From Simulation to Sea Trials: the Science of Simulating Ships
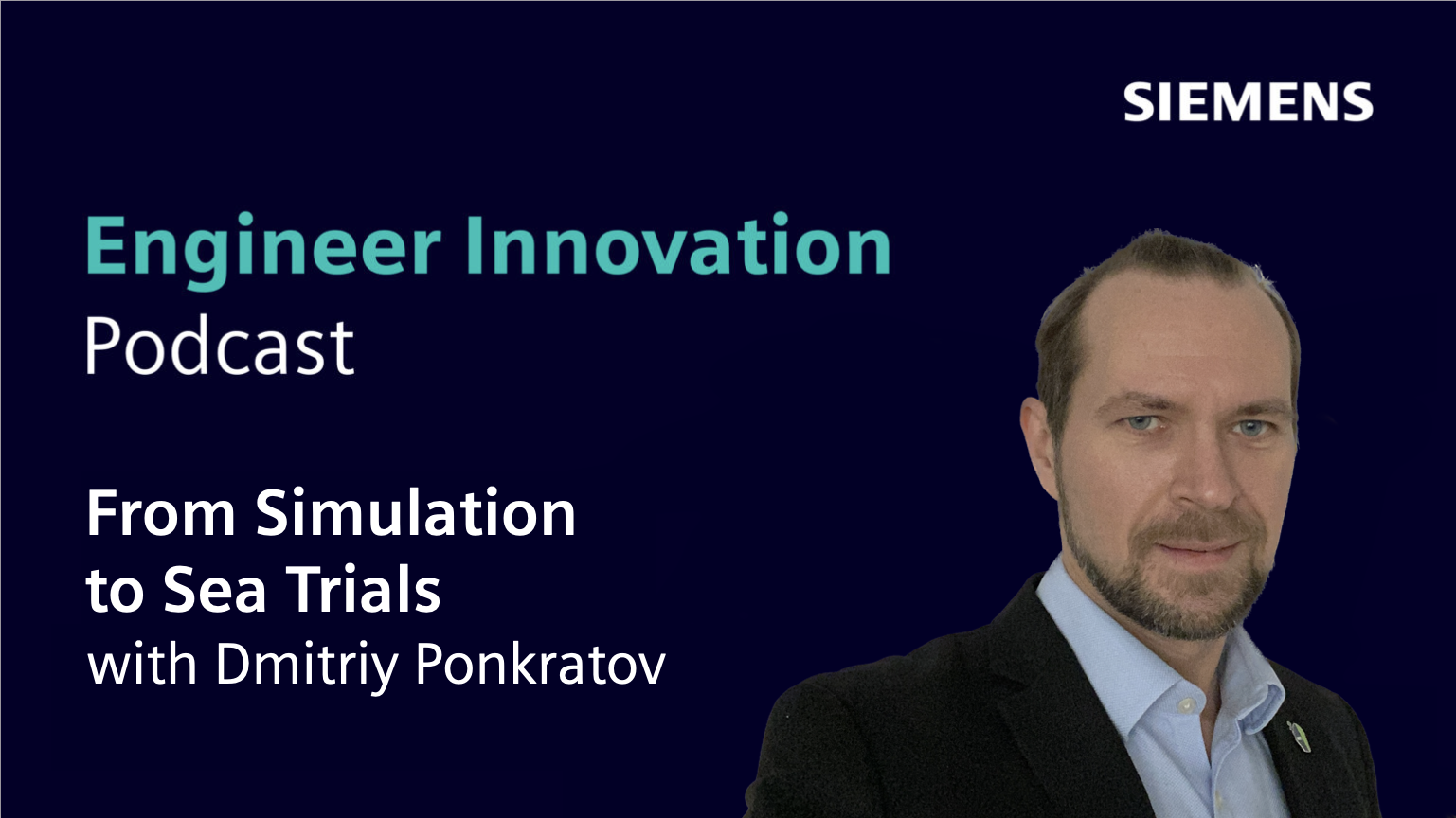
In this episode of the Engineer Innovation podcast we take an in-depth look at the science of simulating ships. We go behind the scenes of the world’s largest ever marine validation experiment, in which 54 teams of engineers compete to simulate the performance of a cruise ship which is full of passengers.
My guest is Dmitriy Ponkratov from the Royal Institution of Naval Architects who has been performing marine CFD simulations for more than two decades with Lloyds Register of Shipping and RINA, and who is also a veteran of many sea trials.
We talk about:
- The challenge of meeting IMO’s Zero Carbon Shipping target by 2050
- The pivotal role that simulation plays in designing the ultra-efficient ships required to meet these standards
- Exploring novel marine propulsion systems
- Establishing trust in CFD simulation as an alternative to towing tanks and sea trials
- Creating a dataset of sea trial data that can be used to validate CFD simulations at full scale and in real world conditions
- A massive validation effort that includes 54 companies and institutions.
- How CFD engineers deal with sometimes getting the answer wrong
- The Marine Digital Twin
- Artificial Intelligence and Machine Learning as applied to the marine industry
- Conducting sea trials on a cruise ship full of gin-and-tonic sipping passengers
This episode of the Engineer Innovation podcast is brought to you by Siemens Digital Industries Software — bringing electronics, engineering and manufacturing together to build a better digital future.
If you enjoyed this episode, please leave a 5-star review to help get the word out about the show.
For more unique insights on all kinds of cutting-edge topics, tune into siemens.com/simcenter-podcast.
- The challenge of meeting IMO’s Zero Carbon Shipping target by 2050
- The pivotal role that simulation plays in designing the ultra-efficient ships required to meet these standards
- Exploring novel marine propulsion systems
- Establishing trust in CFD simulation as an alternative to towing tanks and sea trials
- Creating a dataset of sea trial data that can be used to validate CFD simulations at full scale and in real world conditions
- A massive validation effort that includes 54 companies and institutions.
