FMEA as a Business Process Tool
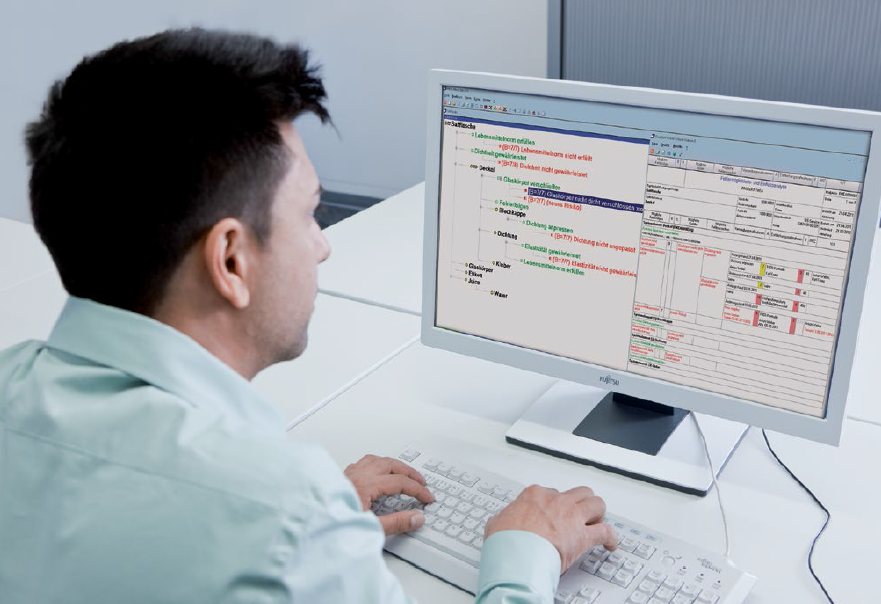
More and more industries are discovering what the Automotive and Heavy Equipment companies have known for years. The same tools they use and trust to define, quantify and control risk around manufacturing design and associated processes can be used for defining, analyzing and controlling risk for any business process. Investing in the education, structure and discipline of a design and process-centric approach to developing and refining your company’s strategy for almost anything you need to do reliably and repeatedly can yield huge and immediate benefits.
If the entire concept of Design and Process FMEAs (Failure Mode Effects Analysis) is new to you here is the Cliff Notes explanation of the basics.
A DFMEA (Design Failure Mode Effects Analysis) essentially is a long stream of consciousness construct of:
- Each component, subassembly and assembly into one or more documents.
- Each component, subassembly and assembly is subjected to a serious “what can go wrong with this item or material” exercise.
- An offsetting control is established or identified for each scenario.
- Then, an accepted mathematical formula is used to quantify the risk with the identified controls. The resulting number is typically called a Risk Priority Number (RPN). The formula is the product of the following:
- Likelihood of Occurrence (What are the changes that this can happen?)
- Likelihood of detection (If this does happen given the current identified controls, how likely is this issue to be detected?)
- The last element of the calculation is Severity. (How “severe” is the potential impact if this defect or condition is not detected?)
- Once you have the RPN you can assess the effectiveness of existing or proposed controls. The process from there is determining “actions” as either “None required” which means that the risk is low and the controls are adequate, or some other corrective or preventive action.
- If the risk, even with the off-setting controls remains high enough to be of concern the action identified involves adjusting the “Controls” and repeating the calculation until the risk is acceptable.
A Process FMEA (PFMEA) is handled in much the same way but is focused on breaking the manufacturing process into a sequential flowchart as a first step. Then this process flow goes through the exact same control identification and RPN exercise to assess the risk and adequacy of controls for each step in the process. You can repeat each item in the DFMEA and PFMEA under:
- Normal Conditions: All conditions including materials, operator and environment are as specified and presumed.
- Abnormal Conditions: The calculations reflect identified deviations from defined and presumed materials and process.
- Emergency Conditions: Materials and process methodology are acting under uncontrollable duress.
The final list of “controls” are then condensed into a “Control Plan” which becomes the basis for inspections and product and process control tests and audits.
In the case of applying these same principles to a business or quality process such as Corrective Action Investigations and fiduciary processes for financial disbursements, the PFMEA is typically more frequently used of the two tools. The development of a resulting Control Plan remains the same.
- Start with that crucial process flowchart.
- Deconstruct the process into each step and calculate your RPN number. Make sure you really address each step in the process. Making an assumption that a step is unimportant or bulletproof without further analysis is a potential trap that can manifest later. In the event that something does go wrong and you are trying to analyze what permitted the situation to manifest, you will expend unplanned time and effort chasing down phantoms needlessly.
- In the case of business processes, short frequent process audits and control tests that are a mix of regularly scheduled and ad hoc actions with a diverse cast of audit and control test participants keeps the perspective fresh and the burden manageable.
Setting reasonable thresholds that trigger the need for corrective and preventive actions (CAPA) and other actions, is particularly valuable in business processes that are not conventionally the subject of structured improvements and formal corrective action investigations and root cause analysis tools. Add to this the ability to include and report on metrics as part of Management Review and Business Intelligence, you can avoid organizational crisis that has hidden in areas historically exempt from regular structured scrutiny and improvements. Fiduciary, Human Resources and Contract Review typically have had limited and specific oversight. This opens up real possibilities to proactively identify potential legal and compliance issues before they happen and certainly, while they are manageable and more easily contained.
In the interest of brevity, we are short-cutting all of the steps and benefits of a true Advanced Product Quality Planning (APQP) process. This element requires ongoing communication and examination of the processes for changes in conditions and the potential for improvement.
Expand your focus and vision to apply elements of your quality toolkit to your entire scope of business processes. In many cases it is as simple as inviting them to the party and offering some training on the tools most of you use every day. You might just find yourself running to keep up with the response.
To find out more about quality management systems that support the above processes, visit our “Planning Quality with FMEA” page.
Comments
Leave a Reply
You must be logged in to post a comment.
By using a chlorine dosing system, you are giving you and the users of your shower to alleviate all of the possible effects of chlorine on the body. For your skin, the filter can get rid of any of the lingering itch that you tend to get when such chemicals come in contact with your skin. With regards to your hair, expect it to shine more.
To learn about the system that my family and I use in our home, I invite you to visiting my informative website listed below. If you are interested in chlorine dosing system, please check our website at https://www.qileegroup.com for details.
Or contact us
Tel: +86 021 5169 7580
Phone: +86 13817134452 &+86 13817145452 &+86 13918724674
Email: qilee@qileegroup.com
Contact person: Xia Miao
Add: Room 412, Xianglu Building, No. 3009, Gudai Road, Minhang District, Shanghai, China