Overcoming the challenges of a volatile supply chain
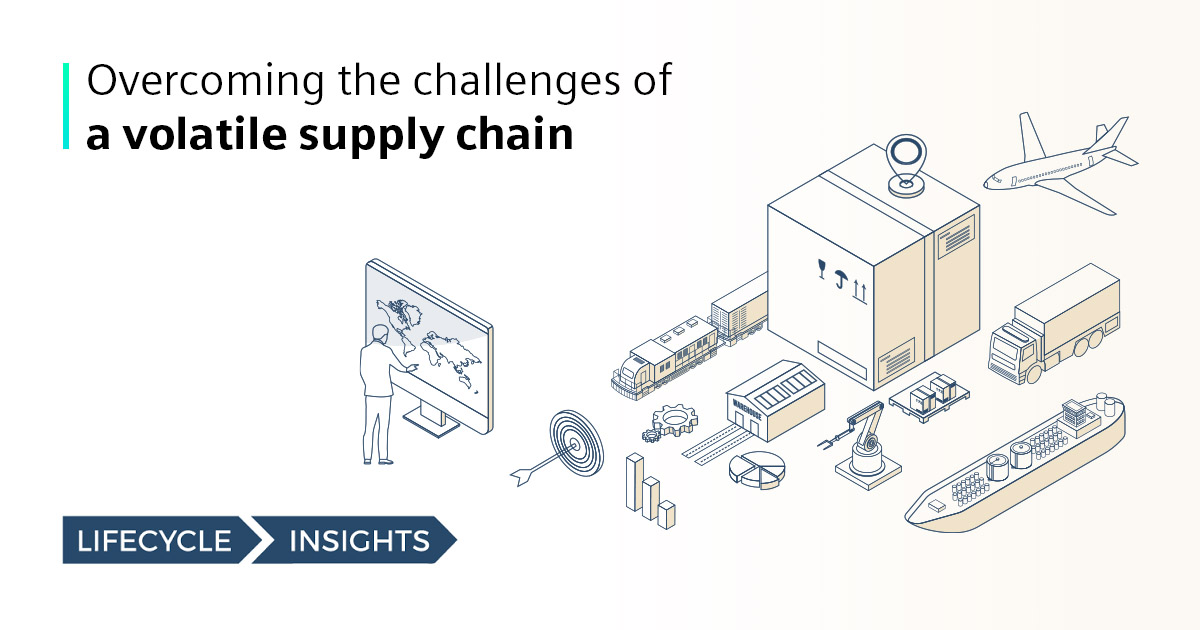
This blog was written by Chad Jackson, Chief Analyst & CEO at Lifecycle Insights, and comments have been provided throughout by Stephen Chavez, one of our own product marketing managers. Check it out and join the conversation below!
Today’s manufacturers are dependent upon an increasingly volatile supply chain. That is why it is so critical for companies that design and manufacture printed circuit boards (PCBs) to have reliable, accurate component supplier intelligence to guide them. Supply chain intelligence provides insights into specific component availability and pricing. It also offers real-time information that decision-makers can use to ensure they have all the components they need in inventory when it comes time to fabricate a design.
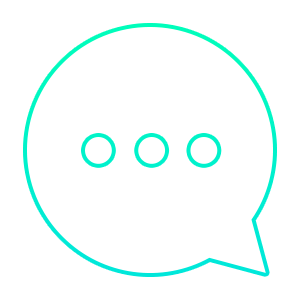
I agree with this opening paragraph. Supply-chain knowledge up upstream, at the point of design, will ensure greater potential for success downstream… from engineering to manufacturing to assembly. Bringing external touch-points internal arms engineers to make better intelligent component selection decisions when creating schematics. This reduces the potential of multiple loop backs in the process in the PCB layout due to supply-chain disruptions potentially forcing circuit redesign.
