Reinventing the Wheel: Cycling Innovation with Frederic Poppenhäger
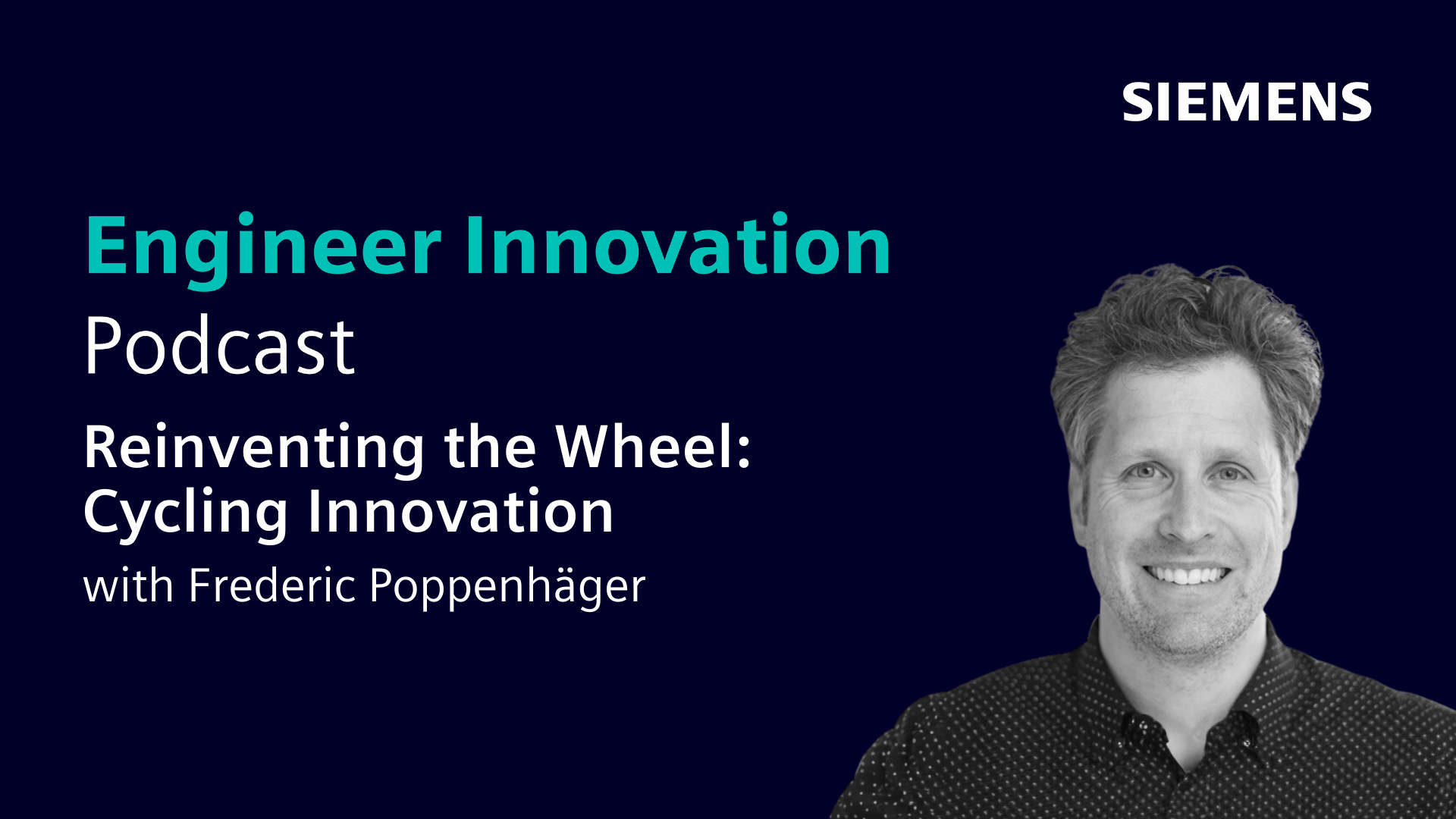
Listen to the Engineer Innovation podcast on
In this episode, we discuss advanced cycling technology with Frederic Poppenhäger, Founder and Partner at Radiate Engineering & Design AG. He is a specialist in simulation-driven engineering, particularly in the bicycle industry.
Key Takeaways:
- Radiate’s commitment to simulation-driven engineering in product development.
- What the edge simulation-driven design offers in creating innovative solutions.
- The role of AI in optimizing product design.
- The importance of balancing aerodynamics, weight and comfort in road bike wheels.
- The extensive simulation process behind the new wheel design.
- How aerodynamics are optimized for stability and handling in different conditions.
- The trade-offs between aerodynamic efficiency and wheel weight.
- The debut of the new wheel in prestigious cycling events.
- The broad applications of simulation-driven engineering in diverse industries.
- Frederic’s personal experiences with the prototype wheel.
Resources Mentioned:
Radiate Engineering & Design AG
This episode of the Engineer Innovation podcast is brought to you by Siemens Digital Industries Software — bringing electronics, engineering and manufacturing together to build a better digital future.
If you enjoyed this episode, please leave a 5-star review to help get the word out about the show.
For more unique insights on all kinds of cutting-edge topics, tune in to siemens.com/simcenter-podcast
- (00:07) Radiate’s commitment to simulation-driven engineering in product development.
- (01:10) What the edge simulation-driven design offers in creating innovative solutions.
- (01:28) The role of AI in optimizing product design.
- (02:43) The importance of balancing aerodynamics, weight and comfort in road bike wheels.
- (04:55) The extensive simulation process behind the new wheel design.
- (07:19) How aerodynamics are optimized for stability and handling in different conditions.
- (10:29) The trade-offs between aerodynamic efficiency and wheel weight.
- (12:22) The debut of the new wheel in prestigious cycling events.
- (14:05) The broad applications of simulation-driven engineering in diverse industries.
- (17:20) Frederic’s personal experiences with the prototype wheel.
Frederic:
Basically, you can say, road biking is all about speed. So, in general, you can say that a great aerodynamic wheel is generally a fast wheel, but still, there’s a bit more to it because it has to be also comfortable to ride. So you have to find an optimal solution between low weight, low inertia to speed it up, low aerodynamic drag, rolling resistance, and still provide a feeling of security, which means that the handling is nice for the rider, he or she can corner well and doesn’t feel unsafe or unstable while doing so.
Stephen:
In this episode of the Engineer Innovation podcast, we’re talking about aerodynamics in sport. If you were to do a survey that asked which sport is most influenced by aerodynamics, I think that most people would pick Formula One, in which millions of dollars are invested into perfecting the aerodynamics of the cars. However, for my money cycling is the sport which is most affected by aerodynamics, which you’ll know if you’ve ever tried to cycle into a headwind. This is best illustrated by a story from the 1989 Tour de France in which Greg LeMond beat Laurent Fignon by just eight seconds after almost 88 hours of cycling. Subsequent aerodynamic analysis suggests that the aerodynamic drag on Fignon’s signature ponytail lost him more than those eight seconds and ultimately cost him his chance to win the greatest prize in cycling.
You’ll be relieved to hear that in this episode, we’re not talking about the aerodynamics of various hairstyles, but instead about the engineering effort that goes into the most aerodynamic carbon fiber wheelset ever engineered. We talk about aerodynamics, we talk about structural mechanics, and we talk about the advanced manufacturing that goes into mass-producing carbon fiber wheels. This podcast is quite literally about reinventing the wheel. Enjoy your listen, and don’t forget to follow or subscribe to the Engineer Innovation podcast. To start off with Frederic, can you tell us a bit about Radiate’s simulation-driven engineering philosophy?
