SimRodエクスペリエンス: 振動プロファイルを合成し、加振機の加速試験を作成
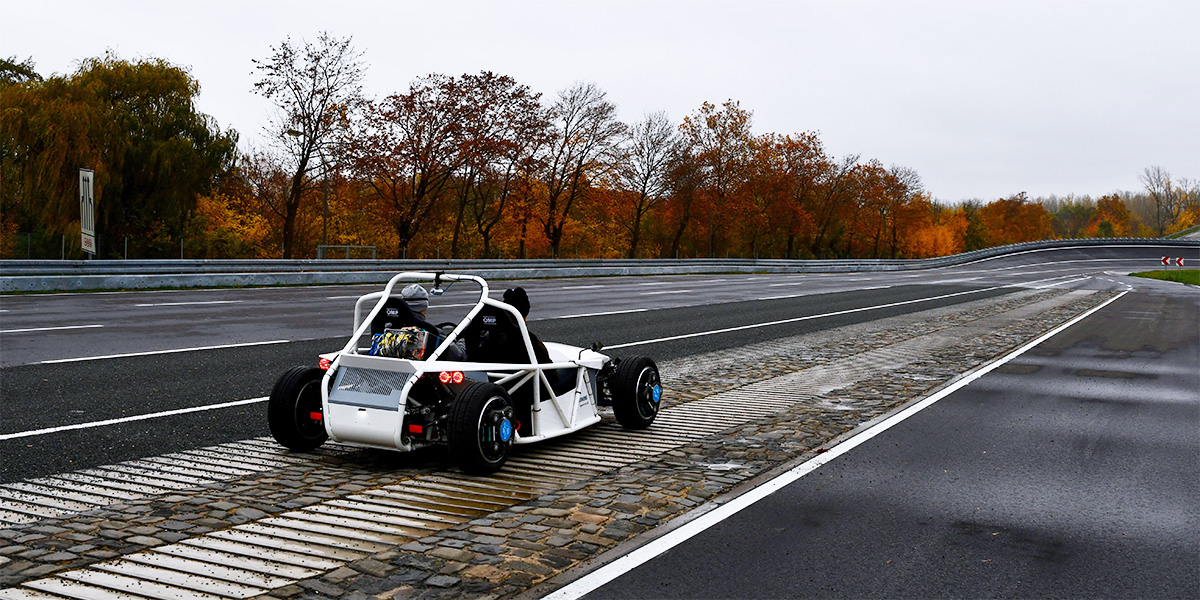
現在の自動車メーカーは、非常に厳しい競争を通じて車両を市場に投入するという状況にあるため、すべてのテスト・エンジニアは、短期間でテストを行うことを余儀なくされています。消費者も、技術的にさまざまな改良が加えられた、エネルギー消費量が少なく耐久性が高い車両を誰よりも早く入手したいと考えています。そのようななかで自動車メーカーが市場における優位性を確保するには、工期を短縮しなければなりません。
車両開発において経営陣が最初に考えるのは、長時間にわたるテストを減らして、時間とコストを削減したいということです (本来は、開発期間の短縮が主な目的で、コスト削減による効果は二次的な理由です)。
しかし、テスト・エンジニアが振動プロファイルを合成して加速加振機試験を作成する際に、検証試験 (加振機の振動疲労試験など) が正しく設定されていることを確認するにはどうすればよいでしょうか。テストが不十分で、将来的に顧客の不満やコストのかかる製品リコールにつながる可能性があるとしたらどうでしょうか。あるいは、過剰な試験を行って材料費が高騰し、試験期間がさらに長くなるとしたらどうでしょうか。
標準に従えばよいというのは正しい考え方です。しかし、それらの標準は実際のニーズを満たしているでしょうか。それらの標準を参考にして、車両の各コンポーネントのテスト仕様書を作成できるでしょうか。
試験を効率的に調整することが、これらすべての疑問に対する答えとなるでしょう。そのため、テスト・プロファイルは次のようにする必要があります。
- 現実的に対応 – 標準ではなく、実際の条件に依存
- 加速試験に対応
- 正しく判断 – 実際の条件と同等の損傷

ウェビナー
実環境を反映した電気自動車のバッテリー振動試験
加振器でテストするエンジン搭載部品の例を考えてみましょう。ここでは、車両の寿命を約10年と仮定します。また、実際の条件に基づいて加速 (10年ではありません) 等価損傷試験プロファイルを作成することとします。
ワークフローは以下に示します。
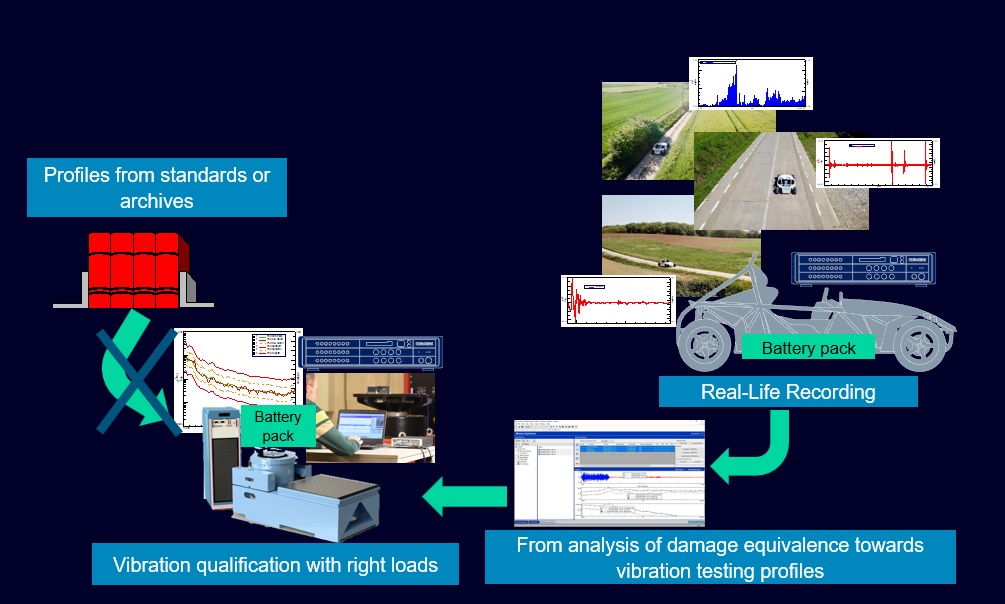
SimRodでテスト済み
