Smart is Sustainable.
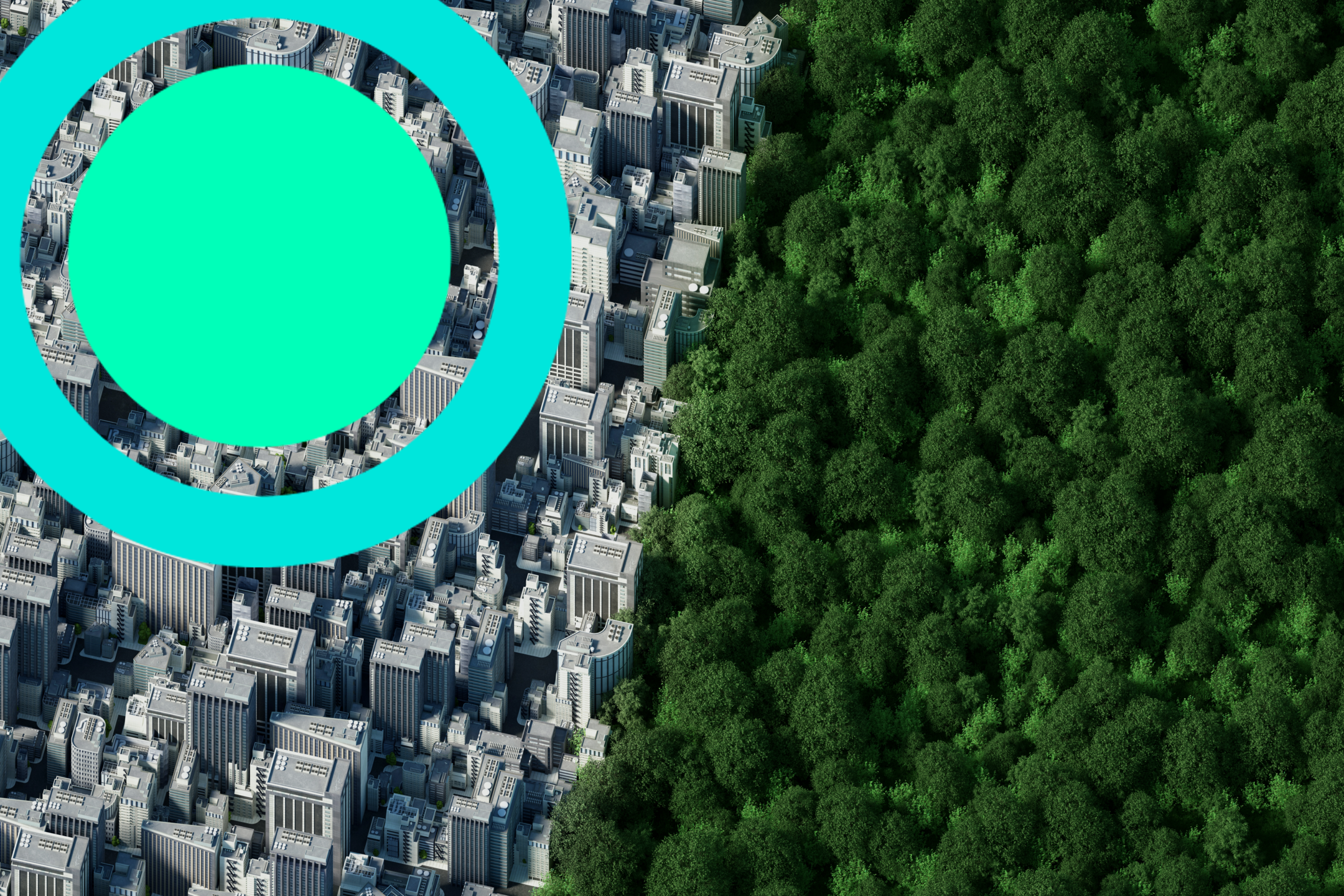
Alan Porter, Global VP, Electronics Industry, Siemens Digital Industries Software –
Post 1 in our Blog Series, “Sustainability in Electronics. Every Detail Matters.”
Electronics processes are complex, and every detail matters from design to production in achieving sustainability. A world in critical need of a sustainable future needs smart manufacturing solutions because the demand for smart technologies – phones, computers, medical devices, data centers, defense and transportation – continues to grow, and so does our responsibility to ensure their design and production is environmentally responsible.
The revenue generated in the Consumer Electronics market worldwide is projected to grow to a staggering $1.096 trillion USD by 20291. Unfortunately, by 2030, global electronic waste will reach more than 74 million metric tons, with only 17.4% currently collected or recycled properly2, which presents a looming environmental challenge.
Electronics manufacturing plants, which typically operate almost continuously, contribute significantly to this challenge through high energy consumption, chemical use, water consumption, and emissions of greenhouse gases and hazardous pollutants.
…but what if electronics companies could advance sustainable design and production processes to scale up with smart, secure operations throughout the product lifecycle – while minimizing their carbon footprint? Getting there is a process, but it is one that our industry must make a priority.
Sustainability is a journey
In every journey, the most important step is the first one. Designing for sustainability begins with the commitment to reduce the carbon footprint. Lowering energy consumption, eliminating waste generation, and reducing chemical usage are good places to start. Then comes next steps such as selecting environmentally friendly materials, less regulated substances, and sourcing alternatives to PFAS (per-and polyfluoroalkyl substances) to decrease the environmental impact. Next comes steps such as incorporating Digital Twins to plan and optimize processes and plants and leveraging the Siemens FMCS (Facility Monitoring and Control System) to optimize resource and plant efficiency. And there are many other vital steps ahead.
What makes the journey even more challenging is pursuing sustainability while meeting unprecedented demand for electronics in everything. That’s where legacy methods fall short and where smart manufacturing begins.
Why? Traditional methods fall short in addressing these complex productivity and sustainability challenges. We need a new approach. This is where smart manufacturing comes in. Smart manufacturing integrates technology to streamline operations, reduce waste, and enhance resource management, making it a crucial component in advancing sustainability in the electronics industry. Electronics equipment engineers and machine builders also play a crucial role by collaborating to create a cohesive system that minimizes environmental impact while maximizing productivity.
The path to sustainability is smart manufacturing enabled, where the secure and sustainable design-to-production process becomes a Digital Enterprise (DE). DE serves as a comprehensive roadmap, a digital transformation pathway that guides electronics manufacturers on their journey toward digital maturity and operational excellence.
As a digital enterprise, smart manufacturing capabilities, techniques and programs enable electronics manufacturers to achieve transformation by developing and executing one sustainable business strategy, from design to production to finished product.
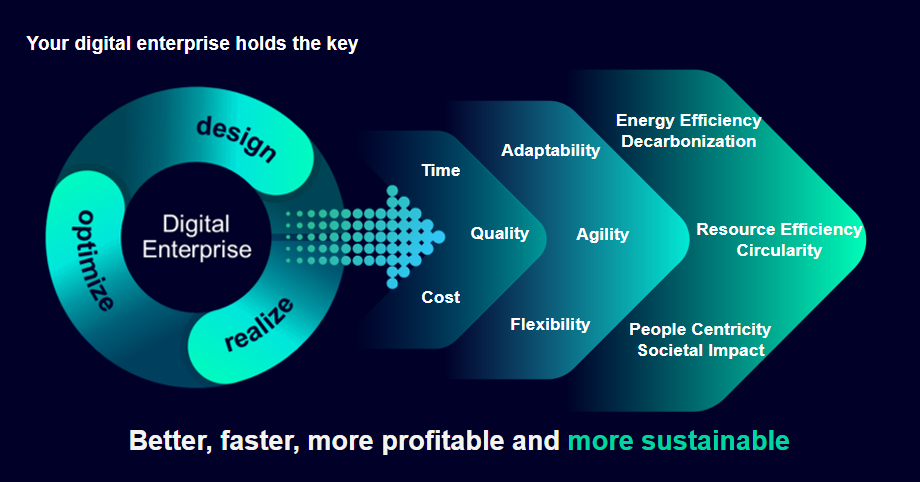
Embracing artificial intelligence (AI) and the advanced analytics of smart manufacturing provides electronics companies with real-time visibility into their production processes. Improved visibility enables optimized resource allocation and proactive identification of potential bottlenecks without disrupting operations. Pursuing a digital approach fosters agile, seamless operations, minimizes waste, and aligns progress with environmental responsibility.
Smart manufacturing for electronics
Smart manufacturing makes the difference. With smart manufacturing, electronics companies and machine builders can design and build future-proof manufacturing ecosystems by implementing a wide range of digitally integrated automation solutions. Smart manufacturing solutions include reducing energy consumption, enhancing efficiency and productivity, and providing attractive people-centric workspaces in plant operations to appeal to the next generation of workforce talent.
