Aerospace program risk countered with digitalized solutions
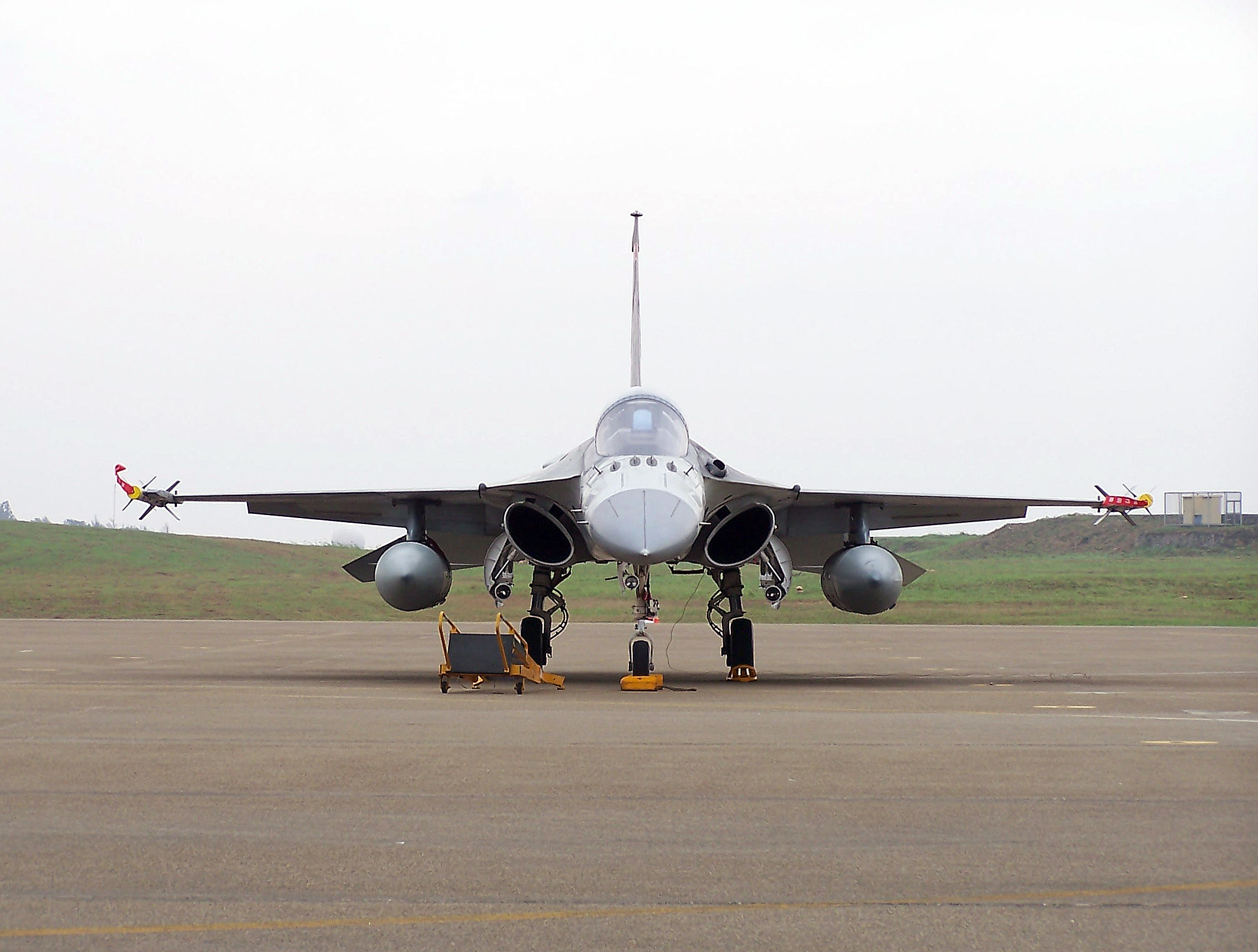
Electronic and electrical design demands of the 21st century will no doubt present a tremendous challenge to aerospace OEMs. There is a need to constantly innovate, but with innovation comes risk. How do you limit aerospace program risk to stay profitable?
Today, addressing exposure arising from electrification must be part of the mix. For example, while electronic and electrical content infuse long-term value into platforms, they bring new uncertainty to the task of platform integration. Historical platform integration approaches, dominated by processes optimized for the mechanical discipline, must be updated.
