Advancing Electric Motor Design and Simulation with Adrian Perregaux
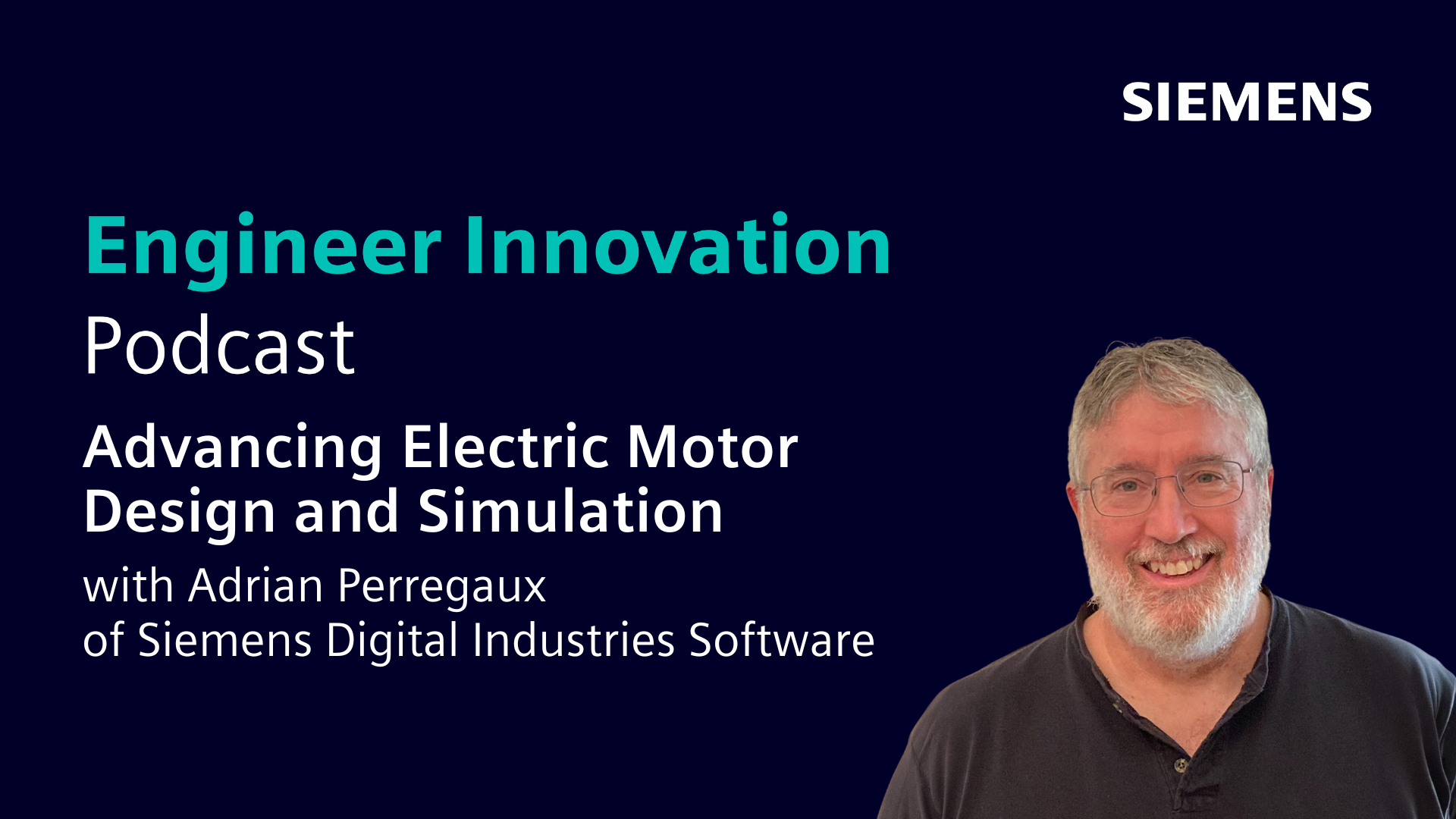
Listen to the Engineer Innovation podcast on
In this episode, we’re joined by Adrian Perregaux, Product Manager of Electromagnetics at Siemens Digital Industries Software, His team focuses on low-frequency electromagnetic solutions within the Simcenter portfolio. Adrian shares his insights into the evolving world of electric motor design and the role of simulation software in enhancing this process.
Key Takeaways:
- (02:33) What Adrian finds appealing in electric motor problem-solving.
- (05:07) The complexity in motor design is due to the non-linear behavior of electromagnetic steels.
- (07:50) Efficiency trends in motor design driven by global electricity consumption.
- (14:36) Early software development technology limitations.
- (16:00) The introduction of Simcenter Speed and Simcenter Motorsolve.
- (21:12)The upcoming release of Simcenter e-machine design.
Resources Mentioned:
This episode of the Engineer Innovation podcast is brought to you by Siemens Digital Industries Software — bringing electronics, engineering and manufacturing together to build a better digital future.
If you enjoyed this episode, please leave a 5-star review to help get the word out about the show, and subscribe on Apple or Spotify so you never miss an episode.
Find the show on your favorite pod catcher: Engineer Innovation podcast.
