Design for manufacturing output files – optimizing engineering to manufacturing efficiency
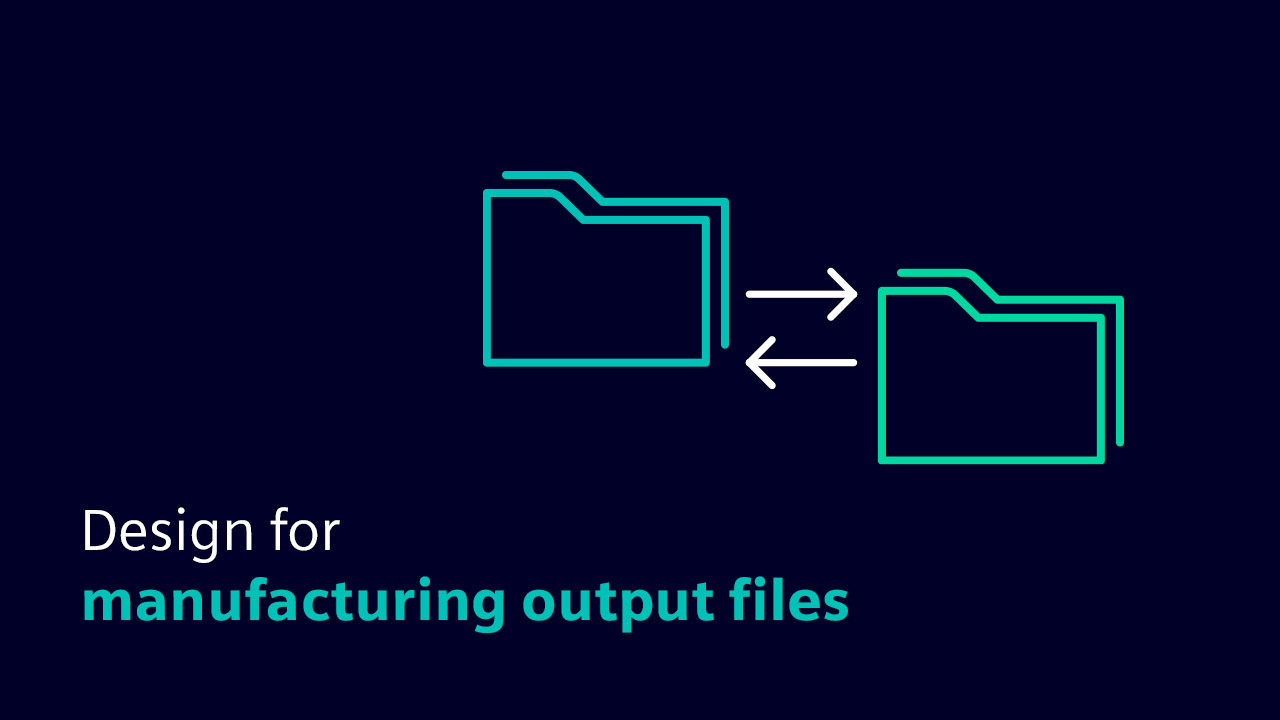
Design for Manufacturing (DFM) is a critical approach in product development that ensures a design is optimized for efficient, cost-effective, and scalable manufacturing. Acknowledging manufacturing as one of the key stakeholders in the project and by including them from the very beginning is today’s industry best practice for electronic systems design. Considering manufacturing constraints early in the design process, engineers and designers can optimize the design cycle process, streamline production, reduce waste, and enhance product reliability.
As PCB design and manufacturing become increasingly complex, the choice of design for manufacturing output files plays a crucial role in streamlining processes, reducing errors, and improving time to market. There are four fundamental high-level manufacturing data package issues typically seen in the industry today. These issues include design errors, conflicting design documentation, design for manufacturing output file data format (Gerbers along with associated required files, ODB++, and IPC-2581), understanding fabricator capabilities (designing to supplier expertise/strengths). This blog explores the significance of design for manufacturing output files and best practices for achieving seamless manufacturing integration.
Understanding design for manufacturing output files
Design for manufacturing output files refer to outputs such as non-intelligent and intelligent file format types (i.e. Gerber files, ODB++ files, and IPC-2581 files, respectively), documentation, specifications, and design elements that translate an idea into a manufacturable product. These outputs ensure that the design can be efficiently manufactured without unnecessary costs, delays, or quality issues. The key here is conveying the engineering intent to manufacturing with the most correct, accurate and complete data package while communicating instructions/requirements by utilizing industry specification in the simplest documented manner possible.