- How CFD engineers deal with sometimes getting the answer wrong
- The Marine Digital Twin
- Artificial Intelligence and Machine Learning as applied to the marine industry
- Conducting sea trials on a cruise ship full of gin-and-tonic sipping passengers
Stephen:
Hello and welcome to the Engineer Innovation Podcast. With me today is Dmitriy Ponkratov from the Royal Institute of Naval Architects. Tell us a bit about yourself and how you got involved in engineering and what you do at RINA.
Dmitriy:
Yes. First of all, I should probably point out it’s a Royal Institution of Naval Architects, not Royal Architects. But yeah, it’s a normal thing, a lot of people just be confused by that. Let me start with a few words about myself. I’m a naval architect, I graduated created nearly 20 years ago. And actually, my first job was in China, I spent two years in China working in CFD, validation and development of D2. And then I moved to Norway, I spent three years in Norway, teach university and research work in marine tech, now it’s [inaudible] Ocean. And then in 2012 I was invited to join Lloyd’s Register Techniques litigation department. It’s a quite unique department within Lloyd’s, specifically focusing about the failure investigation, the performance and so on.
Basically, we had great opportunities to travel globally, GP Arts on board of the vessel and trials, absolutely quite exciting role. Proper Engineering Simulation, hands on. And then four years ago I joined the Royal Institution of Naval Architects in [inaudible] of technical director. And now we’re also involved in quite a lot of in projects both in the UK and globally. But just a few words about the institution, it was established in 1860, so 163 years ago. And basically that time it was some sort of community of naval architects, mainly in the UK, thinking, discussing and sharing ideas how to improve in business, how to [inaudible] better and so on. Strictly speaking, 163 years later we do absolutely the same, but obviously, we’re doing it on a greater scale, so it’s a global community with about 10,000 members globally.
And we’re involved in a lot of interesting projects with universities, with our publication, we’re organizing a lot events, conferences globally again. We had a conference in Japan last year, in the Netherlands for next year, we’re thinking to have a conference in Australia and so on. And another instant but important thing is we have the NGO status at IMO, International Maritime Organization. Basically, we had a great opportunity to oversee from the technical perspective, what’s actually happening regular this side.
Stephen:
You obviously have your finger on the pulse how simulation and tests are helping. So what kind of role do you think simulation plays in the [inaudible]
Dmitriy:
Well, I think it’s playing the major role, but I think there are a lot of more opportunities in the future because as you probably know, in July this year, so just some months ago, IMO came up with a new strategy which kind of says, “We need to have zero carbon, just prepare zero carbon shipping by 2050 or around that year.” Basically, there are a lot of technical challenges, how to actually achieve that. And basically being on the simulation side and the digital side, actually it’s a lot of opportunities to make sure that we can design the energy efficient vessels, so basically make significant [inaudible] of all the processes and make it system as accurate and efficient as possible. And then obviously, bring on top of that the fuels. Only the coming of these two factors will make the change, actually.
Stephen:
Do you think that those regulations and that kind of push towards a low carbon future is causing a lot of stress in the marine environment? Good stress, I guess?
Dmitriy:
Yeah, it’s very good stress. Basically, I think it’s very exciting times now because obviously, if you think in the past what’s happening, like a adaptation of the steam engine, it took quite some time, a lot of decades to put the steam engine on board of the vessels and to progress to the next level, your engines and so on. So basically, it was quite a significant and time consuming process. Now we don’t have so much time, we have nearly 27 years to achieve this. From the historical perspective, it’s a very short timeframe with something. And basically in that sense, it’s very exciting times, so now we need to really put all our efforts to make it happen. And the only thing is actually to collaborate, to share, to be innovative, to look outside the box and just to bring all the possible solution in one pot.
Stephen:
Because there are still a lot of possible solutions as well, isn’t it? It’s not like you’re just on one path. It’s not like we’re going to make all boats electric or we’re going to use synthetic fuels. Realized a couple weeks ago I was speaking to lots of people and people were even involved in some kind of wind as propulsion systems. You talked about the time it took to put steam engines and we’re going back to wind might be one of the solutions to this as well, so it really isn’t exciting with lots of potential for innovation.
Dmitriy:
Exactly, I don’t think there is a silver bullet to make it happen. So basically, the only opportunity is just to look around and for each specific business, for each specific market, for specific sector of the shipping, that might be a slightly different solution. If we’re talking about the wind propulsion, we are working very closely with internationalisation and we have a lot of interesting projects with them. And we can see that in some areas of the planet, it’s actually the solution. So if you just consider some specific areas with a lot of energy, that’s definitely the case, that’s probably very win-win situation. In some other areas it might be not that appealing, so we might still think about the alternative fuels and something else, but definitely, we should be mindful about this.
Stephen:
You said you’ve been in the engineering for about 20 years, was that right?
Dmitriy:
Yes.
Stephen:
20 years ago, I guess your industry has changed a lot because I remember talking to some people at Lloyd’s Register 25 years ago and almost everything was still done in towing tank and models. And now some of these innovative solutions, it’s going to be difficult to test just in a towing, so I guess that’s part of the role of simulation, is these kind of interactive, more complicated scenarios where you simulate whole systems rather than just elements.
Dmitriy:
Yes. I think in the past, the towing tank was a primary solution because it was quite difficult to develop the alternative for that. Obviously now, we see the technology with computational fluid dynamics, so we can do a lot of various stuff. And even those things, it’s quite difficult to implement in towing tank. The challenge obviously, the validation. We need to make sure that the things that we’re simulating in CFD actually makes sense, so we need to crosscheck and validate our results. And that’s another challenge, another complexity. But at the same time, with a lot of initiative happening now so we can address this challenge. We are running an interesting project to create these validation cases. It should help the industry to make sure CFD is actually working.
