4 étapes pour prédire le bruit de la route : un projet en collaboration avec Hyundai Motor Group

Sans le masque du moteur à combustion, le bruit de la route est plus important dans les véhicules électriques et est devenu la principale source de bruit pour les conducteurs et les passagers. Le bruit de la route est présent dans presque toutes les conditions de conduite. Pourtant, il est notoirement difficile de prévoir le bruit de la route et c'est devenu l'un des problèmes critiques auxquels sont confrontés les ingénieurs qui travaillent sur les véhicules électriques.
"Comment évaluer de manière fiable le bruit routier dans un éventail de conditions de conduite et de variantes de véhicules à chaque stade de développement ?"
Cette question a été posée par une équipe de recherche du Hyundai Motor Group (HMG). Respecté pour son travail de pionnier dans le domaine des technologies automobiles, HMG dispose d'une solide expertise en matière de bruit routier, mais souhaitait l'étendre davantage.
Les ingénieurs de HMG avaient déjà commencé à étudier comment combiner les technologies de test et de simulation pour créer un jumeau numérique plus fiable. Ils souhaitaient notamment caractériser un modèle de suspension et se sont donc attachés à créer des modèles de test compatibles avec les modèles de simulation. Cependant, ils ont rencontré des obstacles importants.

Étape 1 : Comprendre les limites de chaque sous-système
Comme le savent les ingénieurs automobiles, il est difficile de mesurer la contribution de chaque composant au bruit de la route. La roue, la suspension ou la carrosserie du véhicule est-elle principalement responsable du bruit ? Le premier défi consistait à comprendre les conditions limites opérationnelles de chaque sous-système en tant qu'élément d'un ensemble plus vaste. Nous avons appliqué le test structurel dans une configuration libre-libre. Il n'est pas facile d'obtenir une représentation correcte car les sous-systèmes s'influencent mutuellement.
Chez Simcenter Engineering and Consulting services, nous nous efforçons d'aider nos clients à atteindre leurs objectifs technologiques et commerciaux en s'attaquant à des problèmes complexes. Notre travail est intéressant parce que nous travaillons avec du matériel, des logiciels et des personnes, en utilisant les compétences et les ressources nécessaires pour remplir un mandat. Logiquement, nous avons souhaité apporter notre aide lorsque Sangyoung Park, ingénieur de recherche principal chez HMG, nous a demandé si nous pouvions collaborer avec son équipe.
Étape 2 : Séparation de la suspension
Nous avons commencé par nous concentrer sur la relation entre le pneu (en tant que source de bruit) et le corps, y compris la suspension en tant que récepteur. Nous avons utilisé l'analyse des trajectoires de transfert basée sur les composants, ou TPA basée sur les composants, pour comprendre la nature de chaque sous-structure et estimer la charge. Nous avons validé cette méthode d'estimation des charges indépendantes sur les pneus lorsque les ingénieurs de HMG ont confirmé que l'utilisation de ces charges et de la représentation des pneus sur une autre voiture permettait de prédire avec précision le bruit de la route.

Lisez ce livre blanc pour en savoir plus sur la méthodologie TPA basée sur les composants.
Pour aller plus loin, nous avons utilisé la sous-structuration basée sur la fréquence (FBS) pour comprendre la contribution de la carrosserie, de la suspension et des roues du véhicule. Comme la suspension est une chaîne de différents composants soumis à une précharge spécifique, elle ne peut pas être mesurée facilement en condition libre. Au lieu de cela, nous avons utilisé la nouvelle technique de découplage FBS pour caractériser le comportement vibratoire d'un composant en supprimant l'influence d'une structure de support ou d'un banc de test.

En juin dernier, lors du congrès de l'ISNVH à Graz, nous avons présenté, en collaboration avec HMG, un article sur la première identification d'un ensemble de suspension basée sur des essais, incluant la précharge et les non-linéarités opérationnelles. Suivez ce lien pour lire l'article technique : Découplage FBS au niveau de la suspension pour les applications de bruit routier.
Étape 3 : Conception, construction et validation du banc de test
Pour appliquer la technique de découplage FBS, nous avons travaillé sur la conception, la construction et la validation d'un banc de test personnalisé pour évaluer le modèle de suspension. Ce banc devait être conçu de manière à pouvoir être utilisé ultérieurement en interne par les ingénieurs de HMG, ce qui permettait de monter différentes suspensions aux points d'interface.
Nos deux équipes ont travaillé en étroite collaboration. L'équipe des services d'ingénierie de Louvain, en Belgique, a créé des fichiers CAO pour proposer des emplacements de capteurs et d'excitation qu'elle a envoyés à HMG en Corée du Sud. Là, les ingénieurs en test ont utilisé ces modèles CAO pour fabriquer des instruments, mesurer les fonctions de transfert requises et fournir un retour d'information à la Belgique pour une validation plus poussée.
Après avoir identifié la configuration de testi idéale, positionné les capteurs et assuré l'accessibilité, nous avons utilisé le gabarit pour tester un modèle représentatif de suspension avant intégrée avec les conditions limites appropriées et sous la précharge adéquate.

