Improving visibility using tomorrow’s machine shop management
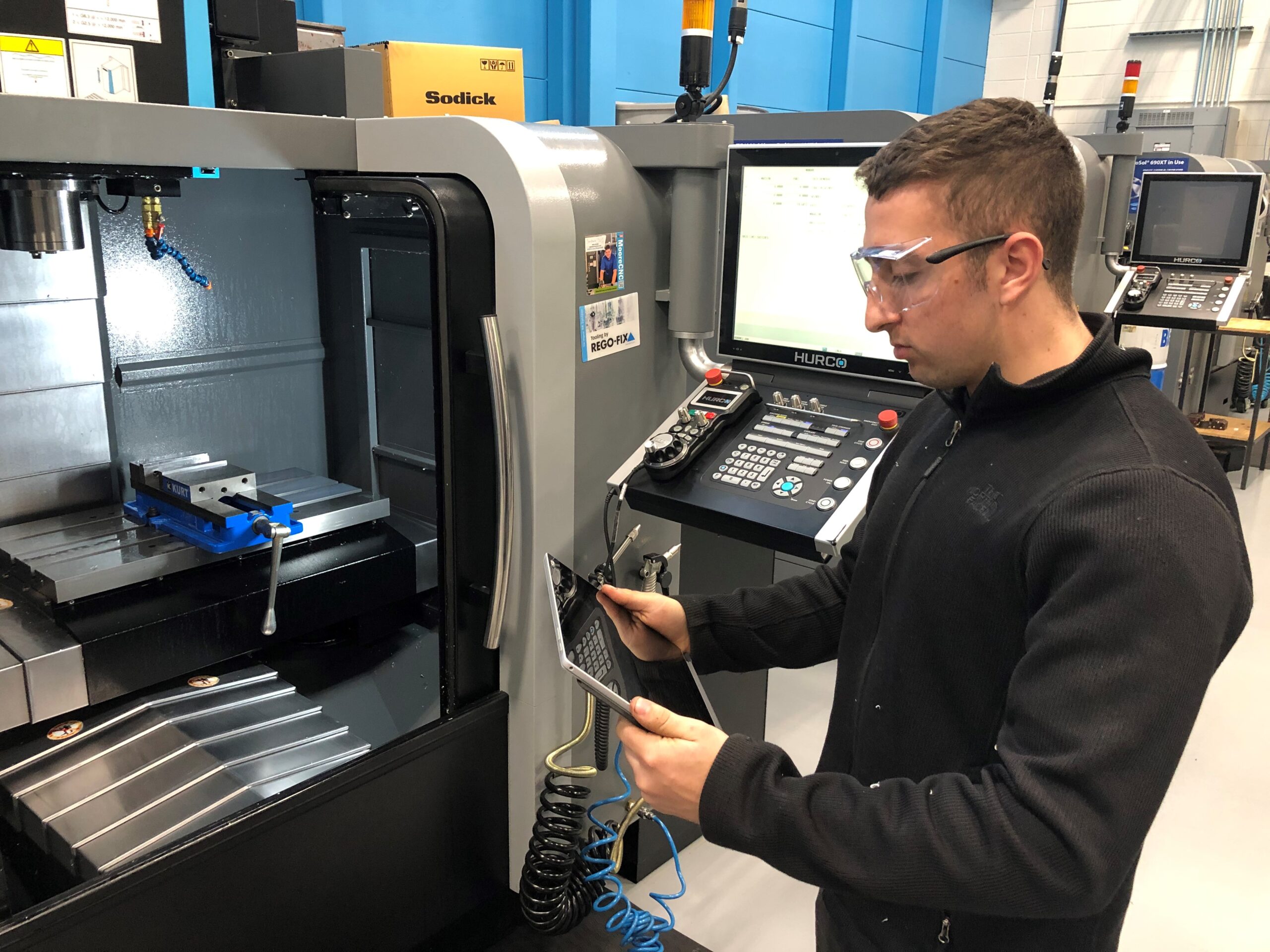
Welcome back to our blog series on machine shop efficiency. As mentioned in the introductory blog, I’ve been working in this industry for the better part of 20 years. My positions have ranged from production to CAM programming to tooling design in the automotive, aerospace, and machinery industries. These jobs have allowed me to see all aspects of machine shops – the good, the bad, and the ugly. When things get ugly, we usually find a lack of communication, or miscommunication, as the main culprit. The root cause is almost always related to paper-based machine shop management.
Job shops are a fast-paced, demanding environment with a lot of moving parts. As such, it can be difficult at times for managers and employees to keep track of the work in progress. Often times, job details are filled in on paper, using assumptions based on incomplete information. When those assumptions are incorrect, wasted time and resources result in decreased profit.
First-hand experience in machine shop management – selecting jobs
There was an instance when miscommunication cost my company an entire day of wages when the wrong job was worked on. At the time, I was recently hired as a CAM programmer in a Michigan-based tooling shop. The company itself was also fairly new and didn’t have their standard operating procedures refined yet.
After finishing a set of work, I was in need of a new part to program and took what was available in the job queue. Without anyone managing the machine shop assignments, it was a free-for-all system of first-come, first-served. The job was typical 3+2 axis milling work, which I’ve done plenty of times before in this industry. It took most of the day to complete the process planning and tool path calculation time. When everything was finished, my milling plan was submitted to the rest of the machine department for setup and run time. CAM files, setup sheets, and G-code were all well prepared for consumption by the next stage in the process.
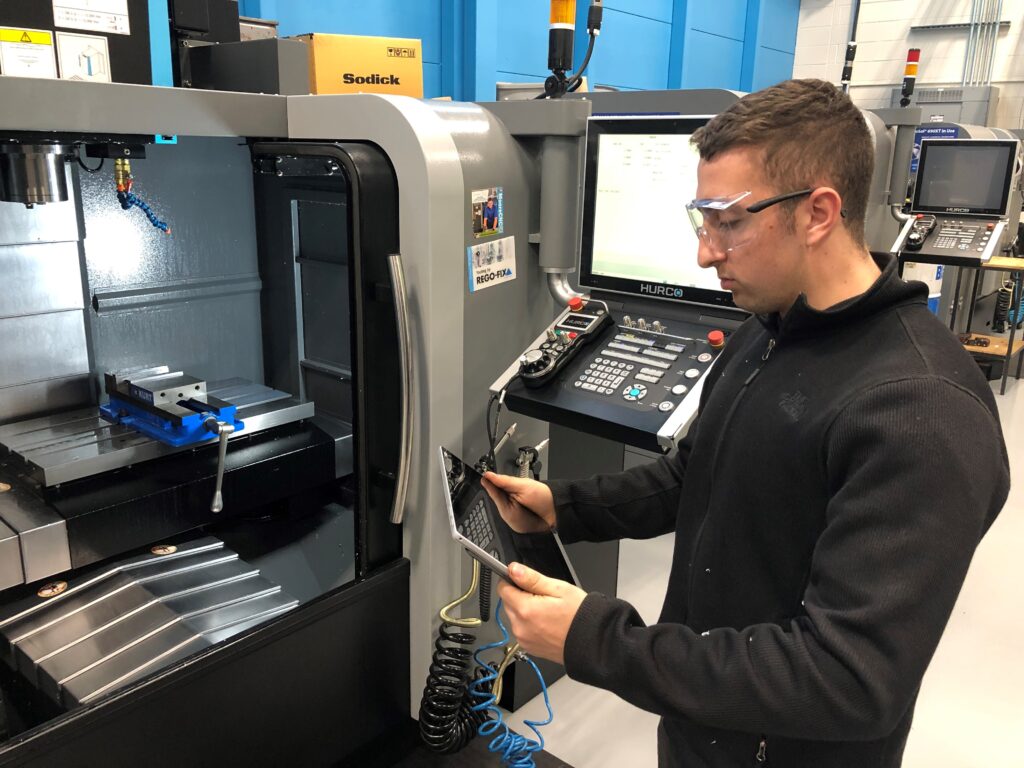
Doubled up due to machine shop miscommunication
Unfortunately, this is where the truth came to light. Another programmer had taken the job and programmed it before me. The job was already in the process of being set up and run with the other programs. The other programmer worked in a different area of the job shop; where they were on the shop floor doing both programming and machining, I was a full-time programmer. We had different immediate managers at the time, which caused some confusion and exasperation for all involved.
The issue was obvious. The proper mechanisms of directing work and managing jobs were not in place. The job appeared to be available for programming, but nothing signaled that someone else had already taken it. The result was valuable time wasted – not only mine, but the time of our managers and other employees as we tried to figure out what happened.
The larger problem – the cost of inefficient machine shop management
This type of mishap is indicative of an environment without automated systems support, standard processes, and scheduling. Take my small example and apply it to a machine shop with many programmers. Consider the impact on production efficiency and cost if this same inefficiency is present in the entire workflow of the machine shop. If the example from above happens here, then it is surely the tip of the iceberg for the total fallout from poor communication.