Stephen:
That was going to be my next question, is how do you trust the results of simulations? Because we’re not just talking about ships operating in nice, steady, calm conditions. We’re talking about ships which have to operate in sometimes in horrible conditions and still do their job. You can’t just sometimes anchor up and hide from the weather. So how do you prove that these designs that you’re looking at are going to be robust across all operations and make sure you trust the results? How do you do that?
Dmitriy:
I think at the moment we just blindly rely that it’s working. Unless we hear horrible story, we believe it’s okay. And I think in the past it was because the level of expectation was pretty… The engineering approach was like, “Okay, we see de can deliver something and we can get 10% accuracy, it would be good enough.” Now because we’re fighting for a tiny percent, what if we have the energy saving device which can give you 3%, 5%? Basically in that case, we need the extra level of accuracy. And in order to do that, obviously, we need to have proper validation cases. And that’s exactly what we’re doing within the [inaudible]
Stephen:
Previously, if you were designing or certifying the experimental testing phases, that would be trials. The sea trials are difficult to get data from typically, because they’re not really set up for providing this data. How long do sea trials usually last for a new vessel?
Dmitriy:
Normally when the new build is delivered to the client, the proper trials takes about 10 days, but it’s going to include all kind of tests. For the performance trials, it’s about eight to 10 hours.
Stephen:
And you’re stuck with whatever weather conditions happening in place for that experiment as well?
Dmitriy:
Exactly.
Stephen:
So you are working on a bigger project to provide a better validation set. And can you tell us a bit about that project?
Dmitriy:
Yes, basically the idea of this project is create some sort of database of industry recognized test cases that anyone could use in the future to validate their CFD. And that’s actually quite important thing that, even though it’s a Siemens podcast, we’re not saying that only Siemens people should be using these validation cases. Basically, it should be open for everyone, that everyone could use these test cases to make sure that [inaudible] was actually working. And in that case, what we wanted to do, we just wanted to select a few test cases, a few actual vessels, actual seagoing vessels and make the very comprehensive measurements and trials with these vessels. And then obviously share the geometry files, the HAL lines, propellers and all the results of the researchers, the universities dataset to.
Stephen:
What sort of vessels are we talking about?
Dmitriy:
At the moment it’s quite interesting. Initially, we started only with two vessels. We wanted to have two vessels in our fleet, let’s say. It was a general cargo vessel and it was another container ship. At the moment so the fleet is expanding, so now we have six vessels. So it’s a general cargo vessel, it’s a tanker, it’s a twin screw ferry, it’s a twin screw cruise liner, it’s a tug boat with a duct propeller and also bulk carrier.
Stephen:
What sort of data trials?
Dmitriy:
In general for all the cases, we recorded the speed and power, so basically the traditional performance [inaudible] vessels. Obviously, it’s quite difficult to measure the resistance, but we can measure the power, the torque RPM, the whole other parameter propulsion units. It’s done for all the vessels but in some cases we developed very specific, very enhanced things. Like for the tanker case, we measured the flows. We developed a special unit, it’s called PA or flow pipe, was developed by Maring. We managed to measure the flow, which is actually coming to propellors, so with the three components on [inaudible] It’s actually quite interesting for the CD practitioners, it’s not just check the integral characteristics like power and RP, but also to compare and check the flow, which is actually its own dataset.
Stephen:
And how do engineering practice with using this data in part of this?
Dmitriy:
At the moment, because the project is organized as a joint industry project, basically it’s about 54 companies, it’s actually the largest initiative in the project. Usually in the joint research project we have about 15, 20 companies. In this case it’s 54, it’s a global community from 18 countries. They contributed with money, to put money in the port and we spent this money to achieve our goals making this measurement. Basically at the moment, the results, they’re only shared with the project participants, but because we do understand the importance of this dataset for global, so later on 2024, this data will be shared within the public domain in all the results.
Stephen:
And then we’ll basically provide a validation data set which will become a standard for the industry and everybody will use, going forward it.
Dmitriy:
Yep.
Stephen:
Is there any competition aspect to this where you compare the results from different groups who investigate as well?
Dmitriy:
Basically what we do is actually the key part of the project, it’s a validation. And we would like to introduce the blind validation. Basically what we actually do, we perform the trials on a vessel. We have the geometry files of the vessel and we have the final results, let’s say torque and power and RPM of the propeller. So basically then within the community, within the project we organize the local workshop and basically within this workshop, we share the geometry files and we share the basic setup like the vessel speed, but not the final results. The final result, the participant, they don’t know what they actually calculating.
And then we ask them to submit the data in the specific format and then we come together, we just put the results together and show them, “Okay guys, these participants under predicted 10%, but that participant is spot on with the results.” So basically, you should kind of share and learn from each other, what they did in order to make it happen. But at the same time all the participants there are anonymous. So if someone actually made a significant silly mistake and their result’s 50% off, obviously, they know that they made a mistake because they compare with other results, but at the same time, no one can blame them, saying, “What kind of results you submitted?” So in that sense it’s pretty fair approach.
Stephen:
And the truth of simulation, it’s quite difficult. It’s difficult to predict how a vessel’s going to perform in those as well. And so sometimes it’s as interesting to learn from the people who’ve made mistakes and identify mistakes as it is to pick out the best practice. I mean, guess that’s the way of defining best practice, is you have to look at both ends of the spectrum as well. It must be very stressful for participants. It’s quite difficult as an engineer sometimes as well, we have to trust our simulations, but you don’t really know. To be in that kind of environment where you’re looking and comparing against others, it’s stressful but real interesting.
Dmitriy:
It’s stressful but exciting at the same time, because obviously it’s interesting for a company to run the case, submit and just to see how it’s actually comparing with the actual measurement. Because obviously, you can learn a lot from that. And you’re exactly right about the feedback we receive. Sometimes actually, we see specific participants. For instance, they underestimate the results for 18%. And then once they see that, “Okay, we actually now did something wrong,” so [inaudible] will rerun the case and improve something.
And then suddenly months later, they’re coming back with a better result. For us it’s actually a good question and a good opportunity to ask what exactly they did in order to improve the results, because that’s exactly the lesson learned, we would like to share with the community and just understand what exactly things should be improved in order to get the accurate results.
Stephen:
I don’t think you’re a proper engineer unless you’ve stood up in front of other people and presented some results which you later find out are wrong. And it’s part of the game, what we do is difficult and that’s part of it. So when you look through these workshops, are there a variety of different approaches of people trying different ways? Because it’s not just simulating whole resistance these days, you have to take account with propulsion and propulsion systems. And so some of the simulations I see are more and more complicated and more and more simulating the whole vessel, including 1D models of engine propulsion, maneuvering, all those. So is there a kind of evolution of the best practice, would you say?
Dmitriy:
Definitely, there is a learning curve. We can see that participants, they’re actually improving the results, so basically there is some sort of convergence we can restore. But another interesting observation that we have is sometimes different participants, they put a lot of effort just doing, okay, we have a very fine mesh with millions of cells with a fully resolved propeller with everything done properly. And sometimes we see the results, actually it’s not as excited as it could be and someone is actually making a pretty coarse mesh, we know with a very simplified geometry.
And they actually might be pretty close to the results, so it’s kind of the main conclusion, it’s sometimes with the right skillset with knowing where exactly to make the mesh courser or when they make finer. So what exactly you should be focusing on, which boundary layer you should have put a bit more cells. It actually might help you a lot in terms of the simulation time, but at the same time give you a pretty accurate result.
Stephen:
The truth about engineering simulation is you want the simplest model that’s going to give you the right result, additional complexity where it’s not necessary, it’s an obstacle isn’t it? Because actually, doing this in a workshop is one thing, but when you have to do this practically day-to-day, simulating vessels every week, you can’t throw 6 billion cells at it, you have to have a practical solution. That kind of engineering expertise, a truth of what keeps us useful as well. On that note, have you noticed so far in any of your workshops, the appearance of any kind of artificial intelligence or machine learning aspects to some of the submission, or is it something you expect to see in the future?
Dmitriy:
I don’t think we’ve seen this now, but I definitely expect to see this in the future because actually, what we can see is the solution based on the experience, rather than on the actual mathematics. So basically, if you have run a lot of interesting simulation cases and then you can use the machine learning or artificial intelligence just to replicate this based on the already run simulation. So I think it’ll be quite an interesting scenario to [inaudible]
Stephen:
And combining data from different types of vessels and different operations, there’s lots to be done there, as well as basically learning some of this best practice and implementing it in the future as well. So it’s exciting time with regard to that as well.
Dmitriy:
We were just thinking about recently, we had an interesting chat about let’s say the car. In the car industry, it’s a pretty small object compared to ship. You can put the car in the wind tunnel straight away and just make all the measurements in the one-to-one thing, so you don’t need to have the smaller model. But obviously in the ship, actually, it’s quite difficult. It’s like this level of complexities, it’s normal.
Stephen:
Yeah. Some of this just occurred to me, is digital twins. Because in the car industry, have all their cars altered, they track every single car in their database, proper digital twins. I guess in the future, having some of this instrumentation on onboard ships permanently will provide kind of a constant stream of data. Is that something you think might happen in the future? I mean obviously, the trials you’re talking about are very specific and involve lots of tuning and making sure, you talked about all the detail you have to take up. But do you think there’s any future in being able to download data from operational ships and using that as valid simulation?
Dmitriy:
I’m not sure why you’re talking about the future, it’s already here. For the last, I don’t know, five, 10 years, actually a lot of ship owners, they’re recording a lot of data about the vessels. Basically even for our vessels, we have access to the long-term monitoring data and we see a lot of parameters like speed, power, RPM, fuel consumption, drafts, everything. But this actually-
Stephen:
Is it useful data?
Dmitriy:
Ah, that’s another question. That’s another question, yes. Now actually, the first phase, I’m not sure you probably heard about this, it was like ISO standard 9030 was established few years ago about the long-term monitoring data collection. And it was a significant wave, a lot of ship owners sounded like, “Oh, so cool. Now we can install a lot of sensors, we can just measure a lot of data and we’ll finally understand the actual condition of our vessels or our fleet.” And that was very exciting moment. And then when we actually established, not we, but the industry established all the sensors and we realized how much data you actually have, and it’s actually quite difficult to understand what’s actually behind this data.
Basically now, you can put all the plots and it’s massive, it’s a little bit cloud of points. And it basically, it’s quite difficult to understand, so what’s actually behind those? Now it’s a lot of project happening about and now it’s actually time for their artificial intelligence to help us to understand what’s actually this big data, it’s about. Because obviously, it’s a lot of data now happening in the market, so a lot of owners, they’re collecting. But at the same time it’s still not very clear idea how to make an interpretation.
Stephen:
And then every time I’ve been involved, it turns into a data cleaning exercise as much as anything else because all the data’s going to be dirty, there’s going to be problems. And so sorting out data, cleaning that data, maybe doing that algorithmically with machine learning, I mean, that’s a huge challenge. But in the future it’s going to give us more insight, I guess into how this real world, which is sometimes different in the way that you design them, which is another thing. I guess the lifetime of a typical big vessel is long, isn’t it? And so they’re designed for one set of operating circumstances, but I guess in practice during the lifetime of a vessel, they get reconfigured and reused. Is there much work done on existing vessels who are operating outside their original design spec or not?
