5 steps to optimizing E/E systems in aerospace with Capital
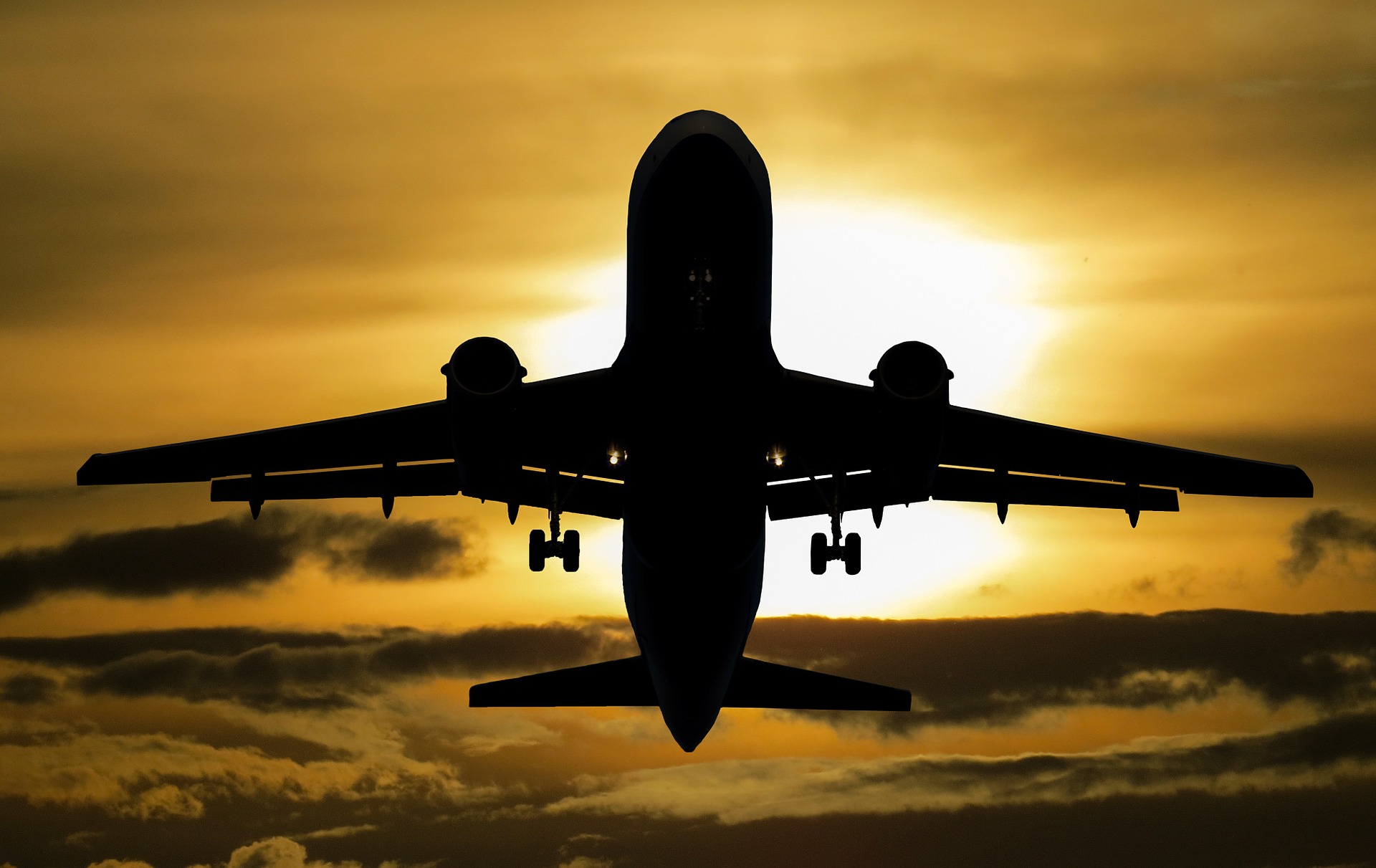
Modern aircraft feature increasingly complex electrical and electronic or E/E systems. In fact, the electrical wiring interconnect system in today’s aircraft now accounts for about 3% of their total weight. Accordingly, this demands more power than ever. What’s more, electrical systems volume increases by 25% every five years. Higher costs and increased electrification present an array of challenges for aircraft manufacturers. For example, this can include staffing difficulties, tougher certification requirements and compliance headaches. All of these can delay entry into service.