Further, aerospace design complexity is compounding dramatically year over year. Now more than ever, design requirements interact across multiple disciplines impacting the product hierarchy across the supply chain, demanding sophisticated implementations and increasing program risk.
Outside of growing complexity, additional challenges exacerbate program risk:
- Greater pressure on profit margins from new competitors
- The need to continuously increase production rates
- An increasing number of government/safety regulations
- New and tighter cost controls
- Greater emphasis on just-in-time, quality deliverables
- The need to re-purpose and re-use across multiple platforms
- More supply chain collaboration and automation
In order to address these mounting demands – and stay competitive – OEMs are digitalizing the design and integration of electrical and electronic systems. Moving to an integrated and digitalized approach allows manufacturers to achieve a much better balance between innovation and risk by seamlessly exploiting what is known about the product and its production process at any given time (figure 1). With it, design project teams stand a much better chance of staying within budget and time constraints.
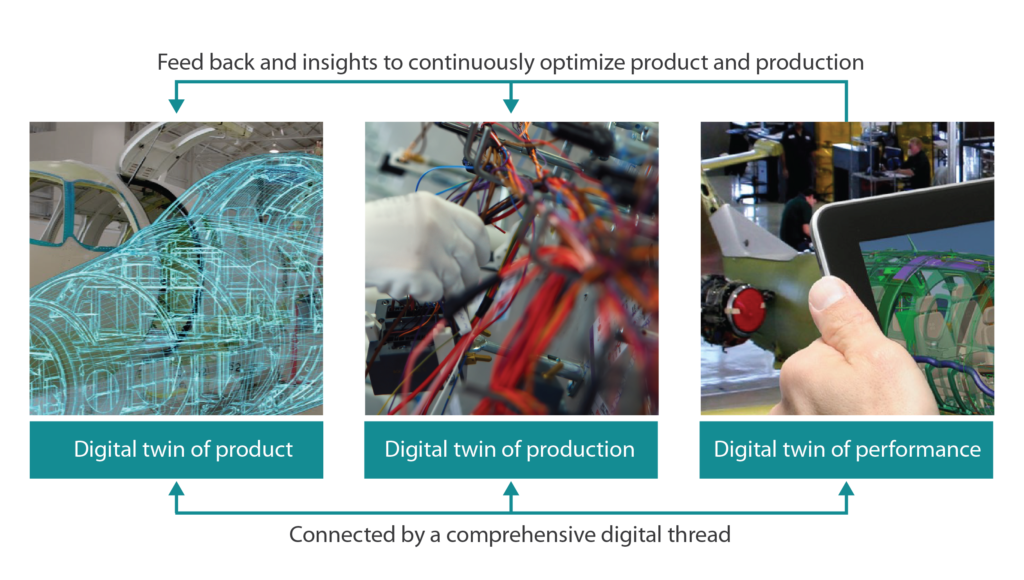
Because electronically enabled functions are being introduced into all aspects of the platform, semi-manual development methods of the past are no longer adequate and, in many situations, counterproductive. On a single commercial aircraft today, there are hundreds, if not thousands, of electronic devices/units, miles of electrical wiring, a multitude of configurations to implement and numerous safety and certification requirements to take into consideration. Manual and disjointed hand-off of requirements, work-in-process design data and final product descriptions are no longer an efficient business practice.
Implementing the digital thread
As we enter a new era in aerospace development, digitalization will require a new perspective on familiar challenges as well as new methods to deal with a growing list of complexities. This will be critical to lowering risk throughout the entire product lifecycle. The Capital tool suite from Siemens offers aerospace electrical system developers a significant step forward.
By grounding the electrical discipline in a more integrated and virtual environment, aerospace manufacturers increase engineering team and vendor engagement, improve response times, introduce new technology and innovation, reduce cost of documentation and improve affordability up and down the supply chain through repurpose and re-use. Most important, engineering teams reduce the probability of being surprised by an unexpected issue during platform integration that could force a costly iteration, which in turn, could impact budget, schedule and individual careers.
The E/E tools from Capital provide the only mature, end-to-end digital thread for electrical system design and integration. The tool suite is at the forefront of Program Execution Excellence. It is the only electrical environment that spans the full electrical system value chain – from electrical system definition, through design, manufacturing and into support and maintenance.
To read more about reducing aerospace program risk, please download our whitepaper The digital thread: Reducing electrical system program risk.