Frederic:
Yeah, sure. So basically, we are an engineering consultancy, here in Zurich Switzerland, and this philosophy of simulation-driven engineering is right behind everything, basically, we do, we believe that in this kind of philosophy, we move the simulation parts and product development to the very beginning of the development process. That’s why we call it simulation-driven, and for some of our customers, it’s quite a new approach. Obviously, this has been used in the automobile or aerospace industry a lot, but in other industries, it’s very uncommon still. For instance, if we take the bicycle industry, they usually do not work in this way, and we try to implement this and to talk about it with our customers and try to get them to see the benefits of it, of the process.
Stephen:
One of the projects that you’ve been working on recently, and I can — the clue is behind you, by the window — is you’ve been working on redesigning, which is probably the world’s most fundamental engineering object, which is the wheel. So we’ve been designing wheels for 6,000 years. How have you helped design better wheels using simulations?
Frederic:
Yeah, basically, if we use a simulation-driven approach and designing something very, as you call it, very old-school basically, as a wheel, you have totally new opportunities to do this. For instance, you can run in the simulation, you can run countless iterations without having to build any prototypes. You can, really, also employ artificial intelligence into it and really come up with solutions that are not intuitive to a human. So the simulation will guide you to a new structure, for instance, that you wouldn’t come up with otherwise. So you can really optimize it in every dimension that you want, whether it’s weight or stiffness or aerodynamic. So you have a whole new world of possibilities with simulation technology behind you.
Stephen:
So tell us a bit about the wheel. It’s on the market already, isn’t it? Which is the wheel, what’s the manufacturer and what’s it called?
Frederic:
The wheel is called Capital SL, and basically, it’s our second wheel that we have been developing with this kind of method. The first one was for mountain biking, which is also for the same client behind it. I think I can mention it, no? It’s no problem, it’s Syncros for SCOTT Sports, who’s the customer behind. And they sell it already on the market for quite some years now, the mountain bike wheelset, and we now use the same methodology to specifically build a road bike wheelset and also optimise it aerodynamically. So it’s based on a method that we have been using for some time, but this is now the first approach for road biking or road bike wheels.
Stephen:
So what goes into a good aero wheel for a road bike?
Frederic:
Basically, you can say, road biking is all about speed. So in general, you can say that a great aerodynamic wheel is generally a fast wheel, but still there’s a bit more to it because it has to be also comfortable to ride. So you have to find an optimal solution between low weight, low inertia to speed it up, low aerodynamic drag, rolling resistance, and still provide a feeling of security, which means that the handling is nice for the rider, he or she can corner well and doesn’t feel unsafe or unstable while doing so. Because if you, for instance, ride a wheel or a bicycle at high speed, if you go down a mountain pass, which can happen quite a lot in Switzerland, there can also be some kind of crosswind coming up and you don’t want to have an aerodynamic wheel that feels unstable while cornering. And these are constraints that you have to take into account when you try to construct or design it. So basically, it’s a combination of all these different parts that goes into it to make it a great aerodynamic wheel.
Stephen:
And cyclists are obsessed by marginal gains, aren’t they? So small improvements in aerodynamic performance have big payoffs in a sport which is basically dominated by aerodynamics. So how much did you manage to reduce the drag by?
Frederic:
You can say, it all depends again a bit to which kind of other wheels you are combining it to or challenging it. We have tested it to very similar equip, also carbon wheels on the market, and basically, we can say that our wheel is 7% past, or has a 7% more drag reduction when compared with other models. 7% doesn’t sound much at first, but you have to say it’s quite a lot actually, if you ride it. And as you mentioned-
Stephen:
And for cyclists, they really are obsessed by marginal gains. So every gram of weight saving, every percentage point of drag reduction is really important in that sport. Especially competitively, where you might be cycling into the wind for several hours trying to keep ahead of your competitors who are nicely tucked up in a nicely aerodynamically sheltered peloton, as well. Aerodynamics is everything in that sport. If you look on your website, you can see some videos of the wheels being wind tunnel tested and looking at different designs to wind tunnels. How much down selection of designs took place because of simulation before you got to the wind tunnel stage?