- What Adrian finds appealing in electric motor problem-solving.
- The complexity in motor design is due to the non-linear behavior of electromagnetic steels.
- Efficiency trends in motor design driven by global electricity consumption.
- Early software development technology limitations.
- The introduction of Simcenter Speed and Simcenter Motorsolve.
- The upcoming release of Simcenter e-machine design.
Adrian Perregaux:
When that software first came out, there were no things called hard discs. There were floppy discs and most people don’t even know what a floppy disc is today. Monitors were monochrome. Maybe you had three colour. So you’re talking about at the cutting edge of technology at the time for desktop computing, and now most of us have a phone that’s a thousand times faster and more capable than it was. So that’s the kind of scope you’re talking about.
Chad Ghalamzan:
Hello, I’m Chad Ghalamzan, and welcome to the Engineer Innovation Podcast. 30, 50, 100? How many electric motors do you think are spinning around you right now? These omnipresent devices can be found in applications from household appliances and transportation systems to power generation and industrial machinery, encompassing a broad spectrum of uses. While they may operate on a relatively simple principle, the apparent simplicity of this fundamental concept can be deceptive. The design and construction of electric motors can vary wildly. The complexity often depends on the specific application and requirements.
My guest today is Adrian Perregaux. He’s here to talk about all of this and some exciting changes to the Simcenter portfolio when it comes to electric motor design. Hello, Adrian. Why don’t you introduce yourself to our listeners?
Adrian Perregaux:
Hi Chad. I’m Adrian Perregaux. I’m one of a small team of electromagnetic specialists who are developing the Simcenter software.
Chad Ghalamzan:
And you have a pretty great career in electric motor design. You bring a lot of experience to the table on this topic. Could you maybe share some of the highlights from your journey in electric motor design?
Adrian Perregaux:
Sure. I’ve been working with electromagnetics since 1983 and I have worked on small motors for robotic pick and place applications or large wind generator or defence related machines, and have a wide spectrum of opportunities and experience with different software. And I’ve been with Siemens for 12 years now, working on electromagnetics.
Chad Ghalamzan:
And what do you think led you to have this career path? Is there specific interests in electric motors?
Adrian Perregaux:
In general, I got interested in electric motors and electricity and electronics when I was a young boy in elementary school and I got really curious about how things work. And so I just explored that and then followed that with my studies, and now with my extended career.
Chad Ghalamzan:
And is there anything about them that you found interesting that made you continue on that path? Is it the uses? Is it the complexity of the design? What is it about electric motors that you think was so appealing to you?
Adrian Perregaux:
Fundamentally, I think it has to do with the problem-solving and trying to figure out how the materials are going to coordinate with one another in order to deliver the end torque or the end result for the machine.
Chad Ghalamzan:
As I mentioned in the intro, electric motors are almost everywhere and that they’re such a fundamental part of modern life, but they vary so much in size and use and applications. What do you think are some of the challenges that come with working on such a device that can be used in a multiple of designs and uses?
Adrian Perregaux:
It all comes down to the crux of the end application, but typically that’ll put constraints on the size of the device and the amount of heat that it can actually dissipate. And then all of that works together as a big puzzle, and the engineers that are involved try to do their best and historically they did trial and error and they tested things in the lab from a physical prototype. And so the joy of my career actually has been to work on simulation software to help them do that sort of prototyping on the computer. And so it’s been beneficial and interesting for me to participate that way.
Chad Ghalamzan:
You mentioned heat, you mentioned size. These are some of the constraints that go into the design of an electric machine, depending on its application. Heat, size, is that the two big ones? Is weight one of them? What about materials? Right now especially, what are the key constraints or key design difficulties that an electric motor designer is probably encountering?
Adrian Perregaux:
Typically, weight and package size. You can’t just have a machine that’s the size of an elephant driving a car. There’s going to be an envelope or a small space that is going to be required to fit in. That directly impacts the kind of cooling that you need. You also mentioned materials. We are highly dependent on our permanent magnet materials from China and there’s an impetus or an emphasis to reduce the amount of volume and the risk associated with using those sorts of materials. So that all goes into the puzzle. It’s not always physics.
Chad Ghalamzan:
So this is going to sound probably to you like a very dumb question, but when we need a small motor, why don’t we just take that motor and make it so big? And then when we need a big motor, we take the same design and just scale it up whatever many times to make it the size we need? What’s all the complexity here then? Why are they so complex to design?
Adrian Perregaux:
In general, the machines are not scalable and there’s limitations. Why aren’t they scalable? Because the material properties are not linear. Outside of most other materials, electromagnetic materials are highly non-linear and the general scaling of a water pipe or a water tube or something, you can change the cross-sectional area and increase the amount of water that can go through it. Well, you can’t necessarily do that with electromagnetic steels because the materials don’t have that linear behaviour. They’re highly non-linear with slopes on the order of 10,000 to 100,000. So you have all of that goes into the puzzle and makes it much more difficult to do that sort of more simple scaling.
Chad Ghalamzan:
And obviously there’s different topologies here. We’re not talking about just one type of device, electric motors comes in many different flavours as well. What are some of the different configurations that you’ll see in electric motors?
Adrian Perregaux:
Probably the most widely accepted construct is called a radial flux motor. And that generally means that all of the magnetism in the flux resides in a single plane. An axial flux machine is a second type of machine and it actually implies that the flux travels through more than one plane. And the complexity of the overall design is incumbent upon how they understand how that flux is going to work and how that channels into the energy or the torque that’s developed.
Chad Ghalamzan:
How do we generate that flux? That’s where some of the differences come as well, right? There’s not just one way to build an electric motor, there’s a whole range. So do all of these nuances make it very difficult then to come up with a solution then that all the potential end users of the software will be able to take that tool and do the work they need to do because it’s so varied in terms of usage and ways the device can be constructed?
Adrian Perregaux:
Really good question. Basically what we have to do is try and guess at the highest probability of users that we could get because we can’t possibly encompass all of the possible configurations. Yes, in general, the way that you generate magnetism reflux is with a current-carrying conductor. And so anything that has a current running through it is going to generate magnetics. And thankfully, we have additional kinds of devices called permanent magnets which store that energy. So most people don’t know it, but permanent magnets don’t have an energy and can’t exhibit magnetism unless they get charged. And that charging comes from a very large magnetic pulse from a series of coils. And once it has experienced that energy, then it can keep it.
So whether you have it on your fridge to hold up a calendar or whether you’re actually using it in your electric motor for your electric vehicle or whatever application you’re looking at, it’s a storage device. And so we take advantage of those and take advantage of cleverly a range conductors to generate the magnetism that we need in these devices.
Chad Ghalamzan:
So there are some common principles or some design principles that need to be respected here, but there is still quite a bit of variation that comes into play, again depending on what the constraints are, what the size is, what materials you’re using, what kind of motor, configuration you have. One thing you haven’t mentioned so far is efficiency. Efficiency comes in many forms, but here, I’m going to talk specifically about power efficiency. We’ve seen the global rise in electricity consumption due to a number of factors. Is creating electric motors that are more electrically efficient also a trend that’s influencing how they’re being designed and built?
Adrian Perregaux:
Oh, absolutely. In fact, you probably can’t find a municipality or a region or a country that doesn’t have regulations imposed on them for improved efficiencies. In general, efficiencies come in the form of the conversion of energy, in the form of heat, and you can’t really get away from a minimum of that. And so we’re pushing that envelope. A lot of machines now are upwards of 90% efficient and the designers are pushing that envelope, but in general there’s going to be a maximum of which they can deal with that. And because you’re always exciting, as I said, some form of conductor, and when you excite a conductor to generate electricity and magnetism, there’s always going to be some form of losses from that energy and the current passing through it, and that translates directly to heat. And so that will always be something we’re fighting against, but we’re getting very clever and we’re doing a lot of machines now are upwards, as I said, of 90%.
Chad Ghalamzan:
And when it comes to dealing with heat as well, I think there’s a lot of challenges that come into play in terms of how that heat is either dissipated or regulated. And that’s another key component in terms of how a motor is built or its operation, whether you’re able to passively or actively cool it?
Adrian Perregaux:
Yeah, in general, the machines of yesteryear were over-designed and they had a large enough volume and mass so that they didn’t need exotic or special cooling. That’s all changed in the last 10 to 15 years. And since then, we’ve had to have more active force convection cooling with fluids passing through and in the machine to remove that heat for us. And so there are some really exotic ways of doing that, but in general, there has to be some form of cooling fluid that passes through the machine to remove the heat.
Chad Ghalamzan:
And I guess another critical aspect to the usage of these devices that we haven’t talked about would be the controlling mechanism behind it or what is driving the motor. Because as much as we’ve talked about what goes into building or designing them, they do need some sort of controlling mechanism when they’re in operation to either spin it at the right speed or control its position if it’s a position-controlled motor. Is that also a critical part of the design process and what challenges does combining that aspect with the machine itself bring?
Adrian Perregaux:
It brings a lot, if you want to call them that. The control or the drives and control engineer is typically a completely different department than the motor designer. And so those guys have to communicate, they have to exchange information, and you’re hoping that they actually can provide the most optimum machine based on that. And Simcenter’s tools allow them to more easily and more cleanly collaborate to do that.
But you have a really good point because an electric motor in an elevator made by an Otis elevator has a very interesting design spec because anytime any human gets into the elevator and once they go up four floors or down 10 floors or something, the machine has to deliver the torque that it has and in essence, they need an unlimited voltage. However, with an electric vehicle, the voltage is capped because there’s only so much battery and there’s only so much voltage that can be delivered. And so the engineers have completely different puzzles, so to speak, to come up with and problem-solve when they’re doing just those two different kinds of applications for the motor.
Chad Ghalamzan:
And then even when you look at those two applications that you mentioned, elevators and vehicles, when it comes to elevators, on top of everything you mentioned, when you’re looking at a large building that might have several units in operation where they are at a resting position when there’s no surface call, versus when they expect the next service call to come in and optimising where they should be or which floor they should be waiting at, goes into improving energy consumption efficiency there.
Adrian Perregaux:
Absolutely.
