Generative design solves automotive E/E systems design challenges
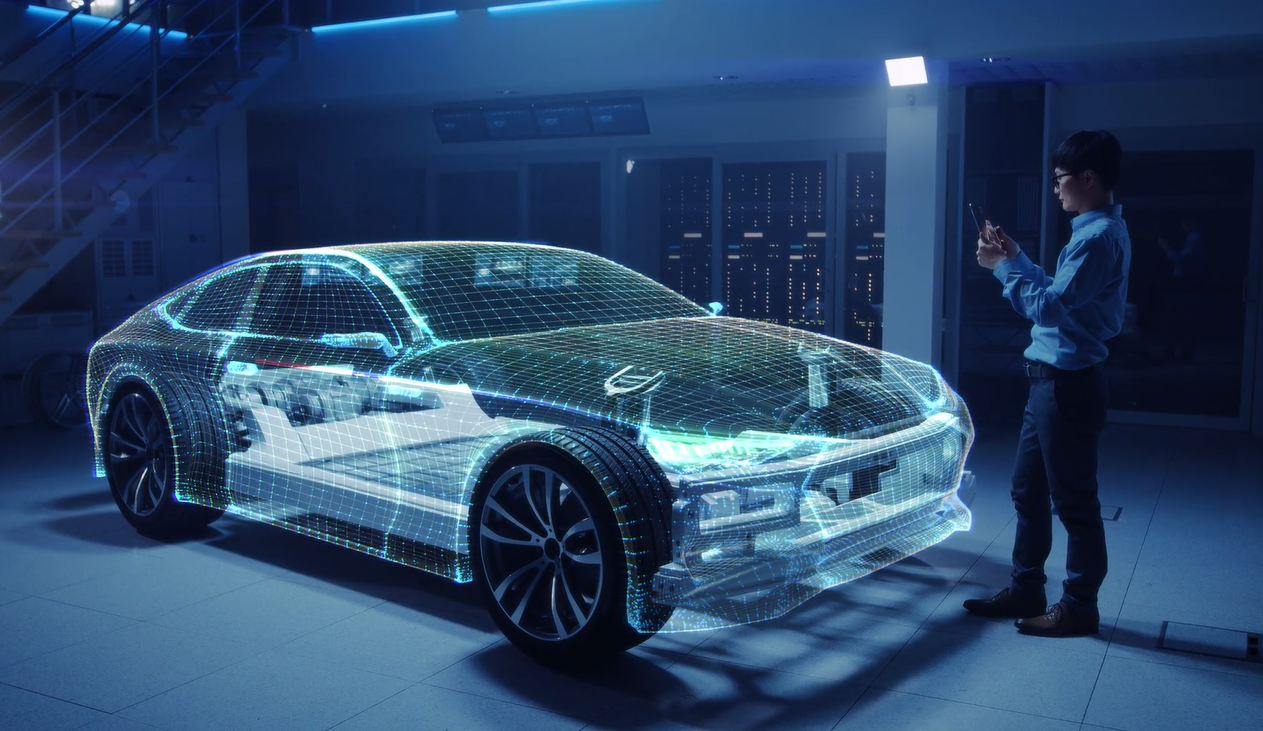
Automakers are integrating more electrical and electronic (E/E) content into their vehicle platforms to enable a wider array of electrically enabled features. The resulting increase in automotive design complexity demands a shift away from legacy automotive design flows that heavily rely on manual design work, data exchange, and requirements tracking.
Generative design will be a key enabler for new and established automotive companies as they develop next-generation vehicle platforms. The ability to generate electrical system architectures automatically enables teams to manage complexity and perform early design exploration and optimization while baking company IP into the design flow. Additionally, generative design creates a singular source of data that promotes consistency between domains, design reuse, and enhances the analysis of change impact.
In part one, we examined new challenges in vehicle E/E systems design and briefly described how a generative design flow provides a solution. In part two, we will more closely examine the capabilities of generative design and best practices for its implementation. These include automation, engineering within a platform context, cross-domain integration, and data re-use.
