Improve Service Efficiency with Accurate Visibility of Your Physical Asset Configuration
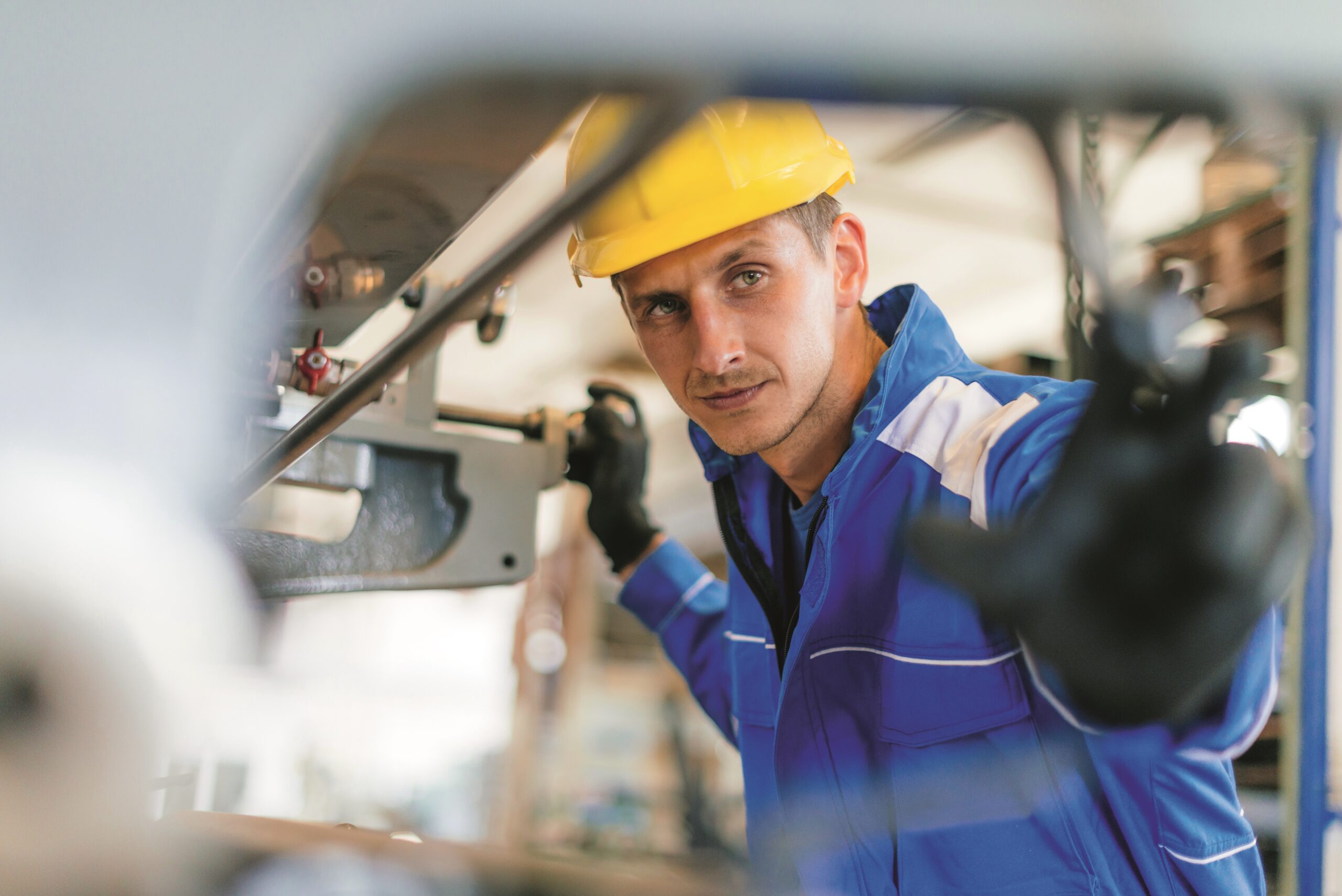
Challenges with service efficiency for physical asset configurations
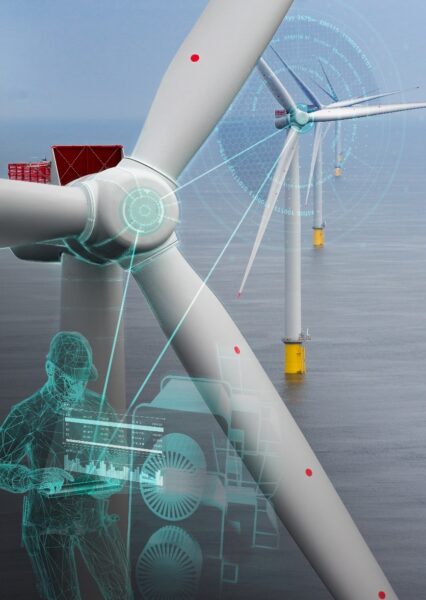
Regardless of the industry you’re in, if you are a service operator, it is likely that one of your main challenges is to obtain up-to-date visibility of your serviced physical asset configuration.
Lack of such visibility could result in repeated technician visits due to a missing working tool, technician skill, or spare part. Furthermore, this could also result in technicians not using accurate service work instructions, matching diagrams, 3D visualization, and other handy engineering data, all leading to quality and compliance issues. On an even larger scale, accurate proactive maintenance, upgrade offerings, and spare parts inventory optimization can also be impacted negatively. In other words, many service inefficiencies are a direct result of this gap in physical asset configuration visibility.