Chad Ghalamzan:
And the same thing with vehicles. When we look at how vehicles are driven, range, what’s their time to recharge and how quickly do we need a vehicle to be recharged? Is it on a set path? Then again, we could always expand these problems into a larger context and then take all these principles we’ve been talking about to another level of we’re looking at the entire system. So obviously they’re everywhere and they’re in every facet of, like I said, our modern life. But maybe before we talk about where we are today, we can go back, what? About 30, 40 years ago to the University of Glasgow, and I think where I’m going with this question, it was around then that a professor from this university came up with an idea. Maybe you could tell us what was his idea and in its context, in its day, how was that revolutionary at the time?
Adrian Perregaux:
Wow, it was revolutionary from lots of levels. The first level is that electric machine designers at that time had very little in the form of tools. They had some basic relationships for how the machine was going to perform or at least how they thought it would perform. They maybe had a slide rule or they did long division in math on pieces of paper. There was no such thing as a computer, certainly no such thing as a desktop computer. And this software and the concepts that you’re talking about from the University of Glasgow was revolutionary in the sense that it combined some theories about how a machine would respond, mapped it into an electric circuit equivalent model and then used a computer to solve that and predict machine performance.
And so that allowed electric machine designers all over the world to have a much better perspective on the scope of their design and how to problem-solve it in order to deliver the optimum machine.
Chad Ghalamzan:
If we’re going to talk about origin stories, which are often used in comic books, that’s the origin story for Simcenter SPEED.
Adrian Perregaux:
That’s correct.
Chad Ghalamzan:
Developed out of University of Glasgow, right? And it’s hard to maybe state just exactly how much knowledge and theory behind motor design got compressed into that tool at the time.
Adrian Perregaux:
The theory of electromagnetics and motors got wrapped into it, got wrapped into its tutorials. The founder that you’re talking about also co-authored multiple books associated with the performance of different motors. He had a mission to help electric machine designers around the world to better their designs.
Chad Ghalamzan:
For a very long time, it was a very popular tool used by engineers in a variety of industries across the globe really. And I know at one point in your career you were involved with that software directly. And again, it was reflective of the capabilities available at that time in terms of computational power because we’re always limited by the possibilities of what the technology at that time enables us to do. And at that time, you had mentioned desktop computing was a relatively new concept and did not have the power and memory capacity that the machines do today.
Adrian Perregaux:
I think it’s important to underscore that a little bit because of the nature of everybody’s perspective today. When that software first came out, there were no things called hard discs. There were floppy discs and most people don’t even know what a floppy disc is today. Those are five and a quarter inch floppy discs and the computer booted up on it. And if you had something you wanted to save, you would do that as well. Monitors were monochrome. Maybe you had three colour. So you’re talking about at the cutting edge of technology at the time for desktop computing, and now most of us have a phone that’s a thousand times faster and more capable than it was. So that’s the kind of scope you’re talking about.
Chad Ghalamzan:
Most people listening to this podcast probably don’t remember the frustration of reaching disc 404 to find out that it was corrupt and didn’t work and you had to start the whole process all over again. But that’s something some of us may remember with lots of pain. If we jump ahead, probably to the next step in the desktop computing evolution, we get to advanced graphics, we get to Windows-based machines, we get to a whole different era. And then we have an increase in computational power and memory and computers started having hard drives, which is a big thing too, and internet connections. And then we have this advancement that allows for more than just what Simcenter SPEED offered.
And then that’s probably a good place to maybe introduce where another tool in the Simcenter portfolio, this origin story came from, and that’s actually where our friendship origin story comes from because probably when we first met and started working together was on a product called Simcenter Motorsolve. So maybe you can help, again, give some context to Simcenter Motorsolve in this story and how it impacted motor design at the time?
Adrian Perregaux:
Well, Simcenter Motorsolve is very similar to Simcenter SPEED. Its fundamental basis is based on circuit model equivalents for the behaviour of a machine. However, one of the fundamental core differences is that Simcenter Motorsolve relied on a new concept called the finite element method or finite element analysis. And that meant that we could set up the geometry of a motor and actually solve for the torque and the real physics associated with the thing going around. And then we could use that information to calibrate or to modify the constructs within that circuit equivalent. And that significantly improved the accuracy and then coupled both of those concepts into a very fast, very efficient simulation result for our users to be able to very nicely virtually prototype their electric motors.
Chad Ghalamzan:
Maybe just to make it more clear for people listening, we’ve been asked many times too, how are Simcenter SPEED and Simcenter Motorsolve the same?
Adrian Perregaux:
They’re very similar in several ways. One of those ways is they’re both template-driven interfaces, which means that the user doesn’t have to enter any CAD, they don’t need to enter any mesh, they don’t need to enter any very laborious setups to run their experiments. Instead, they can concentrate on using a template to enter the topology of the rotor, enter another template and review the topology of the stator. And then they can choose from among say between 10 to 20 different experiments to review the performance of that motor.
And so from that standpoint, they’re all very similar. The differentiator is that SPEED has the reliance on that circuit and Motorsolve has that circuit and relies on finite elements to give it an extra calibration and a higher fidelity associated with the data and the solution.
