Implementing information transparency solutions to prove medical device compliance
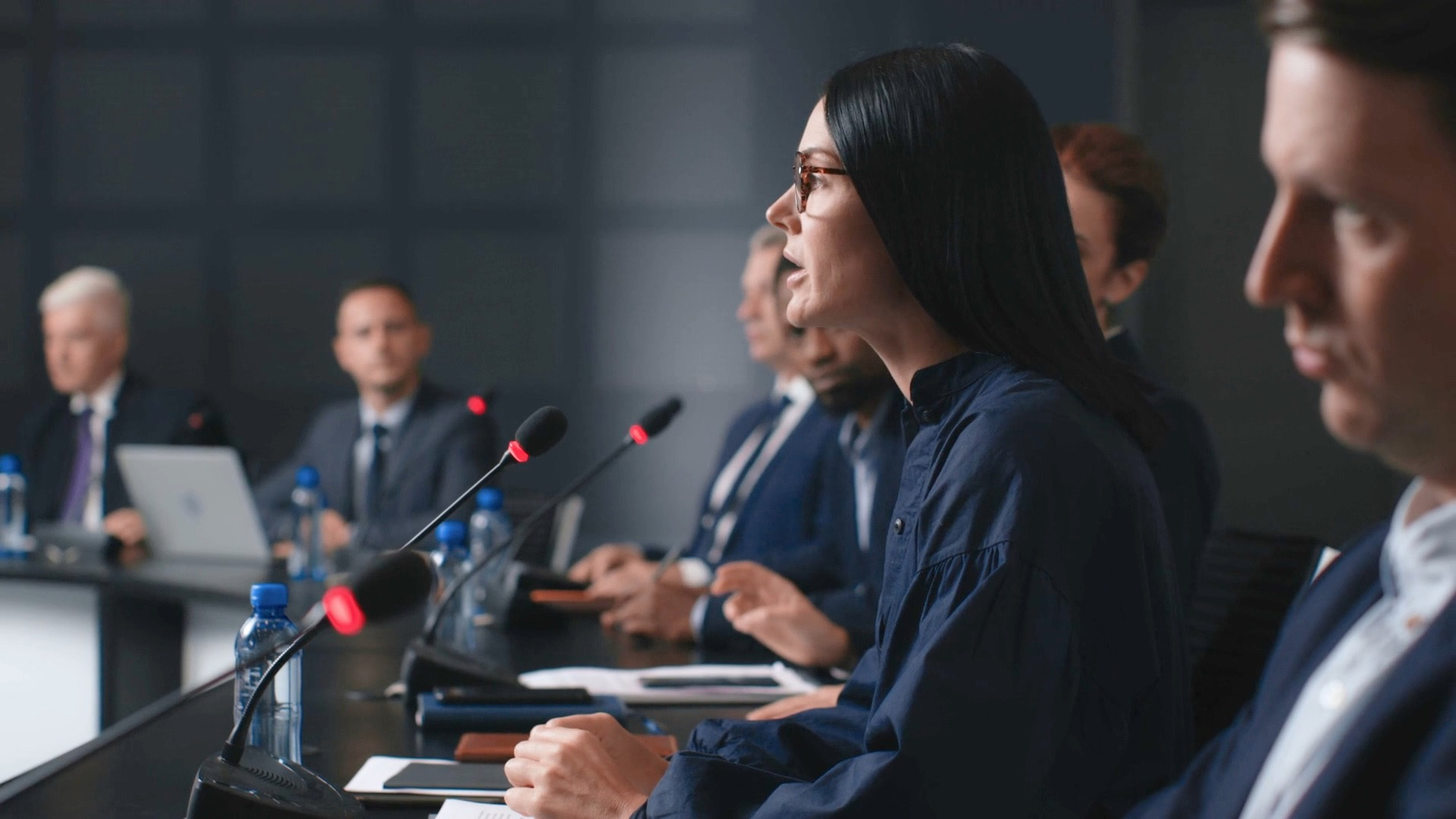
To prove medical device compliance, manufacturers are responsible for providing a wealth of information to the appropriate regulatory bodies. When it’s possible to gain easy access to all information based in a centralized location, you’ll be able to improve your communication with health authorities.
Being able to connect quality processes and data ensures you’ll have the proof that your medical devices are safe, effective and that they meet all necessary regulatory requirements throughout their lifespan.
Focusing on regulatory information transparency
The complexity of requirements makes labor-intensive spreadsheet-based methods unsustainable. Many medical device manufacturers continue to control regulatory information management with disparate systems and manual tracking and, therefore, are putting themselves at risk for not presenting the data needed for compliance.
One pivotal step manufacturers can take to not fall into this trap is by developing a quality-based culture focusing on information transparency. This begins with every employee acting as a part of a complex ecosystem, where quality is a structured way to work. To accomplish regulatory and quality information transparency, medical device manufacturers must shift focus to product quality enhancement through prioritization of better solutions, information and processes. This is especially true for new and innovative medical technologies that can carry patient risk.
Prioritizing compliance enhances product quality as well as benefits new and high-risk medical technologies.
Siemens Closed Loop Quality and Compliance
The right tools enable traceable, controlled regulatory information management and foster interactions with health authorities throughout the product lifecycle.
Siemens Closed Loop Quality and Compliance information tools can:
- Improve compliance
- Boost collaboration
- Enforce correct data
- Accelerate product releases
Enable transparency to internal and external stakeholders
Implementing an integrated data management system ensures the availability of all necessary information, from documents to data. With our Closed Loop Quality and Compliance tools, manufacturers can centralize all medical device compliance data in a streamlined regulatory information management system (RIMS) instead of investing in a standalone system.
This will help connect all data and makes it easy to identify what’s been shared with regulators, including the ability to track deliverables for use outside of the system, and monitor these interactions.
Achieve process efficiency with a comprehensive quality management system
With the goal of increasing information transparency that promotes medical device compliance, users of the Siemens Closed Loop Quality and Compliance tools can expect:
- Data pool to centralize device-related data and process it in an organized way
- PLM integration system that receives product-related device submission and unique device identification (UDI) data as well as external regulatory database submissions
- Electronic signature requiring every stakeholder in the process to sign off once their assigned tasks are completed
- Business logic & set of rules that ensures that required information for registration processes is provided by stakeholders
- Workflows so that all registration steps are processed and that stakeholders know which steps to perform
Efficiency in medical device compliance with information transparency
The more a manufacturer can automate regulatory affairs activities, the greater efficiency they have in meeting medical device compliance, safeguarding data accuracy and improving outcomes.
Siemens Closed Loop Quality and Compliance enhances organizational compliance and continuously acts on medical device quality. Enjoy peace of mind knowing that your team has access to comprehensive up-to-date information for market submission and audits and device quality with continuous monitoring for improved patient safety.
Download the ebook to learn more about information transparency, improve interactions with regulatory authorities and develop a quality-based culture.