Many service operators, whether OEMs or 3rd parties, struggle to achieve a viable solution for capturing these on-going configuration changes in order to retain accurate visibility of their assets’ latest configuration. Some operators leverage their Service Operations system to capture these asset changes, however, this resolves only the visibility aspect, while there is still a disconnect with OEM design data. This partial solution can result in the inability to provide service technicians live up-to-date data specific to how the asset is configured at the time of their service activity.
Interested in learning more about Service Lifecycle Management and how it can help you reduce risks?
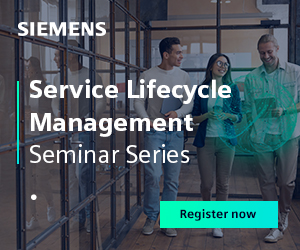
For a complete list of Service Lifecycle Management virtual seminars and dates, go here.
Look for software solutions that support physical structures that allow service providers to digitally represent each one of their physical assets.
The Service BOM (sBOM) is the neutral representation of the product with a defined set of OEM service related definitions. As part of the sBOM, you can define which parts should be serialized, which should be part of a lot, what usage characteristics should be documented during service, etc.
Complete tasks right the first time, and improve asset uptime
The physical BOM represents a specific instance of an asset. Using the right software solution, it can be tightly coupled with the sBOM, leading to accurate visibility of the physical asset configuration throughout its life. This robust link between the sBOM and physical BOM is a key enabler for providing service technicians live, up-to-date, contextualized design data such as design requirements, validated configurations, service requirements, change history, design specifications, and more.
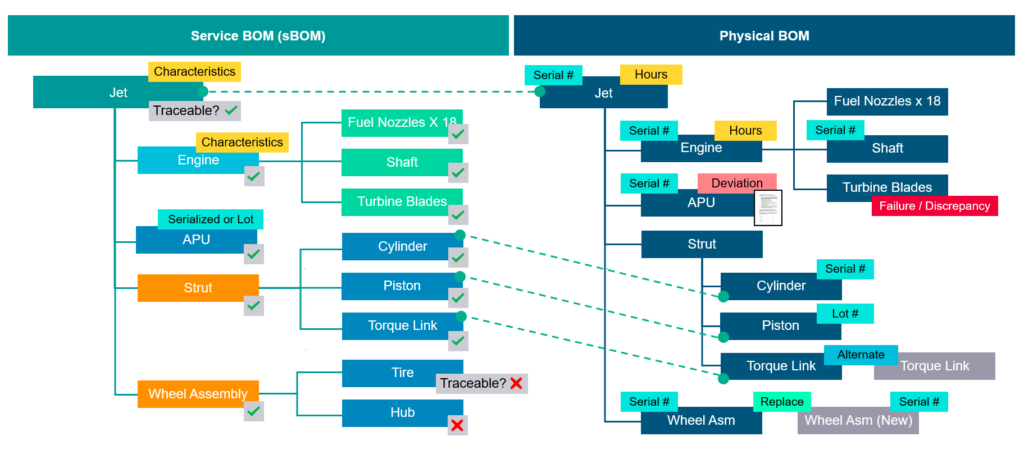
In the case of a design change, upgrade, or a recall, the service provider could get an immediate notification on the set of impacted physical assets in their operated fleet.
Along with the link to design via the sBOM, physical structures are getting a consistent feed of information from the physical assets with maintenance details, failures, asset utilization, and deviations. This helps to ensure that maintenance job details, such as part movement for example, are being recorded. Technicians going into future service calls will then have full visibility of the most updated configuration of the asset. They will have complete knowledge about the required tools to service the asset, and the necessary resources and skills needed to complete the task right the first time, leading to an improved asset uptime.
Meet compliance requirements and avoid human error
Service operators in industries like Energy and Utilities and Aerospace and Defense are required to comply with strict compliance regulations. By leveraging the right physical structures implementation, data collections as well as measurements are recorded and saved in the context of the physical asset’s configuration. As a service provider, this helps you ensure compliance against regulations, and can also act as your checklist to avoid technician human error. The physical structures are tracked with these historical records, making sure that all compliance requirements are met. This is especially important today due to the growing trend of longer asset lifespans. This information could be critical in case of failure investigations and prevention of human error in maintenance and inspection. A good example of this is noted in the International Journal of Industrial Ergonomics where a failure to replace horizontal stabilizer screws on a Continental Express aircraft resulted in catastrophic errors.
Optimize design, reliability, and serviceability
With the connection to physical structures from the sBOM, design teams benefit from improved visibility to customer specific asset configurations. And, as the lifetime of customer assets become increasingly longer, these insights can help OEMs to optimize their design, reliability, and serviceability of their assets during and even prior to product design. They can drive continuous design improvements, and open a new revenue stream from product upgrades.
To summarize, digital representation of physical assets with connectivity to design and data feeds from the actual assets is a key enabler for implementing a truly comprehensive digital twin that considers the individual assets in production. It addresses an existing gap between design and operations, generates significant values on both sides, but even more importantly it is a fundamental tool for OEMs and service providers to use, for ensuring service quality and efficiency, and improving their profitability.
Register for the Service Lifecycle Management Virtual Seminar Series to learn more.
This is the fifth in a seven-part series where we will discuss our integrated Service Lifecycle Management (SLM) capabilities and the potential benefits that can be realized.
If you missed the previous parts, please find them here:
Part 1: Digitalization Strategies for Service Lifecycle Management (SLM)
Part 2: Improve Serviceability with integrated Service BOM Management
Part 3: Reduce Downtime through Accurate Service Planning
Part 4: Leveraging Service Data to Drive Technical Documentation
Learn more about Teamcenter Service Lifecycle Management (SLM) and how it can help you improve service efficiency.