Chad Ghalamzan:
So we talked about the past. Let’s talk about today again. Having these differences that you just mentioned, how are they still relevant to someone today to have both of those methodologies available to them when looking at designing an electric motor?
Adrian Perregaux:
That’s a good question. In general, the SPEED software has a really good capacity for developing, call it a first pass design, where you can go through a large filtration of ideas and come up with the construct for the number of poles for the rotor, the number of slots for the stator and some approximations for how the general machine is going to run within the constructs and restrictions and requirements that you have. Then you can utilise Simcenter Motorsolve as an additional fidelity. That means things like you can review eddy currents that might get induced in the permanent magnets. Or you can review saturation effects in the steels and get into what I would term second order or more fundamental effects of the phenomena of the physics, which because we’re pushing the envelope all the time with the designs, these sorts of things creep in, start to be prevalent and you have to be very careful of them.
Chad Ghalamzan:
So to use a poor analogy, as we mentioned at the beginning of this conversation, when you’re looking at electric motor, they’re so diverse. There’s so many different ways the design can be thought of to meet the requirements given, that’s like a whole big map. Would it be a clunky analogy to say that Simcenter SPEED would first get you in the right neighbourhood and Simcenter Motorsolve might help you find the address a little bit easier?
Adrian Perregaux:
That’s a really good metaphor.
Chad Ghalamzan:
So there’s obviously benefit to having both. There’s obviously a lot of ways that even though some of this initial concept of technology was developed back in the 80s, it’s still relevant today to have available to electric motors designers. I presume there’s only more and more demand for more and more novel electric motor design tech as paradigms to meet our growing need. But still, again, the principles may be simple. The deception is how we actually build the device, but there’s only so many different ways you can build a machine that spins, but that doesn’t mean it’s easy for us to right off the bat, know how to pick and choose the right design configurations to meet the needs.
So it sounds like having both of these in one tool would be beneficial, and it’s my understanding that’s what you’re here to talk to us about today, how Simcenter SPEED and Simcenter Motorsolve are moving to the next step in their natural evolutionary process.
Adrian Perregaux:
Absolutely correct. The development teams of both products have been meshed and melded together into one. And over the last year and a half or so, we have made a concerted effort to unify the products. The new product is going to be called Simcenter e-machine design, and what we’re going to do is we’re going to take the best of the best from both of those and put them in this new software. And so it’s going to be really exciting for our present users and our future users because it will allow them to do a wide range of different kinds of machines and to go from original concept to a full test of the design through the process.
Additionally, it will, because it’s part of the Simcenter suite, allow them to explore the machine within a system. It allows them to exchange data and do noise vibration and harshness or structural assessments and acoustic assessments to see if the entire machine passes. Got to make sure that we understand. The puzzle here isn’t just to develop a really cool electric machine. We have to develop a really cool electric machine that fits in within a system, and that means we have to have thermal considerations, we’ve got to have electrical considerations, we’ve got to have mechanical acoustic noise. All of that has to be incorporated into a very interesting multiphysics assessment, and the suite of Simcenter tools is really the only one in the marketplace that allows you to combine all of those things in a holistic way to look at what you might want to call the powertrain or the ability for the full system to be assessed.
Chad Ghalamzan:
Yeah, there’s many design factors that go into a machine. There’s the performance of the machine itself, based on, like you said, torque and heating dissipation, but then when you’re looking at noise, vibration, these things, structural integrity, these things also come into play. And noise too with electric vehicles. Noise isn’t about loudness. Noise is about avoiding that annoying hum or that range of discomfort that we have when the sounds are at a low enough frequency that we can detect.
So there’s obviously such a variety as well in terms of how these machines get used and what the requirements are for all of those additional parts to the puzzle.
Adrian Perregaux:
And it extends to really interesting applications like CPAP machines, which help people with sleep apnea to go to sleep. If that was a noisy machine, it wouldn’t be of any assistance. All of us who have dishwashers,
Chad Ghalamzan:
Dishwashers, yeah.
Adrian Perregaux:
or refrigerators in our kitchens, you certainly don’t want that thing clanking and making a lot of noise.
Chad Ghalamzan:
No. Front-loading washing machines is another one where completely changed… And then there’s the maintenance of all of these as well, so you have to consider operation and use. So there’s so many different factors that make these such a difficult thing to design and conceive for its end usage.
Adrian Perregaux:
Correct.
Chad Ghalamzan:
So Simcenter e-machine design, this is part of the Simcenter mechanical portfolio. Is there any integration with the rest of the portfolio that’s worth noting?
Adrian Perregaux:
Sure. There is a direct connection to our design exploration software called Simcenter HEEDS, and you can actually utilise a portal there and it will read a machine design motor file and all of the parameters that describe the topologies are available for review as an input. And then all of the experiments that you might want to run are available as outputs, and then you can run a study to review and obtain the optimum type of machine, but you can also exchange directly data files for the performance of the machine as a behaviour model or reduced order model and exchange it with Simcenter Amesim, and review the machine in a full drive cycle or review the machine with a thermal network, or review the machine with drives and controls, and all of those are possible.
