TOP 5 Benefits of Manufacturing Digitalization in Medical Device and Diagnostics
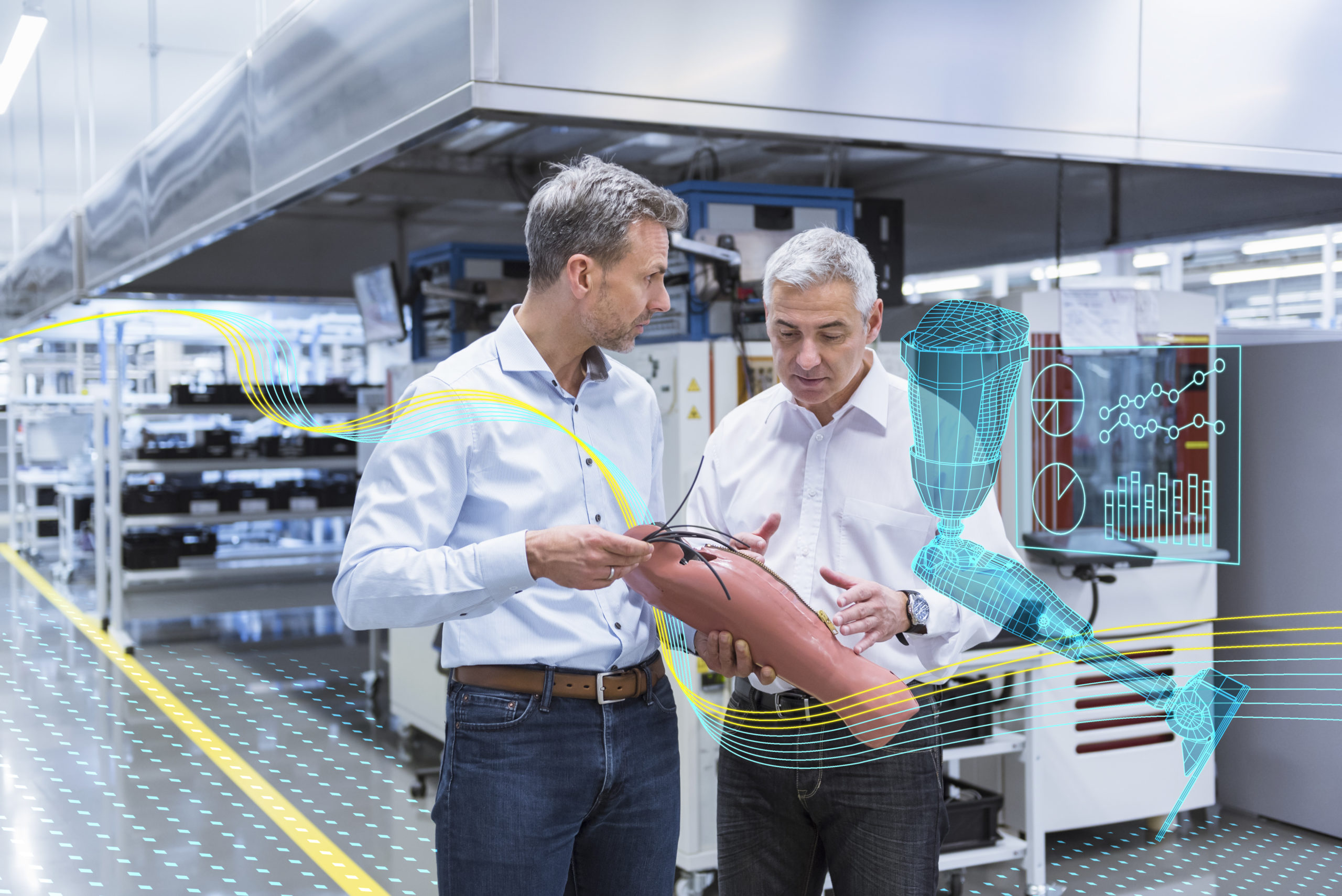
“The sooner, the better” may be the best answer to the question of when medical device and diagnostics manufacturers should digitalize their operations — both because of a rapid return on investment (ROI) and because digital technologies will be paying dividends well into the future. Benefits of digitalization will be considerable for med-tech companies in particular, given the demands of today’s healthcare marketplace.
