Digital Threads in Semiconductor Engineering
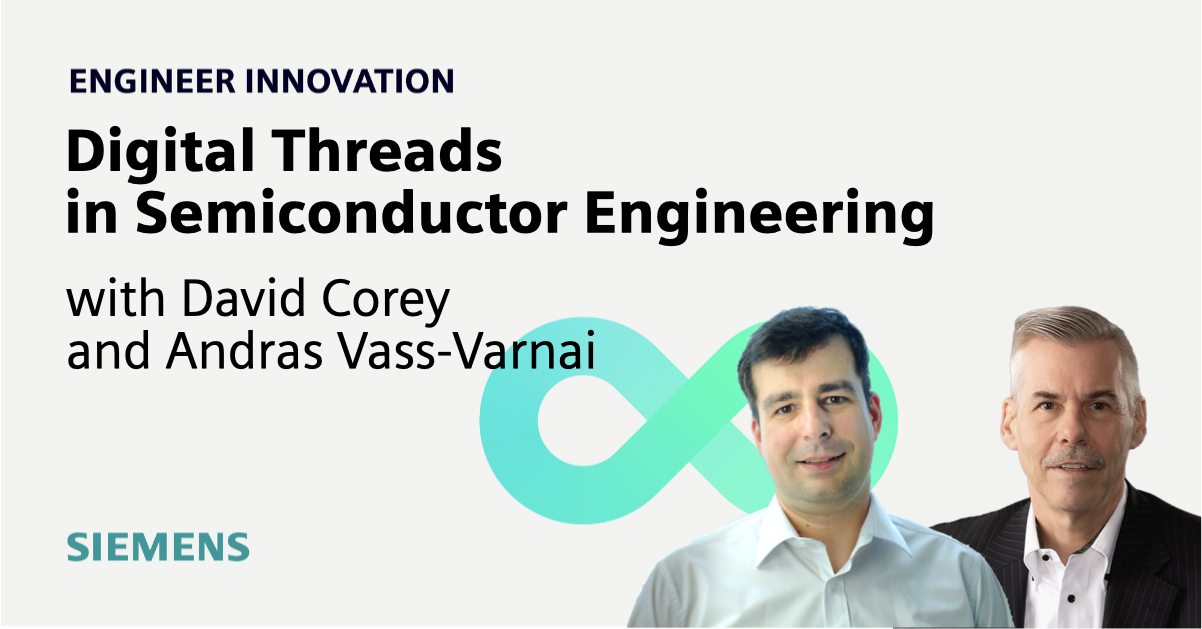
Guests David Corey and Andras Vass-Varnai
Listen on Apple
Listen on Spotify
Show Notes
In this episode of the Engineer Innovation Podcast, host Stephen Ferguson is joined by two experts from Siemens—David Corey, VP of Semiconductor Industry Sales, and Dr. Andras Vass-Varnai, Business Development Leader—to explore the latest trends and challenges in semiconductor technology.
Our conversation covers the economic limits of Moore’s Law, the increasing complexity of semiconductor packages, and the critical role of digital threads in streamlining design and manufacturing processes. David and Andres break down how digital threads connect data across all stages of product development, helping companies manage the growing complexity of semiconductor design and production. The episode also delves into how simulation and automation are revolutionizing the industry, and the hard lessons learned from COVID’s impact on global supply chains.
Whether you’re curious about the future of your smartphone’s chips or deeply involved in the semiconductor industry, this episode offers valuable insights into the innovations that are driving the future of electronics.
Key Topics Discussed:
- Moore’s Law and its economic limits in the semiconductor industry
- The rise of advanced semiconductor packaging and heterogeneous integration
- What digital threads are and how they connect every stage of semiconductor development
- The importance of data management and simulation in reducing time-to-market
- Lessons from COVID: How global supply chains adapted and what’s changing moving forward
- Real-world applications of digital threads in semiconductor manufacturing
Notable Quotes:
- “Digital threads are not just buzzwords; they’re the backbone of how companies are managing complexity and driving innovation.”
- “The semiconductor industry might be hitting the limits of Moore’s Law economically, but innovation is just getting started.”
Resources & Links:
- Learn more about Siemens’ work in the semiconductor industry: Siemens Digital Industries
- Follow David on LinkedIn: https://www.linkedin.com/in/david-corey-siemens/
- Follow Andras on LinkedIn: https://www.linkedin.com/in/andras-vass-varnai/
- More about digital threads in manufacturing: https://blogs.sw.siemens.com/simcenter/digitalizing-the-semiconductor-industry/
Episode Highlights:
- [02:30] David Corey discusses the economic realities facing the semiconductor industry and the shifting focus on packaging.
- [10:45] Dr. Andres Vasvane explains how digital threads streamline product development and the impact of simulation.
- [18:00] The importance of a flexible supply chain and how companies are using digital threads to move data more efficiently.
Tune In:Subscribe to Engineer Innovation Podcast on Spotify, Apple Podcasts, or wherever you download your podcasts to stay up-to-date with the latest in engineering and technology.