However, sometimes a small job shop can’t afford to hire a full-time manager to assign every task. In fact, the smaller the shop, the more responsibilities fall on each employee and manager to keep things running smoothly. This leaves little time to worry about what others are doing.
Paper travelers have been used as a solution in many shops for decades. A job packet is printed and kept in a folder, allowing every employee handling the job in progress informed of the expected work. The problem arises when things change. In today’s fast-paced, digital age where changes happen quickly, a physical paper trail has a hard time keeping up.
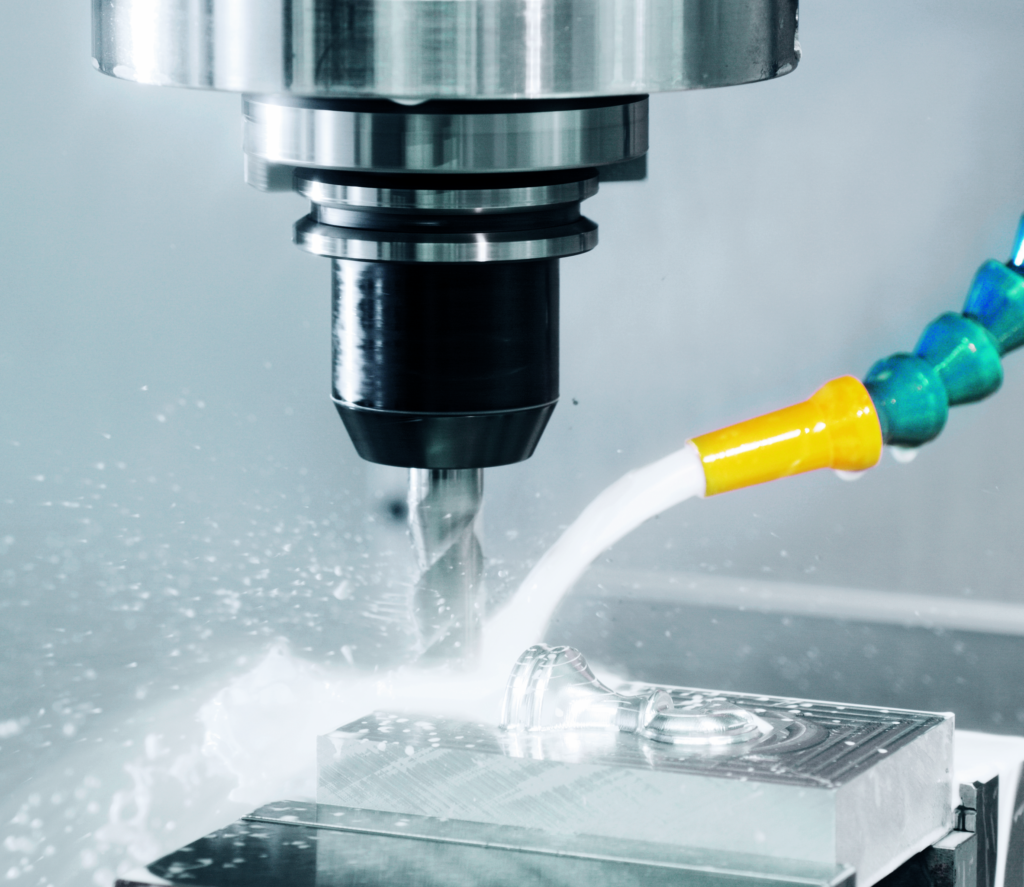
Solutions for today’s small- and medium-sized machine shops
There are, of course, ERP systems available to help with machine shop management. Resources can be defined in a system that is kept up to date with relevant job details and current file revisions. The downside for the smaller job shops is that these systems are often too complex and too expensive. You often see a smaller machine shop pay for functionality that is not necessary for their daily needs. It not only adds complexity and implementation time, but a full-time IT staff required to maintain the system.
What is needed for these smaller machine shops is an affordable yet powerful solution that is simple enough for everyone in the shop to use and requires little or no attention from IT staff. Machine shops have workers that have varied levels of technological skills. The solution must be easily usable by every level of skilled worker.
So, how do we create that type of solution? By tailoring it specifically to the needs of the small- to medium- machine shop environment.
Stay tuned to find out more!
Check out the first blog in the series: Finely Tuned Machine Shops: How to get your shop running smoothly.