Forging a new path: game-changing electro-thermal design advancement
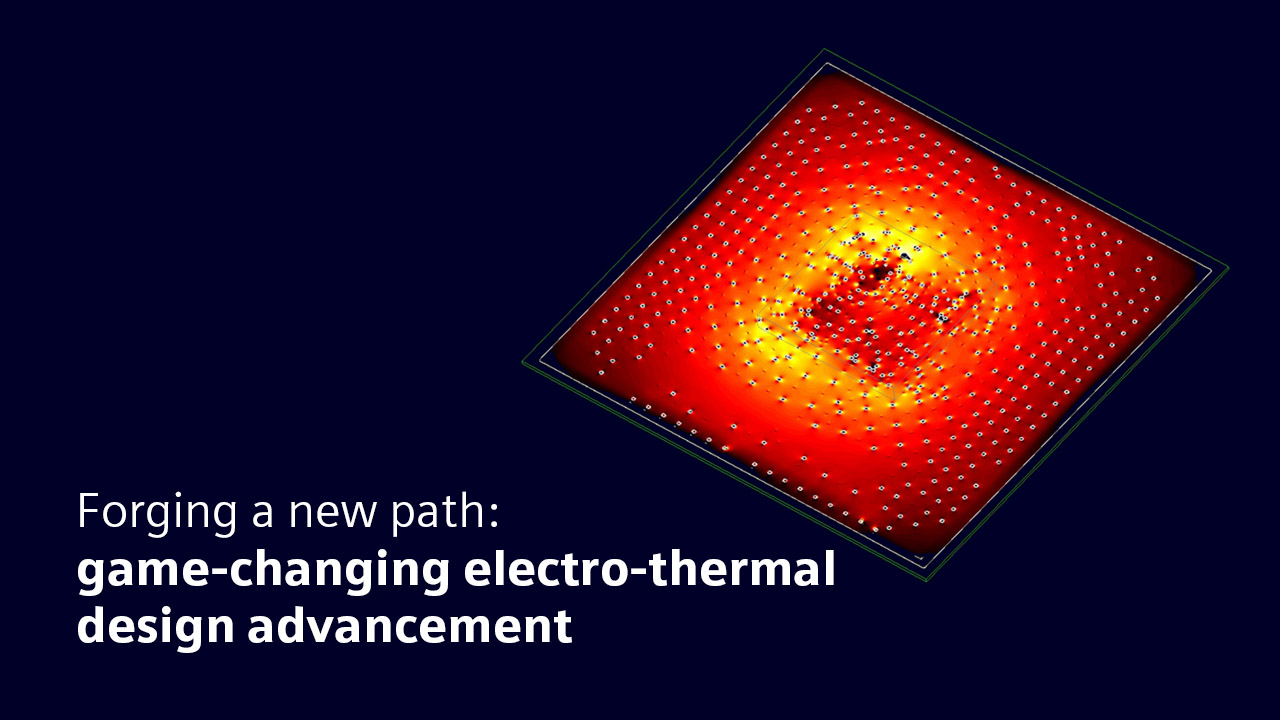
Let’s talk about revolutionizing electro-thermal design. But first, some context. To meet the functional requirements of a circuit under design, electronics engineers meticulously select components, evaluating them based on their electrical attributes, performance benchmarks, and rated capacities. The selected components must all work harmoniously together to provide the desired circuit characteristics. To support the OEM design community, electronic component manufacturers have furnished models in the widely used SPICE format. In hand, these models empower customers to simulate their application circuits, thereby enhancing their comprehension of the intricacies encompassing the capabilities, the potential, and complex interplays of these parts within the broader system framework.
Emerging challenges
The above dependency between component manufacturer (the SPICE model provider) and OEM (the SPICE model consumer) has worked for many decades, however, that relationship is showing significant signs of strain.
- An increasing number of traditionally “analog” components are becoming more “digital” – adding programmability, state machines, and other advanced features that are beyond the capabilities of existing SPICE-based analog design tools.
