D-Cubed 2D Components version 75 release
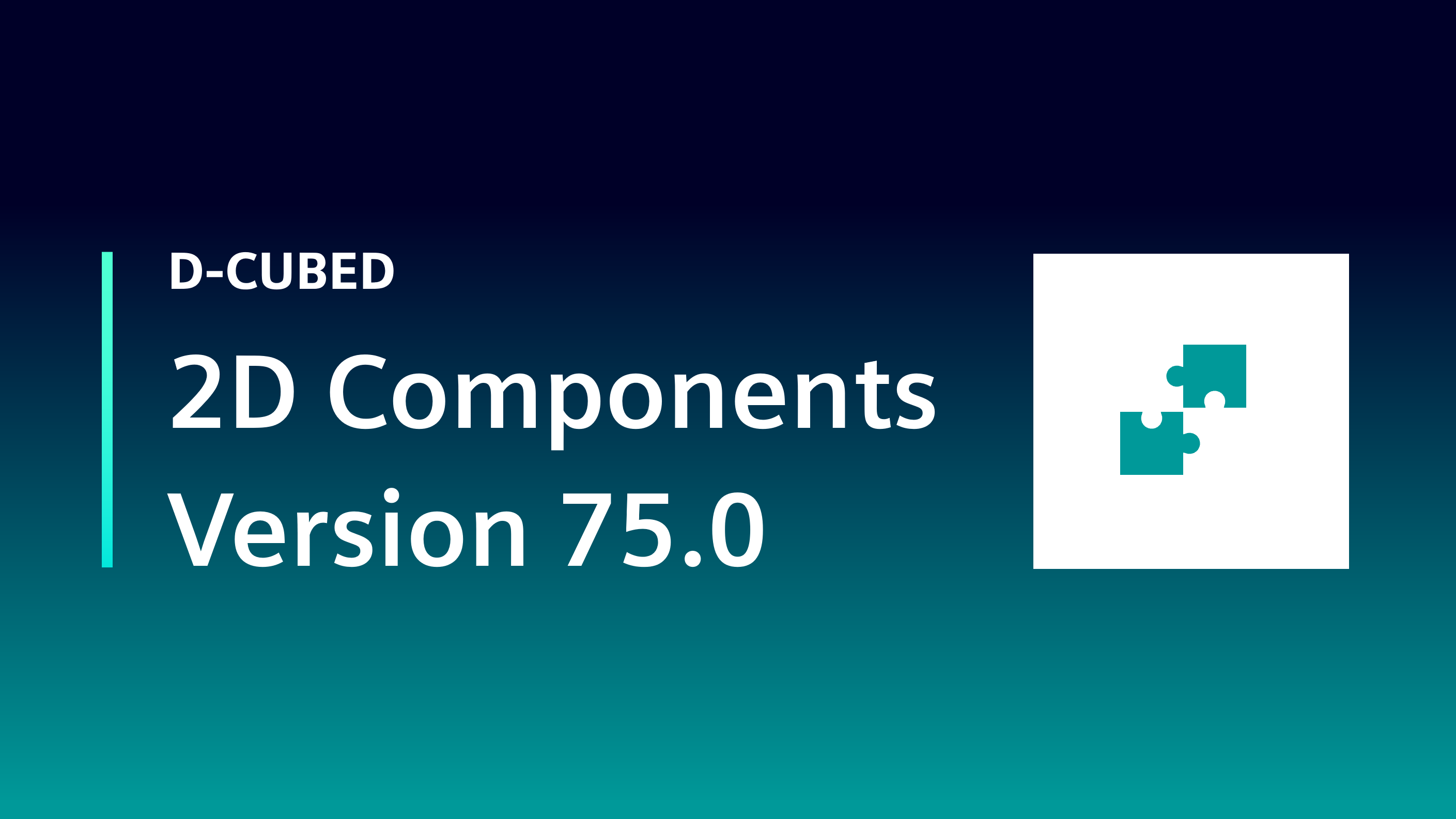
D-Cubed 2D components are integrated by software developers to add functionality to the sketching environment of CAD/CAM/CAE and AEC software applications. These applications are used to design, analyze, visualize, and manufacture products from consumer goods to aircraft engines and commercial buildings.
D-Cubed 2D DCM version 75.0
D-Cubed 2D DCM (2D Dimensional Constraint Manager) is widely acknowledged as the leading 2D geometric constraint solver. In addition to driving the sketcher in many CAD products, 2D DCM is used in CAM, CAE and other geometry-based applications. Enhancements introduced in version 75.0 of D-Cubed 2D DCM are described below.
Alignment control for symmetry constraints
The 2D DCM enables engineers to apply rules of symmetry in their designs, so that any two defined collections of geometry will remain precisely reflected about a given axis of symmetry, while any other aspects of the wider sketch are being modified. This higher-level ability to “mirror” arbitrary components in a sketch is an important capability in productive design applications.
The 2D DCM symmetry constraint has been improved in v75 as follows:
Certain sketch geometry, such as lines and ellipses, have an associated direction that is very useful for orienting them in a sketch. For example, directions enable you to constrain a line to be parallel, or anti-parallel with another line, so you can reverse their relative orientations, together with any other geometry that each line is constrained to.
Starting with version 75, applications can directly control the relative alignment of directions involved in symmetry constraints. A symmetry is aligned if reflecting one geometry about the axis would make it coincident and aligned to the other geometry. A symmetry is anti-aligned if reflecting one geometry about the axis would make it coincident and anti-aligned to the other geometry.
