The E/E architecture and the future of automotive innovation
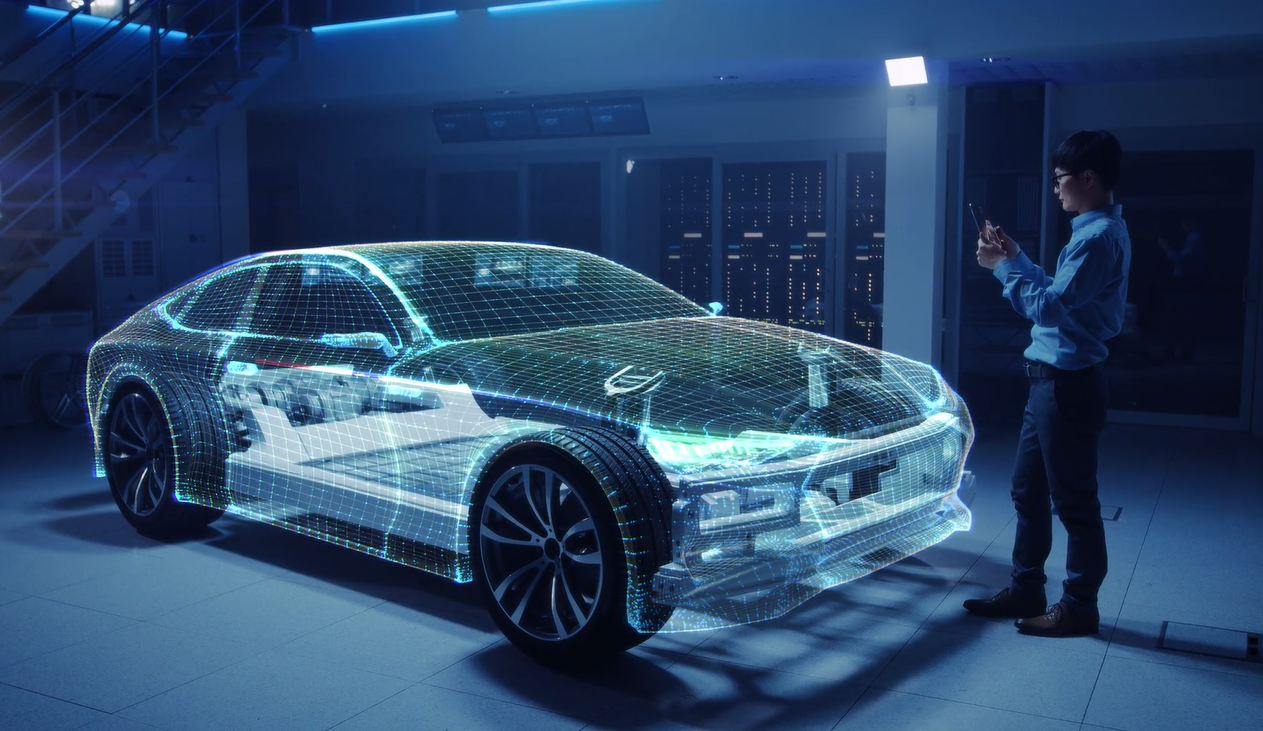
Over time, vehicles have become dramatically more complex due to technological advances and consumer trends. Mechanical systems accounted for most of this complexity for much of the car’s history, but electrical and electronic systems have steadily increased in sophistication. Engine management, braking, steering, infotainment, and other comfort and convenience features rely on the electrical and electronic systems. Embedded software has also come to play a dominant role in vehicle functionality. Modern cars contain millions of lines of code that make up applications for everything from the most advanced infotainment and passive safety features to the automatic door locks. Today, a majority of vehicle features are aided or enabled by electronic components, embedded software, and the underlying electrical and electronic (E/E) architecture.
As vehicle features continue to evolve and grow in sophistication, previously unrelated subsystems will come into contact. Systems that previously evolved independently will begin to integrate, and depend on each other to realize new functionalities. The introduction of cruise control in the late 1950s was the first integration of electrical and mechanical systems in a vehicle (figure 1). Since then, cruise control has continued to evolve. Adaptive cruise control systems allow modern cars to slow down and speed up as needed to maintain a driver-determined following distance (figure 2). And, automated emergency braking systems can bring vehicles to a complete stop even if the driver is not paying attention.
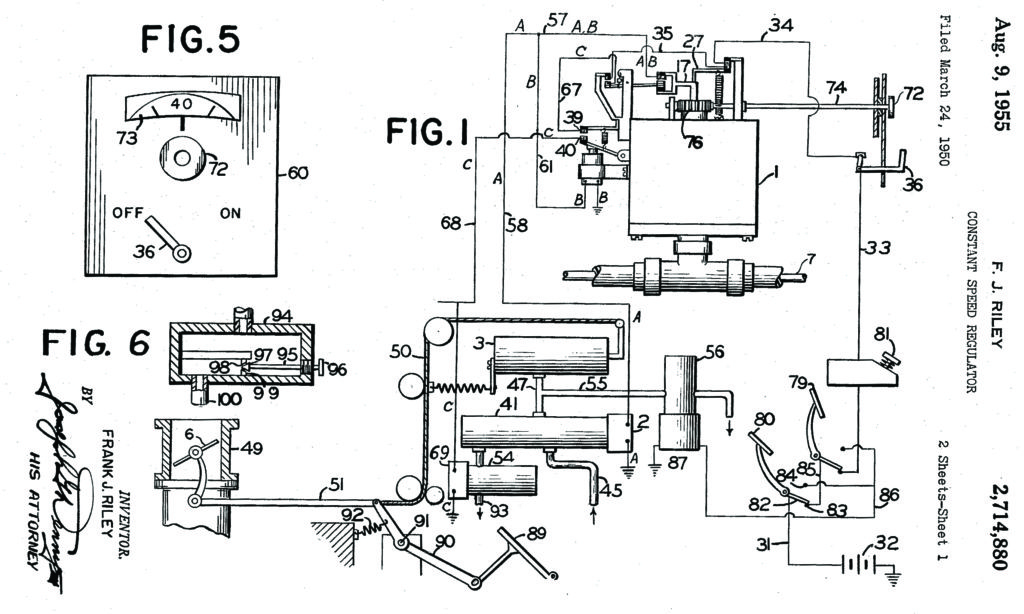
Figure 1: Cruise control was the first integration of electrical and mechanical systems in a vehicle. Early systems used fluid pressure to activate the throttle and were governed by solenoids (U. S. Patent No. 2,714,880, 1955).
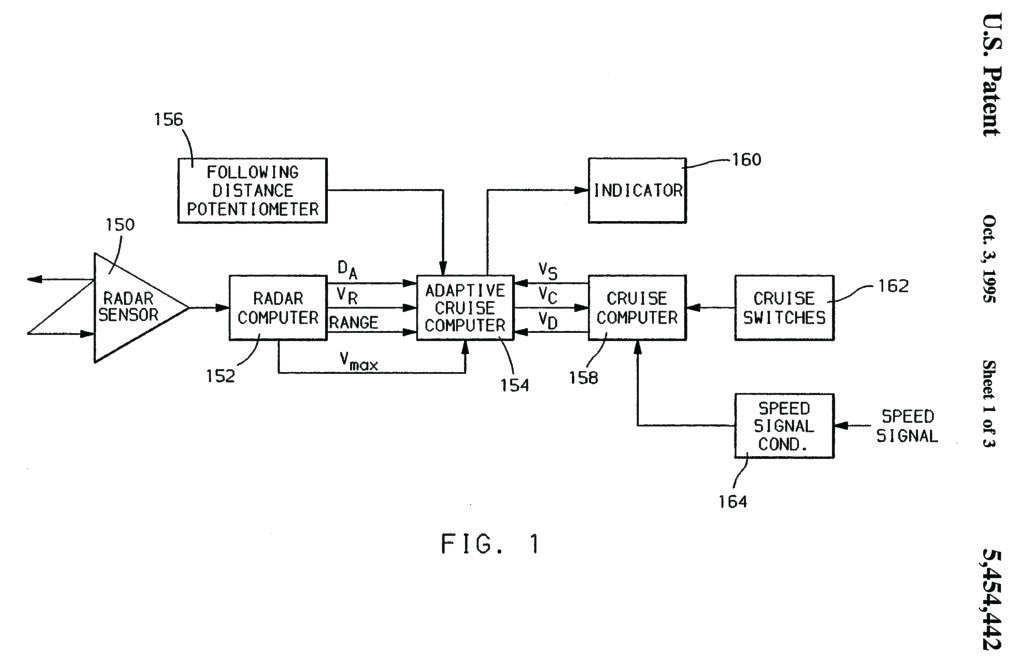
The result of this innovation and integration is a tremendously complex system of electronic control units (ECUs), sensors, actuators, and wiring to connect it all together. The size and complexity of these architectures create new challenges for automotive original equipment manufacturers (OEMs) and their suppliers. These challenges will only become more intense as companies continue to advance vehicle technologies, particularly in the automated driving space. In this environment, the importance of the underlying E/E architecture is paramount.