以前、ドイツのアーヘン近郊のアルデンホーフェンにある試験場で、電気自動車のデータ収集キャンペーンを実施しました。今回テストした車両は、フル電動スポーツカーのSimRodです(SimRodの詳細はこちら)。SimRodでSimcenterのテスト・ソリューションとシミュレーション・ソリューションを使用して、以前と同様のテスト・キャンペーンを行うことにより、顧客とそのニーズについて詳しく理解することができます。
このテストでは、さまざまなセンサーからデータを取得するための装置をSimRodに装備しました。また、SimRod上のコンポーネントの構造的な動作を評価するためのICP加速度計も使用しました。加振機で試験するこのコンポーネントの加速疲労試験プロファイルも作成しました。この情報を念頭に置き、テスト・プロファイルの作成に焦点を当てたすべての重要なタスクを段階的に示します。
1) ミッション定義とデータ取得
最初の質問は、「顧客が使用すると製品はどうなるのか」ということです。
この問いに答えるにはまず、車両が使用される環境を特定する必要があります。以下の例は、ある市場における総生涯走行時間における分布について、4つの効果的な環境を示しています。

これらの異なる環境で、必要なデータを収集する必要があります (ミッション)。通常、テスト・エンジニアは、テスト・コンポーネントの取り付け位置から振動データを収集し、そのデータを加振器でテストします。収集した振動データからパワースペクトル密度 (PSD) を計算します。
Simcenter SCADASデータ収集ハードウェアは、振動、ひずみ、力、変位、マイク、ビデオ、GPS、温度、圧力、電圧など、幅広いセンサーからアナログ/デジタルデータを収集でき、複数領域をサポートする設計になっています。
2)損傷ポテンシャルの解析
前述のように、取得した振動データをPSD計算した結果が加振テーブルへの入力になります。これは、 「標準ではなく、実際の状況に従う」ということです。しかしこれだけでは、実際のユーザー環境と同じ損傷が反映されたプロファイルを作成して試験時間を短縮するには不十分です。そこで、次のように考えるかもしれません: 「過酷な環境が製品に与える影響を定量化するにはどうすればよいか」