You can also then exchange force data from the machine with Simcenter 3D, and that force shows up as an input to a structural or an acoustic simulation. And so you can directly look at how your machine will generate noise. As you mentioned, the ear can hear between 200 hertz and roughly 4,000 hertz, and you definitely don’t want to have an electric vehicle generating 3,000 hertz and drive all your customers nuts because the reality of the frequency is just not pleasant. That’s all part of this puzzle and long since time ago, we can no longer just look at the electromagnetics and assume that we have the answer. It definitely has to be a multi-attribute type of assessment to get the best solution.
Chad Ghalamzan:
And the trade-offs involve when you’re considering so many different attributes to achieve the right balance for the right usage. It’s the same constraints. It’s a good, if you would, example to use when we’re looking at what an engineer focuses on in terms of a workflow with the entire product that they are associated with because electric motors are very rarely the product. They’re just the component in the product, but they’re usually one of the most critical components and device depending on usage, obviously, but most of the time they’re the most critical ones. So even though they get packaged and that’s why they’re so omnipresent, we don’t always realise they’re there. They are a really key component, so versatile, so difficult to design sometimes.
What do you see as the next step then for Simcenter e-machine design in terms of what would be down the line for the next release after this coming one?
Adrian Perregaux:
One of the things that this particular release highlights, which is really cool, is one of those unique topologies that we talked about. Historically, Simcenter SPEED and Simcenter Motorsolve concentrated on the radial flux type of machine, and in the last three to five years, there’s been a huge influx of new ideas and new manufacturers of machines that are utilising the axial flux machine. And so Simcenter E-machine design has axial flux machine capability. And so that first release that’s coming out in a week or so will highlight that technology. That first technology is only going to be available with a lump parameter circuit model.