Industry specifications such as IPC standards for electronics is the universal language between engineering and manufacturing. As a reminder, IPC is the global association that helps OEMs, EMS, PCB manufacturers, cable and wire harness manufacturers and electronics industry suppliers build electronics better. IPC standards are used to ensure quality, consistency, and innovation.
What design for manufacturing output files typically include
Data packages in industry standard file format
There arenon-intelligent data packages such as Gerber data along with associated files. Gerber data versions X2 and X3 are both considered “Extended Gerber” formats, falling under the RS-274-X standard, meaning they are more advanced versions of the older RS-274-D format, with X being the more widely used current standard and X3 offering additional information like component placement data and BOM details; essentially, X2 and X3 add extra metadata to the basic RS-274-X Gerber data format. Keep in mind, 274X was never a sanctioned standard. 274D was sanctioned by Electronic Industries Association (EIA). 274X was not.
Then there’s intelligent data such as ODB++ and IPC-2581 file formats. The ODB++ file format is in an ASCII format and is a single compressed file containing sub-directories. IPC-2581 is one XML file with no subdirectories.
With today’s increased electronic systems design complexity, having a more intelligent file format is key, especially when managing and controlling our intellectual property (IP). It’s important to note that Gerber files, ODB++ file, and IPC-2581 file formats have their own set of pros and cons, respectively, yet the Gerber file format is still the most widely accepted data format in the industry today. However, recent studies show that 48.7 percent of electronics companies now use ODB++.
Detailed engineering drawings (fabrication and assembly)
Clear, precise drawings whether it be for fabrication and or assembly, details that include specific IPC standards that are appropriate for which the drawing pertains to, whether it be for fabrication or assembly.
Bill of Materials (BOM)
An up-to-date comprehensive list of all components and materials required for production. This includes Design for Supply Chain Resilience and needs to be mentioned here. This is where supply chain intelligence is left shifted from external to the overall design process and incorporated at the point of design so that engineering can make intelligent part selection decisions. This helps to reduce and or eliminate the potential of unexpected design changes and or board respins due to supply chain related issues.
3D CAD models and prototypes
A digital twin and physical representations of the product for testing and validation. Today’s industry best practice for electronic systems design is Model-based systems engineering (MBSE). This is a methodology that uses models to design and develop complex systems. It’s a type of digital engineering that helps manage complexity and improve communication.
Manufacturing process instructions
Step-by-step guidelines for fabrication, assembly, machining, or molding. Continued optimization is key here.
Quality control guidelines
Specifications and criteria for testing, inspection, defect tolerance, and acceptability. It’s important to note that Design for Test (DFT) should be accounted for from the very beginning of the project and implemented as early as possible. It significantly costs more to incorporate DFT at the end of the design process and almost always results in lower test coverage.
Benefits of optimized design for manufacturing output files
Investing time in incorporating manufacturing inputs and establishing a feedback loop along with refining and optimizing design for manufacturing output files brings multiple advantages:
- Lower production costs – Reducing manual tasks, material waste, labor costs, and manufacturing errors.
- Faster time to market – Optimizing and streamlining processes ensures quicker prototyping and mass production. Eliminate the potential of project delays from unexpected manufacturing Technical Queries (TQs).
- Improved product quality – Minimizing defects and variations by implementing DFM analysis, standardized guidelines, and manufacturing feedback loops.
- Enhanced scalability – Designs that are easy to manufacture support higher production volumes.
- Sustainable manufacturing – Efficient use of resources leads to reduced environmental impact.
Bridging the gap between engineering and manufacturing
Design for manufacturing output files play a crucial role in bridging the gap between engineering and manufacturing. Knowing, selecting, and agreeing on a specific manufacturing output file format (Gerber, ODB++, or IPC-2581) that will work best for you and your supplier is key for optimizing PCB manufacturing. Don’t just ask the supplier’s salesperson which formats they accept, ask the engineering manager of your supplier which format they prefer. By focusing on manufacturing as a key project stakeholder, material and component selection, tolerances (IPC Class), simplicity, manufacturing compatibility, and assembly efficiency, companies can optimize the integrations and collaborations between engineering and manufacturing and create high-quality products at lower costs.
Integrating DFM principles early in the design phase ensures a smooth transition from concept to reality, ultimately leading to successful and scalable manufacturing. For companies looking to improve their design to manufacturing integration, collaboration, and processes, embracing DFM principles can be a game-changer. To learn more about Manufacturing Driven Design download this eBook by Max Clark: