Increased throughput: A $7M opportunity for manufacturers
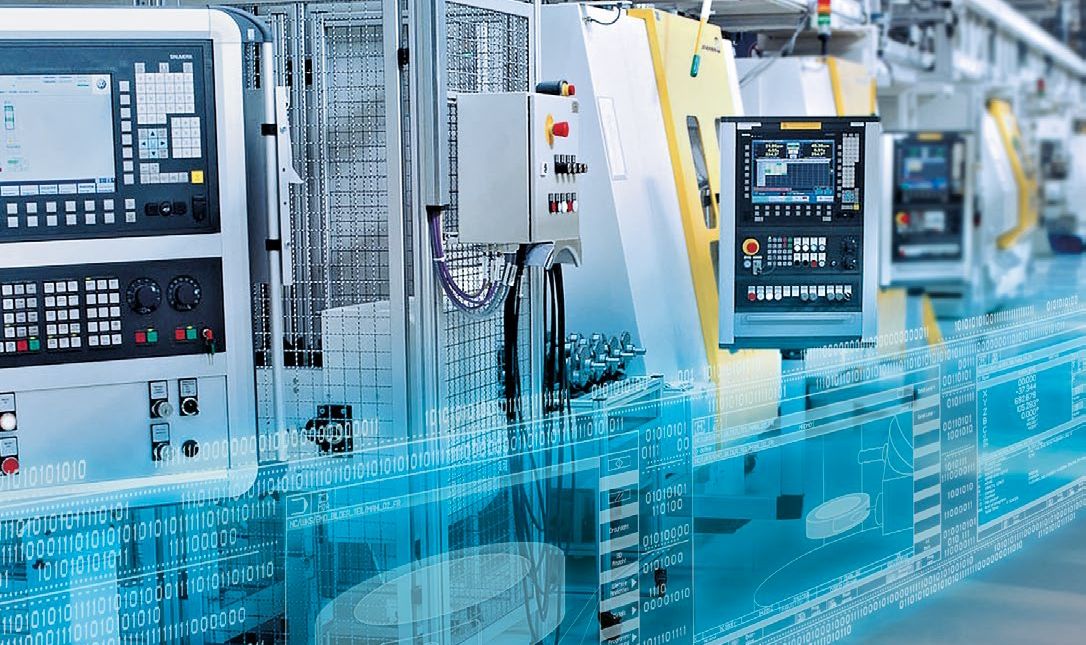
An increasing number of companies see digital transformation (DX) initiatives as a way to improve manufacturing throughput. It’s important for manufacturing organizations to understand where such investments can improve the entire production process. This is the second post in a series highlighting the findings from Lifecycle Insights’ 2021 Return on Investment (ROI) of DX Study, including calculating the financial impact on a fictional part manufacturer for illustration.
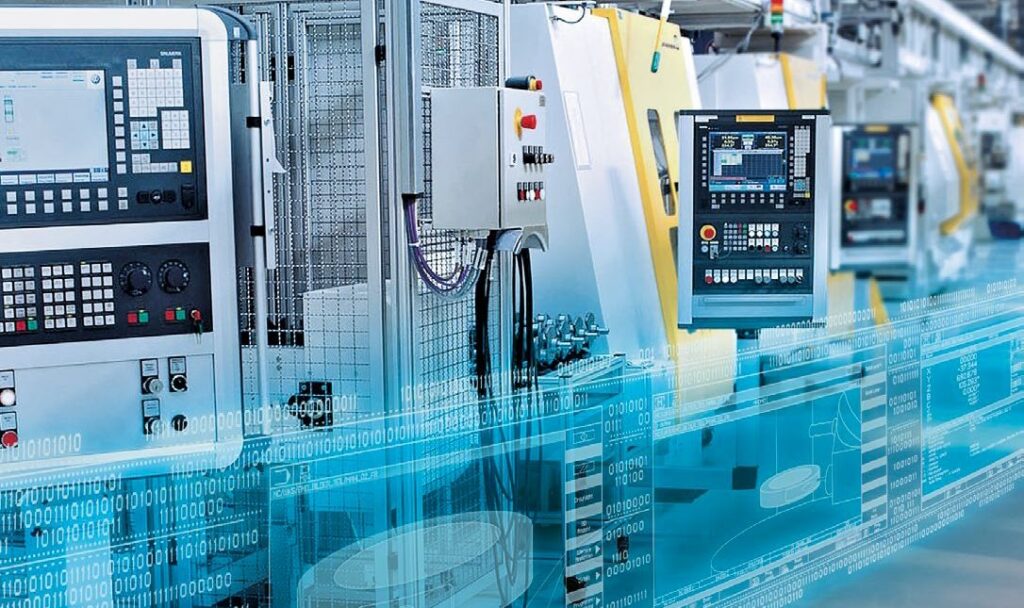
This post is part of a continuing series focusing on the impact of digital transformation initiatives on manufacturing. Make sure to check out the first post in this series, What is driving Digital Transformation today?
The ROI of DX Study
The 2021 ROI of DX study was conducted to better understand why, where, and how manufacturing organizations are adopting different DX initiatives. To highlight essential trends in investments, the respondents were split into different groups according to their DX initiatives activities.
To split respondents into groups, respondents were awarded points for each DX initiative investment. Those points were then summed to create a DX initiative investment score. Separately, respondents were awarded points for each investment in technology solutions that support DX initiatives. These points were tallied to create a technology investment score. The DX initiative investment score and the technology investment score were then multiplied to give each respondent an overall index score on DX progress. Lifecycle Insights then segmented the respondents into three groups by index score: least progressive, moderately progressive, and most progressive.
Lifecycle Insights’ 2021ROI of DX Study
The study found the most progressive organizations are far more active with DX initiatives than the least progressive group. Moreover, these organizations enable such efforts with the right technologies. The end result? The most progressive organizations see tangible improvements across the entire product development and manufacturing lifecycle.
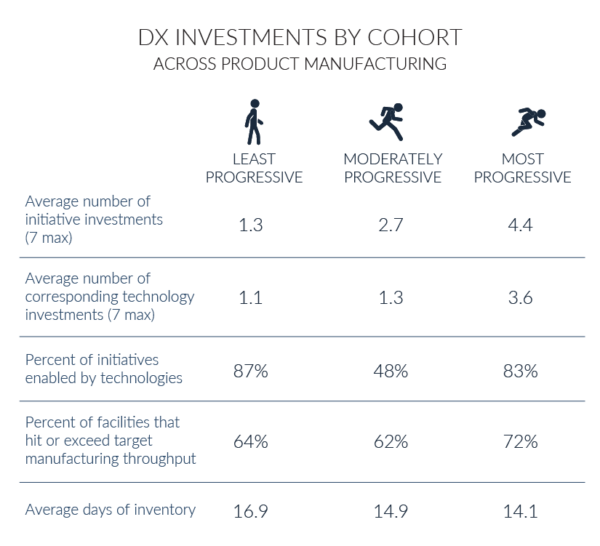
Translating the Findings to ROI
The study showed several key differences between the most progressive and least progressive organizations with regards to managing condensed schedules and more complex products. One finding that stood out was a significant disparity between target manufacturing throughputs. Seventy-two percent of the most progressive organizations were hitting or even exceeding their target manufacturing throughput, thanks to their DX investments. The least progressive organizations, however, were at 64%, meaning 8% fewer facilities hit the desired target throughput. Such a difference can account for significant additional costs, both in terms of time and resources.
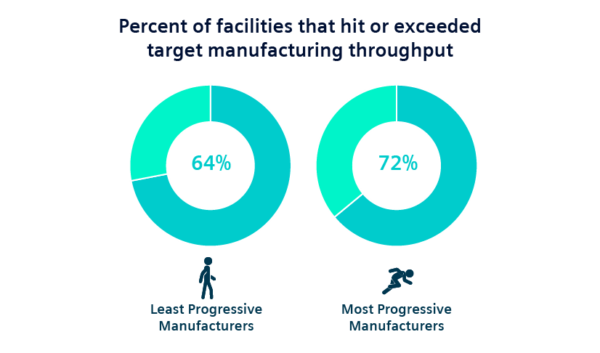
To better illustrate the impact of such a difference, let’s apply the findings to a fictional manufacturing company, TBX Manufacturing, Inc. This medium-size company manufactures turbine blades for turbomachinery, such as jet engines and power generation equipment. Here’s its financial profile.
- The company has a total, maximum revenue of $100M.
- It has six manufacturing facilities, each of which can potentially produce 15,000 turbine blades each year. The company can then produce 90,000 blades per year, working at capacity.
- When a facility falls short of manufacturing throughput, however, it only produces 12,000 blades.
If we apply the findings from Lifecycle Insights’ 2021 ROI of DX study to this example, we uncover the following fiscal impact:
- If TBX Manufacturing performs similarly to the respondents in the least progressive group, only 64% of its facilities hit their expected throughput targets. That means four of the company’s facilities work to capacity, and two fall short of manufacturing goals.
- The four on-track facilities produce 15,000 blades each, for a total of 60,000 blades. The two other facilities only produce 12,000 blades each, or 24,000 blades in total.
- Adding up those components, TBX Manufacturing, Inc. produces 84,000 blades this year: 6,000 fewer blades than capacity. This is a 7% drop in production.
- This drop in throughput will translate to $7M lower revenues for a potential $100M company. That’s a significant and wholly unnecessary decrease.
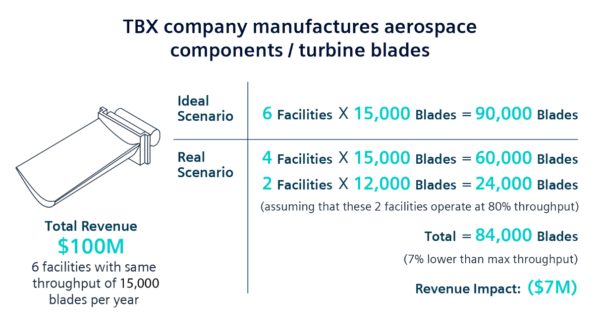
Enablers of DX in Part Manufacturing
How do the most progressive realize more revenue from manufacturing throughput? What could TBX do to increase revenues?
Findings from Lifecycle Insights’ 2021 ROI of DX study demonstrated that the most progressive organizations were more likely to have a range of technology-enabled capabilities in place, enabling higher manufacturing throughput. Those capabilities include:
- The ability to assess, run trade studies on, and improve tooling performance. These simulations improve operations by allowing tool designers to explore different tool design options and understand how they impact manufacturing.
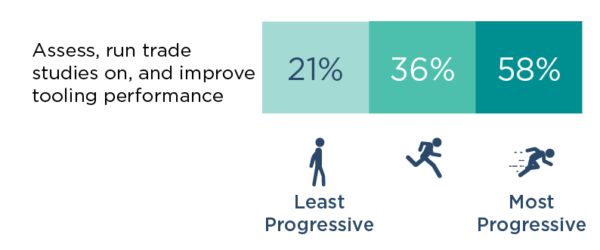
- Investments in automated tooling design as part of mechanical computer-aided design software platforms. Armed with these capabilities, tool designers can reuse company standards and best practices while accelerating the design of tooling. This speeds up the whole process and results in better tool designs.
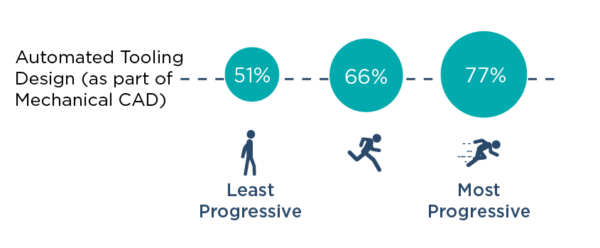
- The ability to define, explore, and manage machining toolpaths; and the ability to assess, run trade studies on, and improve machining performance. Machinists use these capabilities to vary speeds, feeds, and tools while tracking crucial measures like quality and total operation times. Then they can find the right balance between speed and non-conformances. As shown in the figure below, the most progressive companies are more than 3 times more likely to use these advanced capabilities than the least progressive manufacturers.
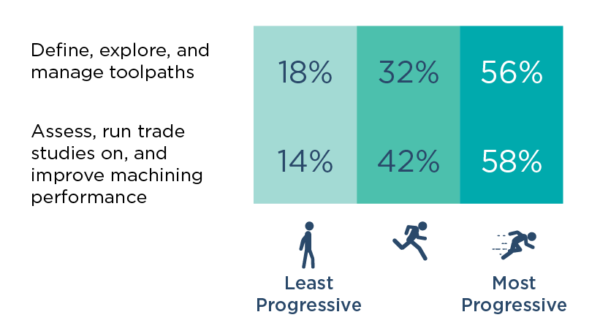
- Solutions that provide automatic toolpath generation for high-speed machining as part of computer-aided manufacturing. Such capabilities incorporate simulation of tooling momentum, allowing machinists to create high-speed machining toolpaths with much less reliance on physical verification of the toolpath. This accelerates ramp-up to production.
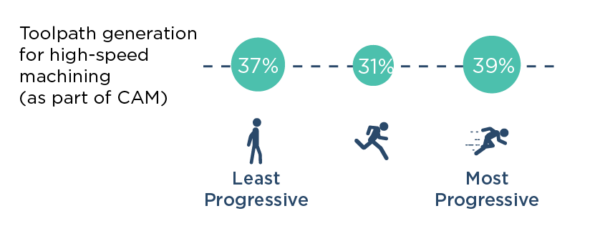
- Toolpath simulation capabilities for verification and validation needs as part of computer-aided manufacturing. Machinists leverage this capability to make sure that the toolpath does what was intended, reducing broken tools, scrap, rework, and even avoiding equipment damage. According to this study, the most progressive companies are almost 50% more likely to leverage toolpath simulation capabilities than the least progressive part manufacturers.
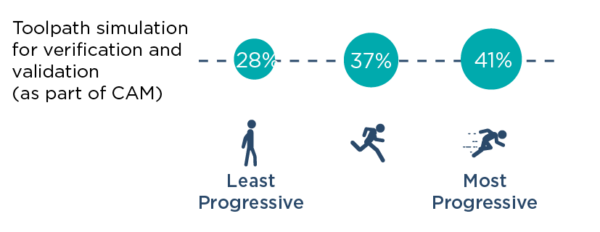
Each of these capabilities contribute to higher levels of manufacturing throughput by exploring, iterating, and finding better ways to execute the production of parts and components.
What We’re Doing at Siemens
At Siemens, our mission is to help manufacturers realize the benefits of DX initiatives as highlighted in this study. As such, we have invested heavily in our part manufacturing offerings to provide the exact solutions discussed in the previous section. In our most recent releases of NX for Manufacturing, we have delivered new, exciting capabilities that help companies achieve success in their pursuit of DX.
Here are a few highlights.
- Fast and efficient software for mold making: Siemens’ NX CAM simulation tools helps iMFLUX deliver precision plastic molds by automating and streamlining the entire mold development process. From mold design to motion validation to machining, NX uses the digital twin to simulate the mold and any downstream steps with limited manual input.
- High-performance milling techniques for 3D machining: Siemens’ NX CAM offers a variety of high-performance milling techniques, including adaptive milling, spiral finish, flow milling, and planar deburring. Such automation enhancements offer significant ROI in machining technologies by helping organizations achieve unparalleled levels of accuracy, surface finish, and efficiency.
- Customer-inspired enhancements in NX for manufacturing: As the NX suite of tools continues to evolve, Siemens is listening carefully to provide new tools and capabilities to support manufacturers of all shapes and sizes.
To learn how manufacturing leaders digitally transform their business to stay ahead, read The executive’s guide to digital manufacturing ebook available here.