Lightweight EV design requires multi-domain approach

Are self-driving cars the future? It’s possible, but significant obstacles – both technological and societal – stand in the critical path to true autonomous vehicles. Predictions on when the first fully autonomous vehicle will become available vary widely. Tesla has predicted its cars will be fully self-driving by the middle of 2020, while other organizations don’t expect these vehicles will be ready for at least another decade or longer, if ever. Vehicle electrification, on the other hand, is already changing how cars are manufactured, sold, used, and supported. While the future of vehicle autonomy is somewhat murky, we can be certain that electric vehicles (EVs) increasingly will become the norm over the next decade.
This does not mean that EV design, manufacturing and deployment is devoid of any challenge or complexity. Manufacturers of EVs face unique challenges in designing and manufacturing compelling offerings in a market that is rapidly saturating.
In this blog, we will look at efforts to reduce vehicle weight and improve battery technology as a means of maximizing electric drive range, a key differentiator for a competitive product.
The weight of electrification
Vehicle weights have steadily increased over the last thirty to forty years. One of the most striking examples is the modern Mini. In the 1960s a Mini Cooper S weighed under 700 kilograms; today’s Mini Countryman comes in at almost 1500 kgs, more than doubling the weight of the original (carfolio.com, 2019; Car and Driver, 2019). The increased weight of the Mini Countryman is the result of years of evolution in the automotive industry in which the car has gone from a relatively simple machine to a highly sophisticated mixture of mechanical, electrical, electronic, and software systems.
Electric drivetrains and batteries add even more weight to the vehicle; the battery alone can weigh over 1,000 pounds (figure 1). The weight of EV powertrains and batteries presents a twofold problem. First, vehicle weight is a critical determiner of the drive range of an electric vehicle. An object’s weight directly contributes to the amount of energy required to accelerate that object. Specifically, a 10% reduction in vehicle weight can result in a 6%-8% fuel economy improvement. Second, for most EVs the drive range they can achieve on a single charge continues to be a major limiting factor in their appeal to, and thus adoption by consumers who drive internal combustion vehicles.
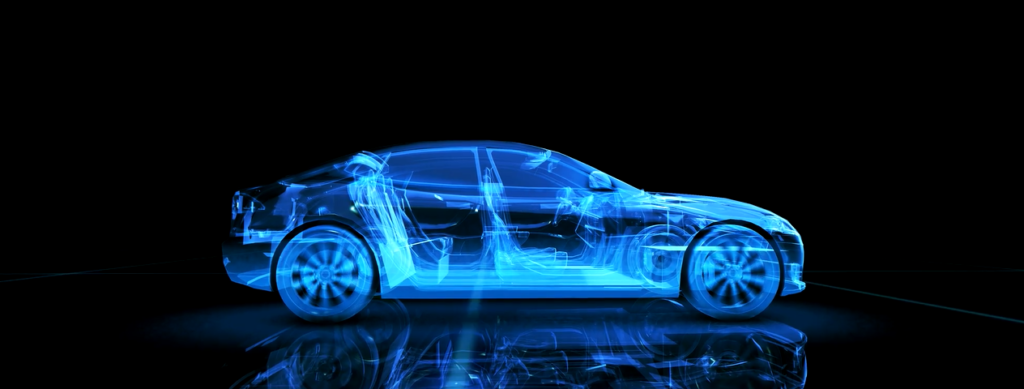
A diverse approach to managing electric vehicle weight
Solutions to the problem of electric vehicle weight and drive range are multi-faceted, requiring a combination of lightweight construction, architectural optimizations, and improving battery technology and packaging. Reducing the weight of vehicle bodies through the use of advanced materials and composites is the most direct method of counteracting the weight of an EV powertrain. Replacing conventional materials with lightweight magnesium and aluminum alloys or carbon fiber can reduce the weight of a vehicle body and chassis by up to 50 percent. However, these materials have to be incorporated intelligently to prevent weight savings from compromising structural rigidity, and thus safety as well as staying in line with vehicle cost targets. You can read more about these strategies in this whitepaper: Moving Electric Vehicle Manufacturing into the Fast Lane.
In addition to multi-material construction, automakers are attempting to reduce vehicle weight by consolidating architectural components to simplify the vehicle wiring harness. Modern wiring harnesses contain roughly 700 connectors and over 3000 wires (figure 2). In total, the wiring harness can weigh approximately 132lbs (60kg), typically making it the 3rd heaviest system in a vehicle behind the powertrain and seats. However, an electric vehicle wiring harness will likely exceed this weight due to the particularly heavy high-voltage wires needed to connect the electric powertrain. Consolidating electronic components, such as ECUs and sensor modules, allows manufacturers to reduce the number of components that must be connected via the vehicle’s wiring harness, therefore reducing its size, complexity, and weight. Consolidating powertrain components can eliminate high-voltage wiring, making it an especially effective light-weighting strategy.
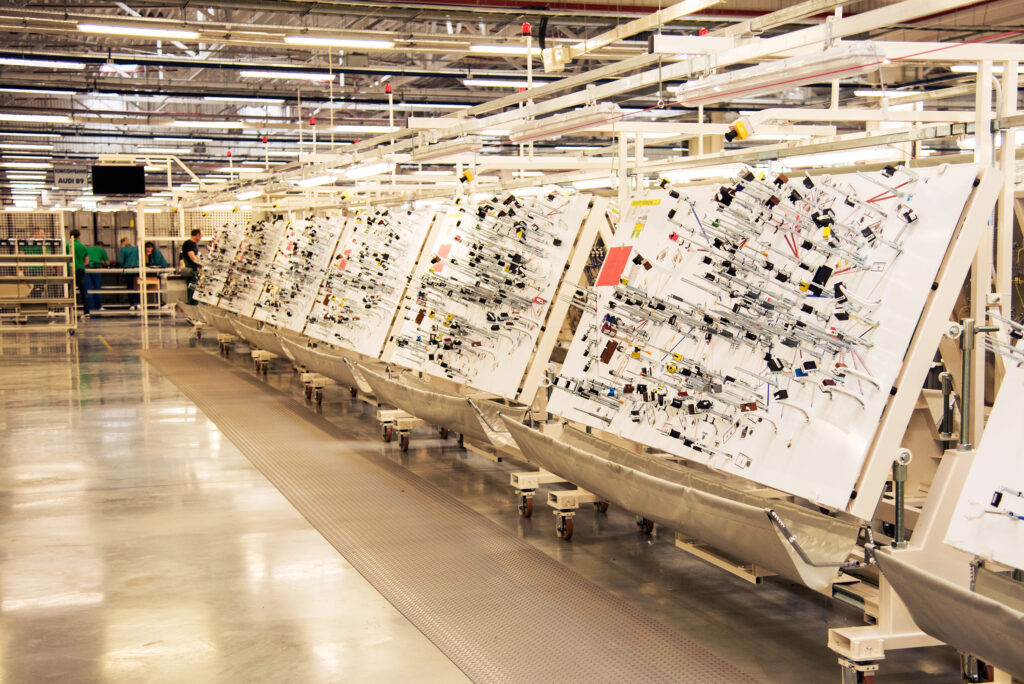
Architectural consolidation, however, requires a balanced approach to achieve optimal results. Some components, particularly sensors, must be distributed around the vehicle to operate effectively. A vehicle with only a few centralized ECUs would still need to connect with each of these sensors around the vehicle, erasing the reduction in wiring from consolidating around those few ECUs. Architectural and wiring synthesis paired with robust analytics will prove critical to achieving such a balance.
Lightweighting and consolidation are useful methods of improving vehicle drive range and reducing weight, but their effectiveness remains limited by the vehicle platform underneath. In an effort to bring product to market quickly, many automakers have based EVs on existing internal combustion (IC) platforms or vehicles. While relatively cost-effective and faster to produce, these adapted vehicles cannot match the range and performance of an EV built upon a bespoke all-electric platform. EV-specific platforms provide greater flexibility in battery packaging and powertrain configuration. For example, EV-specific vehicle platforms can support battery packs that are up to 25 percent larger than adapted IC platforms. In addition to the packaging optimization opportunities that enable weight reduction, the ground up approach allows for not only a streamlined design, but an attractive and compelling one.
Intelligent designs pave the way for EV adoption
To attract new customers and make their vehicles competitive with mainstream IC vehicles, EV manufacturers and suppliers will need to invest in lightweight materials, novel EV architectures, and improved battery packs that both store and use energy more efficiently. Using lighter weight materials in the construction of the vehicle body is a key strategy, but it is not a complete solution. EV manufacturers will need to explore new, native EV architectures that optimize battery packaging along with other electrical and electronic (E/E) systems. Improvements in battery chemistry will also play a key role in bringing EV range and usability on par with IC vehicles.
In support of these efforts, technology partners, such as Siemens Digital Industries Software with its Xcelerator portfolio, provide engineering software that can help EV manufacturers design, verify, validate and produce EV systems and platforms. 3D modeling and structural simulation software can help engineers integrate lightweight materials while maintaining the strength of the vehicle chassis and body. Likewise, an advanced E/E systems engineering solution will provide rapid architectural and wiring harness iteration through design automation and built-in metrics. Finally, specialized battery simulation and design software can help engineers optimize cell geometry and packaging within the battery, while computational fluid dynamics (CFD) software can demonstrate the thermal performance of the cells.