Siemens Xcelerator | Advanced Machine Engineering | Part Four
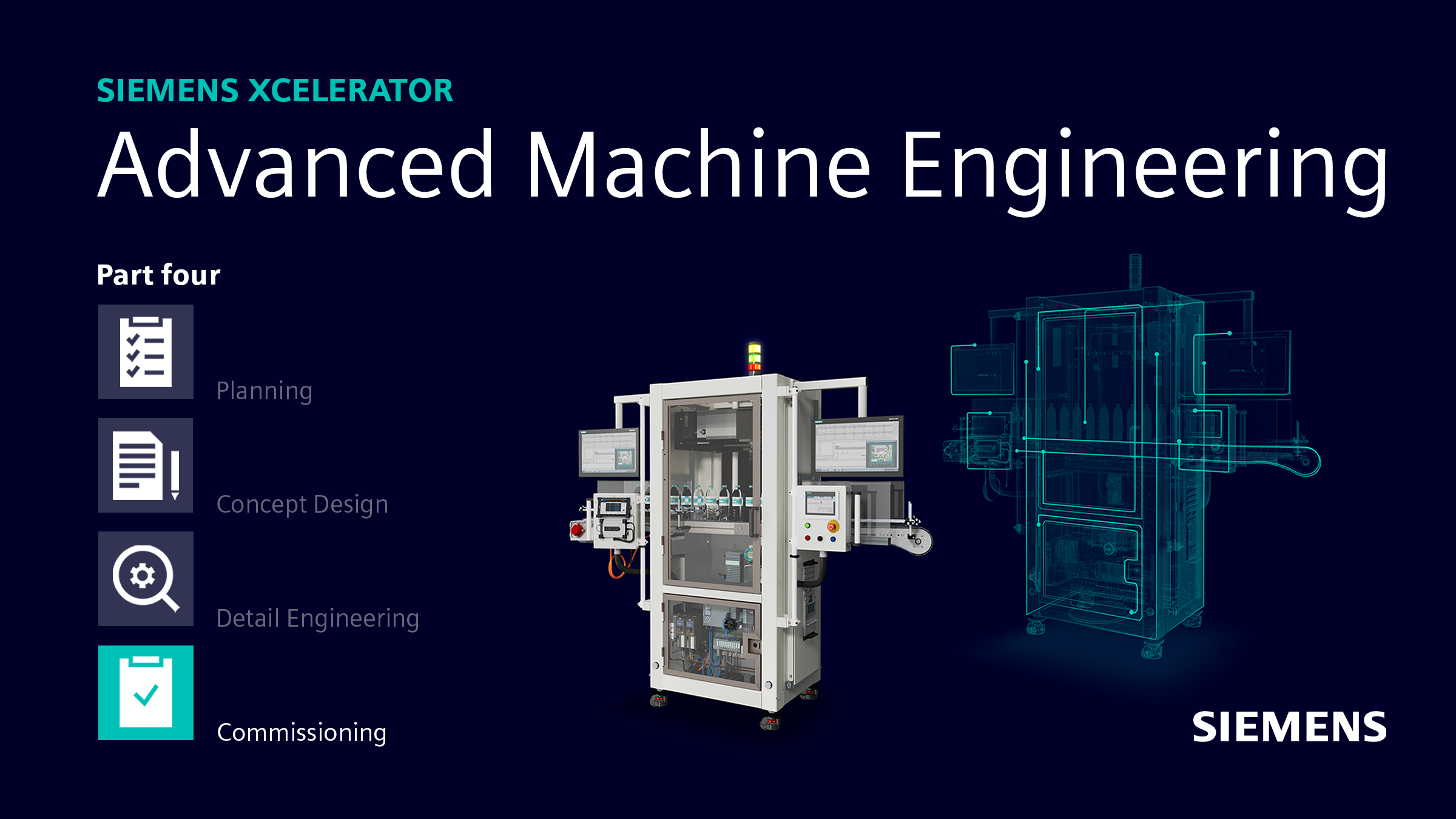
The fourth and final installment of our Advanced Machine Engineering series is here. We will be covering how commissioning with Siemens Xcelerator will enable you to save time and money while increasing the quality of your designs. This can all be accomplished due to the digital landscape that we live in today. From locating flaws earlier within the commissioning process to the ability to train equipment operators virtually, Siemens Xcelerator leads the market in virtually validating designs. Come along as we locate specific functionality that separates us from the competition.
Physical commissioning versus virtual commissioning
Cost reducing process
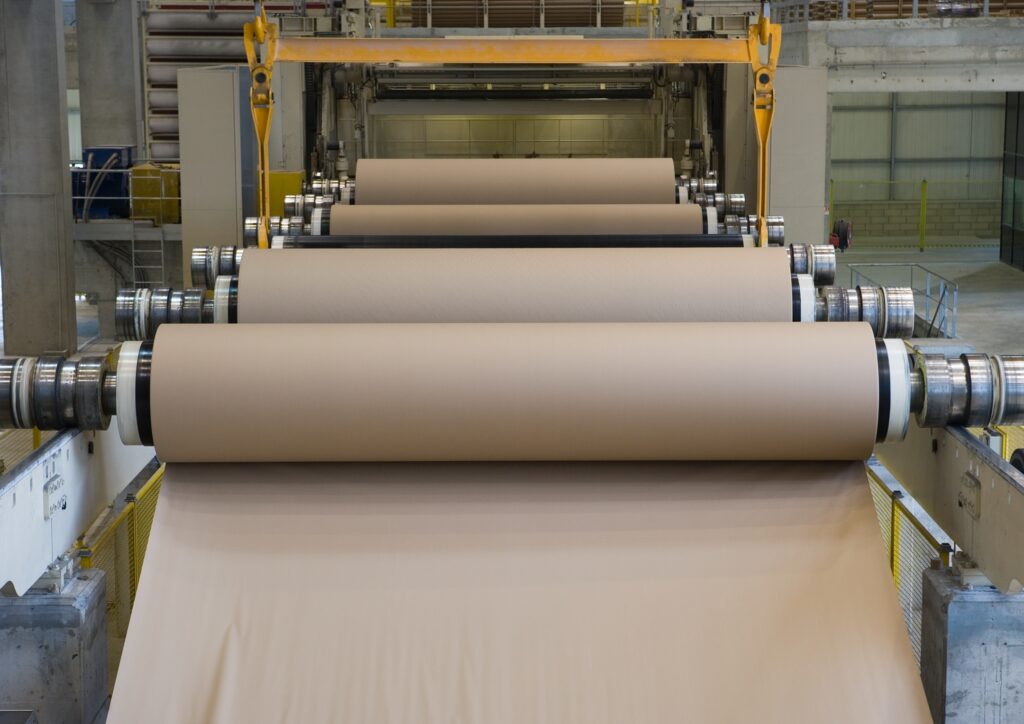
Let’s be honest here — saving money is something that everyone values. This stems from a profitability standpoint as well as security for you and other employees. By utilizing Siemens’ digital twin, this allows you to virtually vet all your designs. When you do not work through issues virtually, you will have to make those changes directly on the shop floor or assembly line. By doing so, this also takes away time that the machine is inoperable, and no product is being produced. This leads us directly into another area where Siemens Xcelerator can improve your workflow.
Time saving efficiency
Being able to design innovative products faster than before is all due to embracing the Siemens Xcelerator suite. With open, flexible, and fully integrated pieces of the factory automation process tied to software, this leads to shorter time-to-delivery — all while cutting costs. This is great news for the industry and something that leads to higher quality products that stand up to the test of time.
Using the digital twin to find issues
Quality assurance
Some of the biggest issues seen in the commissioning process are tied back to errors made early in the design process. Before virtual commissioning, these were only caught when there was a fault in the equipment, but by utilizing virtual commissioning, these are corrected earlier on. Utilizing the digital twin experience within NX is key to being able to put eyes on how the design will interact on the shop floor.
One thing that is often overlooked is the physics behind designs. With Siemens Xcelerator, you can look at physics-based simulation to inspect and validate the performance of products and parts. Nobody could foresee a part tipping off the assembly line without actually commissioning the part first. This leads to better designed products that are capability of anything that comes its way.
Mechanically sound designs tied to automation
Another issue is relying on the design to tell the full story. Some designs might look good mechanically, but when they are tied to automation, there could be errors on how parts interact. This is another chance to experiment with simulation without ever having to build a single part. You can reduce rework and prototyping costs by using digital twins to test your designs virtually before commissioning them physically.
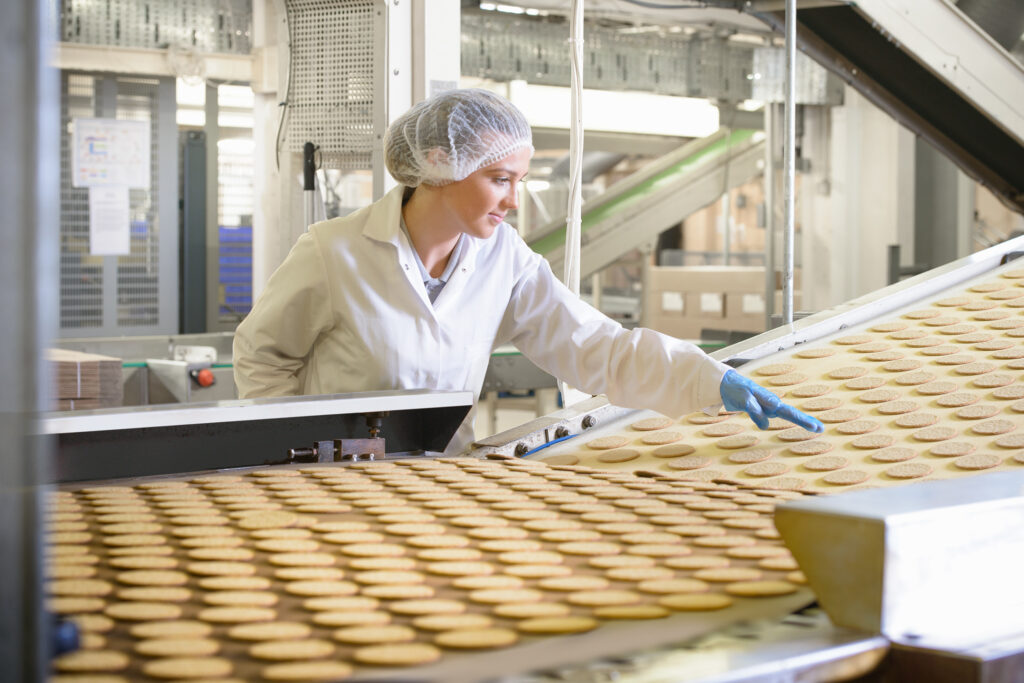
Trained workers before production
A huge advantage is being able to test and simulate automation software with physical hardware to enable the ability to train your workers of the equipment. The advantage of this is that real workers get to see the layout of the hardware and get put into real world situations to be comfortable with machine operation and problem solving. This will reduce errors in the physical world and save down time of equipment when less errors occur. The overwhelming sense of comfortability is a crucial piece to integrating new equipment onto the shop floor. With Siemens Xcelerator, this gives the operators confidence as well as the management confidence for a successful onboarding experience for new factory automation equipment.
Siemens Xcelerator promotes sustainability
The biggest impact of Siemens Xcelerator within factory automation is how it creates more sustainable companies. If you are not constantly rebuilding, using raw materials, electric, gas, and polluting the environment to rebuild broken parts from testing, this not only helps the environment, but helps companies reach their sustainability goals. When you virtually commission your products, the only time materials are used are doing the final build process. The entire process of testing products and waste is eliminated.
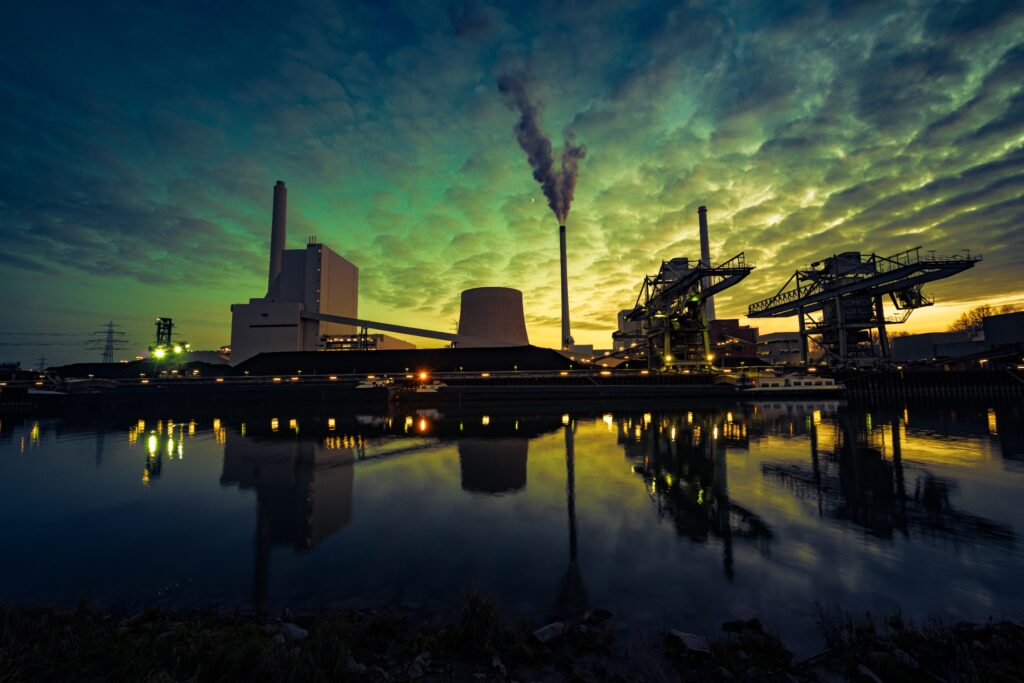
Continue your journey with the Siemens Xcelerator Suite
We hope that you have enjoyed this series. Stepping through each phase of the factory automation process showcases how involved the Siemens Xcelerator Suite truly is. From more efficient designs to vetting virtually through simulation, partnering these products is key to increasing productivity, cutting costs, and reducing waste. Follow the links below to continue to learn more about Siemens products.