Automation
Automation in generative electrical system design combines simple system connectivity with the physical harness topology in such a way that it can synthesize the thousands of wires and splices that implement the electrical distribution system (figure 1). Such automation helps engineers to manage the immense volume of data created during design, and reduces errors by removing manual data entry and other error-prone tasks.
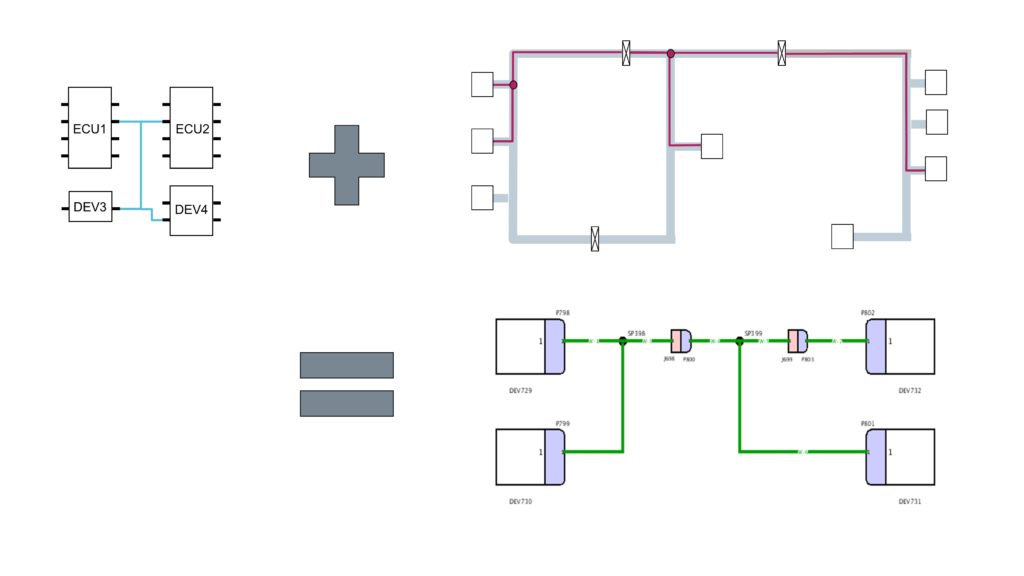
Advanced wiring synthesis solutions support complex wiring types, multiple shielding materials, and various network protocols. With robust design rules, wiring synthesis can generate designs that implement multicore cabling and appropriate shielding to protect the wiring as needed. In other areas of the harness, wiring synthesis will optimize the use of wiring and shielding types to reduce cost while ensuring proper functionality.
Wiring synthesis also generates wiring that correctly supports every buildable vehicle configuration. Each wiring harness must be able to support a variety of optional features that consumers may choose, and the millions of harness configurations that result from such feature choice. The automated wiring synthesis can generate wiring for all these buildable vehicle configurations, ensuring as much common wiring between configurations as possible to minimize cost.
The platform context
As engineers employ generative design to generate and optimize vehicle systems, they must be able to assess these system designs in the context of the entire vehicle platform. Vehicle system complexity affects all facets of the vehicle design. The vast interrelations between subsystems within the vehicle also means that design work in any system or sub-system may have effects elsewhere in the architecture. Designing in the context of the overall vehicle platform promotes accuracy in the design and supports comprehensive validation that can prevent costly recalls.
The platform context also has benefits for understanding the cost impact of architectural decisions across the vehicle. Platform changes can have effects that manifest across the entire vehicle. These effects, in turn, affect the cost of the design as wiring properties, sensor type, or the number of ECUs required could all change. The cost implications must be captured and measured. With this data, engineering teams can compare and assess design alternatives to arrive at optimal solutions.
Cross-domain Integration
Automated wiring synthesis, cost analysis, and other capabilities within the platform context can’t exist in isolation – they must form part of an overall flow (figure 2).
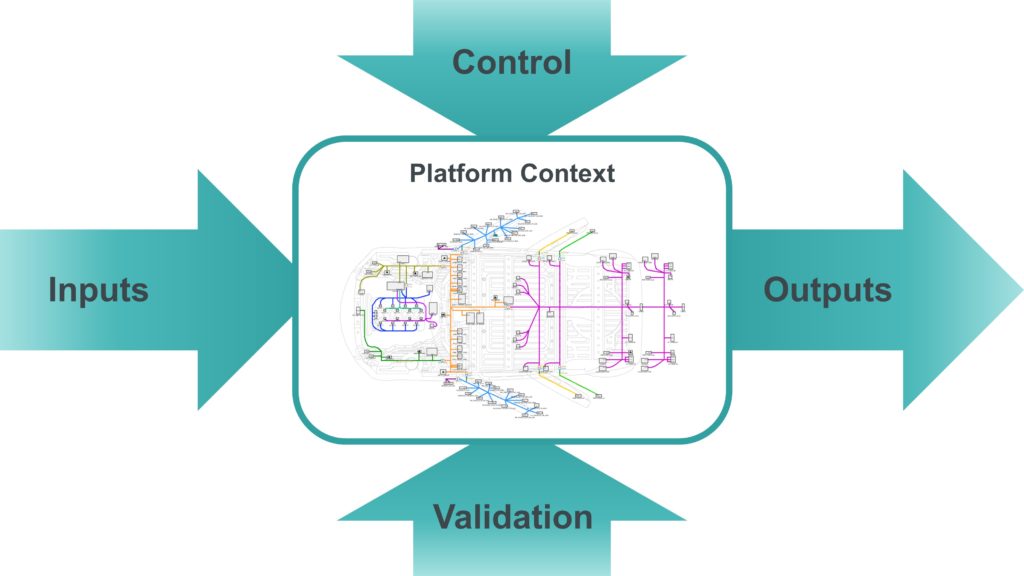
Data inputs are needed to drive the automated synthesis process that generates outputs, such as wiring and architectural designs, to feed into downstream tools and processes. The data comes from design domains that are undergoing change. The automated synthesis must take this data and generate outputs that comply with the design requirements and any relevant standards. At this stage, the team can employ their existing knowledge and expertise to assess and validate the correctness of the design. Then, control can be exerted over the automated process to enhance its accuracy.
Changes come into the synthesis solution from various inputs including the bundle topology, logical system design, marketing requirements, and device interface properties. Wiring synthesis must combine these inputs to generate outputs in the form of synthesized wiring designs. Tight integrations with the entire E/E and vehicle engineering flow allows engineering teams to use the synthesized data, including wiring diagrams, in downstream processes such as manufacturing design and the creation of service documentation.
The whole process is driven by re-usable and configurable rules. These control every aspect of the automation and ensure compliance with marketing, manufacturing and certification requirements. The engineering teams can also use configurable metrics to measure and assess designs, providing insight into the impact of changes or alternative implementations.
Reusable Design Data
Finally, generative design supports extensive design data reuse. To reduce cycle-time and development costs, engineering teams should re-use as much validated data as possible. Integrating existing designs into the platform context reduces the volume of work by eliminating the need to design new systems or sub-systems to serve a given function. Reuse also removes the need to verify the functionality of a new design.
Therefore, once a system design is validated and released, the design must be captured and made re-usable across multiple platforms without the need for platform-driven changes. In addition to designs, it is important that settings, requirements, and other process controls are re-usable and transferrable across domains and designs. Highly automated processes need sophisticated controls to ensure repeatable results that meet business standards and needs. These controls can be created by capturing the expertise of engineers into instructions or constraints that force or restrict the behaviour of automated design systems.
Summary
Change in the automotive industry is only accelerating. Growing automotive complexity, tight budgets, and frequent design change combine to make automotive E/E systems design incredibly challenging. Engineering teams need a new design methodology to cope with the pressures inherent in modern automotive design.
Design automation, a holistic platform context, and seamless integration between design tools are essential to empowering engineering teams to design accurate, optimized designs under budget and on schedule. In addition, this new design methodology equips engineers to manage the staggering complexity of modern E/E systems. With a generative design flow, teams can ensure that the design supports all possible vehicle configurations, integrate new systems without additional workers, manage dozens of multi-domain change orders, and optimize the entire system for functionality and profitability.
Read more in our paper: Keys to generative design