Stephen V. Chavez, MIT, CPCD, CID+ | Sr. Product Marketing Manager
Understanding your supply risks
Lifecycle Insights’ 2022 Electronics Design for Resilience (EDfR) study revealed that 74% of companies have to replace electronic components from their board designs at least once. Some respondents reported that they had to replace as many as 20 items per design due to component availability, lifecycle, or compliance issues.
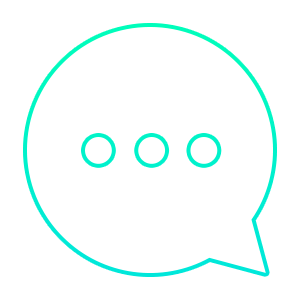
I can still feel this pain! I know firsthand, from my recent experience in dealing with the supply-chain disruption chaos and the negative affect it has on design teams. At this year’s U2U conference, I gave a presentation on the topic of supply-chain resilience where I describe this subject in more detail. I followed it up with a webinar, and I wrote a two-part series article published in June and July issues of Design007 magazine. In all instances, I provided a testimonial of my recent experience where I was forced to redo a PCB layout about a dozen times over just like what is described here in this paragraph. The entire project team felt this pain.
Stephen V. Chavez, MIT, CPCD, CID+ | Sr. Product Marketing Manager
This sort of supply chain disruption is most troublesome when manufacturers rely on a single source for their components. Sole-sourced approaches target the purchase from a single component supplier. This puts the manufacturer at significant risk of project delays that affect time to market and other key metrics.
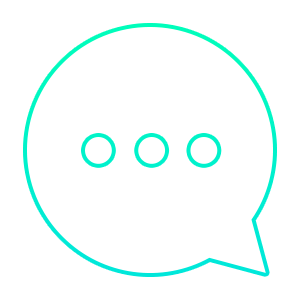
I view a single source supplier as a potential single point of failure opportunity waiting to happen… and today, its most likely to happen or is happening already within your ecosystem. This leads to delays, higher cost, and greater risk. Simply adding a new supplier to your AVL is not the solution to supply-chain resilience. Intelligence and real time data at the point of design is the solution.
Stephen V. Chavez, MIT, CPCD, CID+ | Sr. Product Marketing Manager
The risk is greatest when manufacturers use the traditional “throw over the wall” project workflow. In this linear workflow, engineers select a component without collaborating with suppliers or other company stakeholders and then pass the project to downstream departments. Today’s supply chain realities have exposed this approach as inadequate and unreliable for sourcing parts.
Insight into real-time PCB component availability and alternates is critical, especially in the midst of supply chain disruptions. It helps ensure sourcing for new electronic design projects and eliminates the risk of depending on components that are temporarily unavailable or have been discontinued. When these situations occur, organizations with access to supply chain intelligence can get the information they need on component availability, cost, and acquisition essentials.
Manufacturers are well aware of the need for strong supply chain intelligence—84% of respondents to Lifecycle Insights’ EDfR study stated they have begun efforts to strengthen their electronic supply chain resilience. Those improvements include revamping the processes engineers use to select components during design and moving to multi-sourcing instead of single sourcing for parts.
Revamping our legacy processes and methodologies is a must going forward if we want to stay competitive and continue to be successful. Refer to my published webinar, two-part series article and white paper to view a deeper dive into this specific subject regarding legacy processes and operations.
Stephen V. Chavez, MIT, CPCD, CID+ | Sr. Product Marketing Manager
It is clear that sole-sourcing components puts organizations at risk of supply issues. On the other hand, when companies select components with multiple supply sources, they can procure a part from a pre-specified alternate supplier if their first choice becomes unavailable.
