How Mold Makers Can Improve Their Business
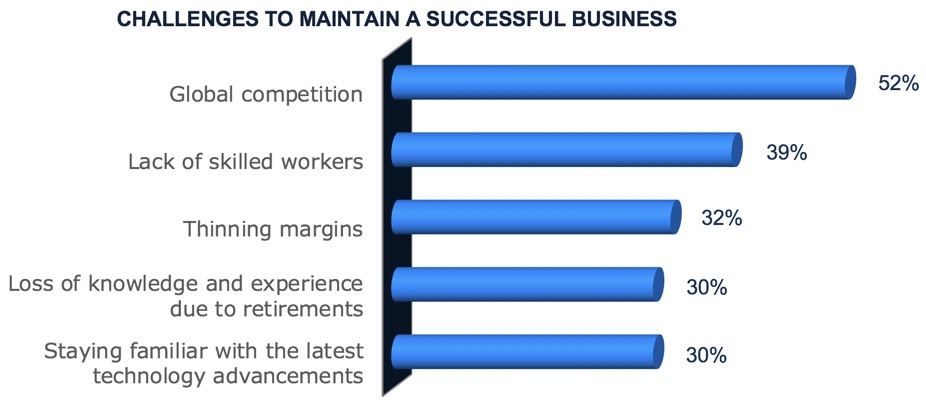
The Business of Mold Making
Mold making is a challenging business. Not only is the process of injection molding incredibly complex from a technical perspective, but the business pressures are also significant. In a recent Tech-Clarity study, we surveyed over 370 mold makers to identify the current challenges facing mold makers today and what it takes to succeed. The respondents included a mix of mold makers that are part of a larger company (42% of respondents) and those that are independent job shops (58% of respondents). The research finds that while there are numerous challenges, there are also opportunities to stand out. Those who have transformed their processes by adopting the technologies of 2020 are finding much success.
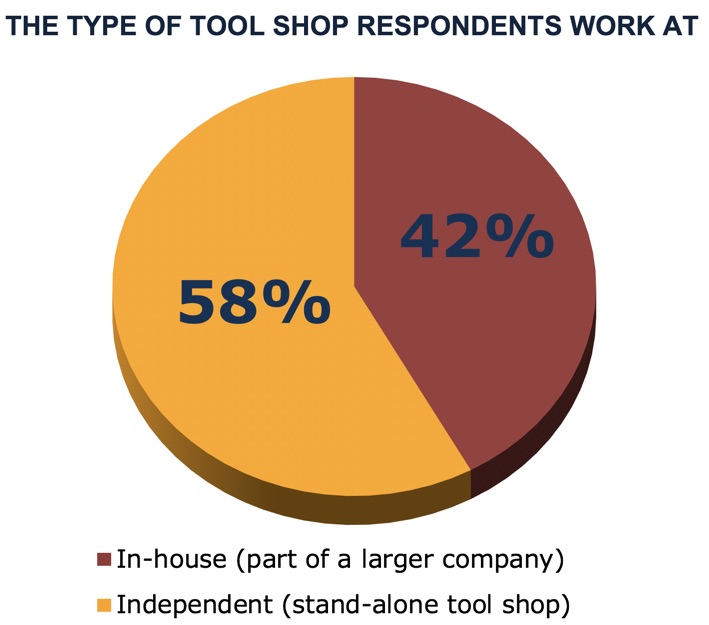
Challenges Facing Mold Makers
Today’s mold makers face many obstacles. The graph shows the top five challenges that must be addressed to maintain a successful business. The challenges can be grouped into three main categories:
- Business trends
- Worker knowledge
- Technology advancements
With strategies in place to successfully address these challenges, mold makers will enjoy a competitive advantage.
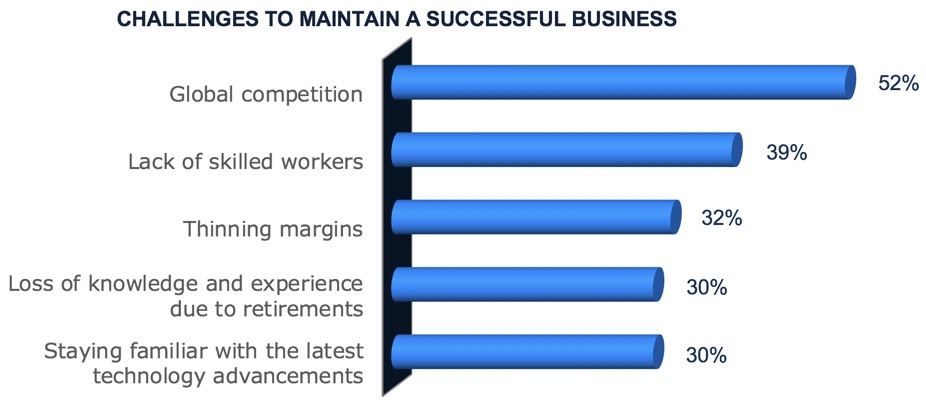
Business Trends
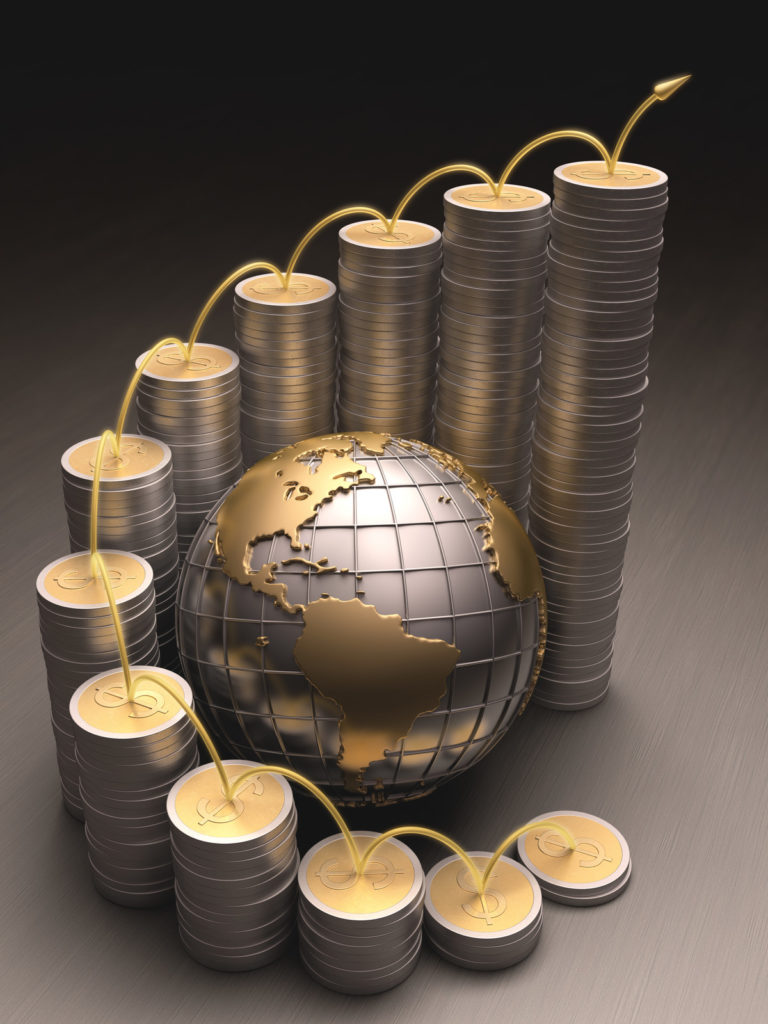
Technology, and the internet in particular, has made the world smaller. It has made it easier to identify and reach international partners and suppliers. Consequently, mold makers have seen a rise in global competition. Rather than competing against a few local or domestic toolmakers, now they compete with others around the world. As a result, they need to offer more for their bid to stand out.
Further, to be price competitive with lower-cost regions, mold makers may need to lower prices, which cuts into already thinning margins. Unfortunately, this leaves very little cushion for things to go wrong. Challenges around worker knowledge compound this challenge further.
Worker Knowledge
Developing and producing molds requires significant expertise. You need a good understanding of plastics behavior, thermodynamics, machining practices, and more. Consequently, mold makers require highly skilled workers. Further, as injection molding technology has advanced, the requirements for technically skilled workers have only increased. Unfortunately, the number of workers with this skill set is limited, and it takes a long time to develop the expertise. Adding to the challenge, many of the most experienced workers are approaching retirement and with that, their knowledge will be lost to the company. This will create even more demand for the already limited pool of qualified staff.
Technology Advancements
While there is already a huge demand for knowledgeable workers, technology is continuously advancing, moving the bar even further. It is hard to keep up with all the advancements. Developments in materials, including fillers, impact how the plastic will flow into the mold. New cooling techniques such as conformal cooling channels influence the mold design. New manufacturing approaches, such as 3D printing, drive new approaches to production. Therefore, those who can make better decisions to optimize applications for new technology are in the best position to create opportunities and improve their margins, which gives them a competitive edge.
What Strategies Should You Focus On?
So what are the best approaches to address these challenges? To understand this, we identified Top Performing companies. We defined Top Performers as the top 20% of companies who outperform their competitors in metrics that indicate a successful business:
- Revenue growth over the last 24 months
- Product margin expansion over the previous 24 months
- Product cost reduction
We then focused on what Top Performers do, especially what they do differently, compared to their peers.
