Trajectory optimization and cable simulation – Kineo v9
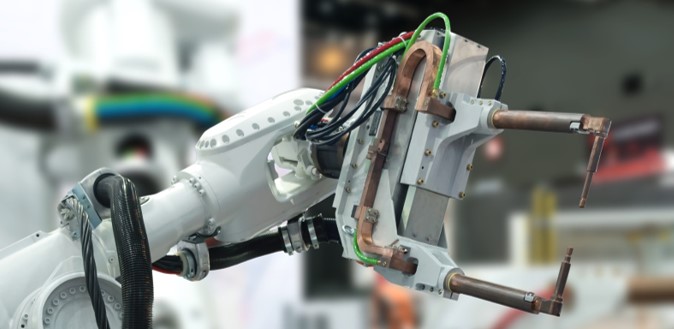
We recently released version 9.0 of Kineo software solutions. Here we put some of the new features for trajectory optimization and cable simulation under the spotlight.
KineoWorks 9.0
KineoWorks is a software component that automatically computes collision-free motion, solving complex path-planning problems in applications such as robotic collision free trajectory optimization.
KineoWorks can optimize trajectories according to a wide range of target criteria such as robot cycle time or energy consumption. Version 9.0 introduces several additional algorithms for trajectory optimization. Let’s take a closer look at a new option for targeting a preferred pose.
Imagine you want to move an articulated system in a constrained environment, such as a robot in a work cell that’s welding two parts. KineoWorks will compute a collision-free trajectory and optimize the process time, for example with automatic weld sequence ordering. So far, so good. But other goals may need to be taken into consideration. For example, during a welding operation, it’s preferable to keep the welding gun vertical to ensure a higher- quality result. Thanks to the new optimization algorithm, you can also specify a preferred value for the orientation of the tool (in general, by targeting certain degrees of freedom for any device). KineoWorks will compute the optimum path, keeping the position of the robot as close as possible to the preferred values. Where possible, the tool will be vertical. If an obstacle prevents a vertical orientation, the optimizer will find the closest position respecting all “hard” constraints such as collision avoidance and joint limits.
This algorithm will benefit many other applications, from targeting the position of a robot on a rail (or any other secondary axis), to keeping a plate horizontal when a robot brings you a glass of beer.
Kineo Flexible Cables 9.0
Kineo Flexible Cables is a software component for simulating cables, hoses, pipes and similar compliant components with interactive performance. It’s well-suited to modeling the deformation and configuration of cables in robotics systems, such as pneumatic hoses and electrical cables, to minimize failure on the factory floor.
To perform a simulation as accurately as possible, it’s important to know certain physical properties of the cable, such as its density and Young’s modulus (representing the stiffness of the cable). These material parameters are not always readily available – in such cases, it’s necessary to experiment with various parameter estimates until the cable behaves as expected.
Version 9.0 introduces a new tool for estimating unknown physical parameters much more efficiently. First, scan the real-world cable with any type of device like a stereo camera or a laser scanner. Then pass the scanned point cloud of the cable to the software. Kineo Flexible Cables uses the new algorithm to automatically compute the best physical parameters for fitting the simulated cable to the point cloud cable, removing the tedious process of determining the missing properties.
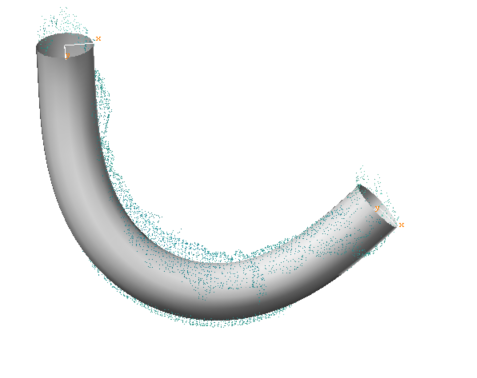
Thanks to Kineo Flexible Cables, simulating flexible cables on the shop floor has never been so easy. Scan your cable, create your cable and interactively simulate your robot’s behavior in real-world.