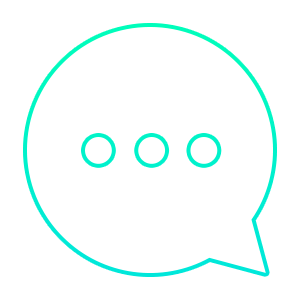
I agree with the general point being made here, but in most mil/aero companies, internal part numbers are used and listed on the BOM. That means that for every part number, there exist two to four approved alternates that can be used. So, when a part number on the BOM is identified as an “issue,” it potentially means that there is no alternate available at all. This is the dilemma most are dealing with today. What do we do in these situations? Go back and design out that part or feature. Search for, and hope to find, alternate available circuitry containing parts that are already approved in your library, or get an unknow part approved and into your internal systems for use? Mind you, that typically getting parts into the library is easily a three to five day turn-around delay. Worse case… take the hit on the delay and miss your target delivery date or time to market?
Having supply-chain market insight and real-time component data at the point of component selection, provides our engineers a greater potential for success. This is the key to supply-chain resilience.
Stephen V. Chavez, MIT, CPCD, CID+ | Sr. Product Marketing Manager
Taking supplier relationships to the next level
Establishing strong relationships with component manufacturers early in the design phase can help organizations stay abreast of component availability. This is particularly important when the component is specialized or there is only a single manufacturer that makes it. Accessing supply resources as early as possible in the design phase can provide engineers with invaluable insights to help drive informed design choices.
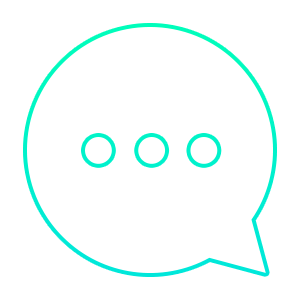
I have mixed feelings with what is stated here in this paragraph.
On one hand, I could not agree more with having a very strong relationship with your suppliers. It could potentially make all the difference. To me, this is common sense and applies to everything, not just in PCB design, but in life. Established “good” relationships have the potential to aid in getting past roadblocks. Like those phrases, “It’s all about who you know” or “I have a person on the inside who can hook me up”. Simply put… relationships are key part of success!
On the other hand, and this is where I disagree with the first statement in this paragraph, will having a strong supplier relationship somehow give you better insight to make better engineering decisions at the point of design? No, it will not. The relationship has nothing to with having or gaining the insight and intelligence at the point of design. Think about it for a moment. When an EE is at his/her computer and is all alone designing his circuit, he/she needs real time component insight and data information right then and there to make the best intelligent decisions on the fly. It is at that moment, the relationship with the supplier has nothing to do with supply-chain resilience at the point of design. The relationship comes more into play from a purchasing procurement strategy and when engineering technical support is needed.
Stephen V. Chavez, MIT, CPCD, CID+ | Sr. Product Marketing Manager
Artificial intelligence (AI)-based software-as-a-service (SaaS) solutions, for example, can provide engineering teams key insights and decision support that was previously unavailable to them. These solutions bring innovative levels of resiliency and performance to product design.
By facilitating the right relationships and partnerships early in the design process, organizations can:
- Address supply forecasting at the earliest point of design
- Be informed of emerging trends and data for sourcing decisions
- Mitigate supply risks by pre-defining alternate parts and suppliers
- Avoid costly component spot buys and other additional procurement costs
- Prevent manufacturing delays and downtime
- Keep product launches on schedule
Creating a supply back-up plan
Visibility into emerging supply trends across the industry is key to managing supply chain disruptions. With the right data available, companies can better support timely, effective, and agile sourcing decisions to ensure product delivery.
Today, supply chain disruptions are causing significant delays in the procurement of “popcorn” components—inexpensive, common, discrete parts like resistors and capacitors. Lead times are as long as 52 weeks and, in some cases, even longer. Suppliers are busy; in fact, they are currently reporting a record high 90% capacity utilization for the production of fuses and varistors across the globe. They are also having to contend with a four-fold increase in demand for connectors by the automobile industry alone. Manufacturers need access to supply chain insights to understand what their suppliers are dealing with and to make better component and chipset selections as they create their designs. Furthermore, they can use that data to make these important orders at the earliest point possible.
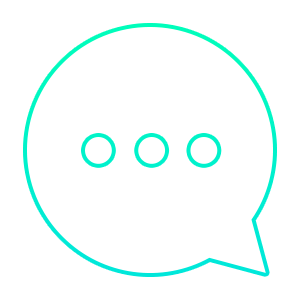
Adding to this problem is panic and spot buying! This rush/panic to buy 1000 pieces of a component instead of the typical 100 piece schedule purchase adds a snowball ball effect within the industry, because everyone else gets notified that available quantities are dropping rapidly, and so the panic begins. Just like in our personal lives with the everyday items at the grocery store… either on limited quantities or simply not available. So having supply-chain insight (knowledge/intelligence) is very important.
Stephen V. Chavez, MIT, CPCD, CID+ | Sr. Product Marketing Manager
Companies must also select component alternatives as early in the design process as possible. Having the insights necessary to make alternate component decisions is a critical step in the design definition phase. Companies recognize this and are expanding their approved vendor lists (AVLs) to further address supply challenges. Some 85% of study respondents noted they have grown their AVLs by as much as 25% in a bid to avoid potential supply issues.
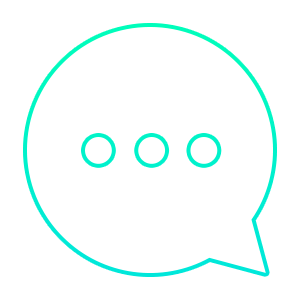
Having an extensive AVL is very important, but caution need be maintained when adding new suppliers to your AVLs simply in response to the lack of supply-chain resilience built into your internal processes.
It’s not the quantity of your suppliers listed on your AVL, but rather the quality and what value they bring to the table. Simply expanding your AVL in response to lacking supply-chain resilience in your processes potentially leads to questionable suppliers and questionable parts. There becomes more potential of getting subpar parts, reclaimed parts, or counterfeit parts. I would be very suspicious if an unknow supplier just happened to have stock of a part that is currently unavailable through all typical suppliers on your AVL, especially if that part is in high demand! You have to ask the question: “How is it that this supplier magically has supply when everyone else does not?” Subpar parts, reclaimed parts and counterfeit parts are now more common than ever before. Be careful…
Stephen V. Chavez, MIT, CPCD, CID+ | Sr. Product Marketing Manager
Harnessing design tools to overcome supply chain challenges
Historically, electronic design tools have not required nor offered access to real-time supply insights. In the past, companies were forced to take a reactive approach to supply issues; there simply was no alternative to addressing them on the fly.
Today, however, it is critical to know when a specified component is unexpectedly out of stock, or whether demand or market prices have increased to negatively affect your schedule or budget. Companies need this information to make quick, reliable supply decisions and avoid production delays.
Real-time supply chain intelligence provides information throughout a product’s design flow, connecting design tools with the component supply chain. When organizations have an integrated connection between their computer-aided design (CAD) tools and their suppliers, they can perform a comprehensive bill of materials (BOM) analysis throughout the design phase. This active supply chain connection enables teams to react to any changes and make component supply decisions when the cost of change is at its lowest.
Modern design tools have integrated component sourcing information so that designers and stakeholders can receive up-to-date supply sourcing alerts throughout the design cycle. This allows them to make decisions quickly without ever having to leave the design tool.
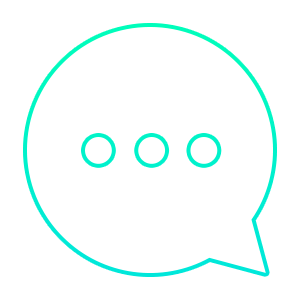
When it comes to designing PCBs with today’s engineering tools, many stay within their confront zones and continue to use known legacy methodologies that have allowed them to be successful so far. But these legacy approaches do not include supply-chain resilience. This is what is missing to mitigate the supply-chain disruptions. Engineers need to be able to have to supply-chain market intelligent and foresight to make better, more intelligent decisions at the point of design.
