Today’s manufacturing companies must be smart. And adaptive.
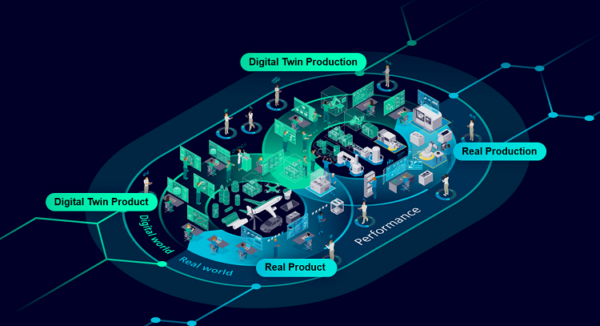
With CES 2025 kicking off the new year, we begin a new series exploring smart manufacturing and how companies must become more adaptive in their digital transformation.
In our time of complex business challenges, manufacturing companies face a volatile mix of market, product and production complexities that too often seems like a perfect storm of market dynamics.
Supply chain disruptions, surging product complexity, increasing demand for mass customization, smaller batch sizes and complex production runs, new compliance pressures, talent shortages, exploding costs and relentless competition must all be addressed. At the same time, these challenges should be balanced against the unprecedented opportunities for growth and innovation driven by soaring customer demand for multi-dimensional software-enabled products.
In this environment, it is no wonder that the manufacturing challenges often exceed the capabilities and the pace of traditional production methods.
So, how do manufacturers balance staffing and resource issues and still deliver products on time with high quality and compliance standards, without raising prices to unacceptable levels?
The answer can be found in the journey to make your factory smart.
Smart manufacturing transforms the traditional manufacturing environment to provide the smart capabilities companies need to stay competitive by integrating digital tools for enhanced production efficiency and flexibility.
Smart manufacturing provides the digitalization needed to combine the real and virtual worlds using digital twins, so that companies can simulate products and production, also using real-time production data to optimize outcomes and predict performance in a closed loop. In addition, they can link physical production and operational processes with digital technologies for a new level of responsive performance on the shop floor.
The marriage of these components provides real-time insights across processes, products, and people for continuous optimization in a make-it-right-the-first-time, high yield smart manufacturing process.
With smart manufacturing, you are equipped with the data and analytics needed to make data-driven decisions for faster time to market. In addition, you gain more effective use of your resources with more predictable inventory needs, while ensuring on-time delivery from capacity improvements and higher initial quality and compliance.
Smart manufacturing delivers what companies need to compete in today’s rapidly-evolving, global market. And to keep up with changing market dynamics, manage complexities and future-proof their business, manufacturing companies must also become adaptive.
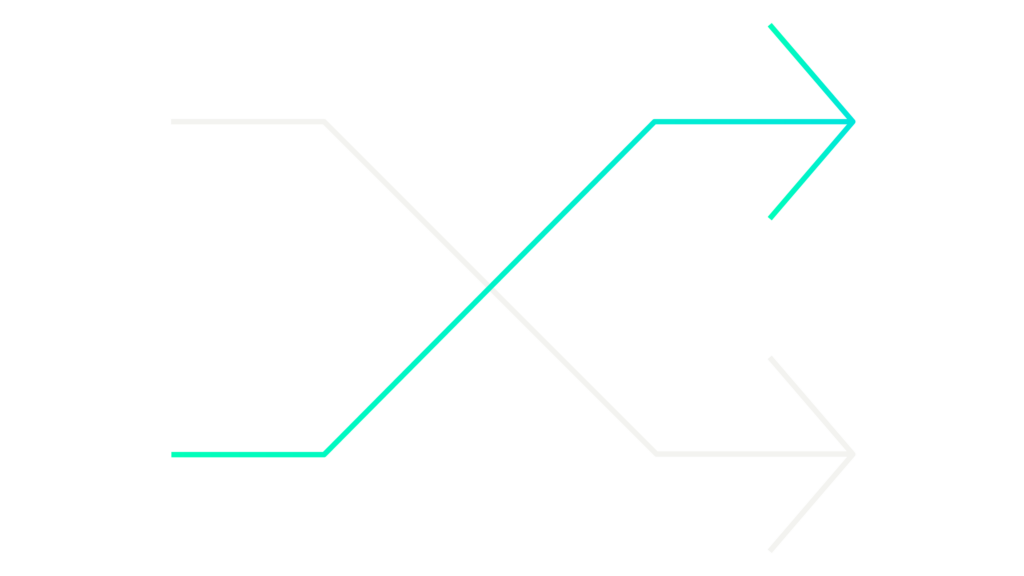
With adaptive manufacturing you can quickly adapt to shifting market dynamics.
You can speed up your transformation from well-automated to adaptive manufacturing as needed. Adaptive manufacturing extends the value of smart by enabling greater flexibility and modularity, allowing production systems to rapidly adjust to changing markets, customize outputs, and reconfigure processes with minimal disruption.
With adaptive manufacturing, you can accelerate IT and OT convergence to unlock valuable data across product and production, make smarter decisions and quickly adapt to changing customer demands and market dynamics. You can integrate IT and software capabilities and proven methods from software development (edge and cloud computing, low code, agile and more) into automation, with machine learning, artificial intelligence and data analytics built in to increase adaptability, always taking into account OT requirements.
Siemens is working in partnership with our customers to unleash the technologies that enable an adaptive future. Together, leveraging our Siemens Xcelerator digital business platform, we are fundamentally transforming how industry operates.
Want to discover how to become adaptive in your smart manufacturing journey?
Explore our adaptive manufacturing solutions at adaptive-manufacturing/use-case-solutions/