From Lean to Smart Semiconductor Manufacturing Execution (Part 2 of 3)
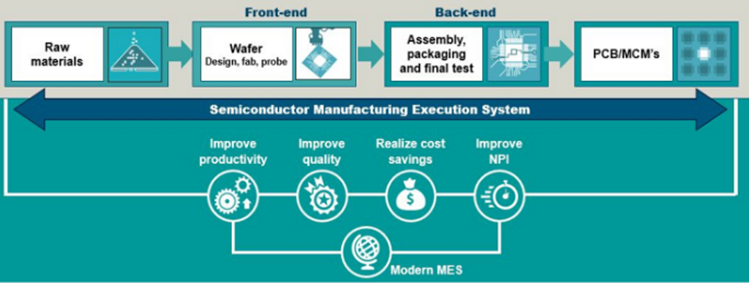
Traditional lean manufacturing brings benefits, but smart manufacturing can propel progress further to amplify profit margins and foster adaptability. In our first post, we talked about shifting left for smart manufacturing. This next post in the series brings us to the execution phase. Executing is where we realize the gains we envisioned in the planning and scheduling phase. So, let’s take a closer look at the key executional components.
Smarter automation in semiconductor manufacturing
The key to realizing this gain is automation. There can be as many as 1,400 process steps in a semiconductor fab.1 Automation, a key cornerstone of Industry 4.0, helps drive maximum utilization, efficiency and flexibility.2 Implementing automation in a fab can sometimes feel like a bottomless drain on resources and time. Like any digital project, it is important to ensure you have a clear vision for implementation – what do you want to achieve out-of-the-box (OOTB) and what does your roadmap look like? Again, managing change is important – semiconductor fab production sites are often modified and the equipment in those sites are constantly being added or deleted. It is imperative to have the right automated system that can provide this level of fab and equipment flexibility.
Gaining increased quality and reliability
Diverse applications in industries like automotive, medical and aerospace and defense have driven an increased focus on quality and reliability. Because the safety of humans can potentially ride on the performance of a single chip, it is important that we know everything we can about that chip, from where it was made and what part of the wafer it originated from, to intermediate test results as it proceeded through the fab. The International Organization for Standardization (ISO) standards like 26262 – which governs functional safety – require traceability from requirements definition through verification and validation all the way to final test and qualification.3
Silicon photonics is a rapidly growing area with applications in high-performance computing, sensors and data centers. It leverages a lot of semiconductor manufacturing techniques and can benefit from the flexibility, automation, quality and reliability of semiconductor digital solutions.
Better back-end semiconductor manufacturing integration
It doesn’t just stop with the fab. The lines are blurring between fab processing and backend packaging. Fabs are doing process steps like through silicon vias (TSV) and wafer level fanout. Semiconductor assembly and test services (SATs) are investing in some simple versions of wafer processing steps like etch and deposition and doing hybrid bonding – a face-to-face connection of wafers.
Leveraging advanced analytics in smart manufacturing
Digital transformation has inspired a new phrase: Data is the new oil. But data is only valuable if you know how to extract knowledge and insights that help drive actions. Semiconductor fabs, particularly connected through industrial internet of things (IIoT) techniques, can generate massive amounts of data. The key is to figure out how to collect, store, process and ultimately analyze data to extract the descriptive – what happened, the prediction – what will happen and the prescription – what should I do?
Orchestrating components for improved semiconductor manufacturing execution
How do you orchestrate these components to improve semiconductor manufacturing execution?
Having access to the right integrated PLM (product lifecycle management) platform is a big key. And that happens to be the subject of our next week’s post. Please stay tuned for more insights to come.
Download our informative ebook “Smart Manufacturing for Semiconductors” to learn more about how a fully connected smart factory, utilizing data-driven insights from operational performance can deliver significant opportunities for continuous improvement.
Sources
1. “Chipmakers Are Ramping Up Production to Address Semiconductor Shortage. Here’s Why that Takes Time,” © Semiconductor Industry Association, February 2021.
2. Johnson, Clint; “A guide to modern factory automation and Industry 4.0 in manufacturing,” August 2020.
3. Murphy, Bernard; “Traceability and ISO 26262,” November 2021.
Blog written by Melville Bryant, Siemens Digital Industries Software