Digitalization can be achieved through lifecycle management capabilities that connect every aspect of electronics manufacturing processes for a flexible plant where all product information and design data are tied to critical processes and tasks all the way from requirements to delivery. Which includes customer requirements, original technical specifications, design definitions, production schedules, analysis results, sourcing plans, sustainability KPIs and quality inspections. For complete traceability, compliance, and verification.
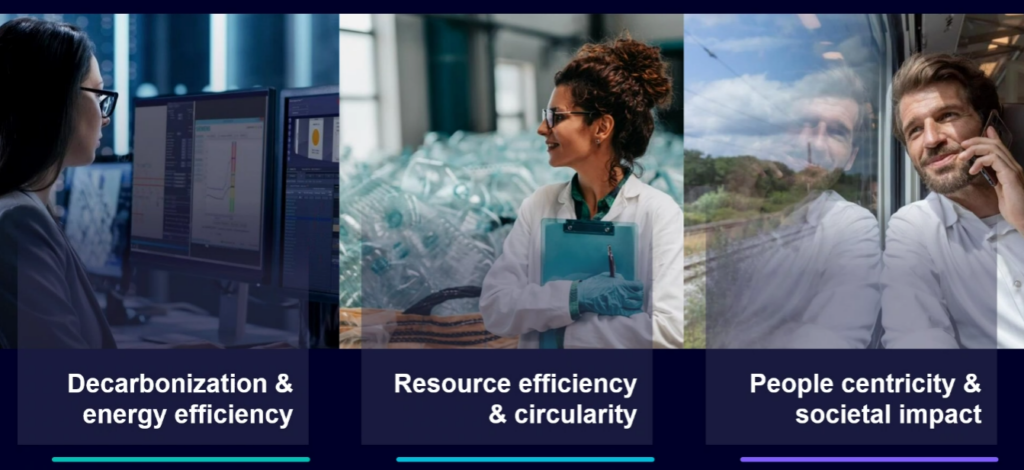
Simulation without interruption
Through collective intelligence, manufacturers can incorporate Digital Twins for highly accurate virtual models of the Product or Production. Our Digital Twins enable a higher level of simulation, learning and advanced planning of fabs and machines, enabling an optimal system and energy setup. Yet it is important to remember that optimization should never interrupt production. Why?
Electronics companies face intense pressure to design and produce their next-generation products while maintaining uninterrupted operations, which creates a ‘high-stakes environment’ where any disruption can have significant consequences.

Fortunately, Digital Twin models can operate without disrupting any current operations, accurately simulating real-world conditions. They are continuously updated by real-time product and production data, creating a virtual model that is unparalleled for process optimization prior to building an electronics product, designing actual manufacturing operations, or planning equipment optimization.
A deeper understanding
Simulation with Digital Twins can enable multiple what-if scenarios that can be evaluated virtually at reduced cost to optimize products and processes. This comprehensive, real-time simulation of scenarios, processes, and systems fosters a deeper understanding of plant dynamics that facilitates proactive problem-solving, predictive maintenance, and continuous improvement initiatives.
Even more effective cross-domain Digital Twins can inform each other, providing insights and enabling continuous improvement. Leveraging Siemens’ innovative solutions creates a synergy between Digital Twins and IoT with cutting-edge software and automation tools. This seamless integration leads to next-generation efficiency in manufacturing operations and machine building, bringing comprehensive sustainability goals within reach. As a digital enterprise, smart manufacturing capabilities equip electronics manufacturers and machine builders to develop and execute a sustainable business strategy, from design to production to finished product and beyond.
Very smart. But just as important, sustainable.
To discover more about how Digital Twins can enhance design for sustainability, see this compelling blog by Eryn Devola, Vice President of Sustainability, Siemens Digital Industries Software: blog.siemens.com/2023/11/sustainability-starts-with-design/
For more about rethinking design for sustainability, visit www.sw.siemens.com/en-US/solutions/compliance-management/
Then look for our next post in the Series, Scale up smart to reduce carbon, coming soon…
References:
1. https://www.statista.com/outlook/cmo/consumer-electronics/worldwide
2. (The Global E-waste Monitor 2020, Forti et al 2020, Pages 24, 58: https://www.greene.gov.in/wp-content/uploads/2020/12/2020120929.pdf )