MBSE enables advanced E/E architecture development
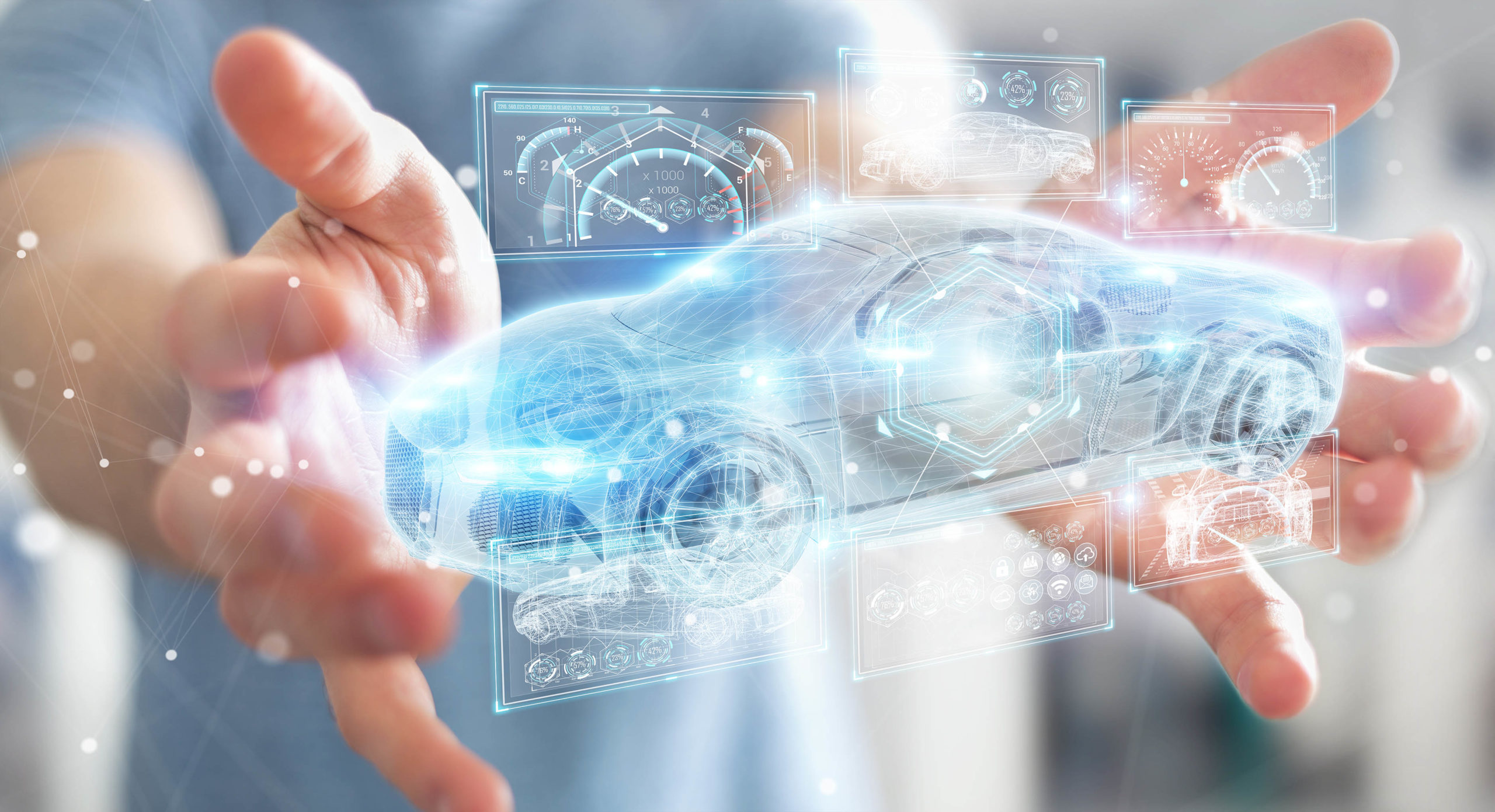
New vehicle technologies are driving a rapid increase in the complexity of vehicles in all segments due to the sophisticated electrical, electronic and electro-mechanical systems required (figure 1). Modern mid-range vehicles contains about 90 ECUs connected by a variety of high and low-speed networks to dozens of sensors and actuators. These modern architectures have grown in size and complexity to support new features such as advanced driver assistance systems (ADAS), sophisticated infotainment systems, navigation and more. Now, more sophisticated vehicle automation, electrification and connectivity systems are driving vehicle OEMs to incorporate new technologies into their vehicles. In particular, manufacturers are attempting to integrate new communications technologies to connect their vehicles to 5G networks, WiFi and to enable vehicle-to-everything (V2X) communications.
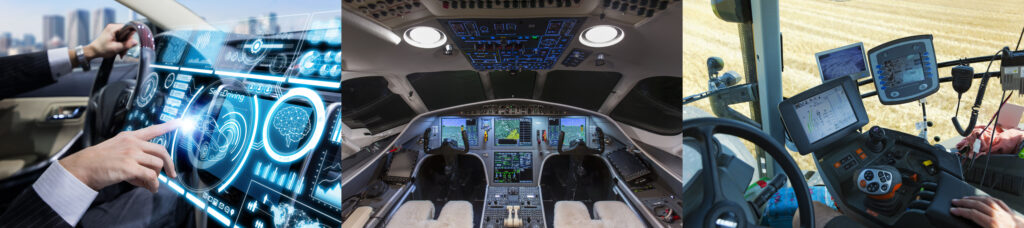
In addition to more complicated vehicles, OEMs have to manage the lifecycles of all of these software, network and electrical components, along with all of the other vehicle systems and parts. This involves the coordination of the development cycle to support the launch of the lead program, while ensuring that requirements from later programs have been incorporated. As OEMs manage the production life-cycle of the software and components, they must ensure components are appropriately used in the production and service of each vehicle variant and configured to match each vehicle specification. This involves multiple teams in very different parts of the organization.
A small error in the partitioning of functions in the vehicle definition could lead to safety related functionality being dependent on systems with insufficient integrity in the design and development process. This can lead to costly late program changes or, worse, in field recalls to update multiple ECUs after field failures occur. Incorrect component configurations can also lead to incorrect or lost vehicle functionality, causing customer dissatisfaction and additional cost to identify the population of affected vehicles in production and in the field. Managing this complexity and ensuring traceability throughout the development process will be crucial to creating advanced automated and connected vehicles and to bringing these vehicles to market on the tight timelines common in today’s automotive, aerospace and commercial vehicle industries.
MBSE for E/E architecture design
The exploding complexity of modern vehicles demands a change in design methodologies. Where traditional methods relied on manual operations and separated engineering domains into silos, future engineering strategies must employ automation and support collaboration through robust data integrity and integrated solutions. Model-based systems engineering (MBSE), with an advanced portfolio of engineering software solutions, can provide these crucial capabilities for developing the increasingly sophisticated E/E architectures of modern cars, planes and commercial vehicles.
MBSE enables engineers to leverage existing functional models and engineering data from various environments in the creation of vehicle architectures and more detailed system designs. By continuously building on data from upstream processes, MBSE ensures traceability and streamlines change management and implementation (figure 2). Much of the processes involved in consolidating models, creating architectures and maintaining traceability, however, are still accomplished manually. Modern E/E systems engineering solutions can improve these processes by automating manual tasks and providing a unified database to ensure data continuity throughout E/E architecture and system design.
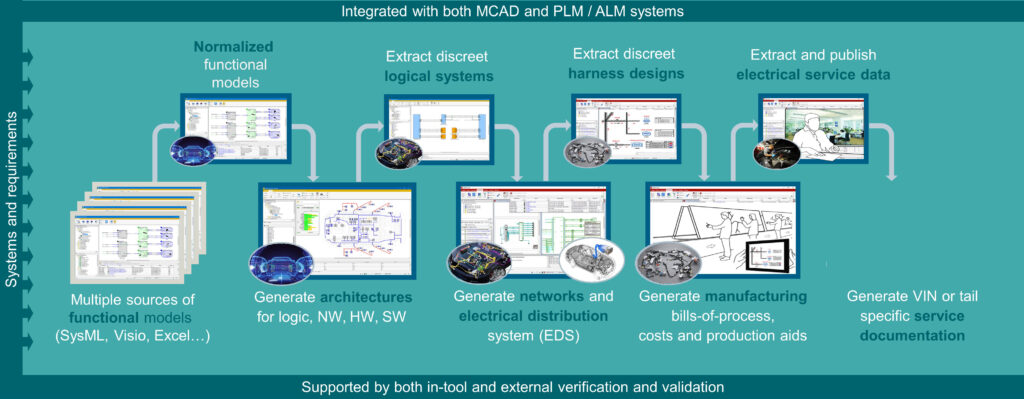
Today, E/E systems engineering solutions, such as Capital from Siemens Digital Industries Software, can automate much of this work. Instead of adding the necessary domain detail in the systems engineering environment, advanced E/E systems engineering software can import the functional design abstraction, allowing engineers to embellish this abstraction, at the platform level, with domain details for the software, hardware, networks and EDS. The software then uses rules-based synthesis to deploy functionality in the vehicle platform with the granularity required for subsequent domain engineering processes.
These specialized E/E engineering solutions also feature built-in metrics for both logical and physical key performance indicators (KPIs), including cost, bandwidth utilization and more. These metrics can drive early optimizations and, coupled with rule-based synthesis, rapid iteration of the E/E architecture. Design rule checks can then identify violations or issues in the physical design abstraction, such as excess bandwidth or ECU utilization.
To learn more about how modern E/E systems and wire harness engineering solutions can support an advanced MBSE development flow, download our whitepaper, The advantages of MBSE-driven E/E architecture development.