Guest biographies and episode transcript
- Moore’s Law and its economic limits in the semiconductor industry
- The rise of advanced semiconductor packaging and heterogeneous integration
- What digital threads are and how they connect every stage of semiconductor development
- The importance of data management and simulation in reducing time-to-market
- Lessons from COVID: How global supply chains adapted and what’s changing moving forward
- Real-world applications of digital threads in semiconductor manufacturing
Stephen Ferguson:
Hello. Today we’re talking about a revolution in semiconductor development with digital thread engineering. I’m joined by David Corey, who is a semiconductor industry executive at Siemens, and VP of semiconductor industry sales, and Dr. Andras Vass-Varnai, who works in business development. So, starting with you, David, can you tell us a bit about your expertise, and your current role at Siemens?
David Corey:
Sure. I’ve been in the semiconductor industry for more than 30 years. Over the course of that time, my primarily responsibility has been to work with customers to solve complex problems around the manufacturing domain, and specifically wait for fabrication, and advanced assembly, and test processes. It’s been a great 30 years, and I look forward to speaking with you today.
Stephen Ferguson:
Thank you. And Andras, can you tell me a bit more about your role, and how you’re involved in promoting engineering innovation in the semiconductor industry?
Dr. Andras Vass-Varnai:
Sure, Stephen, and hello everybody. Similarly to David, I’ve been in the semiconductor industry for quite a long time, although in my case it’s been a little bit more than 15 years. My background is semiconductor device physics, but most of my time I’ve been working in semiconductor packaging, and semiconductor thermal management. I work with customers across the board helping them design better semiconductor packages, and advise the tools which they need to complement their designs.
Stephen Ferguson:
So, David, obviously the semiconductor industry has been in a state of flux over the past few years. Can you identify some global trends in the industry, and tell us about some of the challenges that companies in this industry are facing?
David Corey:
Yeah, I think there’s two, or three significant trends. I think the first trend is the device itself, right? In the past we always had the idea of Moore’s Law about how the semiconductors would shrink in size, and have additional transistors as more manufacturing advancements came out. And I think the rule was like every 18 months there would be a significant increase, but we’ve kind of hit that limit economically, maybe not from a process technology standpoint, but economically. When I started in this business, we were making 200 millimeter wafers, or even 150 millimeter wafers, and those fabrication facilities cost about two billion to four billion dollars to build, and it would take two to four years to bring those online. Today, I was with some customers this week, and they’re talking about a new 300 millimeter facility that would be maybe three nanometer technology. And those costs are north of 20 billion, approaching $28 billion depending on the type of technology.
So, if you think about it, how many companies can really afford that level of capital to build advanced process technologies? And so what I see is that the market is segregating itself by financial ability, let’s say. If we take somebody like Global Foundries where they’ve said, “Okay, 14 nanometer is our technology platform, and we’re not going to chase 10 nanometer, or seven nanometer, or whatever”, okay? They’re carving out the market niche of where they’re going to be. And then there’s other companies like Tower Semiconductor that are pretty much analog device fabrication facilities, and they’re quarter micron type things. But what you find is that depending on the product type, not every product needs to be three nanometers. So, if I’m an automotive company, and I make a window lift control loader for the car, I don’t need two nanometers. They resist any improvement to that window lift motor unless it’s absolutely necessary, because of all the qualifications that they need to go to enable a change in the car, you need to keep records for the life of the chip in case of recall, in case of all the traceability.
And the average life of a car is 15 to 20 years. So, whenever they make a change requalification of all these devices, then the traceability, and the maintenance of those records for so long. So, I’d say that’s the first trend is that people are picking the types of products that they’re going to manufacture, and financially, they’re going to stick to their lane because there’s always going to be product needs in that domain. The second big trend that I see is around manufacturing improvements. When I say manufacturing improvements, what do I really mean? It means that if assembly, and test packaging used to be I have one device, and I’m putting it into a lead frame, and I’m taking that lead frame, and then I’m wiring, I’m dye bonding it, wire bonding it, and I’m making a device. And the difference now is because of the inability to advance some chips further, I’m now making packages consisting of 10 devices, 15 devices.
In some cases, we have customers that have 47 devices in their package. So, this is a whole new level of complexity, and I’m seeing the shift of focus in the manufacturing domain now to advance assembly, and test techniques. To be able to, first of all, if I have 47 dye in one package, then as they’ve been out at different capabilities, how do I make the desired product I really want to make? I’m on the manufacturing floor. I’m sitting there with maybe that’s consisting of five, eight, 10 different types, who knows? But if I need the right bins, the right performance of every one of those chips to make the highest level product, and if I don’t have the highest level bins of those sub-components, then what level of product can I really make? And so there’s all these rules around how I could make the best possible package out of the raw materials that I currently have available.
And it is bomb explosion, right? And the semiconductor industry is not used to bomb explosion. So, that drives to the third trend. And the third trend really is if I have all these manufacturing complexities, where does the master data come from? In the past, no company’s really been successful in semiconductor domain with product lifecycle management. And the reason why is because product lifecycle management systems were invented for automotive, and for aerospace. So, wheels, and wings. It’s where I would start with 40,000 parts, and I would end up with an airplane. But semiconductor works exactly the opposite. I start out with a wafer, and from that wafer, I’m going to create a number of different products off that same wafer depending on the quality of each one of the individual die on that wafer. So, I can’t necessarily predict with great accuracy what product I’m going to come out with at the very end, because there’s a thousand process steps, say in the wafer manufacturing piece, and maybe there’s another 100, 150 in the assembly of test domain, and throughout that I’m going to have loss, or different performance levels.
Dye at the edge, are going to perform differently than dye in the center of the wafer, and so on. So, I have all these variables I’m trying to manage. So, now I need a way to control my master data. And we at Siemens actually have invented a system specifically for semiconductors to do that. And it’s gaining quick market acceptance. And I see that as the biggest trend that’s coming down the pipe is moving upstream in the data model, having a data model that encompasses all of this, and the ability to distribute that master data out to the individual sites. Today, master data is contained at the individual site where it’s manufactured, and that’s now moving upstream, and being centralized, so these companies can manufacture any product in any factory. So, three big trends. The last one, I think, being the biggest when it comes to managing master data, and having the ability to distribute it out to the field, and manufacture anywhere. So, I have a flexible supply chain.
Stephen Ferguson:
So, we’re going to talk a bit more about managing that data a bit later on. But before we move on, Andras, what do you say the biggest trends, and challenges facing the industry right now?
Dr. Andras Vass-Varnai:
This is a great question, and I agree with David when he talked a little bit about Moore’s Law, but I like to think about Moore’s Law from a customer’s perspective, a consumer’s perspective. So, if you look at the last decade, as consumers, I think we’ve been spoiled, because it doesn’t really matter for a consumer whether the number of transistors double every two years. But what really matters for us as consumers is that our compute power is increasing sharply, even doubling every two years with a number of those transistors. And from an economical perspective, we are actually used to getting our new phones, or tablets, or PCs pretty much at the same time every two to three years when we change them. So, the technology limitations David mentioned earlier actually are disrupting that. And the only way forward to keep consumers happy, and keep the increasing compute power in my opinion, is packaging.
So, David mentioned integrating a large number of dyes in a single package. This is one of the most economically viable ways to keep on adding more compute power at a reasonably acceptable price to the consumers as well. Now, this obviously goes beyond consumer, so you’ve seen all the big changes recently when it comes to machine learning, and artificial intelligence, and it’s disrupting, the industry disrupts our everyday lives, and these new technologies are also built on the same availability of compute power. But what’s really interesting about it is when you think about the design of these packages, I’m talking about digital semiconductor devices, the complexity of the design itself is kind of getting, when it comes to simply putting a large number of cheap lats, or tiles into a semiconductor package, if you look at it from a physics perspective, and nowadays more, and more, even as consumers, we face these challenges.
You’re looking at thermal problems, there is a very strong power density built into these packages, potentially affecting reliability. You might need to understand how these different dyes would interact with one another electrically, thermally, maybe from a structural perspective. So, as a company going down this route of heterogeneous integration, you need to consider physics-based simulations in your design process more than ever before. So, I see that as a major trend, and I see many of our customers embarking this journey together with Siemens.
Stephen Ferguson:
And I’m going to query you a bit more about that in a second. But from a consumer point of view, I was just complaining to my boss that my laptop is four years old, and so I needed a new one, which goes to show just how entitled we are these days that a four-year-old piece of electronics is absolutely defunct, isn’t it? So, that’s how fast things are moving. And probably I should have asked him two years…
Stephen Ferguson:
… really defunct, isn’t it, so that’s how fast things are moving, and probably I should have asked him two years ago if was to keep up with the trends. So, I think you’ve already answered this partially David, but are the challenges the same for high speed electronics as they are for other industry applications?
David Corey:
Can you define high speed electronics?
Dr. Andras Vass-Varnai:
Yeah. Yeah, I think what Stephen means by high speed electronics is really high compute power, at least in my opinion. And talking about speed though, obviously when it comes to compute power, it has to do a lot with cloud frequencies and being able to simply move that vast amount of data needed for the computations. For personal computing reasons, this may not be a big issue, but if you look at global trends, we didn’t speak about IoT today, which is actually one of the diverse of machine learning and artificial intelligence. It’s basically data and that data can come from devices, from even analog sources. I think the global library has been digitalized and being used to train AI models. So moving that data is becoming essentially important. In order to be able to process all that data, you need faster data communication, ways that optical data communication is also becoming a very strong area of research nowadays.
In fact, some of these heterogeneous packages start to have literally optical interfaces instead of copper interfaces on a printed circuit board, so I think that’s one area. But David, you mentioned earlier, the automotive industry and automotive electronics. I think that’s really a whole different market. And I like to call this our semiconductor domain where, even though the technology nodes are not as advanced, that there is still a lot of research going into this area. So there, I think the big change, the big trend is, instead of using silicon, the use of compound semiconductor devices such as silicon carbide, gallium nitride, type of technologies. Even we’ve seen some experiments with gallium oxide, which I don’t think is already in the public domain, but might be materials for the future.
In this domain, what becomes really important is efficiency. So as you switch high power with really tiny semiconductor components, you need to make sure that that switching is efficient. Also, that there are switches work in a reliable way because very often these are the drivers of the traction systems and the braking systems, the steering systems in our vehicles. So the need for reliability is actually as important as in any other parts of the automotive or aerospace manufacturing, which is, I think, a very new area for the folks in the semiconductor space.
Stephen Ferguson:
So on the topic of reliability and data, David, looking through some of your blogs, you talk a lot about digital threads. Could you tell us what they are and what they mean to you?
David Corey:
Sure. A digital thread is a collection of products or services that accomplish a specific, some task in the overall enterprise. So if I think about a digital thread, let’s take for example, like Andras is talking about here about package design. The digital thread would include first of all the master data about the requirements of the product and the verification or validation of how the product would meet its original requirements.
But within that thread, I need to use a product like Substrate Integrator that is going to allow me to do the floor planning or a rough design of that package. I need another product to actually individual design every device that goes within the package. I need a way to do the mechanical design to make sure that it fits in the actual device that the package is going to fit into. I need to do the thermal stress analysis to make sure that it doesn’t heat. Andras talked about chips or chiplets that are next to each other, the influence of one heat or thermal effect of one chip having on another chip or on the interfaces. There’s mechanical simulation that goes on to make sure that there’s no solder ball cracking or stress or whatever, the vibration. And then finally, the ability to then tape that out and make that actual device, so that is one thread of the entire enterprise. It’s thread for IC design, a thread for package design, potentially another thread for PC board design, a thread for manufacturing.
So if I focus on a thread, because companies always ask me, “Where do I start? I want a digital enterprise.” I hear this every day from executives. “We have a huge digitalization project going out,” but digitalization means something different to everybody. So if you break it… And then they get overwhelmed on where to start and how to be successful, there’s lots of studies by Deloitte, McKinsey, Accenture about how all these projects fail.
In the learning I’ve taken from them and the customers that I’m working with, focus on a thread, be successful in your thread. Go to the thread that gives you the highest value to start, easy wins, and then move on to the other threads. So you’re really focused and not just moving all over, you’re focused on having a one thread that you can be successful on. So that’s the easiest way to summarize what a thread actually is.
Stephen Ferguson:
So one thread at a time basically is what you’re suggesting.
David Corey:
Well, sometimes you don’t have time to do only one at a time. What I find is that there’s different resources required for each thread, right? So if I’m doing the smart manufacturing thread, there’s very few, if any of those people, that are involved in the package design thread. So they’re two totally separate threads that get connected when it comes to the manufacturing engineering piece. So it comes down to focus.
Most of these companies work with McKinsey or Deloitte, they figure out where they’re going to get the most value. They start there. But ultimately digitalization, you need to get to the point where automation or the ability to reduce your new product introduction cycle. Because in semiconductor, that’s what it’s really about, right? If it takes me five years to design a product, the market window might have moved in that five years and I might not hit that window. So being able to manage the new product introduction and get the new product yield is the single most important thing right now in semiconductor. There’s a lot of factors that go into that, but that’s really the focus.
So if design respins or inability to manage requirements are your biggest head equal, you’re going to that thread first. If it’s, I have a low first pass or initial yield, but then I’m going to the smart manufacturing thread first. Every company has a different type of need and most companies know what that need is.
Stephen Ferguson:
So Andras, this one’s for you. What value does simulation add to digital threads?
Dr. Andras Vass-Varnai:
That’s a great question, and before I directly answer that, just to add to what David said, from my perspective when it comes to digital threads, one beauty of the digital threads is it helps break down traditional engineering silos. So David mentioned, for example, the packaging threads starting from a requirement, going through electrical design, mechanical design, maybe I will position simulation in a second into that flow, then pretty much finishing the product, getting it ready for tape out, maybe even testing it after the tape out. So if you look at these steps within the threads, traditionally these have been done in silos, meaning engineering teams working fairly independently from one another.
As the complexity arises, that poses a threat on a company’s operation. David mentioned design respins, and obviously we’re trying to avoid those, but to avoid those design respins, a more integrated way of working is very necessary. And to your question Stephen, I think, where simulation is becoming really, really valuable is as the different teams are doing, their design works more and more together, simulation gives the ability to virtually test, virtually validate, the designs at the very beginning. If you use it correctly, not only it can help you validate your design and make sure you are meeting the criteria and your specifications, that actually using simulations, marketing some automation, it can actually help you get to that best or optimal initial design in the first place.
So we have tools in our PLL and EDA portfolios, allowing our customers to do multi-physics simulations, which can be power and signal integrated from an electronics perspective. That would impact thermal management. We can simulate that too, but the thermal field will create thermal mechanical stresses. So that’s another angle we need to understand and simulate and validate. So that’s already value.
But then if you look at these three areas, the electrical, the thermal, the mechanical, very often if you improve one, you actually just made the other one worse and this is where automation can help. If you get those teams, work together and maybe automate that workflows, you can easily find an optimum design. And that optimum design can be actually found much faster than running through a number of iterations one by one. So you can increase your MPI quite a bit with the help of simulation, in my opinion.
Stephen Ferguson:
And that optimal design can also be found with a lot less engineering input as well, because engineers are quite a valuable resource and all that. And the more you can automate, the more money you can save and the better you can use your engineering resources. I guess engineers doing the things which are important, which is making decisions based on data rather than manual tasks.
David Corey:
Yes, so just to follow up on Andras’s comment, so when we talk about digital thread, and we’ve just talked about the electrical design, the mechanical design, the thermal and mechanical simulation and so on, today most customers have a different product for every one of those functions. And you’re importing, exporting, importing, exporting, or emailing. There’s a lot of human glue in the process, so what is a digital thread, just to further expand on that? It’s for these products to efficiently exchange information without…
David Corey:
… to efficiently exchange information without having to import, export, import, export. Because if I’m down to the tail end of the process and all of a sudden my simulation shows that this isn’t mechanically viable, then I need to go all the way back to the head end of the process and start importing and exporting all over again as I move from different vendor to different vendor to different vendor.
So Siemens prides itself on really being an open-type system. Not only do we provide all these products and we flow them, this information between our products today, but beyond that, if there’s a different product in there, we have the ability to bring that data in and work with it. So digitalization is really about automation, about being more effective by combining these things and passing the information more efficiently.
Stephen Ferguson:
I think that’s the best description of digital thread that I’ve ever heard. So in terms of the amount of simulations being used in these industries, have companies reached saturation or are they adopting more and more simulation in their workflows all the time, would you say?
David Corey:
I think that it’s interesting because I just spent this week at the Consumer Electronics Show and the level of simulation as we know it, capabilities are exponentially increasing.
So there was a gentleman from Sony, I think he was the executive vice president of Sony, he came out wearing a VR headset, and he had VR sensors in his hands. And what he could do is he could actually sit inside the car and by moving his hands with these sensors and moving his thumbs on the sensors, he was able to interact with all the components within reach in the car. It gives the designers a way to essentially move around the device that they’re designing and interact with it.
So okay, that’s for electromechanical devices. Could that be applied to packaging? Could you put yourself inside the package to see things you’ve never seen before? I don’t know. But that technology, what they’ve just invented and partnered with Siemens to deliver to market, I find extremely interesting if in the future we’ve always wanted to see the interconnects, we’ve always been limited by certain geometries or shapes within the device. And now that you’re stacking packages and things or devices on top of each other in the package, it’d be great to be able to do the Iron Man thing and explode it out and put it together and see how all that works.
So I looked at that as a industrial metaverse, and that device has two significant advancements or announcements this year at CES. It was really quite exciting.
Stephen Ferguson:
So at the moment, if you want to understand and explore engineering data, you have to sit and look over the shoulder of an engineer who knows how to use the software and watches as he or she twiddle the mouse and changes things on the screen. But this gives an opportunity for even non-specialists and even consumers to explore this kind of technology and engineering data as well, which is really exciting, I think.
David Corey:
Yeah, it would definitely be a game changer in terms of a lot of people when they design these things are working in 2D still. Even the stacking of 3D, a lot of electrical designers don’t, while they are working on the connection that goes to the layer above them or to the device above them, they’re not understanding of the mechanical limitations that could be associated with these interfaces and the thermal impacts. So it would be a way to bring, maybe make a new breed of engineer, maybe an electromechanical engineer instead of electrical engineers, mechanical engineer or thermal engineers. The future could be one person working inside using these tools to actually change the game and make a more efficient design.
Stephen Ferguson:
Okay, David, so you mentioned you’ve just been to the Consumer Electronics Show. Can you tell us about some of the other things that you saw at that show?
David Corey:
Yeah, this year Siemens was the keynote speaker at the Consumer Electronics Show. And Dr. Roland Busch started off the keynote, and Cedrik Neike, our board member and CEO of digital industries followed up. And they had outstanding use cases where they showed how Siemens tools have been used in the industrial metaverse to help solve hunger issues, to help prosthetic limb issues, Red Bull Racing, how they use the tools.
So the keynote was really outstanding, but the key takeaway was that the industrial metaverse isn’t about making some utopia that we’re going to escape to. It was about using this technology to basically optimize the real world. The promise of the initial metaverse was just, hey, you go there to escape. This isn’t going there to escape. This is going there to optimize what’s really happening today on the ground.
And the level of technologies that Siemens is providing in the industrial metaverse for physical simulation of manufacturing facilities, for simulation of computational fluid dynamics, mixers, air flows, all these other things, they had outstanding examples of factories that we have simulated, optimized. And then with an executable digital twin, this is a new term that I actually learned there, of being able to take IoT and sensor data and feed it into the industrial metaverse to predict the outcome using the digital twin before it happens.
So I find this as a revelation in terms of capabilities because in the past, simulation was used to create what the factory should look like, and then people go to the factory and move the equipment around and make it like that. And then sometimes you don’t get the exact results because you can’t model everything exactly. But in this case with the executable digital twin, you’re using real data and feeding it into the model. And I think that that is the single biggest advancement that I’ve seen in simulation over the last 30 years. And the examples that they used at the show were really outstanding, and I look forward to helping customers deploy that technology this year.
The other significant announcement at the CES show was the ability to take the Siemens Mendix low-code platform and with AWS be able to drop large language models into Mendix applications. So basically you’re changing the way software will be developed in the future. You’re taking basically a low-code platform, and with the new partnership between Siemens and Amazon Web Services, you can use any of their machine learning or AI models and basically drop those into the application that you’re using this low-code platform for.
So one of the things I’ve struggled with, and I think a lot of people struggle with, what is AI for real and what does it really do for me and in this case, and how do I access it? We all can go to ChatGPT and type something in. That’s not an automated interface. But in this case, it would give you the opportunity for the application to learn about how the application is being used and how the data is being used and to come up with insights that we may not be able to rationalize as humans. So I find that outstanding, first of all. I didn’t know about it before the show, but they demonstrated it at the show and that’s really super exciting for me to see how that will be used in the future.
Stephen Ferguson:
You seem very, very, very inspired by your experiences at that show as well. So it’s great to see your enthusiasm as well. I think you’ve had the come to Jesus moment, haven’t you, at that show?