The challenges created by the evolution of the E/E architecture are not confined to vehicle design and engineering. Major OEMs and suppliers alike are realizing that changes to their organizations and business models will lay the foundation for future success. OEMs are investing in increasing their software competency to bring the development of vehicle software in-house. This is changing OEM-supplier relationships, as automakers begin to source only hardware from their supplier networks.
In response, long-time automotive suppliers are expanding the services they offer to cover the full range of component development, from design through manufacturing. These suppliers, known as Tier 1 suppliers, are caught between legacy challenges like production efficiency and product quality, and emerging challenges such as ballooning harness complexity, accelerated development cycles, and the need to develop new technologies to stay ahead of competition. Moving forward, Tier 1 suppliers will need to move upstream in the value chain to offer full wiring harness and electrical distribution system design and integration services.
Between large-scale technological changes and the resulting shifts in industry dynamics, manufacturers and suppliers face a challenging road ahead.
Consumers want increased freedom to customize their vehicles through optional features without paying a premium price. OEMs are attempting to provide this customization on a mass scale, as their business still relies on making and selling large volumes of vehicles. In contrast, OEMs simultaneously try to re-use bills-of-materials (BOM) as much as possible across vehicle platforms to reduce costs in design and manufacturing. Thus, it becomes more challenging to track and coordinate among thousands of common and unique components, such as the correct version of an ECU or software build, as well as corresponding connectors and terminals across the vehicle platform, all of which are needed to enable functional connectivity between devices.
Second, the typical automotive supply chain is growing longer and larger due to the increasing E/E content in vehicles. Longer and larger supplier pipelines can greatly increase the time required to cascade and implement design changes. Ensuring that all teams understand the change being implemented and its effects on their domain is already a key challenge. Contracting with additional suppliers and expanding the supplier ecosystem to provide desirable features only compounds this problem.
Third, the average new car today contains between 70-100 ECUs. In future vehicles, OEMs will consolidate these into fewer more powerful control units. How far this consolidation should go; however, is a point of major debate. Some advocate for a centralized architecture with a few, or a singular, very powerful ECU(s) managing vehicle functions. Others consider a distributed architecture with a greater number of ECUs a better option, primarily to create redundancy in vehicle systems.
In each case, OEMs will look to limit investments to save on cost, but increasing architectural complexity and more stringent safety requirements increase the challenge of vehicle design. This increased challenge equates to greater cost, as investment is necessary to deliver the sophisticated vehicles demanded by the market. As OEMs and suppliers look to innovate via the E/E architecture, they will need to evolve their development processes to integrate across domains, automate design tasks, and provide robust data coherency in order to tackle the challenges that come with technological and organizational change.
Indeed, the challenge only grows as companies move to scale and creating profit from a new technology once it has been validated. Capitalizing on the vast opportunity of advanced vehicle technologies requires comprehensive digitalization throughout an automotive company, connecting IT, engineering, and manufacturing with a single digital thread. The digitalization strategy must also support agility and collaboration across the OEM-supplier ecosystem.
Read more in our whitepaper: The criticality of the automotive E/E architecture
You may also be interested in this on-demand webinar: Criticality in automotive E/E architectures