CERATIZIT and SIEMENS program novel machine tooling
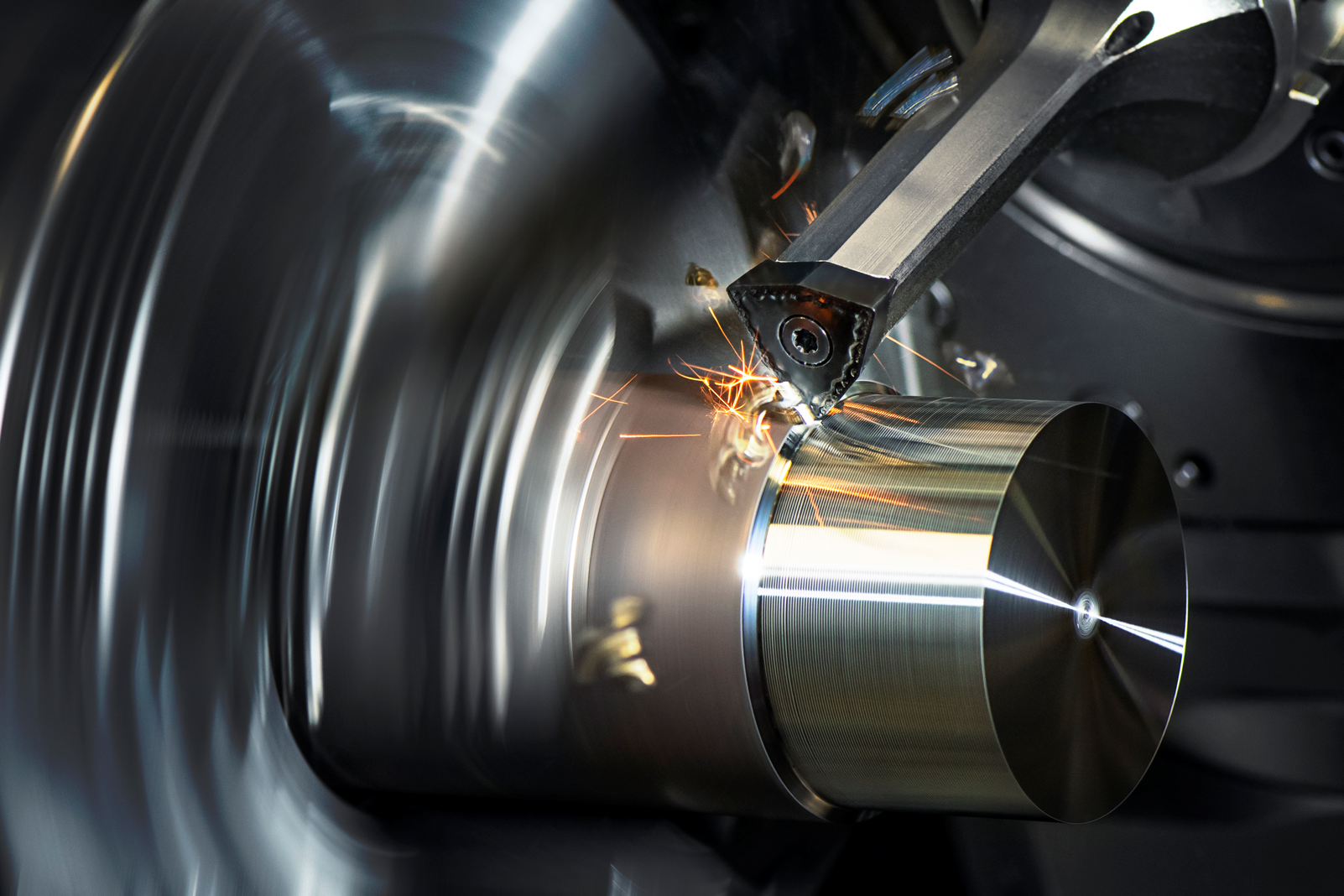
NX CAM software provides easy, safe, and fast programming of simultaneous three-axis turning tools
When Cerametal and Plansee Tizit merged in 2002 to form CERATIZIT, the new enterprise remained committed to the same innovative spirit and focus that its predecessor companies had sustained for nearly eight decades. Now, a century into producing wear-protection and cutting tools, Luxembourg-based CERATIZIT has grown to a global player in the powder metallurgy industry, with 30 production sites and 8,000 employees around the world. One of the company’s latest innovations helps reduce the number of tool changes required in a machining job – and it also challenges the Siemens software machine programming capabilities. “Siemens NX™ software is supporting this new technology to make it reliable for the user,” reports Patrick Zobl, CERATIZIT project leader.
At Realize LIVE 2021, Siemens’ global customer event, Zobl presented CERATIZIT’s new turning tool technology and demonstrated the easy programming provided by NX CAM software for this revolutionary product. This blog summarizes the presentation.
The manufacturing challenge
“Turning, in its most basic form, hasn’t changed in decades,” Zobl says of the manufacturing arena in which CERATIZIT’s new FreeTurn tool operates. A traditional turning lathe offers a static tool configuration in which only the cutting speed and depth can be changed. “If you need a different approach – a different direction of cut or other adaptations – you always have to change the tool,” he explains. “For that reason, the catalogs for turning tools are pretty thick, and you have thousands of options to choose from.”