However, taking shortcuts to speed development time isn’t possible. E/E systems must be carefully designed, tested, verified and validated to ensure their performance, safety, security, and regulatory compliance. Finding issues that result in changes late in the process can cause delays due to lengthy redesigns, time-consuming rework, and the need for recertification. This can drive costs up substantially, eating away at margins.
What if E/E system architects and designers could imagine, invent and understand the implementation implications of alternative E/E system architectures before committing to one and beginning the design phase? Imagine how helpful it would be to explore the development and operational impacts of various approaches first and then choose a better starting point. With Capital, Siemens Xcelerator’s E/E Systems Development environment, that’s possible.
Model Based Engineering and the Digital Twin
Capital employs a data centric approach to E/E system development. It combines data from model-based systems engineering (MBSE) environments, systems architects, and E/E system designers to create an optimized digital twin. The digital twin is a virtual representation of the physical product that’s used to understand and predict the physical counterpart’s performance characteristics. Taking a model-based approach to E/E systems development reduces risk and costs and enables aircraft manufacturers to deliver cutting-edge capabilities to market – faster.
Capital’s integrated solutions and innovative model-based engineering enable data-driven program orchestration, agile product development, and reliable verification with a digital thread that eliminates data silos and simplifies certification and compliance. Let’s examine how Capital optimizes the E/E system development process, step by step:
1. Refine early architectural allocations in the context of the platform
Capital absorbs the physical layer, behavior, and physical components of system models from any source, then normalizes them to ensure they are held within a common data model. Next, it prepares for downstream engineering. The solution transforms multi-domain system models into domain-specific E/E design proposals, enabling optimized, configuration-aware network, software, electrical distribution, and hardware system models.
2. Embellish models with the E/E systems content needed by downstream engineering tools
Within Capital, the E/E system architecture model is enhanced to incorporate signals and functions that span multiple electrical systems. These can then be embellished by E/E architects with network and software signals, configuration specifics and physical characteristics. This step automates function allocation as well as the process of assigning signals and messages to network carriers.
3. Integrate multiple electrical systems into a complete platform, in the full context of its physical topology
Architects can use Capital to generate physical abstractions of the platform and assess the viability of an architectural approach. They can validate and optimize connectivity using the digital twin, accounting for each systems’ functions and signals as needed, before beginning a full-scale physical implementation. This substantially reduces the need for costly rework later in the design cycle, while enabling architects to try out various ideas.
4. Generate detailed design implementation proposals directly from the architecture
Through generative design, architects can skip the process of manually transitioning from the E/E system architecture to designing for implementation in the downstream tools. Instead, they can leverage a data-based transition. This way, everyone is working from the same data, and can easily trace implementation details back to the original design specifications.
5. Perform an architectural assessment
With Capital, architects can estimate system performance to ensure they meet their KPIs for weight, cost, network latency, network traffic and CPU load prior to design implementation. In this way, they can assess multiple architectural models, and select a better starting point for system implementation.
By exploring architectural alternatives early in system development, architects can eliminate obstacles and work through design challenges before engaging design teams in the physical implementation, saving time and effort, reducing the number of iterations, and accelerating the development cycle.
Pushing the Boundaries of Innovation
Siemens Capital enables Aerospace and Defense OEMs to become digital enterprises, with an integrated solution that eliminates boundaries between all phases of E/E systems development – from E/E architecture design and assessment, through E/E system design and implementation, testing and validation. With Capital, organizations can push the boundaries of what’s possible and innovate safe, compliant, high-performing, reliable systems for next generation aircraft.
To learn more about how Siemens’ technology enables System Driven Electrical, Electronics, Network & Software Design, download our whitepaper. Learn more about Siemens’ solutions for Aerospace and Defense, here.
You also might be interested in learning more about digital twins in our paper: Managing change in aerospace platform electrical systems for competitive advantage.
Check out our short video on Aerospace E/E systems development and the digital twin here.
There is also a great webinar on mastering the physical context of aerospace electrical system development.
And finally, check out this very popular industry eBook produced by EE World on addressing complexity and minimizing risk in modern aerospace electrical platforms.