Reduce Downtime through Accurate Service Planning
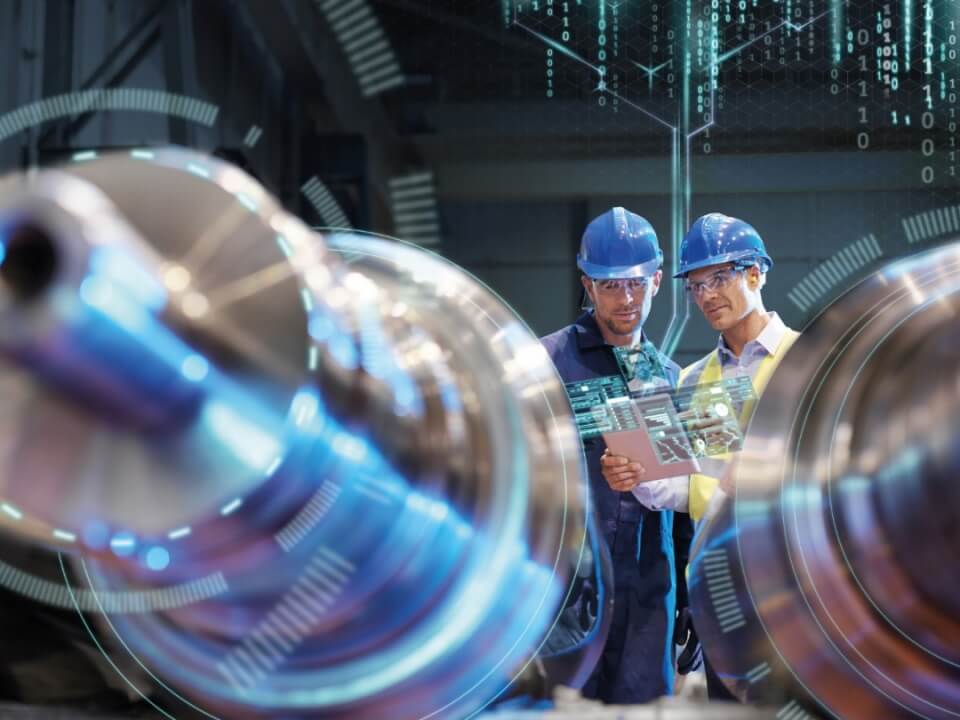
This is the third in a seven-part series where we will discuss our integrated Service Lifecycle Management (SLM) capabilities and the potential benefits that can be realized.
If you missed the previous parts, please find them here:
Part 1: Digitalization Strategies for Service Lifecycle Management (SLM)
Part 2: Improve Serviceability with Integrated Service BOM Management
When you think about a future strategy for your service operations it’s likely that the first thing to come to mind is IoT, connected devices, and predictive maintenance. But have you put the same thought into how to improve and optimize the actual serviceability of your products? In recent years we have seen a lot of focus across industries on how to improve the manufacturability of products, how to evaluate and plan manufacturing earlier in the lifecycle to eliminate issues and shorten product launches. However, there seems to be limited focus in applying similar improvement concepts for servicing the products, to enable earlier service planning and validation. So, while a predictive maintenance strategy may help you identify problems more efficiently, have you considered the following…
- Are your products optimized for service with early input from the required stakeholders?
- Are you able to quickly evaluate the overall service needs for a specific product?
- Do you have a clear understanding of the tasks and resources required to complete a defined scope of service?
- Can you quickly understand the service impact of specific customer configurations or regional spare part differences?
- Are you able to optimize the downtime of your assets with knowledge of related service requirements?
This is not to say that connected assets with a predictive strategy is not important, but we believe it’s only one part of a comprehensive Service Lifecycle Management (SLM) strategy. Also, as the complexity of your products increases, optimizing the serviceability of your products and efficiently managing changes will only become more critical.
What we typically see is that the details of what needs to be done to maintain a physical product is often captured in disconnected documents such as service manuals or repair procedures. Many times, this is based on generalized information and does not necessarily represent the requirements of a specific physical asset. Or worse, it relies on the expertise of specific technicians and knowledge gained over many years of experience. These scenarios can cause delays and errors from incorrect interpretations or lack of experience by the technician.
Additionally, while many manufacturers have made efforts to improve the collaboration between engineering and manufacturing, service continues to be left as a silo with limited collaboration or data continuity. These disconnects limit the visibility across your enterprise which creates data redundancies and quality escapes, preventing collaboration, data sharing, and reuse across your organization.
With service planning, you will manage all the service requirements for your products within a fully integrated solution. You will be able to evaluate service tasks collaboratively with your design engineers, allowing for earlier feedback that will improve the overall serviceability of your products. You will have the ability to define and manage your service requirements with direct access to all available product data, like 3D models, drawings, and specification documents. This approach also provides clear visibility across all stakeholders to fully understand impacted service requirements, allowing for the full scope of potential changes to be quickly evaluated as your products evolve. Service planning enables…
- Service requirements linked directly to associated parts and assemblies for clear traceability
- Dependencies between service requirements to ensure accountability of all requirements
- Detailed tasks with required resources, certifications, and parts to accurately evaluate full scope
- Linked fault codes and characteristics to ensure visibility to critical service details
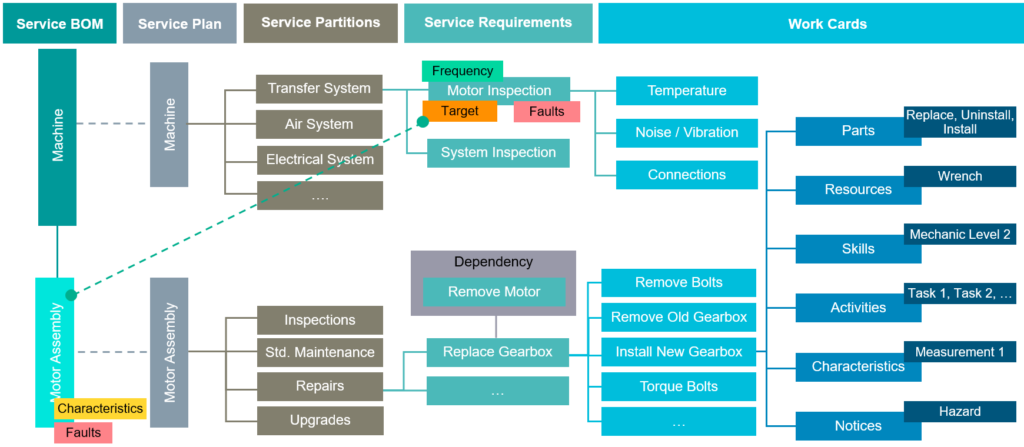
By leveraging this integrated approach to service planning you will significantly reduce the risk of identifying costly design issues too late in the product development cycle. You will also improve the overall traceability, visibility and reuse of all available data. By leveraging a model based and data centric approach to service planning you will be able to…
- Reduce turn-around times by having clear visibility to service requirements of specific assets
- Increase quality and compliance with service requirements integrated into you change process
- Ensure accuracy of information provided to the field through data driven service documentation
Look for part four in the series coming soon where we will discuss the benefits of managing integrated service documentation, enabling technical publications derived directly from managed data already defined in the Service BOMs and Service Plans.
Visit our Service Lifecycle Management web page to learn more