Frederic:
Quite a lot, actually. We extensively simulated all kind of different rim shapes and geometries before we went into prototyping some aspects and go to the wind tunnel. To sum it up, I think almost 200 configurations were simulated, each of them at very different yaw angles, and I think we generated five or more terabytes of simulation data before we found the most promising geometries for which we then were able to build a certain construction to go to the wind tunnel.
Stephen:
And how did you explore the various geometry parameters? How did you select the first designs to look at? Was that an automated process or was it manual configuration?
Frederic:
It’s a combination, no? It’s a bit, certainly looking at simulation data and certain digital simulations or configurations, and then we prototyped, I don’t know, five or 10 most promising geometries with a system that we could implement in the wind tunnel where we were able to construct a metal rim with the same rim geometry as we would use on the final rim. Then you can mount this on a specific prototype model that represents the outer shape, and then you can also even model the spokes into it that have the same shape as the final shapes you’re going to test. And this was the setup for the wind tunnel testing.
Stephen:
In order to generate five terabytes of data for a wheel, you must have had a rather good process to run the simulations and also extract meaningful engineering data from them.
Frederic:
Yeah, for this we have our specialists. They have some certain backgrounds in CFD simulation, also coming from, some of the guys here have Formula One backgrounds, even so they are really equipped to do this, but of course, it has to be a specialist, that really does this well.
Stephen:
And you talked about crosswind stability and that’s done by looking at various yaw angles. What sort of angles did you look at? What sort of variation angle?
Frederic:
All kinds of variations, and you also have to find the right method and how to calculate them depending on the certain conditions you look at. If you look at conditions where the rider’s speed is low but the wind speed is high, or the other way around, you have certain conditions that you take into consideration, and then you weigh different factors against each other. So it’s really a complicated process, I have to say. And the ideal is to reduce the drag, obviously, but make the wheel at the same time predictable in windy conditions so that you’re still able to steer it or to affect the steering in a positive way.
For instance, if you look at these aerodynamic wheels that are already on the market, there’s lots of them. We haven’t invented the first aerodynamic wheel, we just tried to optimize it in a certain way. It’s quite common that if you use deep-section wheels, which have a 60-millimeter or even 80-millimeter rim, they really usually affect the steering in windy conditions, when the wind comes from the side at a high yaw angle, which makes it difficult to steer. You feel it when you go downhill, it’s shaky when you go down at high speeds. And we try to improve this by really making the wheel, let’s say, less susceptible or sensitive to wind conditions at high yaw angles.
Stephen:
That’s not only a stability thing, as well, if you watch your Tour de France, sometimes, in the stages through, kind of, flat Belgium, when you get those crosswinds and you get echelons forming as well, that’s I think my favorite thing about professional cyclists, where you get all the big lads, big Belgian guys, going to the front and pushing away. It can really disrupt the whole race, can’t it? So crosswind performance really is important in cycling.
Frederic:
Yeah, totally. Yeah, it can make a huge difference. These, kind of, echelon stages are usually the most unpredictable also in the outcome because you have to be in the best position, you have to be usually at the front, and also, to get there, you try to use as less energy as possible to go there. And in order to make this step and to be at the front, to be at the right position, you try to save energy and you really are looking forward to a setup that makes this possible, to really give you the possibility to be at the right position before this happens so that you don’t get separated by the peloton.
Stephen:
So you talked a bit about road cycling. There’s a big difference, isn’t there, between designing a perfectly aerodynamic wheel that works perfectly on a very flat and even surface and a wheel that has to work well under real-world conditions? What sort of conditions is this wheel going to be used under, do you think?
Frederic:
So you can use it in several different conditions. Basically, the task that SCOTT, our partner, gave us, was to not only build a wheel that can be used in time trialling, but also that is usable on high mountain passes where you have to climb a lot, for instance, or even in gravel conditions. You can also use the wheel just for a gravel ride. The thing is, usually we would say, that’s why we also made different versions. So we have the 60-millimeter rim and 40-millimeter rim version. For instance, the 40-millimeter capital SL is basically also a good gravel wheel. It’s aerodynamically optimized, of course. But still, it accelerates very fast, and also, you can equip the eight-millimeter tires on it, so it’s also quite comfortable depending on the tire you use. But basically, you can use it for these kinds of things: road biking, time trialing, gravel, whatever you like.
