Old Habits Die Hard
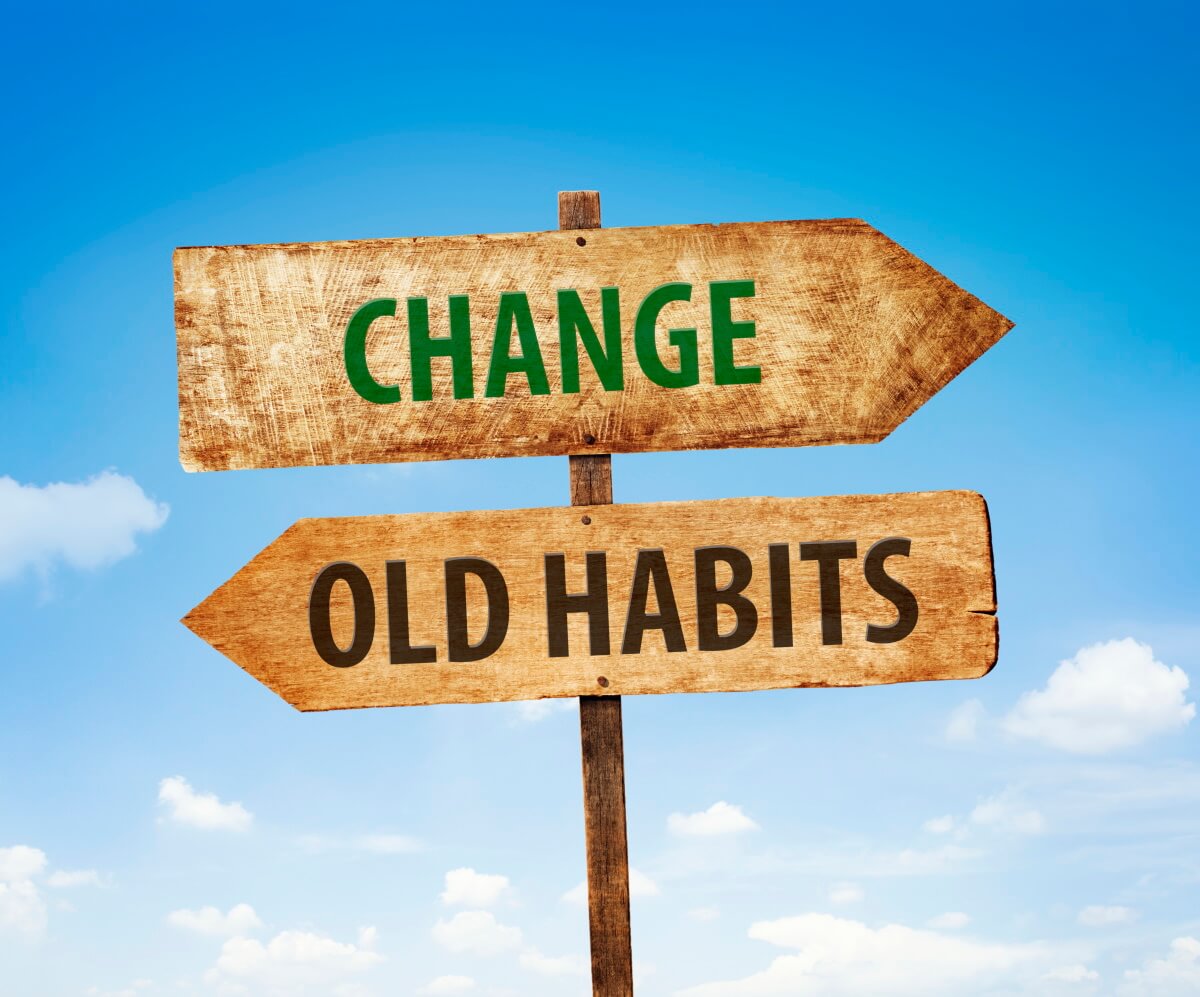
In one of my previous blog posts, I asked the question: Why do designers keep sending Gerber files to their manufacturers, knowing that the manufacturers will have to work hard to restore information that is “lost in transition” due to the format limitations? The typical answer was – and still is – that they believe that manufacturers can manage with Gerbers. Why not? They’ve been managing for decades!
In this post, I will discuss another old habit of designers that won’t die – putting non-copper features on copper layers, without considering the impact on manufacturing.
Non-copper features on copper layers
Sounds like a no-brainer, right? Why would anyone put non-copper features on copper layers? Well, apparently, many designers do so without realizing that any feature they put on a copper layer is considered to be copper and will be manufactured as such.
The simplest and most common example is the text box with common information about the board, the revision, layer, customer, etc. Most likely, there’s no intention to print this information on the real board. But if these features are not deleted explicitly during the pre-production stage at a fab – they will be printed. In most cases, these features are easily recognizable by a manufacturer and thus, no questions need be asked – they are simply deleted. In some cases (when the text box is clearly located outside the board outline, and/or when the board is exported as ODB++, and these features bear a proper attribute) they may even be automatically recognized by CAM software – making it even simpler.
The next example is much less trivial, and more dangerous: lines that run along the board outline. In the below illustration, you can find lines that denote copper traces, as well as inner and outer cutouts – in the same layer – you, of course, can easily distinguish between them. So you most likely rely on your fabrication partner’s CAM engineer to recognize them and to delete them before the layer data is sent to production, right?

Recently, I had conversations with three very experienced layout designers working for different companies in different countries and different industries – but the dialog was very similar:
- Why are you placing outlines in copper layers?
- For reference purposes – in this way I can see if I’m getting too close to a board outline during editing.
- But the outline already exists in a separate object/layer (depending on the CAD tool being used), and it can serve as a reference as well, right?
- Right. But it is more convenient to have it in the copper layer.
- Understood. But why you don’t remove these lines before you hand the board over to manufacturing?
- Why should I? Do they cause any trouble?
- Sure! They have to be removed explicitly before sending for production.
- Hmm, but why?
- Because they are on copper layers and will be treated as such unless explicitly instructed otherwise.
- Strange, I never heard about that.
- So after you hear this, will you consider removing them?
- I’m not sure, up until now there’s never been a problem…
- It wasn’t, because your manufacturing partners took care of it. And what if a manufacturer mistakenly removes too many lines?
And so on… Old habits die hard…
So what can be done?
If you’re looking for a quick, easy way to improve efficiency and accuracy, consider simply removing non-copper features from copper layers before handing them over to production. And don’t forget the solder mask, silk screen and other board layers, either. Deliver the outline features a separate layer – so that the manufacturer will be certain about the exact outline shape, and won’t have to clean it from other layers.
As professional designers, we aspire not only to meet product specifications, but carefully consider every trace, pad or hole, making sure that we cover every aspect of the design. It’s craftsmanship at its best – incorporating a multilevel understanding of the product as a whole, while attending to its finest details.
Now, with the introduction of PCBflow, we can add another layer to our craft – manufacturability. PCBflow introduces powerful manufacturability tools that help us overcome our old habits and boost our performance to a new level of professionalism.
Sign up and try it out at https://www.pcbflow.com/ .
PCBflow runs in a secured cloud environment, so you can rest assured that your IP is fully protected.