Dmitriy:
Yeah, it’s a good question. Usually the vessel is designed for about 25 years and it means that, again, if we would like to have a zero carbon vessel by 2050, it means we need to start designing those vessels now. And at the moment we have no solution for that, so the only solution in the future, it’ll be actually a retrofit. Once a solution is found, few years [inaudible] so we should be able to retrofit just to have the existing vessel and fully do something on the vessel in all the NGO fuels or alternative fuel amplification. In that case it’s actually also quite exciting time. Now those companies which are building the vessel, they should think ahead and also about the possible retrofit. I’ll give you just a very good example. Just recently I’ve been to one of the GPRs, and they deliver the fast ferry. And basically, it’s electrical driven ferry.
It’s electrical motor, it’s actually inside the hull. But obviously, they need a generator to produce this electricity. They’re smart people and they installed the generator not inside the hull, but it’s actually on the deck. And they say that, well obviously now, it’s the solution because it’s like diesel generator, but hopefully in the next 10 years we need to replace this. And instead of cutting the hull and just taking this out of the hull, it’s actually already on the deck. So basically, it will just take them half an hour to unscrew these bolts, take them out this existing generator and put the new one in. It’s kind of the forward thinking about we need to build the vessel now, but in the future we’ll be able to replace this diesel engine with something else.
Stephen:
Something else, we don’t know what that something else will be at the moment, it could be anything.
Dmitriy:
Exactly.
Stephen:
That’s really interesting future proofing for an uncertain future.
Dmitriy:
Exactly.
Stephen:
Tell me a bit about the behind the scenes work that goes on in preparing these validation [inaudible]
Dmitriy:
Yeah, I think it’s a very interesting question because obviously, once we have the file shared, for instance, we’ll share the geometry of the vessels and we also give them some sort of indication about the hull roughness, which is a single value with CD practitioner should be used to simulate the hull roughness. But at the same time, I think it’s very important to say a few words how all these kind of parameters being achieved, because measurement of the hull roughness, actually, it’s quite a challenging task. Strictly speaking, there are a lot of uncertainties related to this. First of all, when we simulate the hull roughness, we should know the roughness in the water. But at the same time at the moment, there is no solution to measure the roughness in the water, so basically the only practical tool is actually to put the vessel in the dry dock and measure the roughness in the dry dock.
But again, so it’s not necessarily the values that we’re measuring in the dry dock will be absolutely the same as in the water because the environment is very different. But that’s kind of the assumptions we have to make because there is not a better solution. Basically what we do is we usually measure roughness in about 120 locations and the various positions of the hull, and basically just post process the data, make the assumption, what’s the roughness in the various areas and just have the power mean out of that. And also, we should do the same for the propeller roughness, just to make sure that in the CFD, it’s not like hydraulic smooth surface because in the actual propeller, it’s not smooth. Even though it’s might be polished, but it’s still not pretty smooth.
So basically what we do, we have this two component part which we apply on the surface of the blades, about five, six location per blade and then we send this to a special lab, have a scan and just know some sort of understanding of the roughness of each blade. Which again, might be different depending on the blade or depending on the hub and so on. And another thing, obviously these tiny things which are also quite important is about, let’s say the displacement and the draft, so the exact position of the bust in the water. In CD, just put the aft draft, forward draft and that’s it, but it’s actually how easy it’s to understand what’s actually the position in the water. Because usually before or after the trials, you see that there are waves and basically the draft marks, they’re all not the same all the time.
And so basically what we usually do is we record the draft with a video, with either drone or GoPro camera for at least one minute and then we just have the average based on that. And again, it might be the draft before the trials might be slightly different than after the trials. So basically, it says quite an instance so this might be coming out of that. What we usually say is obviously, we do everything as accurate as possible, all the measurements, the draft measurements, the roughness measurements and so on. But it doesn’t mean that they’re absolutely accurate, so obviously, there is an uncertainty in that measurement.
And that’s why usually it’s very important to make it very clear message that obviously, if we give you the speed and power curve from the trials, it doesn’t mean exactly this curve. It might be uncertainty associated with the various parameters, so this curve might be a bit higher or a bit lower. But it would be nice to know what’s actually the uncertainty level. For instance, for the tanker, we estimated the curve is about 4% to 6%. It means if you are pretty close to the curve in your CFD results, but not exactly on the curve. But at least within this 4% band, so it should be good enough because it’s exactly in the range of the uncertainty level for the trial.
Stephen:
That’s always one of the big challenges with engineering, is that halfway house between the experimental error and the computational error as well and trying to work out what the truth is.
Dmitriy:Exactly.
Stephen:
It’s usually somewhere in between those two areas and I guess that’s one of the big topics of conversation when you have these meetings.
Dmitriy:
Exactly.
Stephen:
Do people ever get quite precious about their results and convinced that their results are right compared with the experiment, or do you ever find people trying to explain away bad CFD contradicts the experimental results?
Dmitriy:
Actually, it’s very interesting point. Sometimes we can see on the conferences, someone run the CFD case and compare with, let’s say model test results. And they usually say, “Oh no, our CFD results is perfect. It’s most likely the uncertainty level from the towing tank, we don’t really know what kind of turbulent layer, so what was the [inaudible] where it was installed. And so basically, it’s quite interesting that the researchers, they’re trying to stick that their results are 100% and blame someone else who make the validation case. That’s why I’m pretty sure the people will be blaming us at some point, say, “Ah, these guys, they made the [inaudible] in a very accurate way, so that’s why we have 10% difference with our perfect CFD.”