環境の違いによる影響をより深く理解するために、加振に対する応答を計算し、振動疲労についてさらに掘り下げる必要があります。ここで重要になるのが、疲労損傷スペクトル (FDS)、最大応答スペクトル (MRS)、衝撃応答スペクトル (SRS) です。
2-a) 疲労損傷スペクトル (FDS)
FDSは、高サイクル疲労に関連する疲労損傷の可能性を評価するためのツールです。振動信号の共振周波数を1自由度 (SDOF) 系とみなすと仮定し、周波数とQ値 (Q-factor) の減衰を考慮します。これらの各SDOF系から応答 (相対変位) を計算します。次のステップとして、これらの応答をSN曲線上に配置し、各応答の損傷を計算します。Palmgren-Miner損傷累積則により、これらの損傷値を累積することができます。FDS図は、x軸に共振周波数、y軸に疑似損傷を仮定したものです。この図は、さまざまな振動荷重を (損傷別に) 比較する絶好の機会を提供します。
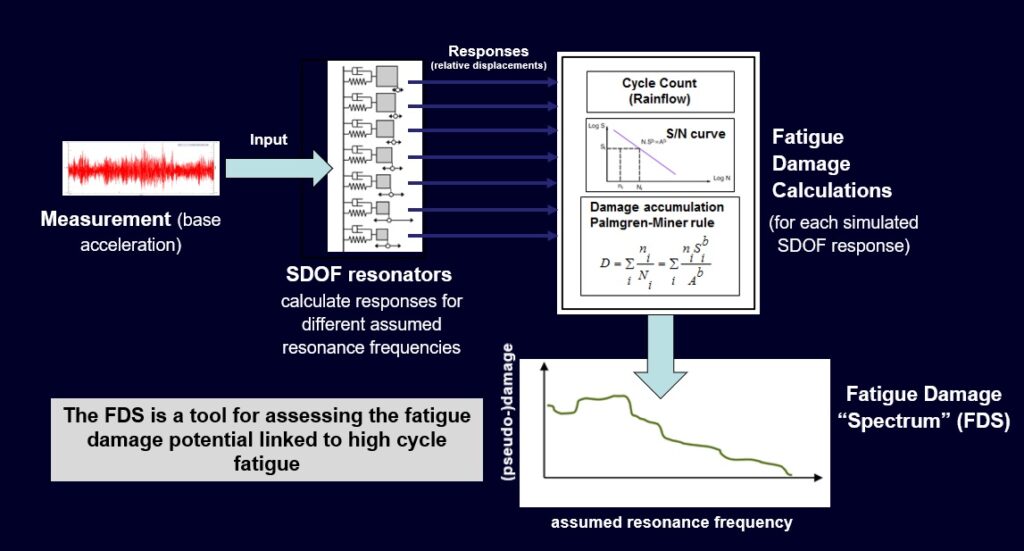
2-b) 最大応答スペクトル(MRS)
FDSと同様、MRSも想定共振周波数をSDOFシステムとみなし、各SDOFシステムからの最大応答を計算します。この方法は、異なる振動信号を比較する場合にも非常に役立ちます。また、試験を加速させる場合の制御方法としても非常に役立ちます。元のデータと加速データを同じMRS図にプロットすることができます。この方法により、元の信号の加速度が特定の周波数でより高いピークを示しているかどうかを確認できます。テストが過剰にならないように十分に留意する必要があります。
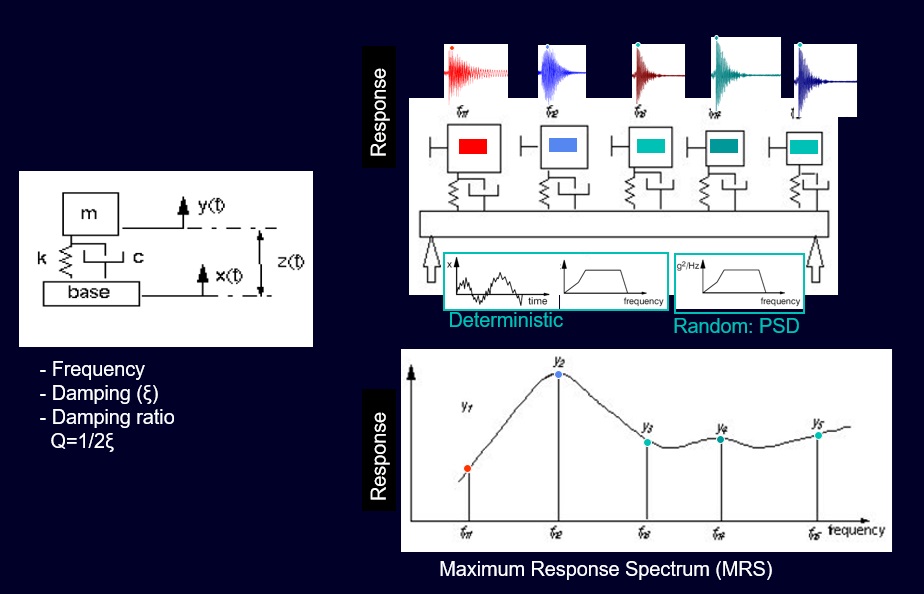
2-c) 衝撃応答スペクトラム (SRS)
SRSには、MRS方式と同様のアプローチがあります。ただし、長期定常状態励起が考慮されるMRSとは異なり、SRSでは極度の衝撃による影響が重視されます (詳細については、SRSのナレッジベース記事を参照)。
2-d) 全体的な損傷の計算
このプロセスでは、さまざまなミッションを考慮して、合計寿命試験を作成します。
例えば、2つの異なる道路状況をカウントする場合、振動荷重のFDSダイアグラムを合計することがあります。ただし、自動車がトラックや船で輸送されることを想定すると、その影響も考慮する必要があります。次に、FDSダイアグラムまたはMRSダイアグラムをエンベロープして、各周波数レベルのワーストケース条件を考慮することができます。