Nous avons mesuré le comportement de l'ensemble. Ensuite, la suspension a été physiquement retirée du total et le banc a été mesuré à nouveau. Grâce à un processus d'itération intense, nous avons progressivement validé les résultats. Nous avons construit un modèle virtuel de la suspension, basé sur les données de test réelles générées en soustrayant les mesures prises au banc de l'ensemble de l'assemblage.
Étape 4 : Prévision des performances des systèmes NVH
L'étape suivante du processus consistait à combiner tous les composants et à appliquer les charges des pneus à l'ensemble du véhicule ou au jumeau numérique afin d'écouter et de valider le bruit de la route.
Lorsque vous disposez d'un modèle virtuel dérivé de mesures réelles, vous savez qu'il est fiable et vous pouvez l'écouter. Si vous n'aimez pas ce que vous entendez, vous pouvez le modifier et réécouter. Vous pouvez fixer des objectifs et faire des choix sur le son optimal en fonction de la contribution de chaque composant. Pour les ingénieurs concepteurs, cela signifie beaucoup plus de flexibilité.

Le banc de test été livré à HMG pour être utilisé sur place, ce qui a permis d'analyser en détail la suspension étudiée, de mesurer d'autres suspensions, de changer des composants ou des supports de suspension, d'apporter des modifications, etc. et d'étudier leur effet sur le bruit de la route. Cela marque un pas en avant dans la capacité de l'entreprise à prévoir virtuellement les performances NVH des véhicules et à passer au développement de véhicules virtuels sur la base de modèles.
Consultez ce blog sur la prévision des NVH des véhicules pour plus d'informations sur la façon de maîtriser les performances NVH avec un prototype virtuel.
Le travail d'équipe donne corps au rêve
Ce projet en plusieurs phases avait des normes et des attentes élevées. D'une part, nous nous sommes efforcés d'innover dans ce projet, et d'autre part, les ingénieurs de Siemens et de HMG ont fait preuve d'un degré de coopération exceptionnel. Nous pensons qu'il s'agit de la première application commerciale de l'approche de découplage FBS, et nous sommes tous fiers du gabarit de test sophistiqué que nous avons produit.
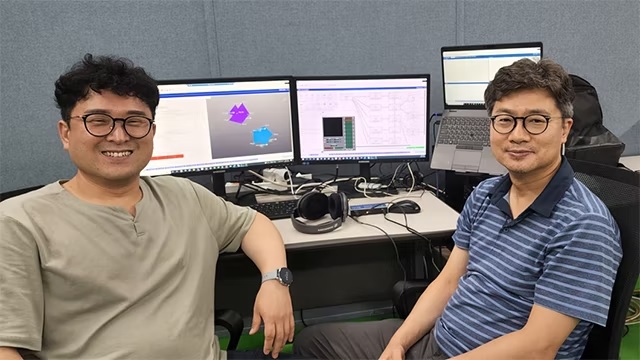
Les deux équipes continuent de collaborer. Notre attention se porte maintenant sur la création d'une base de données de résultats de tests sur différents pneus et suspensions afin que les ingénieurs concepteurs de HMG puissent entrer des objectifs et des paramètres, sélectionner des options et les modifier facilement jusqu'à ce qu'ils trouvent la combinaison optimale pour le bruit de la route.
Découvrez dans cette infographie les défis posés par le bruit routier des VE et comment utiliser les solutions de simulation et de test Simcenter.
Partager les connaissances en matière de prévision du bruit routier

Le 30 novembre, Sangyoung Park sera l'invité du webinaire en direct Prévision du bruit routier - une approche MBSE pour le développement virtuel des NVH.
Il discutera des méthodes, des résultats et des réalisations du projet de modèle de véhicule NVH, de la coopération avec Siemens et de la feuille de route du HMG pour l'amélioration du bruit routier des véhicules électriques.
Le webinaire abordera les défis liés à la construction de bons exemples de véhicules, décrira la représentation des composants basée sur les tests de l'IAO et démontrera comment définir les charges invariantes. Il expliquera comment traiter et modéliser les sources fortement liées au véhicule, par exemple les pneus. Il examinera également les outils qui permettent de remplacer facilement un composant ou un sous-système par une version alternative.
Liens intéressants
- Utiliser l'ingénierie des systèmes basée sur des modèles pour adopter une nouvelle approche du développement virtuel des NVH
- Livre blanc : Ingénierie du bruit routier - Atténuer les sources de bruit les plus dominantes dans les véhicules électriques dès le début du processus de développement
- Étude de cas Renault - Multiplier par cinq les applications de prévision du NVH tout en éliminant les prototypes physiques