Digital technologies can turn healthcare market pressures into market opportunities, empowering you to keep up with, or even leapfrog, the competition. This is especially true of those technologies that handle the central functions of Manufacturing Operations Management (MOM) — what we call the “digital brain” of manufacturing and quality operations. Here are some key benefits to med-tech companies that invest in and implement MOM digital solutions:
Benefit #1: Paperless Manufacturing
Far beyond good environmental stewardship and sustainability, going paperless on the medical device manufacturing floor means digital accessibility to information critical to any and all stakeholders in the value chain. Instead of fumbling through files and flipping through pages to follow work instructions, your production team will click the “Next” button on a tablet. Instead of filling warehouses with product documentation that must be maintained for many years (leaving you vulnerable to paper risk), your operations team will upload automatically populated documents to digital storage — and anyone wishing to access that information will find what they are looking for with a few keystrokes. Paperless manufacturing means that med-tech companies will be able to shift from managing dumb documents to managing product quality and operational efficiency.
Benefit #2: Compliance as a Byproduct of Quality
With the U.S. Food and Drug Administration (FDA) and other regulators shifting to a focus on quality over compliance, integrated MOM solutions enable manufacturers to do likewise. A MOM system automatically controls the manufacturing environment according to product and process definitions, while simultaneously collecting as-built data. Opportunities for errors, non-conformance events and field failures are dramatically reduced, and compliance becomes a byproduct of a digitally controlled process. Managing inspections is greatly simplified with technology solutions that provide rich, timely and accurate data, reducing the time and overhead of producing documented evidence. And manufacturers can leverage their MOM solution to automatically create electronic device history records (eDHR), accelerating their ability to respond to compliance concerns and more intelligently prevent quality issues.
Benefit #3: Closed Loop Cycles of Virtue
By feeding actual product, production and performance data back to the Digital Twins generated and utilized during design and development, manufacturers benefit from a “Closed-loop Manufacturing” (CLM) system centered on MOM technology. CLM enables you to compare the predicted performance of a product or manufacturing process with actual performance. Based on insights gained in this comparison, you can make rapid adjustments in device design and manufacturing processes engineering.
Shorter commissioning and validation times, increased process reliability and product quality are the outcomes.
Benefit #4: New Production Efficiencies
Though greater efficiency results from other benefits listed here, it also stands on its own as a key benefit to consider as you decide upon the steps in your digitalization journey. An integrated MOM solution knows what resources are on local production lines and can optimize production based on manufacturing orders. It also makes manufacturing intelligence available so you can understand key performance indicators (KPIs) such as overall equipment efficiency (OEE), utilization, throughput, rework and scrap, and more. MOM technology will help to:
- Accelerate production by orchestrating automated manufacturing operations with smart human interaction
- Speed response to changes of all sorts — new product introductions, order changes, supplier issues, improvement measures — through real-time, data-enabled collaboration with suppliers and customers
- Improve on-time delivery by minimizing equipment downtime, manufacturing delays, and material shortages
- Produce higher margins
Benefit #5: Insights from Contextualized Data
With digital sources increasing exponentially all along the med-tech value chain, Big Data is readily available to help manufacturers identify factors that affect production costs and quality. But “available” is not that same as “accessible” or “useful.” For medical device companies wanting to leverage this pool of data to their benefit, MOM technology is indispensable. It can contextualize data from various functions and sources and synthesize it into global performance reviews. Large volumes of real-world data (RWD) are also being generated to monitor medical devices as they are used by clinicians and patients. Digital solutions that capture learning from the real world and integrate it with data from other relevant sources can create new dimensions of predictive insights for decision-making.
The FDA recently determined that 54% of product recalls in the years 2013 to 2016 were caused by preventable errors associated with manufacturing controls in the production process. An effective MOM system anticipates and enables prevention of these recalls. This single benefit more than justifies your investment in MOM technology; and all the benefits covered here build a compelling case for MOM: the sooner, the better.