Stephen:
Yeah, I think it’s one of the big problems. We’ve all experienced, we believe our models a bit too much. The old adage that all models and some models [inaudible] you have to be very humble. Sometimes your predictions aren’t right as well, so it’s good. Having that data set helps dispel some of the myths as well.
Dmitriy:
Yep, I fully agree with you.
Stephen:
Obviously, you’re involved with simulation, but do you ever get involved in any of the sea trials yourself and what kind of experiences have you had?
Dmitriy:
Yes, basically when I was working at Lloyd’s Register, obviously I was involved in a lot of sea trails. And now as part of the Jures project, we have opportunity to be on board and perform trials on the actual vessels. Out of the six vessels, I’ve been on board of five of them, so basically most of them. And actually, some of them were very, very interesting because obviously, it’s a very different focus compared to ordinary trials. Because one, usually vessel is delivered to the ship owners, so they usually focus in on specific areas like delivery, the speed that’s specific RPM and specific power, because that’s kind of the part of the agreement. But obviously, they don’t think that this case will be used for CFD validation. That’s why they don’t care, let’s say about how roughness about the measurements, the accurate measurement or the displacement.
They don’t care about the thrust measurements because it’s normally not part of the scope. And so in our case, obviously because we have a specific focus of CFD validation, so we need to be mindful and we need to do everything as accurate as possible. And some of the actual cases were very exciting. For instance, one on case on the cruise line was definitely probably the most unusual trials in my career, because normally the trials, they’re just performed on the brand new vessel. So when the vessel is delivered by the yard to the ship owner, it means it’s not part of the normal commercial operations. So basically, the vessel is not delivered to the owner yet, so it’s going to be on the stage of testing. That’s why vast majority of sea trials support they happen on this stage.
In our case, because we need to take the actual vessels which are actually in service, sometimes the communication with the owners might be quite weird, saying, “We wanted to make these trials on the cruise liner.” And we say, “We’d like to make trials on the cruise liner.” And the owner said, “Yeah, no problem, let’s do that.” But one of our requirements is actually, should be quite a deep water because we should avoid influence of the shallow water effect. And then owner said, “Yeah, it’s fine. But it means the passengers will be on board.” And I said, “Really? Is it okay with you?” And he said, “Yeah, we just make an announcement that we are in the middle of the trial. Say don’t worry if you observe some weird behavior of the vessel, it’s totally fine.”
And actually, it was quite exciting, so we made a proper reciprocal run. We run the vessel in one direction, make a U-turn, came another direction, another U-turn, came back, so basically made a few times. And all the time, 3,000 passengers was actually on board, enjoying their life. It was so weird being on the bridge and just being really focused about, we just another 10 minutes and then we just make a recording, we’ll make turn. And then we just step down from the litigation and you see people drinking alcohol, enjoying their life and so on.
Stephen:
As long as You didn’t make anybody spill their gin and tonics, I’m sure it’ll be fine. \.
Dmitriy:
Everything was good.
Stephen:
They were aware of it, it must’ve been quite an exciting story for them from their cruise.
Dmitriy:
Obviously, we made an announcement, saying that we are doing some very interesting research project, some specific trials, so don’t worry about the vessel going back and forth. But to me, it definitely was quite unusual experience performing trials with the passengers onboarded is something very new.
Stephen:
Do you get seasick or not?
Dmitriy:
It’s another actually interesting point. Because normally for the trials, we need the sea condition as calm as possible, because obviously, the first phase is just to have the CFD validation keys for the calm water condition. That’s why we usually see on the calm water condition, that’s why in those conditions, quite hard to be sea sick.
Stephen:
That’s good as well, which is a relief for you as well, because I’m sure your best work when you’re not leaning over the side of the vessel.
Dmitriy:
Yes, definitely.
Stephen:
Do you have any more trials planned, coming up?
Dmitriy:
This project, we are about to finish this project in October this year. We completed all the trials we actually wanted to do for this project. But at the same time a lot of participants, they’re asking us what’s next, whether it’s going to be continuation. Because there are a lot of things we can do in the future, let’s say on the water radiated noise, which is actually quite a hot topic now. Looking on the different environments, not only on the hydrodynamic side, but let’s say the fluid structure, interaction things, vibration analysis. So it’s quite a lot of things we can do in the future. That’s why we’re thinking how to shape, how to make it the phase two of the project starting from the next.
Stephen:
And will there be a phase two?
Dmitriy:
I am 100% sure, yes.
Stephen:
That’s really exciting. I think it is always exciting, we talk a lot on this podcast about simulation but not enough about validation. So it’s really exciting to me that you are [inaudible] putting the effort in to make sure we have a proper validation data set for which future generations of naval architect, to make sure that we can solve these massive challenges we have to face. As you say, it’s not about making 10% changes, it’s about tuning everything by 1% or 2% to kind of get these massive energy savings out. And so it’s a really exciting time, so thank you very much for talking us through that and it’s been a really interesting talk. Thank you, Dmitriy.
Dmitriy:
Thank you, thank you.
