Medical Device Manufacturing: Why Digitalization is Changing Everything
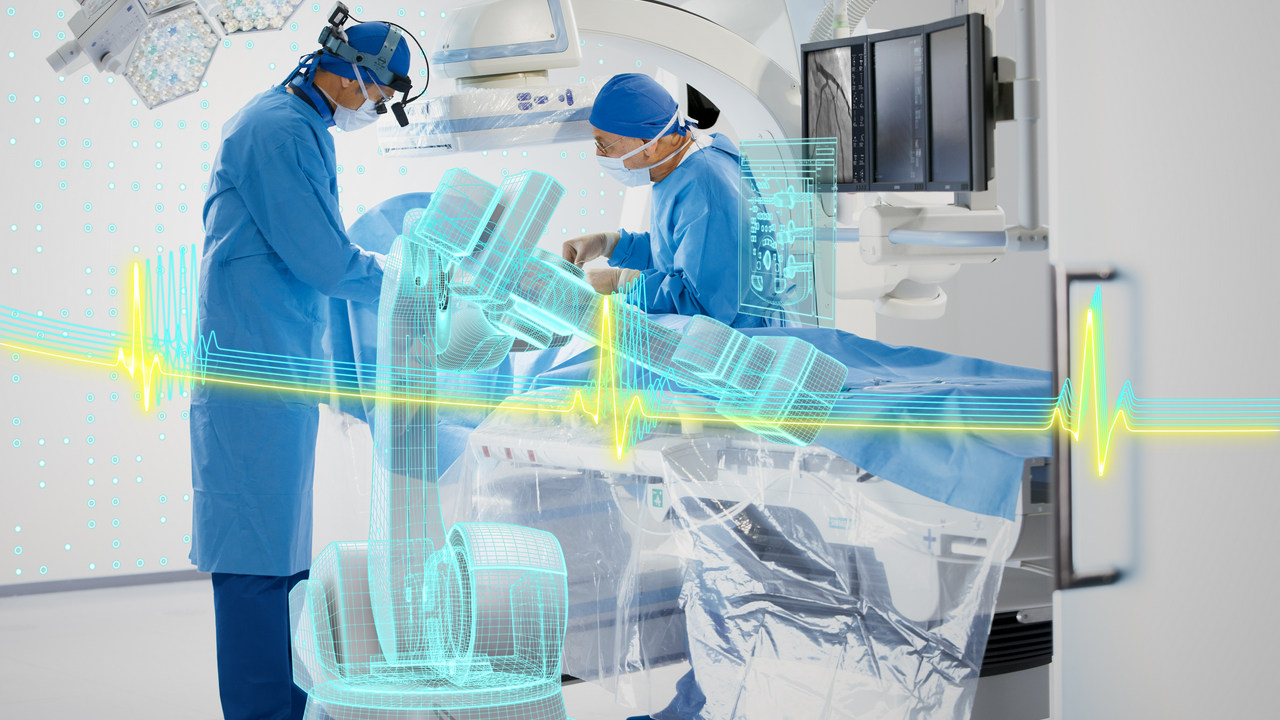
Text Version: Leveraging on Medical Device Manufacturing Digitalization to drive growth
It’s impossible to exaggerate how profoundly the digital revolution has already impacted our lives, from banking, shipping, home-buying to the way we communicate, get news, and perform our work. Digitalization has opened up new and more efficient ways to get products, and has forever changed consumer expectations as well as supply chain demands. When applied the complex world of medical devices, what implications should manufacturers be aware of and preparing for?
First, digitalization is changing the patient’s expectations. Patients have access to more medical information than ever before, enabling them to self-diagnose and “shop around” for providers and treatment options. Patients are becoming more critical of the value received for their healthcare money.
Add to this the growing complexity of medical technology itself. The Internet of Medical Things, connected diagnostics, next-generation implants, customized orthopedics, personalized medicine – these complexities are creating new challenges for medical device manufacturers not only from the treatment itself, but from the data generated throughout. It is an increasingly Big Data conundrum.
This reality is changing the way medical device manufacturers are running their business. Today, best-in-class digitalized med-tech companies are 4 times more likely to monitor intelligent analytics. 66.7% of med-tech executives perceive intelligent analytics as one of the major opportunities for growth (Frost and Sullivan). 64% of providers perceive consumer feedback as a vital benefit of operations within IoMT programs (Accenture Consulting). In short – medical device companies must have an infrastructure to support the analysis and application of this big data, and use it to better meet patient expectations.
The FDA and other regulatory agencies are expecting medical device manufacturers to do this. They have shifted their regulatory paradigm from compliance to quality. They are rewarding manufacturing behavior that applies intelligence and best practices to improve product quality. The FDA states, “From 2009 to 2014, there was a 3x increase in adverse events and a 50% increase in product recalls. These numbers will rise without proper digital processes implemented across all business segments within a given medical device organization.”
So, what are the most important things medical device manufacturers should be doing (if they aren’t already) to operate in a world changed by digitalization?
First, manufacturers must leverage the capabilities of digital manufacturing systems to empower every phase of the innovation process. That requires connected, collaborative, intelligent systems across the manufacturing enterprise. At Siemens, we call this connectivity the “Digital Thread.” It is leveraged by a single platform with a common data model to create a powerful foundation for speed, quality, and cost efficiency.
In addition, “Digital Twins,” or digital representations of the physical world, can be used to predict and optimize quality and performance of devices from design to development to production to utilization. Before large investments are made in producing particular designs, setting up plants, assembly lines, and fabrication work cells, performance can be simulated and improved in the digital realm, where mistakes are much less costly.
When you get feedback from manufacturing operations, Digital Twins enable you act on that feedback by comparing the predicted performance against the actual performance, and based on that insight, make adjustments in the device design and the manufacturing processes. We call this “Closed-loop Manufacturing.” It is the culmination of digital transformation in manufacturing.
Central to this platform is the point at which the digital realm intersects with the physical realm – manufacturing operations. Manufacturing operations management (MOM) systems play a key role in translating digital optimization processes into reality. Some of the key capabilities include
- Integration between PLM and Automation, facilitating a smooth transfer of virtual product and production information from the design and engineering departments to the shop floor and manufacturing operations.
- Orchestration, or MOM as the digital brain of manufacturing and quality operations. MOM collects production orders from ERP and BoM/BoP from PLM and – using its digital intelligence – orchestrates all the manufacturing activities based on the best schedule and real-time shop floor information.
- Data contextualization and closed loop feedbacks – The digital intelligence of MOM enriches production and product data with manufacturing information, transforming them from simple data into actionable information that can be re-used by the right departments at the right time. MOM closes the loop between reality and virtual environments enriching virtual production and virtual products with augmented and contextualized data.
- Connection to product lifecycle analytics – Manufacturing contextualized data are also fed into a complete analytics platform that spans the product lifecycle to enrich Big Data IoT-based information.
Finding the right platform for manufacturing will make or break med-tech companies in the not-to-distant future. With digitalization changing everything, manufacturers must brace for change in their industry by leveraging digitalization in their own operations.