Now, don’t even get me started with designers and engineers of today who don’t harness the horsepower and functionality of the advanced capabilities within today’s engineering tools. You’d be surprised how many still use the same “~20” clicks of a manual approach within their tools that they have been doing for the last 20 years, even though our engineering tools keep advancing year after year in capability and functionality. That’s for a separate discussion regarding industry best practices which I be presenting on at this year’s PCB West. I hope to see you there.
Stephen V. Chavez, MIT, CPCD, CID+ | Sr. Product Marketing Manager
A PCB design flow that supports integrated supply chain access saves companies substantial time and costs by eliminating traditional supply chain issues. The benefits include:
- Quicker BOM approvals: 85% of respondents to Lifecycle Insights’ EDfR Study said it can take anywhere from three days to a month, or even longer, to get BOM approval in their current design flow. This delay increases both cost and time to market.
- Real-time supply issue notifications: Currently, 75% of companies report moderate to high difficulty receiving notifications from suppliers regarding component changes.
- Improved revenue: Some 51% of survey respondents said component sourcing issues had a moderate to large impact on their company’s revenue during the past year.
- Better products: Adopting an integrated solution can address most supply chain problems. Then, designers and engineers are not distracted or bogged down by having to spend time searching for sourcing data. Instead, they can focus more on innovations and optimizing product designs.
- Improved supply chain resilience: Per the EDfR survey, while 84% of companies are working to strengthen their supply chain resilience, only 18% have implemented technology to do that. This means most organizations are grappling with unnecessary product delays and cost increases due to late-cycle component changes. On the other hand, manufacturers that gain access to real-time supply chain intelligence through CAD tools or other integrated solutions are in a better position to fortify their supply chain resilience and respond to unexpected disruptions.
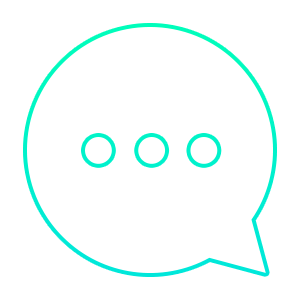
These are all good points regarding the current linear approach of PCB design that needs to be updated with supply-chain resilience at the point of design. By doing this, it allows for BOM analysis to be made farther upstream and real-time supply-chain notices (intelligence) arm engineers to make better more intelligent component selections decisions on the fly, potentially eliminating delays. It provides the best potential for success in designing better products with fewer delays, reduced costs, and lower risks, not to mention, lessening the stress placed on the entire project team.
Stephen V. Chavez, MIT, CPCD, CID+ | Sr. Product Marketing Manager
Designing for resilience
Companies do not have to be at the mercy of an unreliable supply chain. Access to accurate and timely component supplier intelligence enables companies to make informed and cost-effective component selections early and throughput the design process. Today, that intelligence must be directly integrated with common CAD tools, offering engineers and decision-makers real-time information to ensure they will have the parts they need when it is time to start production.
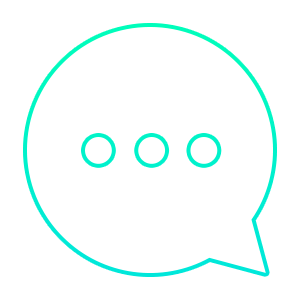
Nice summary here. The bottom line is this: the old legacy approach and methodologies of designing PCBs simply no longer cut it if we wish to continue to be successful as we traverse and emerge from these cloudy waters of the supply-chain chasms we are all experiencing today. Intelligence at the point of designs is key to supply-chain resilience. This includes updating internal collaboration within our respective ecosystems so that multidiscipline collaboration, optimization, and integration can be we achieved. This approach ensures our best potential for overall success.
Stephen V. Chavez, MIT, CPCD, CID+ | Sr. Product Marketing Manager