- Component manufacturers and their OEM customers increasingly battle thermal design issues in many applications during design-in, e.g., power electronics, automotive electronics, renewable energy systems, consumer electronics, to name a few. The interactions between electrical and thermal effects can lead to unexpected behaviors and failures if not properly managed. As a result, effective electro-thermal analysis, modeling, and design are becoming essential to ensure the reliable performance of systems in various industries. Unfortunately, thermal SPICE has not proven to be the answer given its many limitations.
BCI-ROM: a game-changing technology
Fortunately, there is now a game-changing technology that is revolutionizing the electro-thermal design process. It’s called Boundary Condition Independent Reduced Order Model (BCI-ROM) and it captures accurate characteristics from a 3D thermal analysis, ready for use in a 1D circuit simulation. The BCI-ROM-based thermal design/analysis approach is applicable to both components and entire PCB/enclosure and systems. BCI-ROMs can simply be connected in a thermal circuit, i.e., functional schematic, with the heat-flow conservation principle governing the interaction, in the identical way Kirchhoff’s Current Law (KCL) underpins electronic circuit simulation.
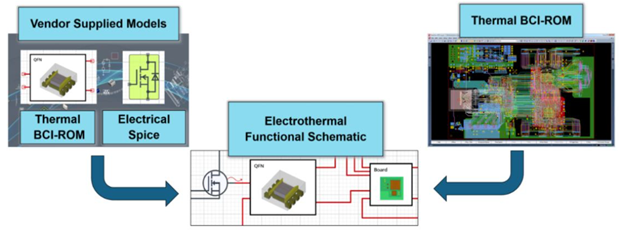
This technology offers a lifeline to electronics designers grappling with formidable thermal obstacles driven by the unrelenting pursuit of smaller, lighter, more cost-effective, faster, and feature-rich designs. These pursuits collectively exacerbate the challenge of dissipating heat efficiently. With BCI-ROM emerging as a pivotal technology for higher accuracy thermal models, a parallel supply chain is developing, especially in VHDL-AMS format. This compliments the functional electronic models such as SPICE, VHDL-AMS, and IBIS.
Tackling electro-thermal design challenges
BCI-ROM revolutionizes collaboration between Component Manufacturers and OEM Electronics and Thermal Engineers, empowering them to jointly tackle intricate electro-thermal design challenges with heightened efficiency. The resultant BCI-ROM models adhere to the IEEE Standard VHDL-AMS format, harnessing the language’s capacity to articulate the interconnected differential equations, expressed in matrix form, essential for capturing dynamic thermal characteristics.
A thermal BCI-ROM implemented in VHDL-AMS seamlessly interfaces with electrical circuit components. To illustrate, the thermal circuit depicted below establishes a bidirectional communication channel for temperature exchange with the electrical circuit element, while the electrical circuit reciprocates by supplying power. It’s important to note that this isn’t a traditional ‘back and forth’ co-simulation methodology. Instead, thermal and electrical circuits are addressed in parallel, solving for the electrical and the thermal concurrently, an advantage made available given both models are described in the same VHDL-AMS language.
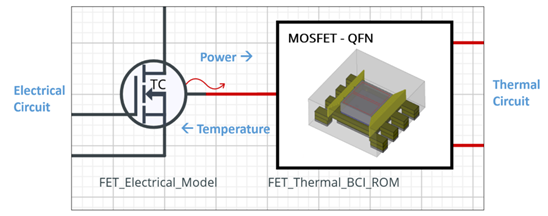
Additional resources
To learn more about BCI-ROM technology and the tools to create these accurate thermal models, go to the Simcenter Flotherm landing page and check out this white paper, “Electro-thermal design breakthrough: Enabled by new BCI-ROM thermal modeling technology”.
To witness the power of electro-thermal simulation using BCI-ROM technology, check out these two blog articles from Mike Donnelly that include interactive, functional simulation examples. The first example is based on a smartphone. The second, a switch-mode power electronics example.
- Introducing BCI-ROM For Electro-Thermal Design
- Electro-Thermal Design: Using BCI-ROMs For Switch-Mode Power Electronics
All electro-thermal simulations were conducted using Siemens’ cloud-based PartQuest Explore, a complete design, modeling, simulation, and analysis environment for electronic and mechatronic circuits and systems. Full coverage for analog, digital, mixed-signal and multi-domain systems including electro-mechanical and electro-thermal. SPICE and VHDL-AMS models supported.