Siemens and IBM solutions deliver comprehensive service lifecycle management
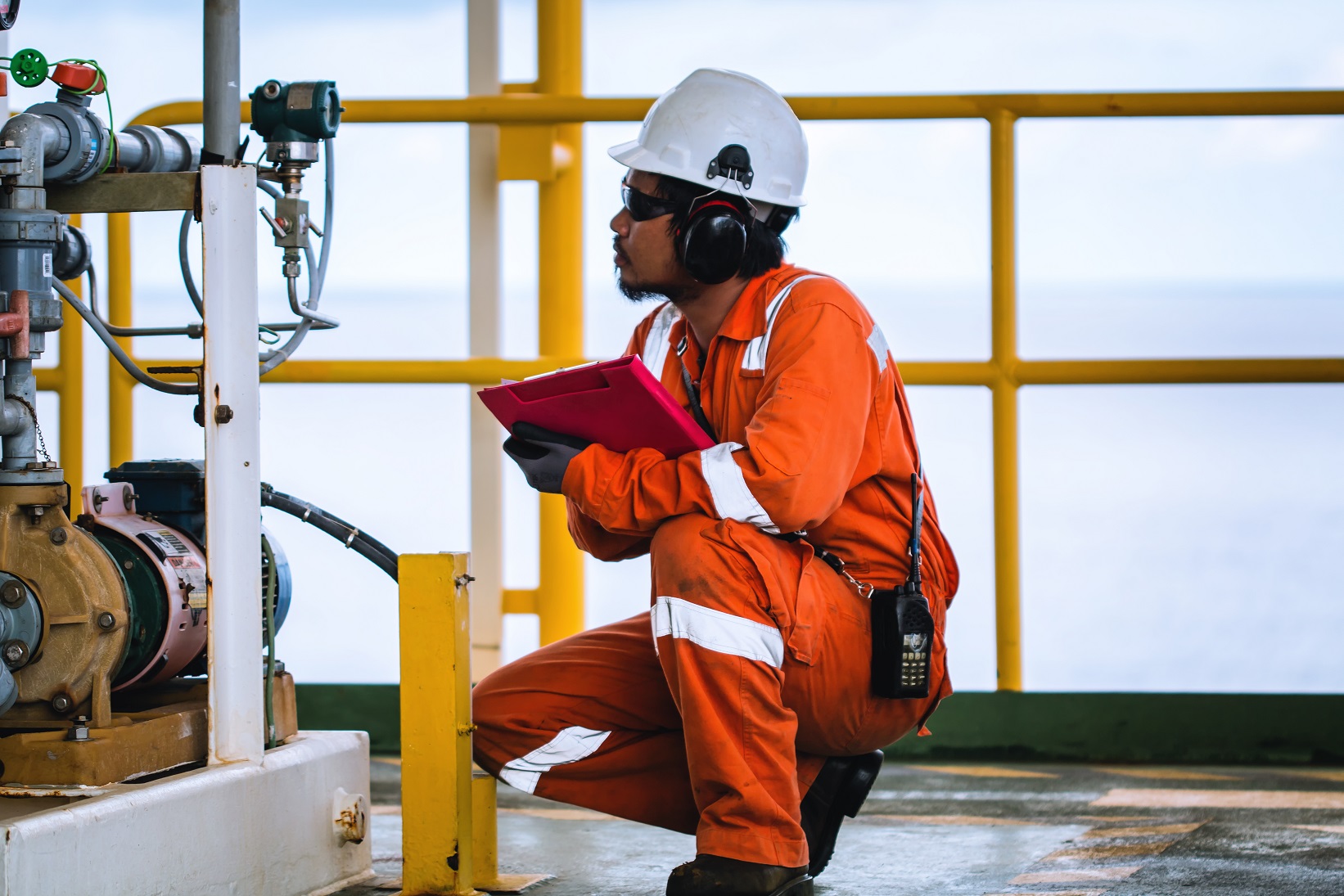
Maintain and optimize the complete product service lifecycle with Siemens and IBM solutions.
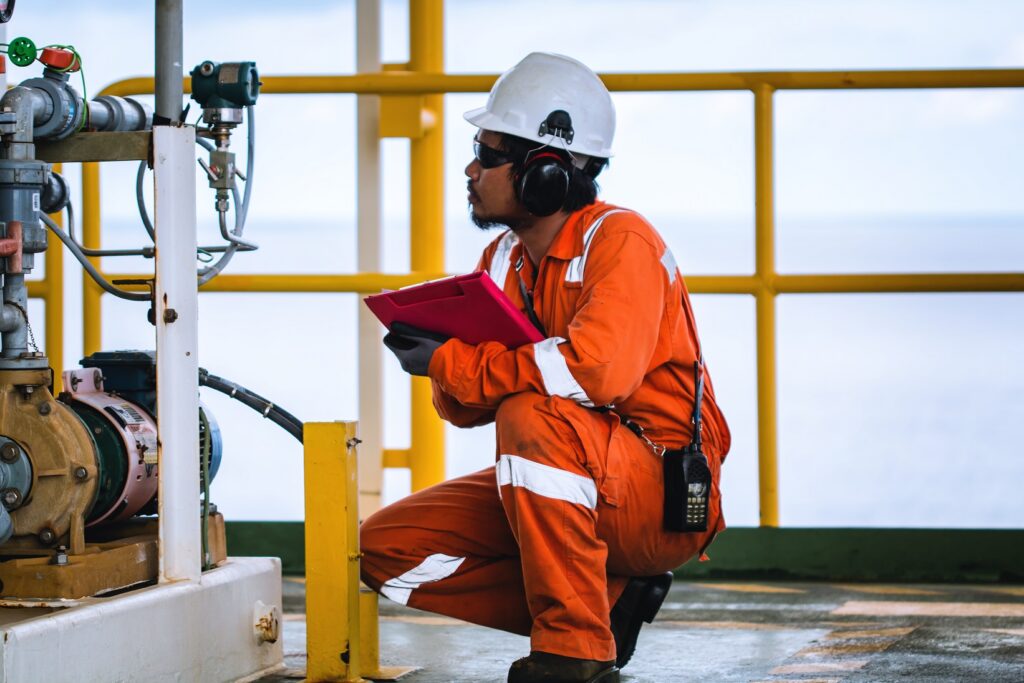
Struggling to efficiently reconcile your latest product design requirements with ongoing configuration changes of your fielded assets? Are you looking to close the gap between design, product service and aftermarket / product support? To achieve the best possible outcomes, it’s critical to maintain an accurate representation of both the product digital twin, and its physical counterpart – the physical asset in its current configuration. By implementing a comprehensive digital twin strategy that extends to service, you can save time and money with operational efficiencies, increase innovation with design for serviceability, and open new paths for aftermarket revenue opportunities.
Integrated service lifecycle management and enterprise asset management
Industry leading solutions from the Siemens Xcelerator portfolio and the IBM Maximo Application Suite have come together for a best-in-class offering of service lifecycle management (SLM) that delivers powerful results. Teamcenter SLM connected to Maximo’s enterprise asset management (EAM) helps manufacturers and owner/operators efficiently manage physical assets and maintain them throughout their service life. The Teamcenter SLM and Maximo digital thread bridges together design and service engineering, planning, and maintenance to close the service loop. This can help reduce maintenance costs and production downtime, and deliver many more benefits for OEMs and owner/operators across industries. For example, design engineers in Teamcenter can analyze failure data provided by Maximo, to more efficiently implement engineering changes. Service technicians using Maximo, can leverage from Teamcenter, accurate asset configuration information, service requirements, and intuitive service instructions with 3D visuals and recordings to guide technicians with step by step instructions for their assigned work. The integrated solutions can help increase customer satisfaction and production output, and even extend the lifecycle of an asset to support sustainability initiatives. And regarding sustainability, with visibility to current asset configurations in the field, asset upgrades will be easier to execute, which can maximize asset efficiencies. For example, an outdated compressor can be replaced with a more efficient version.
Learn more about the Siemens and IBM partnership
Closed loop asset maintenance
To achieve a closed loop asset maintenance process, service engineering should be connected via a digital thread with design, configuration, service planning, and maintenance. This is possible using Teamcenter and Maximo integrated solutions, where the data (asset and maintenance information) flows from Teamcenter to Maximo, and back from Maximo to Teamcenter.
The Service BOM (SBOM), managed in Teamcenter, contains the design of the product with serviceability information such as, whether a design in the SBOM is a lot, or whether it’s serialized, etc. The Service Plan, also managed in Teamcenter, details the steps for servicing the components from the SBOM. The Service Plan has three main components which are Service Requirements, Work Cards, and Activities. Each Service Requirement represents the maintenance that needs to be performed on the asset. This Service Plan definition is used by Maximo to create Work Orders.
The video below shows the Service Plan from Teamcenter service lifecycle management viewed in Maximo, along with 3D service work instructions authored in Teamcenter.
To import the SBOM structure of the asset, Maximo queries Teamcenter using a tracking number such as an Item ID, Serial Number, or Part Number of the Physical Part (Fielded Asset). Once the import is triggered, the entire configured SBOM present in Teamcenter is used to create an equivalent asset hierarchy in Maximo. This results in the mapping of Teamcenter Parts to Maximo Assets or Items. Note – this is the current physical asset configuration that is managed and tracked in Teamcenter and shared with Maximo, ensuring better traceability and less room for service errors.
Work Orders in Maximo are created using the Job Plans imported from Teamcenter. The Work Orders are then assigned to the technicians and are executed based on the requirement and schedule.
Teamcenter users have visibility into the history of all the Work Orders executed on a specific Asset from Maximo. Work Order information includes values such as Action Start and End date, Problem Code (Fault Code), Named Technician, observations recorded by Technician, etc. This information can then be fed back to design engineers for continuous product serviceability improvements.
Watch the webinar to learn more about the benefits of a complete service lifecycle and the integration between Siemens Teamcenter service lifecycle management and IBM Maximo.
More Service Lifecycle Management Learning Opportunities
Explore Service Lifecycle Management at your own pace with a free, 30-day software trial
Catch the virtual seminar series
Read the CIMdata Commentary on service lifecycle management
Listen to the podcast on the Importance of Service Lifecycle Management
About the author: Torsten Beste currently works as the Global VP of Service & Asset Lifecycle Management for Siemens Digital Industries Software and has been with Siemens for over 20 years. He currently focuses on providing value to customers through a digital thread for service and asset maintenance.