Parametric sketching in T-FLEX CAD – offering the best of both worlds
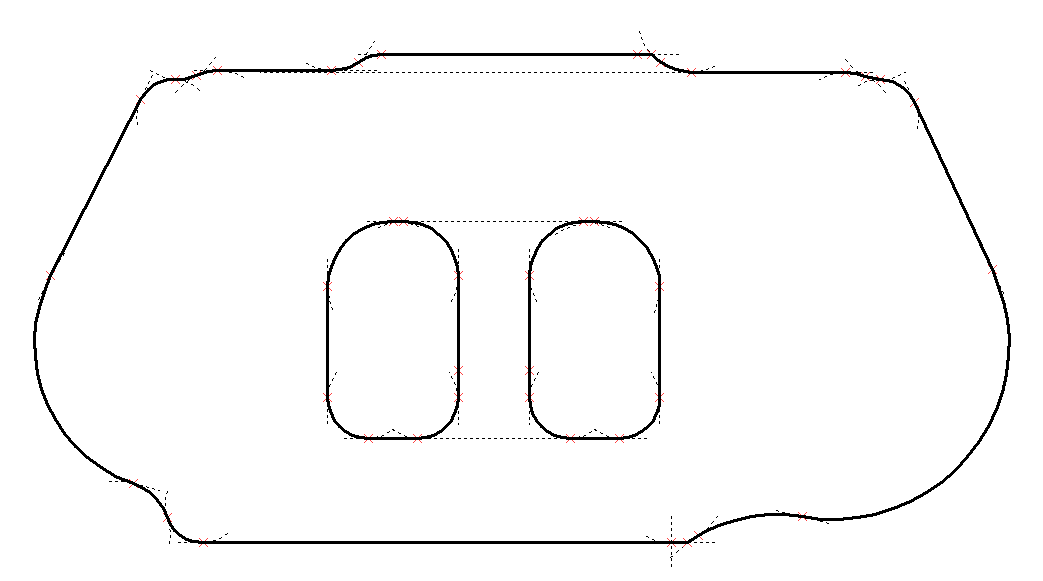
Top Systems is the Moscow-based developer of integrated solutions for product design, manufacturing and data management, and is a long-term adopter of Parasolid for geometric modeling. The company recently announced the release of its flagship product, T-FLEX CAD 16, which for the first time, includes D-Cubed 2D DCM. This geometric constraint solver is integrated into 2D sketching applications to provide parametric design capabilities.
Top Systems has developed its own highly successful parametric design technology, which it will continue to offer and enhance as key functionality in T-FLEX CAD. By integrating the 2D DCM as a complementary solver, the company now offers its customers the freedom to choose their preferred technique for solving the sketch parameters that are used to define and modify their designs. Each of these parametric design technologies offer specific advantages, some of which are described here:
The T-FLEX solver adds parameters (distance, radius, etc.) to construction geometry, which serves as a reference framework for the sketch geometry (see figures below).
Figure 1: Construction geometry with parameters applied (circle radius illustrated)
Figure 2: Sketch based on underlying construction geometry
As sketch geometry is added, its position is defined in terms of the underlying construction geometry, and with reference to the geometry that was previously defined. This means that the parametric model is always fully-defined. Working with fully-defined models has the advantage of ensuring predictable results when changes are made to the sketch. In addition, this method of parameterization means that any change to a design parameter can be rapidly propagated through the sketch, resulting in excellent performance.
The 2D DCM solves geometric constraints (distance, angle, etc.) that are applied directly to sketch geometry. All constraints are solved simultaneously, regardless of the order in which the geometry and constraints were added. This gives users the option to work with under-defined sketches. The 2D DCM also allows cyclic dependencies, where new sketch geometry and constraints can influence the position of previously added geometry.
T-FLEX CAD 16 is unique in offering this hybrid sketching environment for the benefit of their customers – both parametric design systems may be used in any combination in the same project, according to the preference of the user. They share the same set of model variables and provide broad possibilities for assigning relations between elements of parametric models using expressions and database tables. Values can be assigned via custom dialog forms that control model behavior, providing an intuitive user interface for conveniently managing families of parts.
Top System’s adoption of the 2D DCM is another success story for Siemens PLM Software’s openness philosophy – licensing core geometric modeling technologies to other software vendors to deliver benefits to the broadest number of users.
Further information:
Comments
Leave a Reply
You must be logged in to post a comment.
Strong design program.. I use it
osman özdemir.
plastic mold designer.
fersan kalıp pls. san. turkey
siemens nx 8.5 -12
t-felx cad 11