And so the second part of this, what I’m really excited for, is that the machine will actually, in the next release, have the ability to use finite elements to calibrate the physics and give us that second-order feel that we need in order to have a complete or as complete a solution. That’s going to be available. We hope to have direct ties or additional ties to other kinds of software like maybe durability and rotor dynamics and things of that sort, to more fully complete the attribute assessment as the machine is part of that bigger system.
Chad Ghalamzan:
Sounds like there’s great things ahead. Adrian, thank you so much for coming on the podcast today to talk about the changes coming to the Simcenter portfolio. I think it’s really interesting and it was really great talking to you about this and I hope you had as much fun as I discussing this today.
Adrian Perregaux:
I did. Thank you very much, Chad.
Chad Ghalamzan:
Simcenter e-machine design is part of the Simcenter mechanical 2312 release, which includes products like Simcenter 3D and Simcenter MAGNET. As part of the integrated portfolio, data can flow from Simcenter e-machine design to Simcenter 3D for an end-to-end integrated workflow for EV powertrain development. A What’s New in Simcenter Mechanical 2312 is scheduled for January 30th, 2024. Check the show notes and our website for more details about this event. I’m Chad Ghalamzan. Thank you again for listening to the Engineer Innovation Podcast.
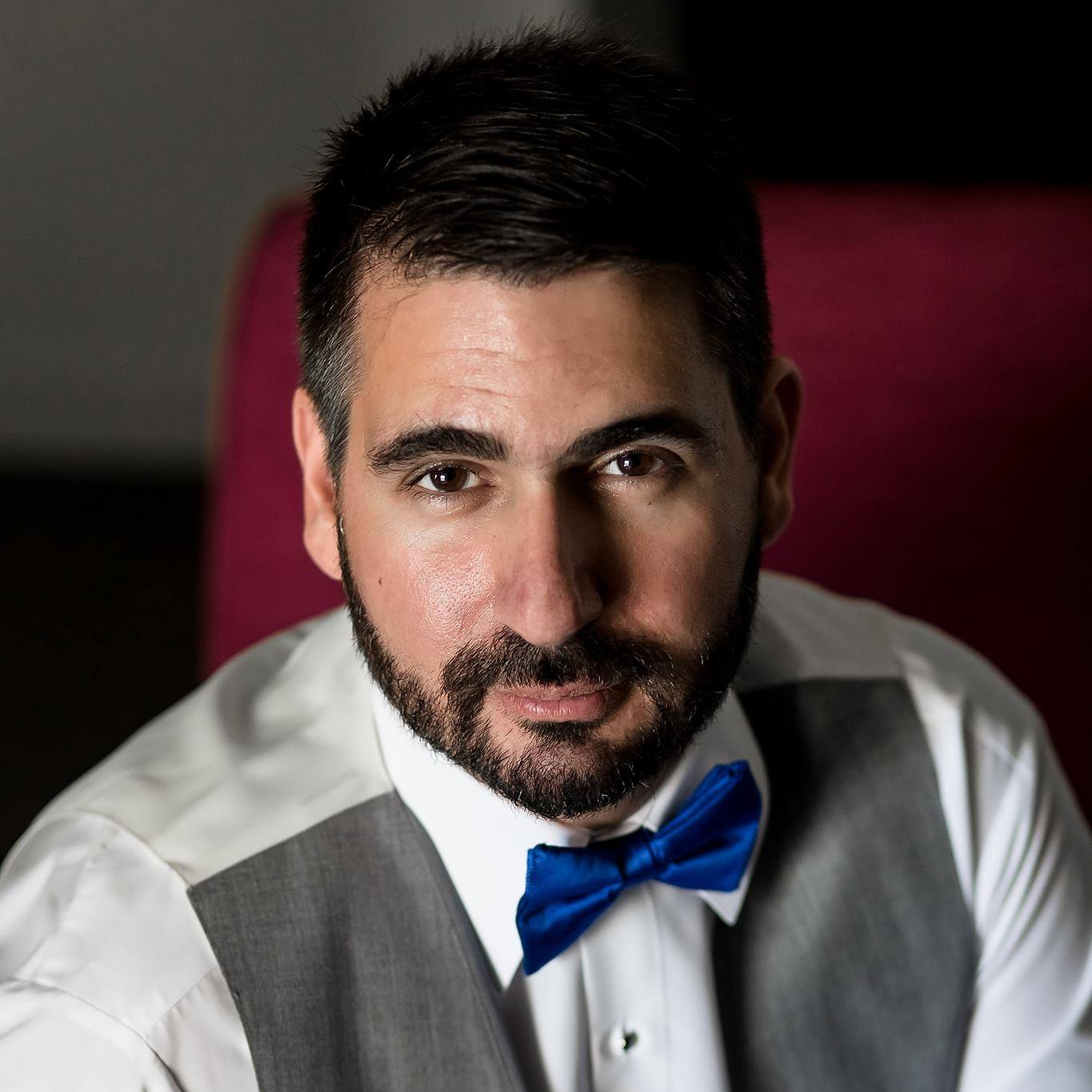
Chad Ghalamzan – Host
Chad Ghalamzan is a computer engineer with over two decades of experience in sales and marketing for the simulation and test industry. He co-hosts the Engineer Innovation podcast and creates content for Siemens Digital Industries Software. He’s tired of people calling him ChadGPT.
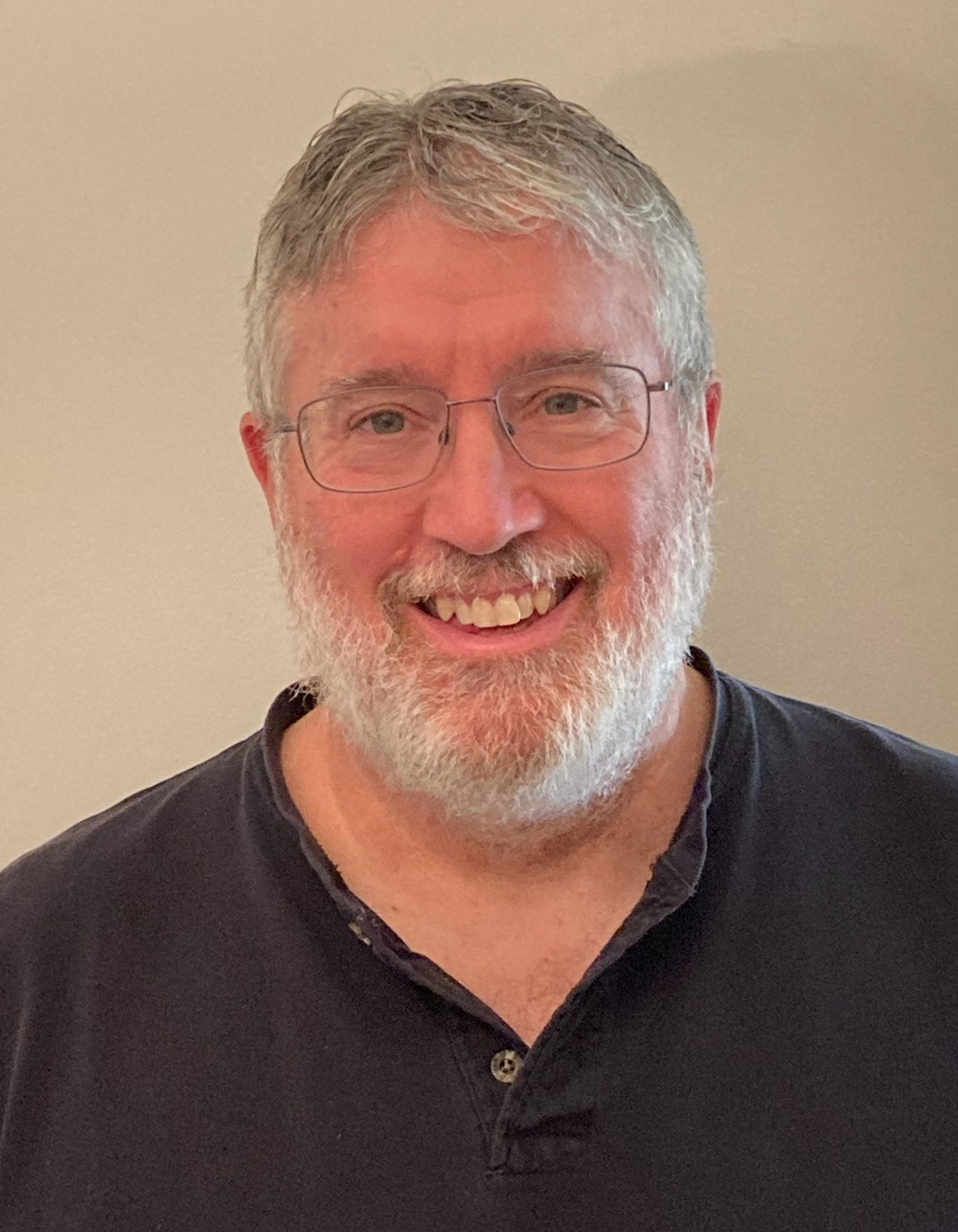
Adrian Perregaux
attended Bowdoin College in Brunswick, ME, USA for his undergraduate studies. Adrian concentrated on Mathematics & Physics and graduated with Honor’s in 1983.
