Parasolid with Convergent Modeling
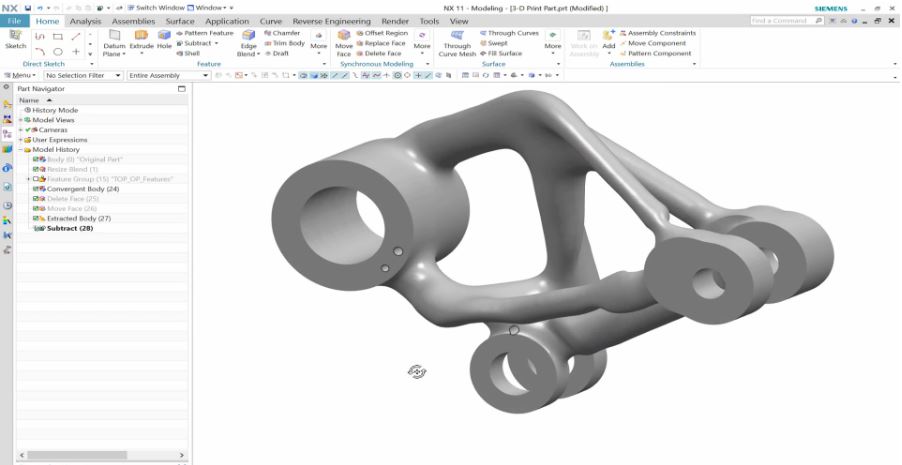
We’ve just announced Parasolid version 29.1, the third release of Parasolid to deliver Convergent ModelingTM technology. This has been getting lots of attention since its debut in NX11, which was the first software application to implement Convergent Modeling.
The end goal of Convergent Modeling is to enable facet data to be represented in Parasolid as facet b-rep geometry, alongside classic b-rep geometry, and to support all Parasolid functions without translation. This article looks at some of the reasons behind the pressing need for this technology in our industry:
Proliferation of facet models
Generic facet models use polygonal meshes to approximate the shape of an object and they’re the currency of scanning, 3D printing and generative design.
3D scanning is getting more sophisticated and less expensive, while delivering higher precision scans. As a result, growth in scanning can be seen in the medical field, where artificial implants and orthopaedic structures are being modelled on the basis of anatomical scans – creating a perfect fit for the recipient. An example can be seen in this NX use case featuring a cranial implant.
3D scanning is complemented by the parallel evolution of 3D printing as a means to manufacture custom, complex shapes, which would be difficult or costly to manufacture using more traditional methods. And it’s not just happening in the medical field – industrial and consumer goods manufacturing is also benefitting from 3D printing and scanning.
Generative design is another recent technology innovation. Also known as topology optimization, this process optimizes the shape of a part based on boundary constraints imposed by the user – for example, a limit on the mass of the part, a bounding region for the part, the location of its attachment points and the forces acting through them.
Topology optimization
You can see an example of generative design and convergent modeling in this NX use case.
Incorporating facet models in the design process
It’s often desirable to move facet data associated with the above processes into engineering design environments which tend to work with b-rep models. The objective might be to make design modifications to the facet data using the extensive and sophisticated b-rep modeling tools that are available. Or it might be necessary to integrate the facet data with an existing b-rep model, since many products that are manufactured using traditional “subtractive” methods are designed in b-rep modeling systems.
Previously, facet data has been incompatible with b-rep modeling, so it has been necessary to convert the facet data to b-rep format to perform b-rep operations. This translation process can be very time consuming, and there is potential for error in converting complex shapes into b-rep format.
Delivering a seamless modeling experience using any combination of facet b-rep geometry and classic b-rep geometry in a single model is expected to bring huge efficiency gains to digital 3D product engineering workflows.
Further information: