If you really want to scare an NC programmer, just show them a deep, narrow cavity on your latest design, and then comment that you must have a mirror-like surface finish at the bottom. Why is that scary? It’s all about leverage. To illustrate, let me tell you about my new exercise program. I grasp a large potato sack in each hand, and then hold my arms horizontal to my body (like Leonardo Da Vinci’s Vitruvian Man). At first, I could only hold the sacks for a few seconds, but now I can hold them out from my body for more than five minutes. My next step is to put potatoes in the sacks (that’s the punchline). As you learned in your beginning engineering class, it takes much less pressure to affect a long lever than it does a short one. When it comes to side pressure, cutting tools are very much like levers.
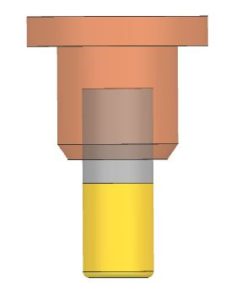
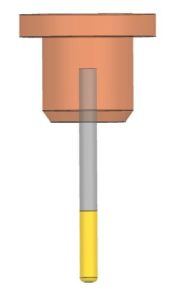
The larger, shorter, cutting tool is more rigid and will be able to withstand higher cutting pressures. That means it can be fed at a higher material removal rate. So why use the longer, narrower tool? Because someone designed deep, narrow cavities that require mirror-like surface finishes.
In my last post, I showed how to use ever-smaller diameter tools to rough-machine stock from a part. In this post, I will show an alternative that can be used for very deep, narrow cavities. Instead of substituting smaller diameter cutters, I substitute longer cutters instead. I use the short, rigid cutter for as long as possible, then swap it out for a longer one and reduce the feedrate. This method allows for more efficient cutting of deep cavities.
In NX CAM, the process works like this:
- Choose a set of cutting tools (from short to long) for the machining requirement. These cutting tools must have the same diameter, but the length is progressively longer.
- Cut the entire deep cavity with the shortest tool (make sure that Collision Checking for the tool holder is turned off)
- Use the Divide Tool Path option to split the path where needed. NX CAM looks at the length of the current tool, and splits the tool path just before the holder violates the part geometry.
- Repeat step 3 as needed for each longer tool.
This video helps explain the process.
Dividing a tool path by the length of tool (the holder) is another option available to NC programmers who use NX CAM.
About the Author
Jim has a Master’s degree in Business Administration from the University of Central Missouri. He has over 30 years of experience in the manufacturing industry, and over 25 years of experience in the CAD/CAM field. He serves as Field Support for Siemens PLM CAM products. Prior to his current role, he held stints as CNC Programmer, CAD/CAM Department Manager, CAD/CAM instructor, and Project Coordinator for Siemens PLM CAM software development.
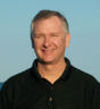