EV component manufacturing – part 1
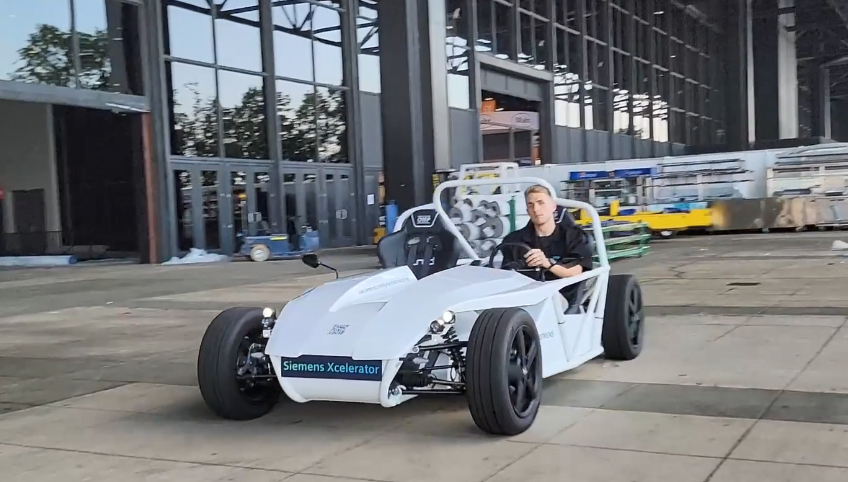
The digital machine shop advantage
We talk about the concept and benefits of digital transformation all the time, but how do all the functions and disciplines of manufacturing design, optimization, and production work together to create superior products? What are they actually doing, and how do they employ digital manufacturing software to assist them? In this blog series we get down to a real manufacturing application with insights from industry experts who will guide us through the process.
Using a real example in EV component manufacturing, we will take you step by step through this entire process, with technical details about the following functions:
- Data management for seamless digital manufacturing
- Design and Additive Manufacturing (AM)
- NC programming using Computer-aided manufacturing (CAM)
- Coordinate measuring machine (CMM) inspection programming
- CNC machining
- The digital manufacturing ecosystem – bringing together trusted solutions
The manufacturing challenge
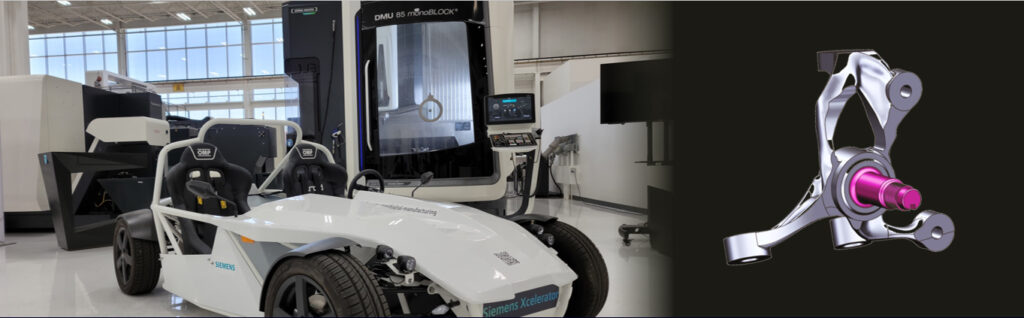
First, let’s look at the challenge we are facing for this specific job. We have an electric sports car that we would like to upgrade with higher performance components to exceed existing specifications. The current model uses standard parts and components that are too heavy for this dynamic vehicle. We need to redesign parts to optimize the vehicle performance and manufacture cost efficiently.
In this application, we will focus on the steering knuckle which is an unsprung mass that we need to make lighter weight and stronger. There was some initial redesign work done using generative design and 3D printing to optimize this part. The results looked “cool,” but couldn’t be manufactured in an industrial process. One of the problems was that the part was not designed with post 3D-printing operations in mind, thus part fixtures for the required machining operations were complicated and expensive with a long lead time. This can be a show-stopper to industrialize a manufacturing process.
When we started, we faced challenges that are not uncommon when manufacturers use off-the-shelve components. We had the CAD 3D model, but no drawings, no defined tolerances, no material information, and no manufacturing instructions. We were starting from scratch. This is a common frustration when engineers are faced with optimizing an existing part.
We further had to consider that not every part that can be 3D printed should be 3D printed. For instance, we looked at the wheel spindle and found that it was not a dominating weight factor and could be easily machined on a simple lathe from bar stock. Every minute, one of these spindles can drop into the part catcher, making an efficient and simple process. Further, all support structures need to be removable on the CNC machine so there would be no hand labor and manual part clean-up required. Ultimately, we chose to redesign the steering knuckle and take that part through a real-world process that would result in a light-weight product that could actually be manufactured in an industrial environment. At the same time, we wanted to increase the quality and durability of the part, and significantly exceed existing component performance. Lastly, the manufacturing of the part must be cost effective, which requires an effective engineering and production process.
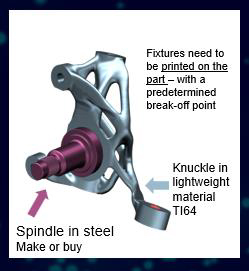
Why take a digital machine Shop approach?
The digital machine shop provides some powerful benefits to manufacturers. It is a data-driven manufacturing environment that seamlessly connects your engineering, process, machines, robots, equipment, and all the other elements of your operation. The digital machine shop provides an infrastructure for speed, quality, and efficiency, and that’s why we utilize this approach.
The digital machine shop provides a seamless flow of information across the steps that must be taken from order to delivery. The typical process in a machine shop is common to small and large operations and is shown in the diagram below.
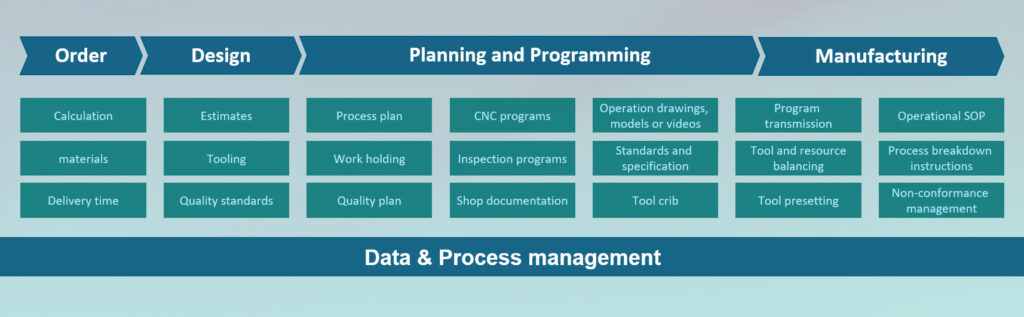
In a traditional machine shop, without a digital manufacturing infrastructure, this work would be done in silos by the respective experts. In our example, the five engineering specialists might generate 26 or more divergent versions in a single week, lacking alignment with one another. It is a slow process with lots of interface discussions, no real concurrent work, and many variants that are incompatible with each other. Additionally, the biggest concern with the conventional approach – the manufacturing teams on the shop floor can never be sure if they use the latest revision to manufacture the part.
To address this issue during the redesign and production of our steering knuckle, we leveraged the Siemens Xcelerator portfolio that powers the digital machine shop.
Below are the key steps of the process starting from design all the way to manufacturing and inspection.
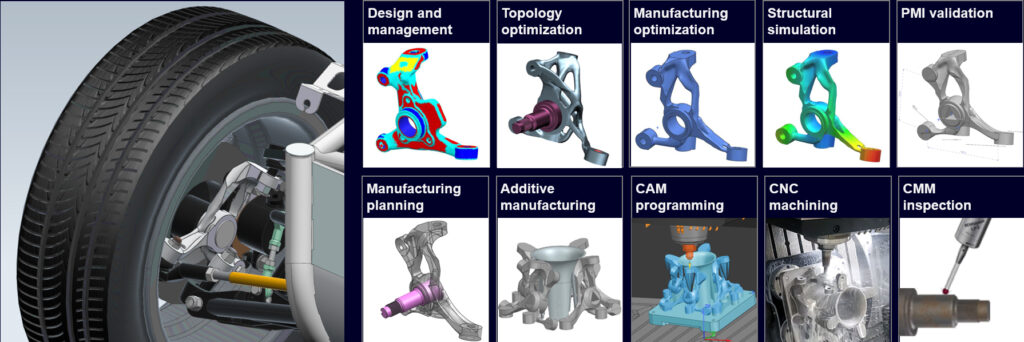
That’s it for today. Hope to see you for the next post when we dive deeper into the remaining parts of this blog series. In future posts, we will detail each of these production steps, and how the Siemens digital manufacturing technology connects them to create a more collaborative, efficient process that results in a higher quality outcome. We will show how the larger team – internal functions, contractors, and sub-suppliers – can access all relevant data, design iterations, and collaborate in real time.
We will discuss real world challenges including:
- How do I know if a part can be 3D printed in this design?
- If the additive manufacturing engineer makes changes, is my part still structurally sound?
- Should we have the “fixtures” printed with the part?
- Can all dimensional features be accessed on the CNC machine with standard tools and without collision?
- Can all support structures be removed on the machine, and can we avoid dust exposure?
Check out part 2 to learn how to use today’s technology to realize your digital machine shop.