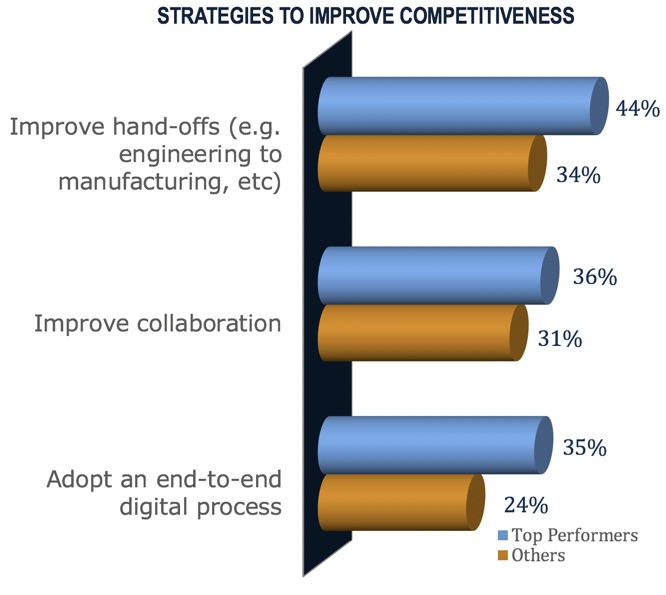
What Top Performers Do Differently
The big difference between Top Performers and their peers is that they are more likely to focus on strategies that allow them to streamline work by supporting an end-to-end process. This improves efficiency, but also leverages their collective knowledge throughout the entire process product development process from the bid, through design, to manufacturing. This helps them save time while reducing the risk of errors, improving quality.
Top Performers are 29% more likely to improve hand-offs. This includes improving the hand-off of the bid to engineering as well as from engineering to manufacturing. This also improves collaboration and supports an end-to-end digital process.
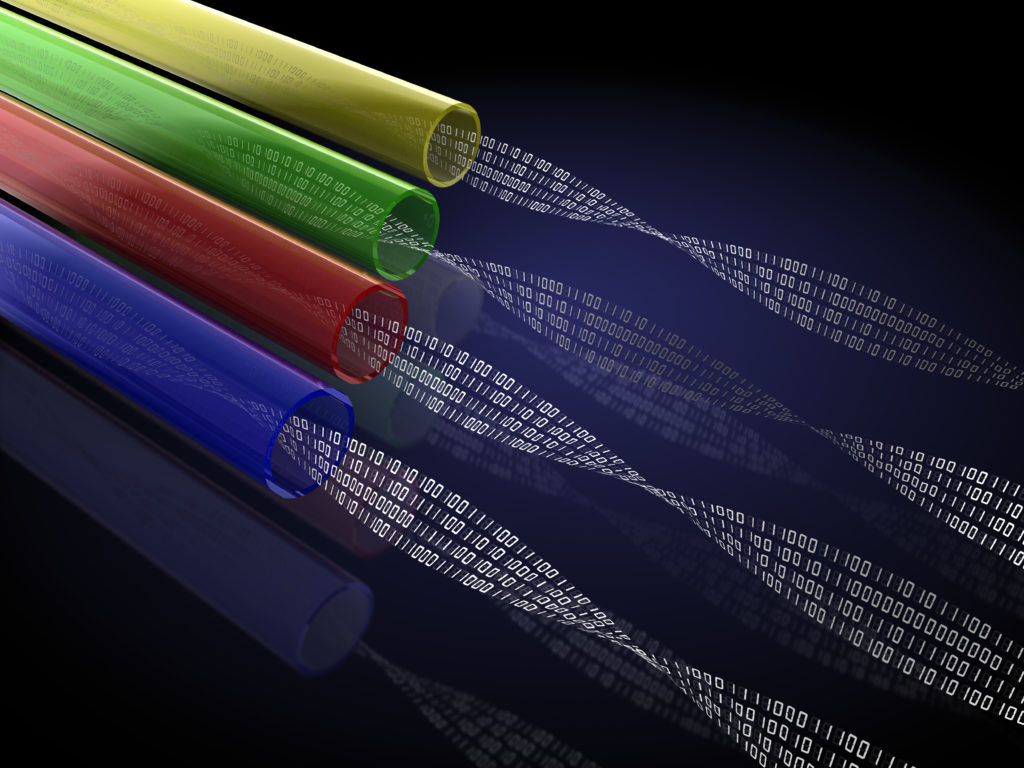
A way to achieve this is by supporting a digital thread across the entire lifecycle. By capturing everything used to develop the quote in a digital model and then handing that off to engineering, not only do you save engineering time, but you also improve communication between sales and engineering. This ensures that engineering work is based on exactly what was quoted. Then, using engineering models to develop tool paths, all the intelligence engineering embedded into the CAD model can be leveraged. Then, should the customer require a change or manufacturing encounter manufacturability issues that require engineering changes, updates to the engineering model will automatically be reflected in the toolpaths. There is traceability across the entire lifecycle, knowledge is shared across domains, and efforts aren’t wasted due to working on outdated information.
Learn More
To learn more about what Top Performing companies do, you can read the entire research study in Tech-Clarity’s new eBook, Breaking the Mold: How Toolmakers Are Transforming Operations to Stay Competitive. This eBook reveals the rest of the survey results and shares recommendations to help mold makers improve their business.
You can also listen to a discussion of the Tech-Clarity survey results as well as learn more about solutions for mold makers by watching this webinar: https://www.plm.automation.siemens.com/global/en/webinar/mold-design-tooling-injection/67702