David Corey:
I didn’t even get in the flying car. I didn’t stand in a 200-person line to get the latest VR goggles on. But from a Siemens’ perspective, Siemens at the Consumer Electronics Show, we don’t make any consumer electronics, but we certainly make the technologies that enable people to do these digital twins and do this modeling, and that’s why I think it was really relevant for us to be there this year.
Stephen Ferguson:
That’s really exciting. So do you have any good real-world examples of digital threads that are being used in practice today?
David Corey:
I think the one that’s been used the longest in semiconductor is smart manufacturing. So the smart manufacturing digital thread really includes taking the plan of how I’m going to make this device, or this product, in multiple factories because today, wafers are fabricated. Those wafers are shipped normally to Southeast Asia or to some lower cost region where they’re probed and they’re sliced and they’re packaged and maybe even to a different country for testing depending on the cost parameters and way things are worked out.
So that data needs to travel, and that includes not just the simulation of how it’s going to happen, but also the control within the factories, one or many MESs, manufacturing execution systems, in those factories. Yield management is going on within those factories, material handling systems that go onto in those factories, so that dispatching, scheduling, so there’s all these different smart manufacturing products that work seamlessly together today to make some of these factories more efficient. And I would say that’s the most advanced digital thread that we have.
IC design is also a very well-baked, designing a single IC, that’s a very known digital thread that’s been happening for a long time. So really the emerging digital threads are overall data management, package design, and maybe some on the PC board assembly side as well. So I see those are the digital threads really ripe for growth.
Dr. Andras Vass-Varnai:
I agree with David 100%. And of course, as I’m focusing more on simulation and packaging in my area of work, I try to make the packaging related digital threads more successful among our customers. And there are a couple of really good examples. One of them actually is with the US Government Research Institute who embraced the power semiconductor package design digital thread. And what they do in a nutshell is they come up with a requirement, and often that requirement is driven by the actual vehicle which would be using this power semiconductor device. Then they continue with an electrical design.
So, obviously, first you need to have a schematic. That schematic needs to be transferred to a layout. Once you create a layout, especially in power, you need to understand the parasitics because those electrical parasitics will have an impact on the behavior of your circuit. So Siemens has tools to do all of that.
And once you have that first design, we hand it over to our mechanical portfolio, create a mechanical description of the package, and try to understand how that package could perform thermally from a…
Dr. Andras Vass-Varnai:
How that package could perform thermally from a structural perspective, so how reliable it will be, maybe run an optimization around among these three domains, electrical and thermal and structural, and then come up with the first few prototypes. And once we do that, our customers can actually test those components. So the in situ time talking about they have all of these tools, all the way up to testing, where they verify, using tests, the entire design process, use test to create actual data sheet parameters at the end of the design, and then use tests furthermore to quantify the long-term reliability potential of the component, and that concludes the design. So this end-to-end thread, it’s that, it works really well. Siemens has all the elements for making it successful. And we have customers, both commercial and also academic, which have been using it successfully.
Stephen Ferguson:
Can you tell us a bit more about how Siemens can help companies interact across the value chain?
David Corey:
Yeah. So one of the more difficult areas in the global… We learned a lot of things from COVID. The things we learned from COVID was that I could have materials in a country and the ability to manufacture using those materials in a different country, and I could not have the ability to move those materials because of quarantine restrictions, shipping shutdown, all these things we learned. And I had many customers that were caught in this predicament. Or even if they had the materials and had the ability to manufacture, the people couldn’t come to work to do the manufacturing.
And another complexity of that is if I have the master data that we talked about earlier, the master data is stored to manufacture that product at the site itself. So even if I could move the materials from, let’s say, China to the Philippines, I can’t easily move the master data, and I might not have the same equipment set, so even if I sent the material there, I may not be able to make a good product. And that actually happened to some of our customers. They somehow found a way to move those materials over there, they somehow tried to fix the master data quickly to consume those materials, and they ended up basically making a product they couldn’t sell, so they lost twice. They lost because they used those materials, and they lost because they couldn’t sell those, and now they didn’t have more materials to, because it was very scarce during COVID, so they didn’t have those materials to actually remake the product or fix the product.
So what we learned during COVID and the interaction between the global supply chain is that I need to be able to move master data efficiently, I need to be able to move material efficiently, and I need to be able to have partners, because a lot of times, in semiconductor, I may fabricate the wafer, but I might send it to what we call an OSAT, an assembly and packaging subcontractor, to actually do the packaging, so I need to get data to them efficiently as well. So this global supply chain, that’s something that Teamcenter does really well, it gives customers the ability to interact with their vendors within the supply chain, because they could have hundreds of vendors, or thousands of vendors, and move information, so everybody’s not working off of email and spreadsheets, they’re actually working off of a consolidated data set that could be shared amongst the supply chain.
So COVID was the come-to-Jesus meeting for a lot of people, and now, I see most, if not all, customers taking action to ensure… It’s something as simple as the correct test program being used at a site someplace in Southeast Asia, because if I’m using the wrong test program, I may not be testing for all the features that the product really has, and I could be shipping product that hasn’t been tested properly out to the market, which leads to recalls and to other issues. So that is the big global supply chain learning that we had about how to move data around the supply chain.
Stephen Ferguson:
It’s good to hear that we learned some proper productive lessons from two years of misery with COVID as well, so it’s nice, isn’t it, that there was some upside to all of that? Brilliant. Anything to add to that, Andras?