Stephen:
So at the beginning, we joked a bit about reinventing the wheel, but I guess one of the differences between modern wheels is that you can construct them from carbon fiber, can’t you? So is there ever a compromise between aerodynamic performance and the stiffness and weight of the wheel?
Frederic:
Yes, there’s a compromise that you have to do because, basically, a wheel that is aerodynamically optimized is usually not the lightest wheel because you have a deep rim section and you have to add material at the rim in order to make it aerodynamically optimized. On the other hand, a very light wheel, usually, when you just optimize the low weight is usually not the aerodynamically optimized wheel. Basically, there is these competing objectives, and we try to make very many iterations to explore this, kind of, what’s the best way or best field to deliver the best combination of aero and weight features?
Stephen:
So did much structural engineering go into the wheel as well and, I guess, advanced manufacturing technology as well? I think you describe it on the website as a one-piece construction, as well. So what did engineering a one-piece construction wheel involve?
Frederic:
So the Capital SL is like a one-piece, as you mentioned, or we call it monocoque construction. So it means that the rim and the spokes are fused together in the single piece, which already enhances structural integrity because if you take, for instance, other full carbon wheels, usually the rim and the spokes are separate, the rim is manufactured and spokes are manufactured and the spokes are usually integrated at a later stage into the rim. With our system, that’s not the case. Our process involves the curing of the carbon fiber spokes and the carbon fiber rim simultaneously in one shot. It’s an all-in-one mold also, basically, and this ensures optimal strength at the spoke/rim interface, and it also has other advantages. And basically, what you gain at the end with it is almost 20% reduction in rotational inertia relative to other traditional carbon wheelsets we compared. And that really enables you to have a very good power transmission and substantial speed increments for riders. If you put the power down to the pedal, it really translates in a very efficient way into the wheel and you gain forward momentum.
Stephen:
And you can accelerate faster. So are we expecting to see this wheel being used in competitive cycling? Will it be seen in the Tour de France next summer, do you think?
Frederic:
It has already been introduced this summer in the Tour de France. So, the team behind the professional team is team DSM-Firmenich, from the Netherlands, and they used the wheels in the time trial, the individual time trial, at this year’s Tour de France. They also use the wheels at the Spanish La Vuelta this year in the fall, and we are expecting to see many more use cases for it in the professional field.
Stephen:
I was going to say Dutch cycling teams know all about crosswind stability, don’t they? In flat countries, you learn a lot about side winds and echelons.
Frederic:
Yeah. I would like to point out that really this wheel is not only for the professional rider, so you can really experience these kind of gains/benefits that I was talking about before, really good handling stability. You’re also doing crosswinds, the aerodynamic gains you have under that section. Or also, the momentum of inertia that you experience when you go uphill, to accelerate fast while you go over small hills or even lower hills, any rider can really experience riding it.
Stephen:
So do you think that this wheel is better than a wheel you would’ve designed without simulation?
Frederic:
Yeah, because as we mentioned before in the beginning, a lot of trial and error is possible in simulation without having to prototype as much as beforehand with other development processes that have been used there in the cycling industry. It’s just not possible to do this kind of iteration in a very fast and efficient way without simulation technology. That’s at least what we believe here.
Stephen:
We talked a bit about your simulation-driven engineering philosophy at Radiate, but that doesn’t only extend, obviously, to the design of bicycle wheels. If you look at your website, you’ll see lots of fantastic, innovative designs. What other projects have you been working on using simulation?
