connected enterprise asset management (EAM) and product lifecycle management (PLM). You’ll learn how you can track maintenance details from your factory and fielded equipment through Teamcenter integration with IBM Maximo Application Suite for Enterprise Asset Management (EAM). This closed-loop integration between service engineering and service execution domains will provide visibility of heavy equipment configurations and product data to service technicians, and feed service activity data captured in Maximo back to Teamcenter to improve future service. This helps you lower maintenance costs, reduce risks, and improve asset resiliency.
What are the benefits of end-to-end Service Lifecycle Management?
By orchestrating service engineering operations throughout a product’s lifecycle, service lifecycle management software generates greater maintenance compliance, faster service, and lower costs for manufacturers, owner operators, and customers alike. You can improve communication between service and engineering teams for better serviceability and reliability. You can effectively coordinate and plan for operational activities with real-time visibility to service events. Service activities can be performed with a full understanding of physical equipment configurations, including equipment BOM records, status, and service history.
Teamcenter Service Lifecycle Management helps you optimize equipment performance
Teamcenter Service Lifecycle Management helps you maximize your service knowledge and asset value with one source of service engineering information. Your service planners have access to the right service requirements to ensure the right service resources are assigned to the job. Your service technicians can perform service activities with a full understanding of factory or fielded equipment configurations, including as-built bill of materials records, status, and service history. They can leverage visually rich service instructions to get the job done right the first time, reducing equipment downtime.
More Service Lifecycle Management resources:
Watch this video to hear more about the Siemens and IBM partnership
View more information about Siemens and IBM together
Listen to the podcast on the Importance of Service Lifecycle Management