Dr. Andras Vass-Varnai:
To your question on the supply chain, again, I’m a little bit approaching this from a simulation perspective, but when it comes to the semiconductor supply chain, I’m starting from actually ready components. So as a semiconductor company, you’ve finished designing your product and you’re talking to your customers, which are primarily electronics integrator companies, that doesn’t really matter which industry they are in, but they would need models of your products so that they can do their own design. The digital twin of the components you make also travels with your products through the supply chain, and the problem with this is, and it comes to a digital twin of a component, if the digital twin is very detailed, it actually carries a lot of IP, which typically a company would want to hide along with it. So you can either have a legal process and try to work with NDAs, but very often, that’s not enough in the semiconductor industry.
And one good example here for packaging is, for example, terminal management. If you have a package, that package has metrics in a data sheet, and it has digital twins or models which can actually be brought into a design environment. Typically, the metrics on a data sheet are not enough nowadays, so you need to go with the digital twins. But how do you hide the actual design information, or how do you hide what’s really in the package, yet maintain the behavior of the component from a certain physical perspective, for example, thermal management, to experiment with that package in the end user environment on a given PCB, with a given heat sink thermal interface material or whatever?
And Siemens recently came out with a very interesting technology called BCI-ROM, and in fact, there is a version of BCI-ROM… BCI-ROM stands for boundary condition independent reduced order model. There is a version which is embeddable into a CFD environment. So when you create a model like this of your package from a thermal behavior perspective, it will give a full detailed behavior, it will carry the full detailed behavior of that package thermally, but it will completely hide the IP. So there are technologies out there nowadays, and Siemens is spearheading this, where you can take the behavior of the digital twin without really revealing how the digital twin was built or what are the components of the digital twin. And I think this is going to revolutionize design, because being able to use these models, from an end user’s perspective, from an electrical company’s perspective, their [inaudible 00:43:57] spins, their MPI, will be positively impacted too, simply by using the digital twin technology.
Stephen Ferguson:
So we’re about out of time, so before we finish, I’m sure people listening to this and are really excited about digital threads, if somebody was interested in starting to use digital threads, what would you recommend that the first steps they take are today?
David Corey:
I think the starting point is identify the pain, and what we’re finding is the pain is around new product introduction, data management, and to basically start there.