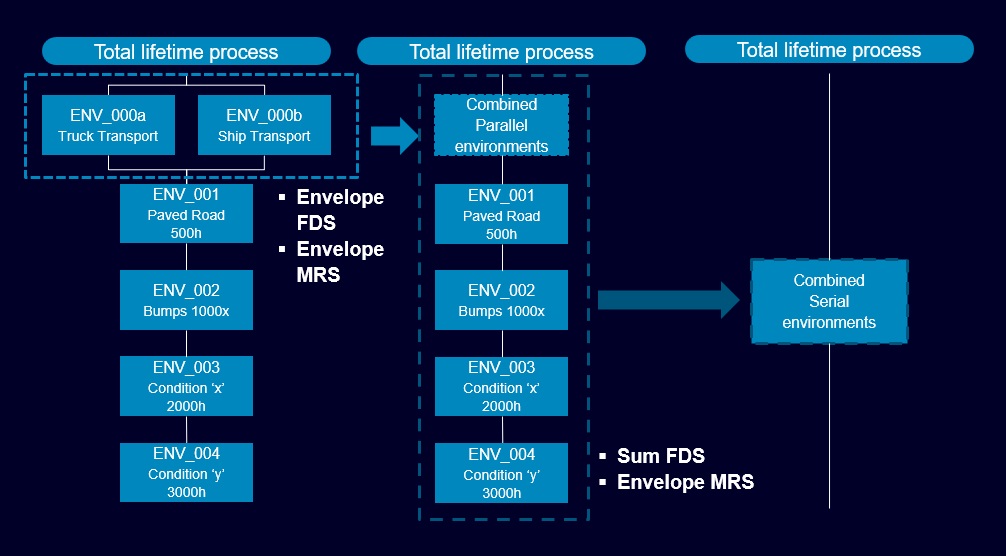
Simcenter TestlabのMission Synthesisアプリケーションを使用して、MRS、FDS、SRSの計算を実行することができます。ミッション合成により、柔軟な方法でSDOFシステムを適切に調整することができます。
3) テスト・プロファイルの合成
最後の質問は、「損傷を維持した状態でテストを加速させるにはどうすればよいか」ということです。
そこで、前回の 応答解析 (FDS、MRS、SRS) に基づいた試験の調整に移ります。Simcenter Testlab Mission Synthesisでは、テスト継続時間をユーザー・パラメーターとして導入し、合成されたプロファイルが自動的に調整されます。テスト期間の計算機能だけでなく、テスト・プロファイルを適切に調整するための「不確定因子とテスト係数」計算機能も用意されています。「不確定因子」では環境と材料の種類が考慮され、「テスト係数」では、限られた数のサンプル試験によって信頼性が向上します。合成されたプロファイルは、PSDまたはサイン・スイープとして識別されます。
振動疲労理論に対する簡単な事例として、以下の2つが考えられます。
- OEMの視点: OEMはFDSを使用して、今後認定する予定の部品サプライヤーを評価できます。
- サプライヤーの視点: 納品先のOEMが変われば、認定仕様も変わるでしょう (PSD、サイン・スイープ、テスト期間なども異なる場合があります)。サプライヤーは、異なる認定を比較することにより、単一の認定試験を作成することができます。
Simcenter Testlab Mission Synthesisをお勧めする理由
- 高品質、高い信頼性、短い試験期間のニーズに対応
- 耐用年数中のさまざまな環境振動 (輸送、路面衝撃、エンジンによる振動など)
- テストが不十分な場合、機械的な故障の可能性が高まり、コストがかさみます。過剰なテストは過剰設計と過剰コストにつながります。

ウェビナー
実環境を反映した電気自動車のバッテリー振動試験
ご質問はありませんか?お気軽にお問い合わせください。どんな質問にも喜んでお答えいたします。メールアドレス: safak.has@siemens.com