Frederic:
We apply this method to different fields or different industries. One industry I can mention, for instance, is also the civil drone or aerospace industry. So we build, or design and build, civil drones here in Switzerland, and we also design and develop medical technology products for the prosthesis or a casing system for a quantum microscope. So we try to not only work in the field of the bike industry but to expand our experience into different sections.
Stephen:
Do you think that the work that your customers ask you to do is influenced by sustainability at all and its drive to lower carbon? Is that a big factor in the work that you do?
Frederic:
It certainly grows as a factor. I wouldn’t say that it’s a dominating factor right now. To be honest, it is still a problem for material or for products that come with carbon fiber. All the sustainability part of this, recycling this kind of material is still difficult. We try to be as, let’s say, sustainable as we can in order to, for instance, construct something that leads to potential fewer materials being used and wasted. For instance, this wheelset we’re talking about right now doesn’t need a rim tape, which kind of reduces a bit of weight. We ensure that the spokes and nipples don’t need replacements during the product cycle, or we try to construct and design something that has a very long life cycle, maybe also contrasting with other traditional wheelsets. We try to focus on this, but still, to be honest, some other aspects need to be improved still in that area.
Stephen:
And I think you mentioned earlier AI, it’s still very early days in AI, but is that something you’re embracing in your, kind of, simulation process, at all?
Frederic:
Yes, we do. For instance, if we talk about the simulation part of the wheel development, the finite element analysis that we do here, the question is always what kind of load cases do you include in this simulation in order to really make it as real-world as possible? And we have found a method that enables us to generate real-world, load-case data. The way, or the method, we apply here is that we build test bicycles with sensors or they’re equipped with different sensors in the wheels, then we can put a rider on it and ride the bicycle and generate the data during the physical test ride. And this data then is being calibrated and enhanced by machine learning. So we have certain applications running in the background that calibrate this data, and then later on we can gain information out of this for our load case that we apply in the simulation afterwards.
Stephen:
And, I guess, the advantage to doing that is when on the test bike you can only physically put a limited number of sensors on, where you can use that sense to run FEM models, which give you an infinite number of virtual sensors. You can see what’s happening at every part of the wheel, which is really quite valuable I think.
Frederic:
Yeah, exactly. Yeah, because the whole system, or the wheel, as I understand it internally here is a system, no? And every part that you can optimize needs to be taken into account. Yes.
Stephen:
Finally, are you a cyclist and have you ridden this wheel yet?
Frederic:
Yes, I have, actually. I have ridden certain prototypes that we had pre-production. I’m not an expert rider, so my information was not very available to the development team, but certainly, it was very valuable for myself, not to experience the difference between riding, I would say, a normal steel spoke wheelset and riding something as efficient and high-tech as this whole carbon wheel, really makes a difference, even for myself.
Stephen:
Yeah, I’d love to have a go, but I don’t think I could pedal fast enough to make a difference. Frederic, thank you very much. That was a really interesting insight into the world of designing wheels. And we look forward, I’ll look out for the wheels on bicycles at the Tour de France this year. Thank you.
Frederic:
Yes, thank you too.
Speaker 3:
This episode of the Engineer Innovation Podcast is powered by Simcenter. Turn product complexity into a competitive advantage with Simcenter solutions that empower your engineering teams to push the boundaries, solve the toughest problems, and bring innovations to market faster.