The other big trend we didn’t mention earlier was that people are moving to platforms. So the average semiconductor company has, let’s say, 200, 300, sometimes as many as 400, individual software systems controlling their business. And the big trend that we’re participating in is to move to platforms, platform being ERP is a platform, PLM is a platform, CRM, customer management, is a platform, and finally, manufacturing, MES, is a platform. So if I say that now I’m going to have four platforms and I have 400 existing applications, then I want to take those functionalities and divide them up to their proper homes and to take those capabilities and execute them within the platform.
So that’s the higher level digitalization that most of these companies are going through right now, and as a supplier of two of those platforms, we are helping customers get to identify the platform, to identify the threads that live within the platform, and then to prioritize how to deploy the capabilities they need to be successful. So that’s your digitalization playbook, get the platforms, make decisions on where your priorities are, and then ultimately execute on the priorities within the platform.
Stephen Ferguson:
Excellent, thank you. I think that’s the end of our broadcast today, so it just reminds me to thank you gentlemen for being excellent guests, and thank you for listening.
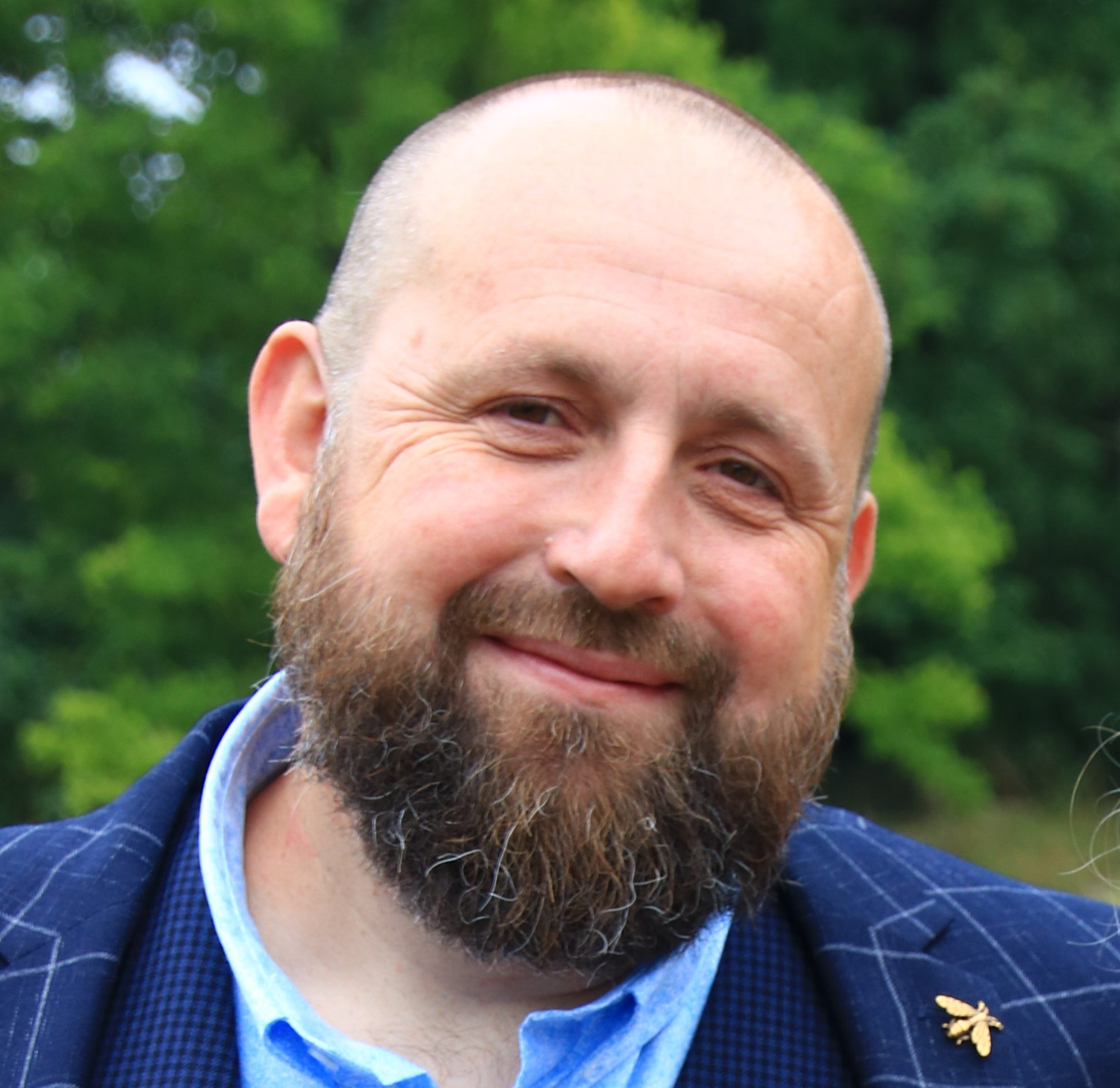
Stephen Ferguson – Host
Stephen Ferguson is a fluid-dynamicist with more than 30 years of experience in applying advanced simulation to the most challenging problems that engineering has to offer for companies such as WS Atkins, BMW and CD-adapco and Siemens.

David Corey
David Corey is the Vice President of Semiconductor Industry Sales at Siemens, bringing over 30 years of experience in the semiconductor industry. Throughout his career, David has worked closely with customers to solve complex manufacturing challenges, particularly in wafer fabrication, advanced assembly, and test processes. With deep expertise in semiconductor manufacturing and a focus on innovation, he is dedicated to driving efficiency and advancing technology through digitalization and the integration of cutting-edge tools. David is a leading voice in the push for digital threads and data management systems that enhance product development and streamline global supply chains.
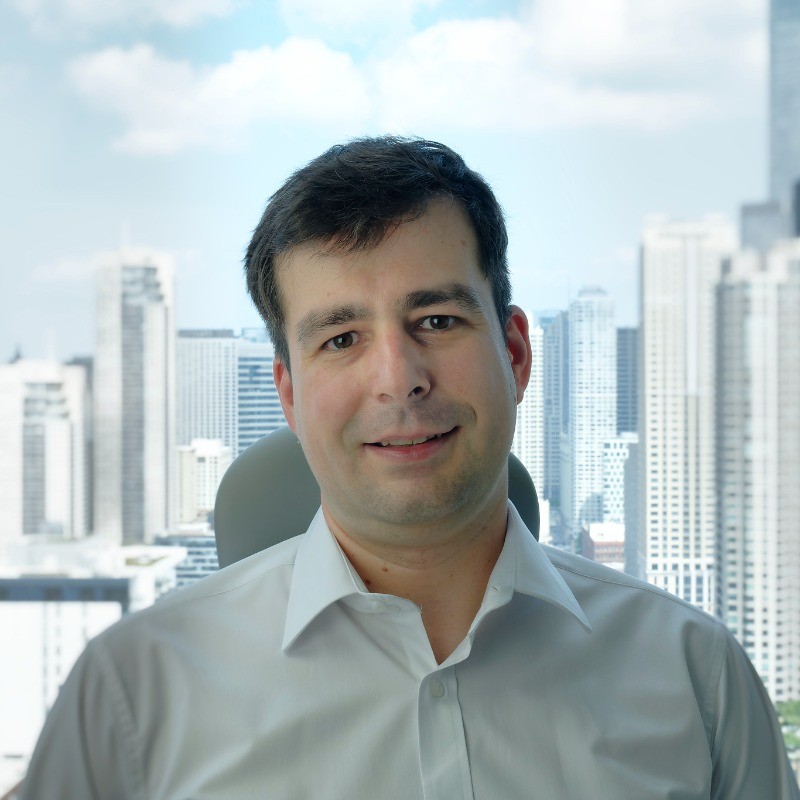
Andras Vass-Varnai
Dr. Andras Vass-Varnai is a Business Development Leader at Siemens Digital Industries Software, with over 15 years of experience in the semiconductor industry. Specializing in semiconductor packaging and thermal management, Andras leverages his background in Semiconductor Device Physics to help companies innovate through digital threads and simulation-based design. He plays a key role in driving engineering advancements and supporting customers in optimizing their semiconductor products.
Take a listen to a previous episode of the Engineer Innovation Podcast: Engineer Innovation: From concept to reality: AI and the digital twin at Realize LIVE on Apple Podcasts