Adrian pursued his graduate studies at Carnegie Mellon in Pittsburgh, PA, USA; he concentrated his research and studies on magnetism, magnetic materials and their applications. He received a Master’s of Science degree in 1986.
Adrian celebrates a Senior member status of the IEEE where he has been a long-standing member and volunteer.
Adrian’s career has continuously focused on magnetism. Where his experience has been split between :
- The design, understanding and manufacturing of devices
- The development and support of simulation software tools to assist in the design of such devices
Adrian has worked as a part of the Siemens team for over 12 years now. His current role is a Product Manager for their Electromagnetic simulation software.
Take a listen to a previous episode of the Engineer Innovation Podcast: Engineer Innovation: Conversations about Industry 4.0, Engineering AI/ML, Digital Twin, & Computer Aided Engineering.: The Evolution of The Digital Twin in Industry on Apple Podcasts
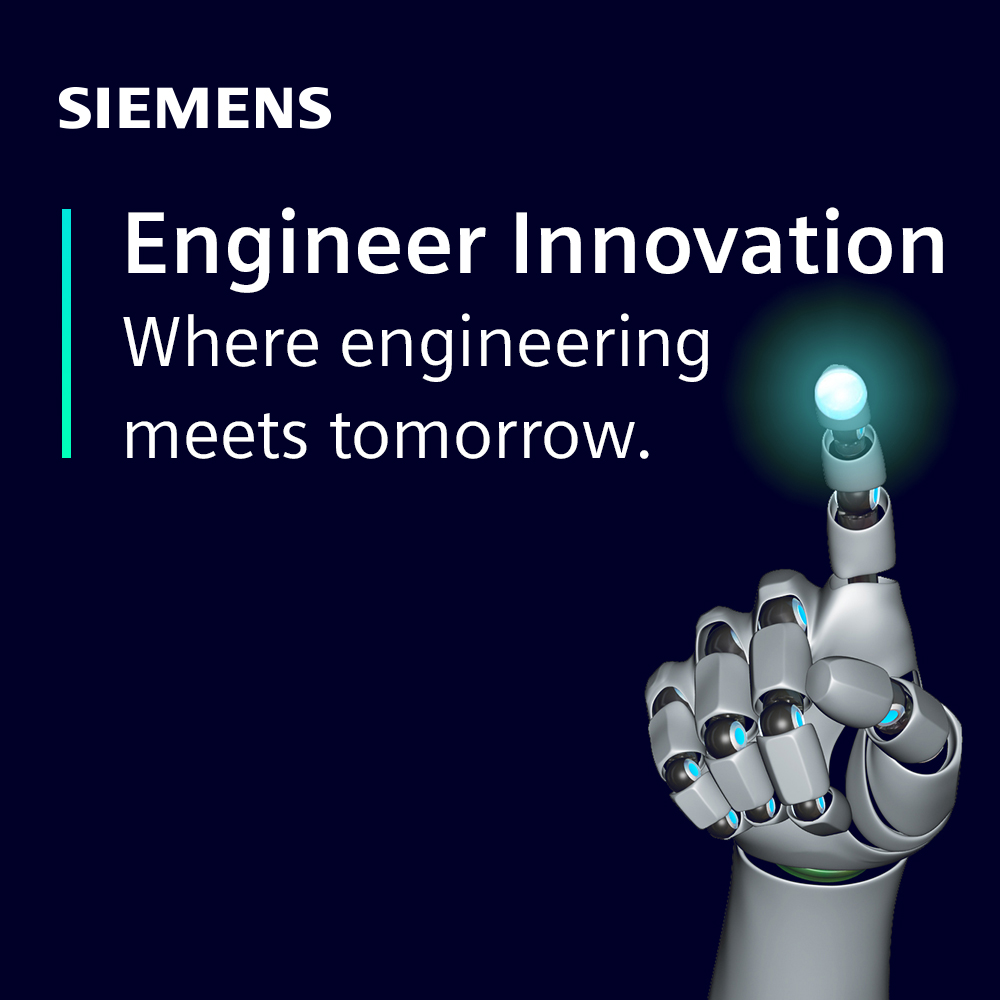
Engineer Innovation Podcast
A podcast series for engineers by engineers, Engineer Innovation focuses on how simulation and testing can help you drive innovation into your products and deliver the products of tomorrow, today.