Your aerospace harness installation design checklist
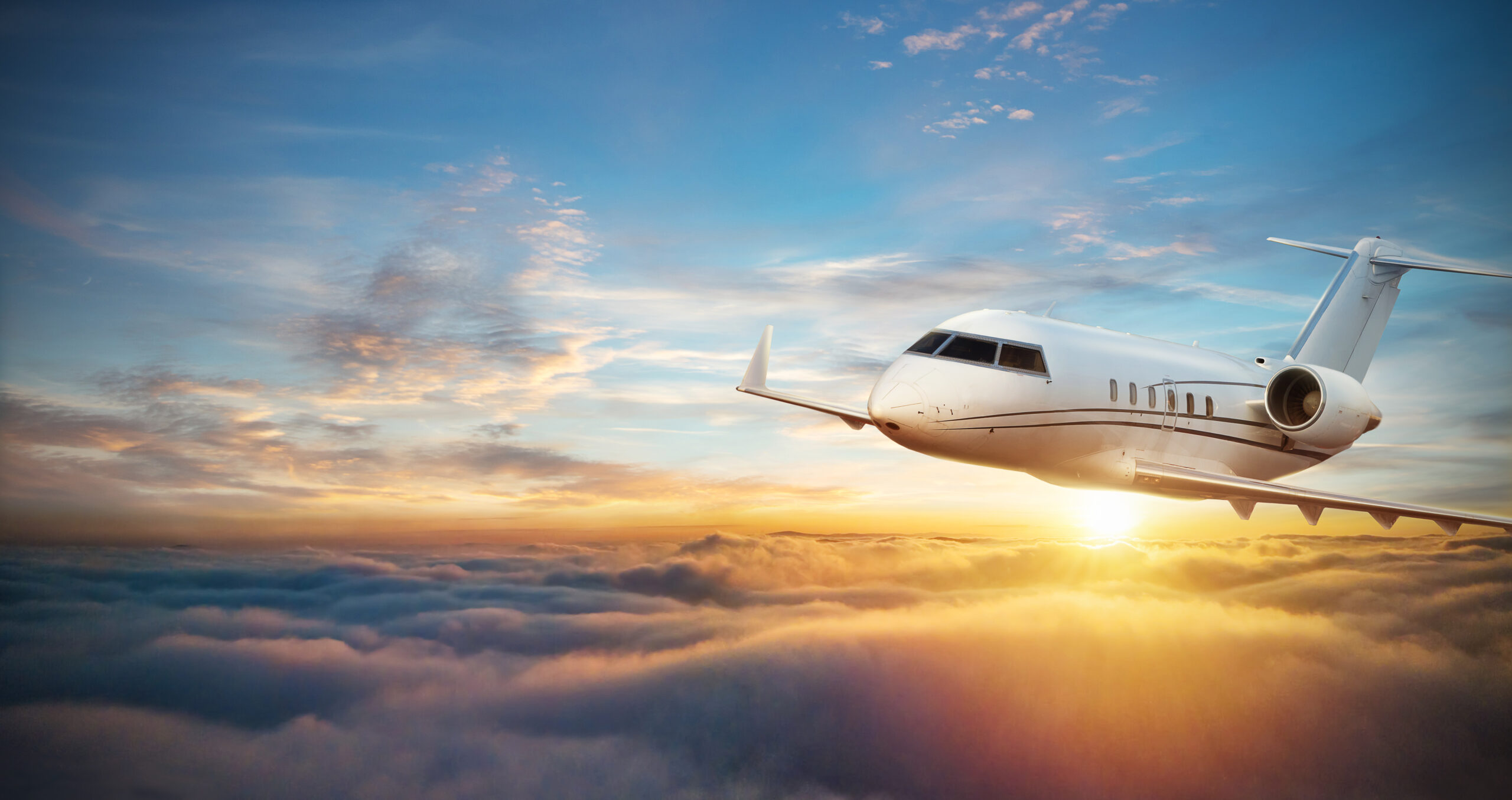
A formula for success as complexity increases in aerospace must include harness installation design. The design for a wiring harness installation can be as complicated as the selection of components for the harness itself.
Each signal, and the wiring harness that carries it, can and will transition through multiple environmental zones. Each zone has a unique installation and component requirements. Signals which transition multiple zones also require wires, connection devices and covering selections. Accordingly, this is so that they will “be of a kind and design appropriate to its intended function (pdf).”
A critical aspect of the installation is the “competition for space” with all other design disciplines. These other disciplines are also attempting to install things like equipment, cables and fluid carrying lines. This competition requires that each area of the aircraft have a “zonal manager” that plays traffic cop to ensure the safe and repeatable installation of all components, including the electrical harness.
However, considerations for the harness and its content does not end with environmental and system function requirements. Here is a checklist of other factors to consider.
- Proximity to other components which:
– Experience motion relative to the harness
– Generate heat
– Have internal cooling fans that, when dislodged, will pose a danger to each harness directly in the path of those fan blades
– Carry fluids or gasses - Separation of signal types, such as digital audio, critical systems, analog and voltage/current levels
- Fluids both internal and external to the aircraft to which the harness will be exposed
- Steady-state and dynamic temperature fluctuations to include altitude
- Vibration and or shock levels
- Redundant system separation in that a single failure by one component cannot pose a threat to each of the harnesses of that redundant system
- Harness bend radius
- Chafing against other components or structures
- Latent harness support failures that could contribute to fuel tank ignition
- Access to inspect and perform maintenance on each harness
- Connectors that could be mistakenly cross-connected to the wrong mating pair are not allowed
Each item listed above requires the appropriate level of design consideration and must meet the intent of any regulations listed in a certification plan. Additionally, the harness installation design must consider the repeatability of that design or the ability of the technicians to install that harness with the same precision every time. Tape markers located along the length of the harness are becoming the preferred method for the commercial market but are a “must-do” for military aircraft. These markers placed strategically along the harness indicate critical installation clamping points and help to ensure the correctness of that installation.
To learn more about aerospace electrical system design and integration, download our white paper here!
You also might be interested in our paper: Managing change in aerospace platform electrical systems for competitive advantage.
There is also a great webinar on mastering the physical context of aerospace electrical system development.
And finally, check out this very popular industry eBook produced by EE World on addressing complexity and minimizing risk in modern aerospace electrical platforms.