The FreeTurn tool extends turning from a two-directional to a three-directional operation, which CERATIZIT has designated “high dynamic turning.” The tool incorporates three cutting edges in various configurations; the one demonstrated at Realize LIVE included two edges with a roughing geometry and one for finishing. High dynamic turning uses the milling spindle in a multipurpose computer numeric control (CNC) machine to enable machining in the third direction. “You are completely free to change the approach angle, even during the cut,” Zobl says. With this flexibility, a single tool can be used lefthanded or righthanded or in the overhead position, and a change to a different cutting edge can be performed on the fly. The tool can switch directions to cut back and forth, which helps minimize noncutting time. The right-hand and left-hand capability also improve tool life compared to machining in one direction.
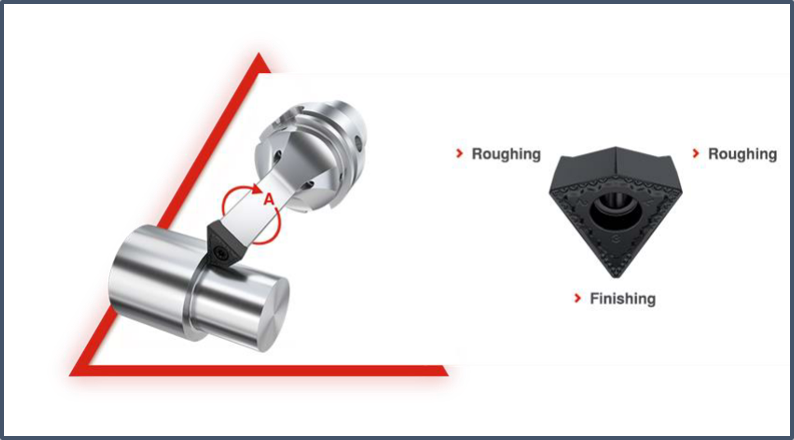
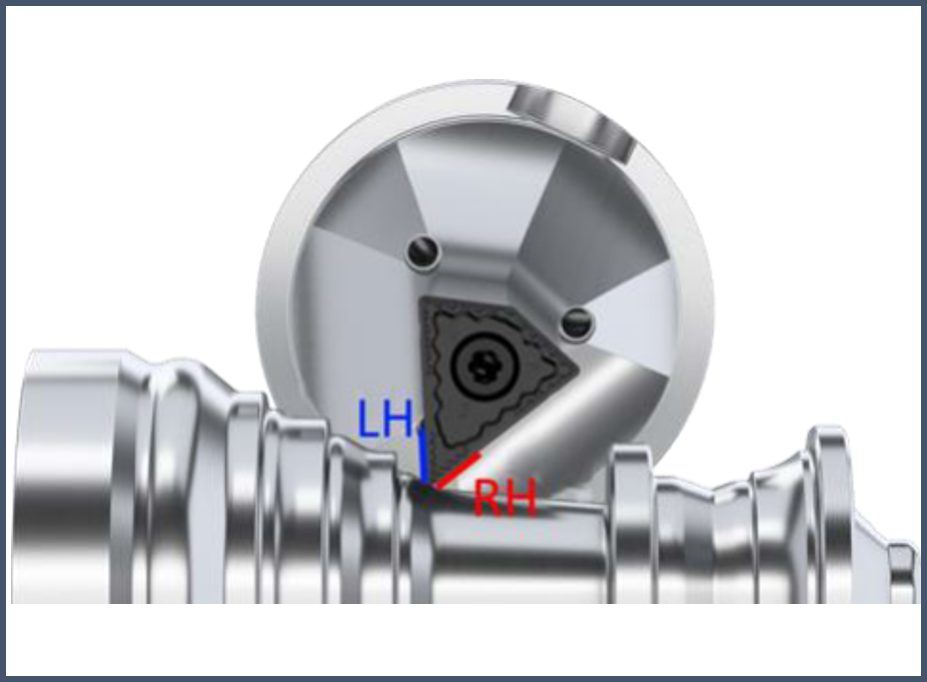
Adding a dimension to a CNC tool’s cutting capability is indeed revolutionary; but it raises new challenges if a machinist is going to successfully employ the new functionality. “Immediately the question comes up, how to program the motion of the tool. This is the point where NX CAM comes into play,” Zobl states.
Programming high dynamic turning
CERATIZIT has enjoyed a long, fruitful relationship with Siemens and NX software. The company uses the NX family of products in R&D, design, and production at its facilities. With the launch of FreeTurn tooling, Siemens has developed solutions for programming machining sequences specific to the high dynamic turning process.
The Siemens NX software family has been designed and developed to support every aspect of product development, from concept design through engineering and manufacturing. For programming of high dynamic turning, CERATIZIT uses NX CAM, which is part of the NX for Manufacturing software portfolio. NX CAM provides comprehensive and integrated NC programming capabilities in a single system.
Valuable features of NX CAM for high dynamic turning start with the digital twin of the machining center. This digital twin supports precision programming and simulation, enabling the programmer to visualize tool paths within the CNC work envelope. NX CAM also provides a digital twin of the workpiece and chuck. Zobl points out that the programmer can use all the standard operations in NX CAM when programming a FreeTurn tool: facing, rough turn, pocketing, smoothing, finishing, and more. NX CAM also supports FreeTurn with different tool strategies, such as linear zigzag and ramping zigzag. “For the programmer in their daily work, FreeTurn is programmed almost the same as a standard tool,” Zobl reports.
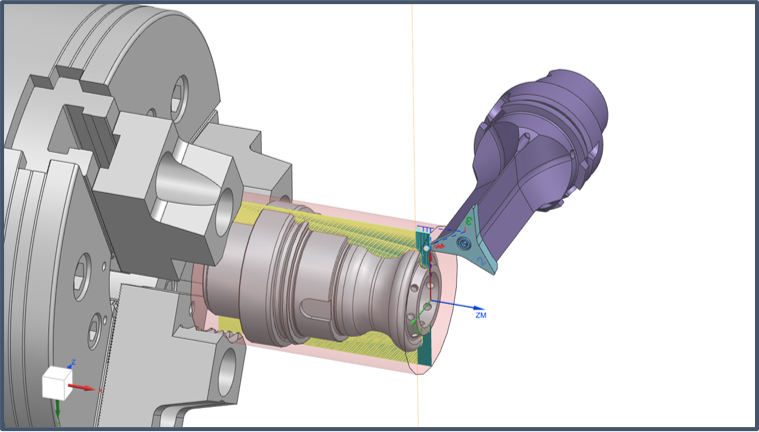
Specific to high dynamic tooling, the programmer can change the orientation of the tool for any operation in the tool settings for the tool holder angle. Another important feature of NX CAM is its automatic feed rate computation. When the chip thickness is entered, NX uses the angle of approach and computes the required feed to achieve the average chip thickness desired. In finishing operations, NX CAM enables tool path definition with numerous interpolation vectors to reflect the dynamic motion of the FreeTurn tool. Three-dimensional visual feedback alerts programmers to any risk of collision in tight spaces and enables them to confirm the safety of the tool path.
Using a FreeTurn tool on a multitasking machining center also may include programming of the main spindle as well as a sub-spindle. NX CAM supports this machining technology very well, Zobl reports, allowing the same programming to be performed on the sub-spindle as on the main spindle. Additionally, NX CAM simulation can show the FreeTurn operation sequenced with drilling and milling operations on the main and sub-spindle.
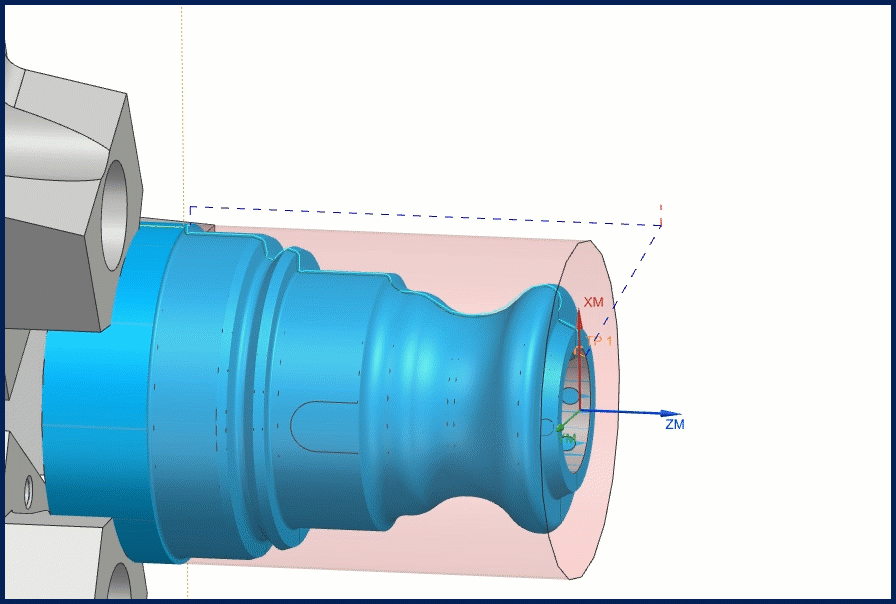
Benefits of high dynamic turning
NX CAM software is a key element of FreeTurn’s success in accelerating machining operations. One practical demonstration of the system resulted in a 75 percent increase in roughing feed rate, a 33 percent increase in finishing cutting speed, and a reduction in the number of tools required from three down to one. Eliminating tool changes is one of the biggest competitive advantages of the FreeTurn system with NX CAM programming. Another way to look at it, Zobl notes, is that high dynamic turning reduces a “tool change” down to a change in the cutting edge being used on the FreeTurn tool. “With the FreeTurn tool, you have the possibility to have the smallest tool change system in the world!” he says.
With innovation continuing to be a centerpiece of CERATIZIT’s work, greater advances in machining speed and precision should be expected. Siemens NX CAM software will continue to support these exciting efforts.
—–