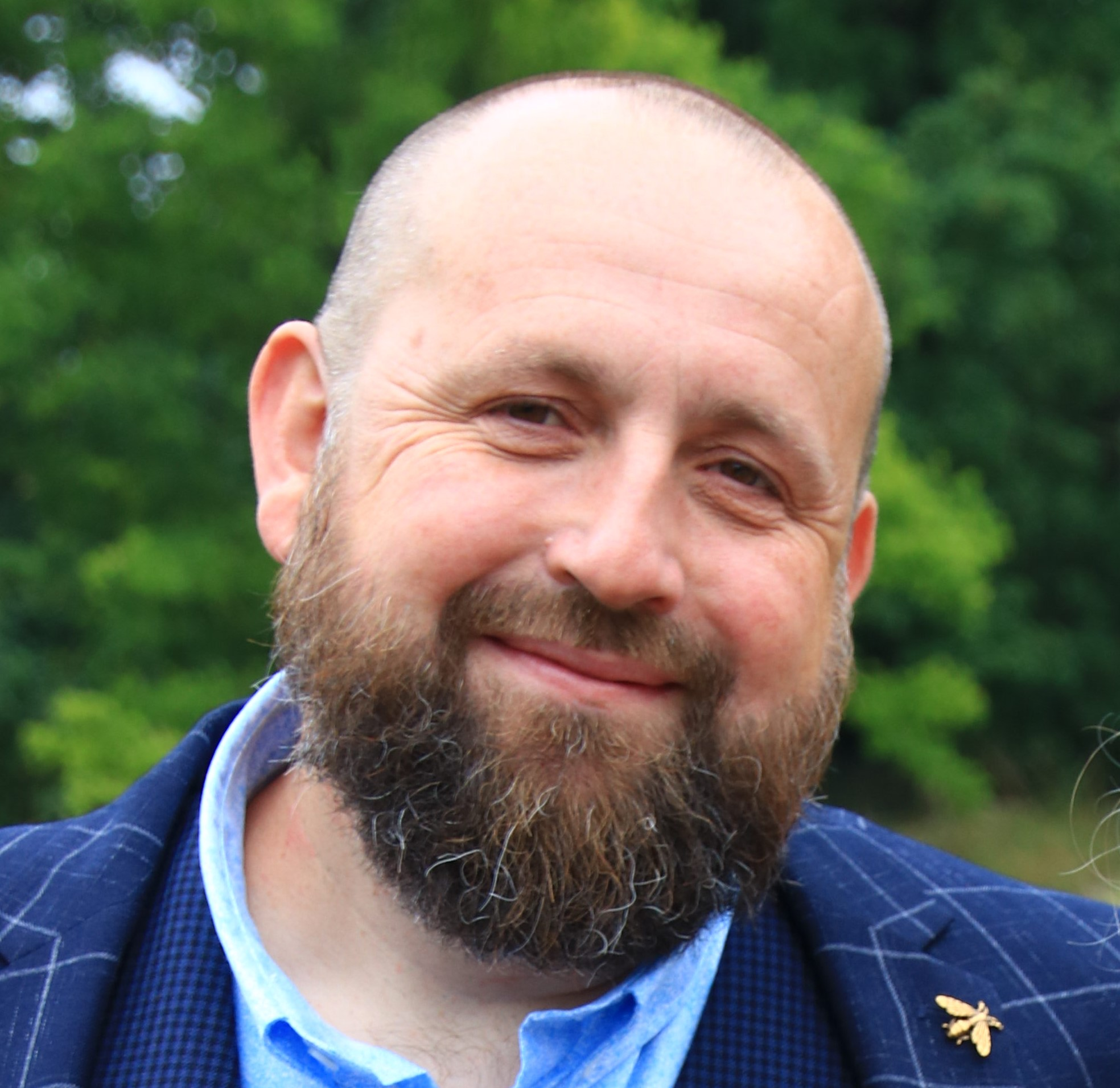
Stephen Ferguson – Host
Stephen Ferguson is a fluid-dynamicist with more than 30 years of experience in applying advanced simulation to the most challenging problems that engineering has to offer for companies such as WS Atkins, BMW and CD-adapco and Siemens. Stephen’s most frightening experience on a boat a 1990 ferry crossing from Newhaven to Dieppe in force 9 gales, on which everyone else was sick. Stephen does not get sea sick.
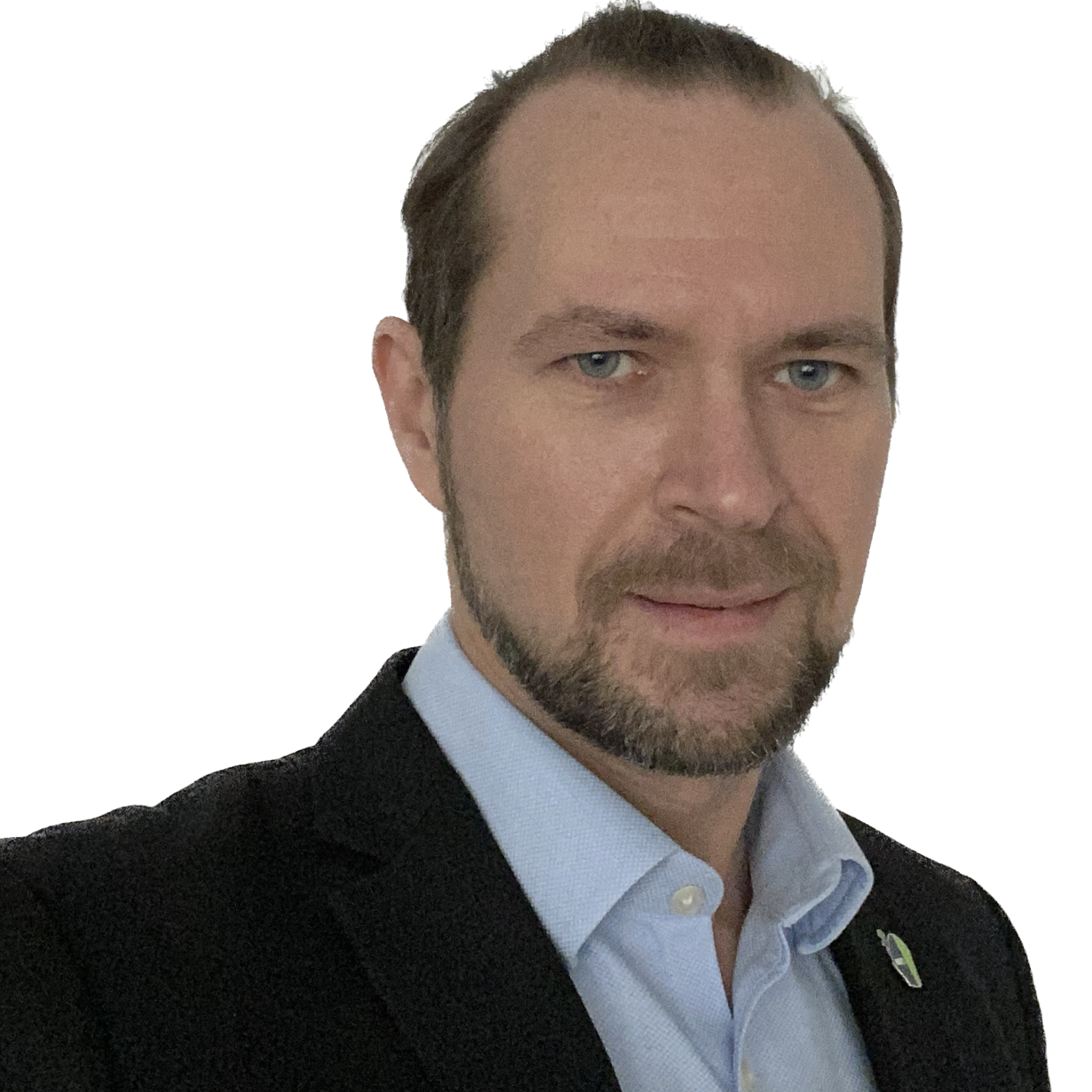
Dmitriy Ponkratov
Dmitriy Ponkratov has a PhD, an MBA, and is a naval architect with international experience gained in China, Norway and the UK. He worked as an associate professor at the Norwegian University of Science and Technology and a senior consultant at the world-renowned Technical Investigation Department at Lloyd’s Register. Currently, he holds the position of Technical Director at the Royal Institution of Naval Architects.
Take a listen to the previous episode of the Engineer Innovation Podcast: “Adapting to a New Era of AI”
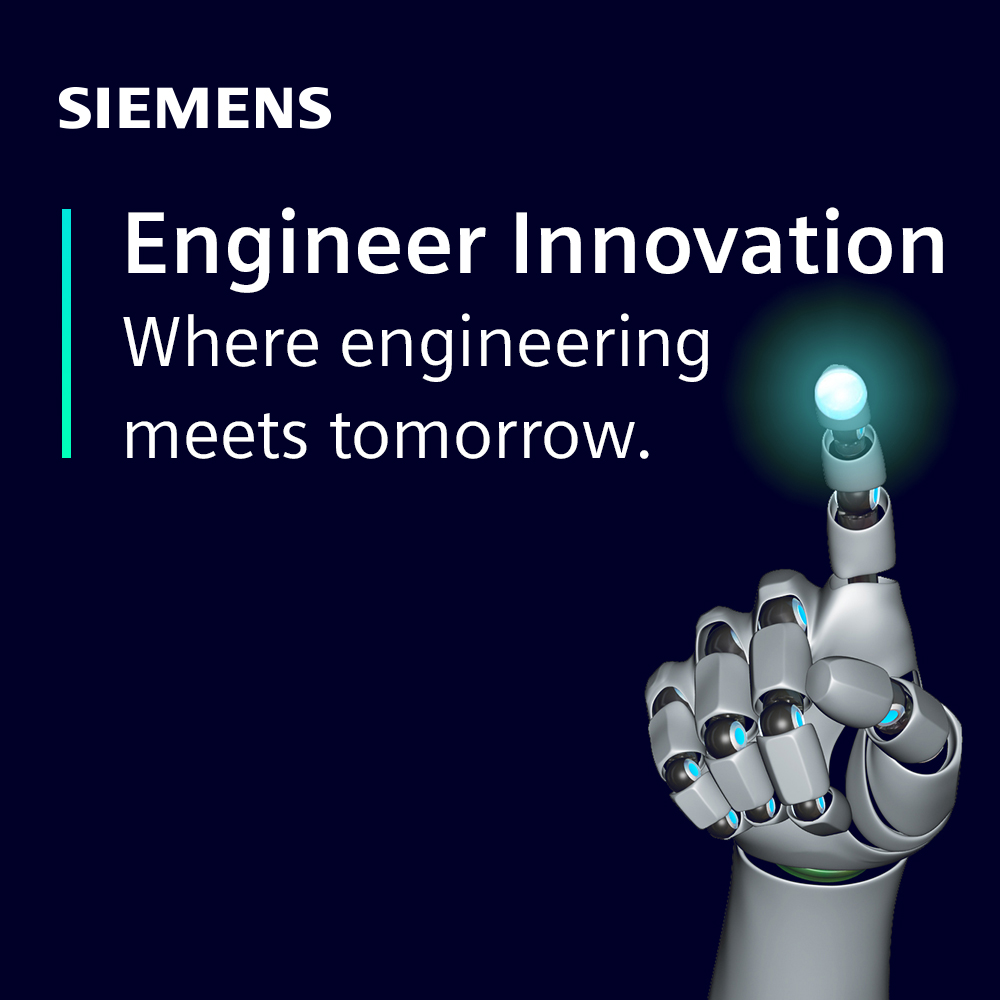
Engineer Innovation Podcast
A podcast series for engineers by engineers, Engineer Innovation focuses on how simulation and testing can help you drive innovation into your products and deliver the products of tomorrow, today.