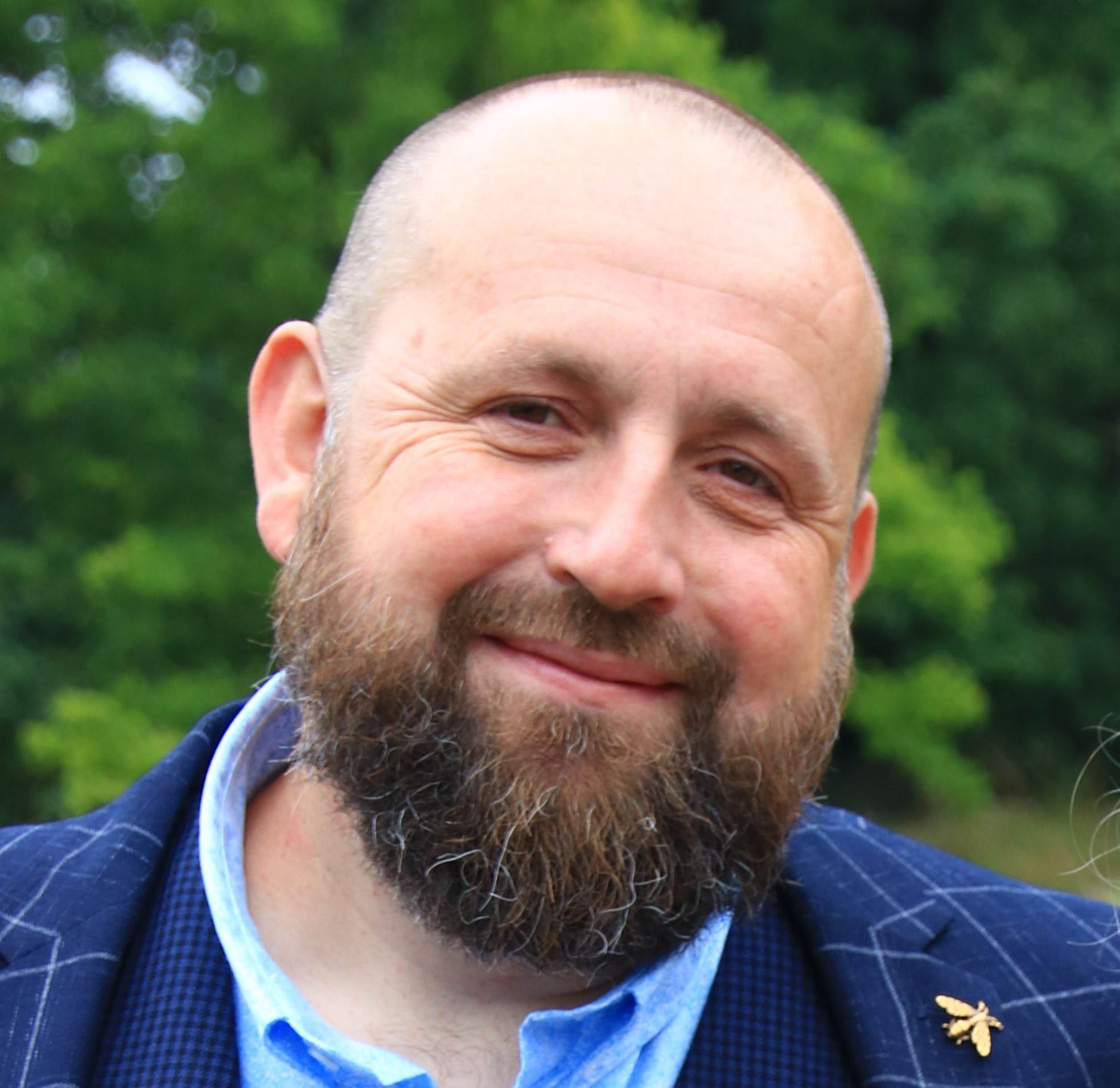
Stephen Ferguson – Host
Stephen Ferguson is a fluid-dynamicist with more than 30 years of experience in applying advanced simulation to the most challenging problems that engineering has to offer for companies such as WS Atkins, BMW and CD-adapco and Siemens.
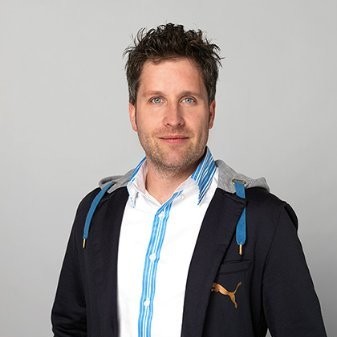
Frederic Poppenhäger
Frederic Poppenhager is the founder and Partner at Radiate Engineering & Design AG. He is an innovative entrepreneur with a strong background in marketing and advertising, with more than 20 years of experience in the industry. Recognized for building successful businesses, leading teams, and implementing effective marketing strategies. Fluent in German, English and Spanish. Founder of Radiate Engineering & Design, Zurich, Switzerland (2014 – Present).