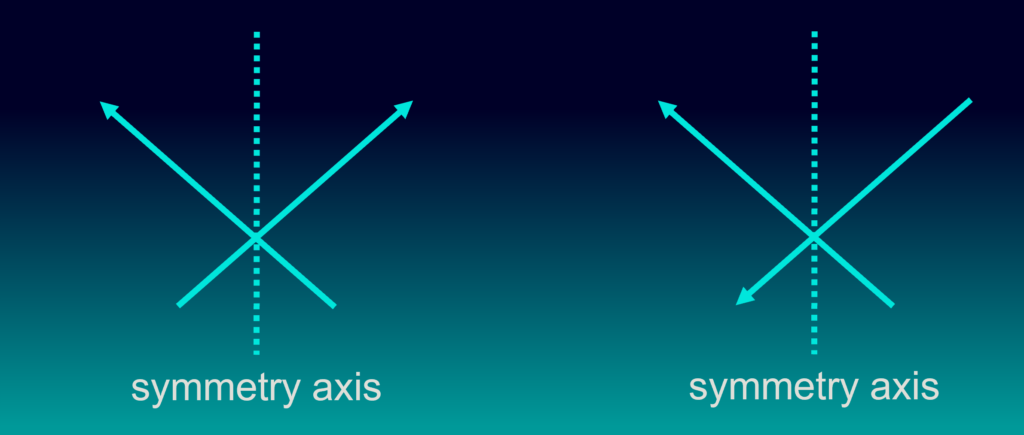
Aligned (left) and anti-aligned (right) symmetry constraints
The new capability is a subtle, though important detail and demonstrates the continuous evolution of the 2D DCM in meeting new requirements as our software end-users create ever more demanding applications on the technology.
Alignment control for normal constraints
Version 75 also introduces alignment control for the normal constraint. A normal constraint can be applied between a curve and line that intersect, or between two curves that intersect. At the point of intersection, the tangent direction of the curve is constrained perpendicular to the direction of the line, or to the tangent direction of the other curve.
There are two alignment configurations that can satisfy a normal constraint, anti-clockwise and clockwise. In the first configuration, the direction or tangent direction of the second geometry is obtained by rotating the direction or tangent direction of the first geometry anti-clockwise by 90 degrees. In the second configuration, the rotation is clockwise.
The figure below illustrates the two possible alignments of a normal constraint between a spline (first geometry) and a line (second geometry).
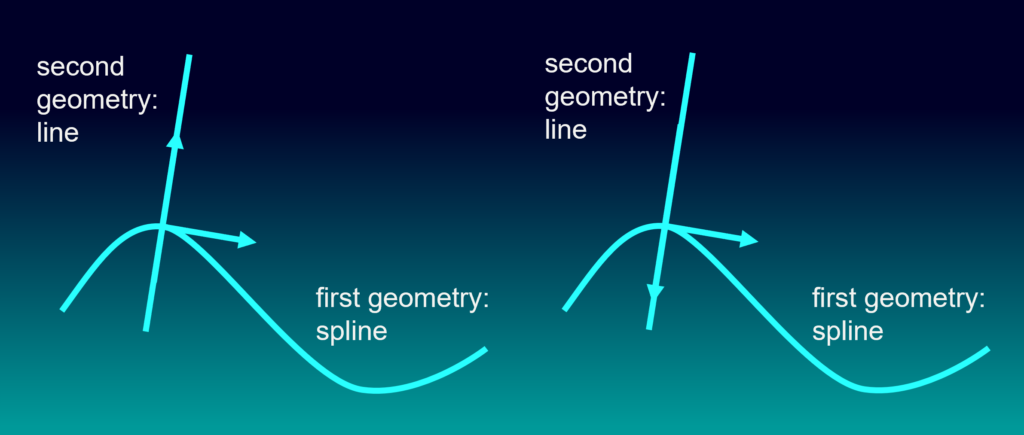
Anti-clockwise (left) and clockwise (right) normal alignment between a spline and a line
Performance enhancements for symmetry and pattern constraints
2D DCM supports advanced constraint types such as symmetry as well as linear or circular patterns of repeated elements. This release further improves performance for constraints that are often used with large, simple symmetric sketches and pattern arrays.
Improved solving and performance for directed distances
Directed distances are measured along a specified direction, which can be an absolute vector value, or parallel or perpendicular to the direction of a line. Version 75.0 provides more efficient and predictable solving for directed distances, including performance improvements.
D-Cubed PGM version 75.0
D-Cubed PGM (Profile Geometry Manager) enhances the productivity of sketchers. It does this by working with higher level geometric data and not individual curves. Examples include offsetting loops while inserting, extending and trimming edges, adding constraints to loops rather than to individual curves, and solving the shape of loops while maintaining their perimeter length or area. PGM is often used to add capabilities to a 2D DCM-based sketcher. Enhancements introduced in version 75.0 of D-Cubed PGM (Profile Geometry Manager) are described below.
General performance enhancements
Improvements have been made to data types and their lifecycle to give significant improvements to the performance of typical operations.
Stability improvements
Changes to certain key computations have been made to avoid instabilities due to different platforms, for example 32-bit versus 64-bit, and x64 versus ARM64.
Reliability improvements
This version improves the reliability of slot offsets, loop finding and solving functions with moving geometry.