Take a listen to a previous episode of the Engineer Innovation Podcast: Engineer Innovation: Engineering the Past: Junkers Reviving the Junkers Ju 52 with Danny Wadewitz on Apple Podcasts
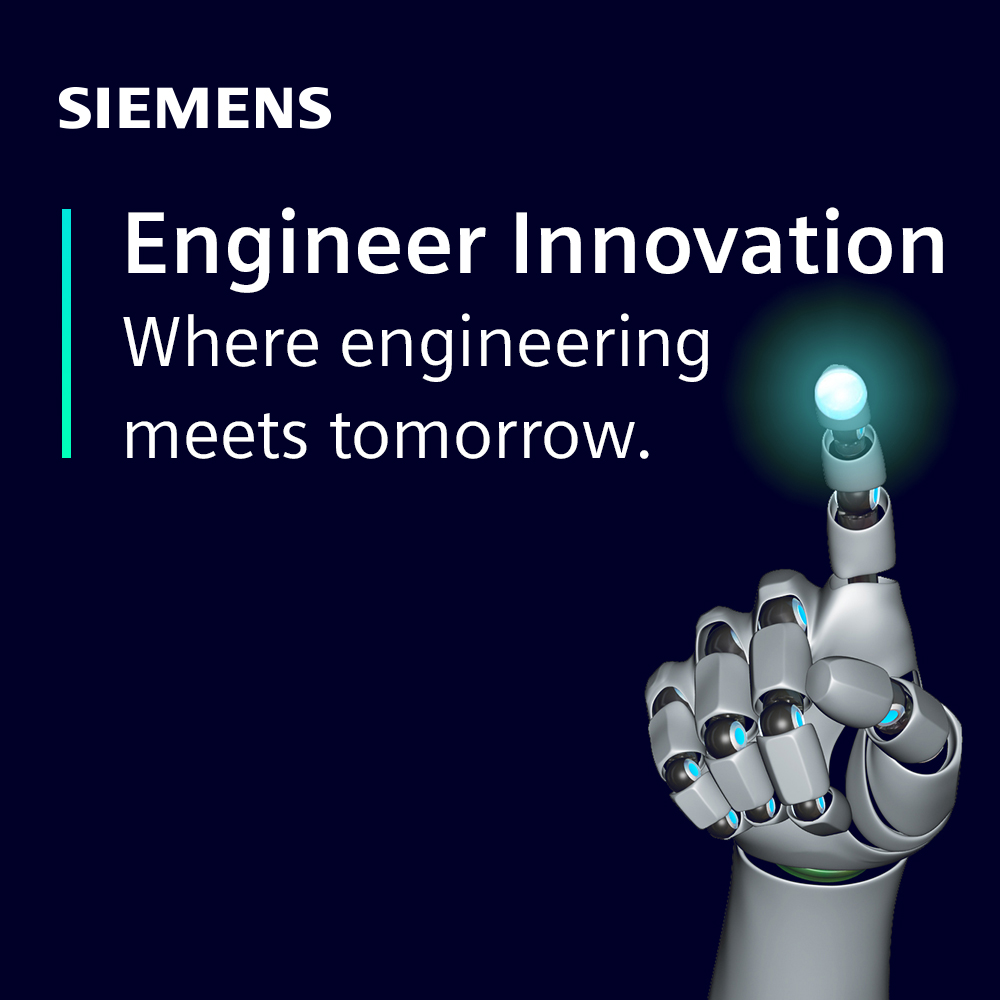
Engineer Innovation Podcast
A podcast series for engineers by engineers, Engineer Innovation focuses on how simulation and testing can help you drive innovation into your products and deliver the products of tomorrow, today.