Elektromagnetische Simulationen als Teil Ihres Konstruktionsprozesses, das ist „EMAG-nificent“
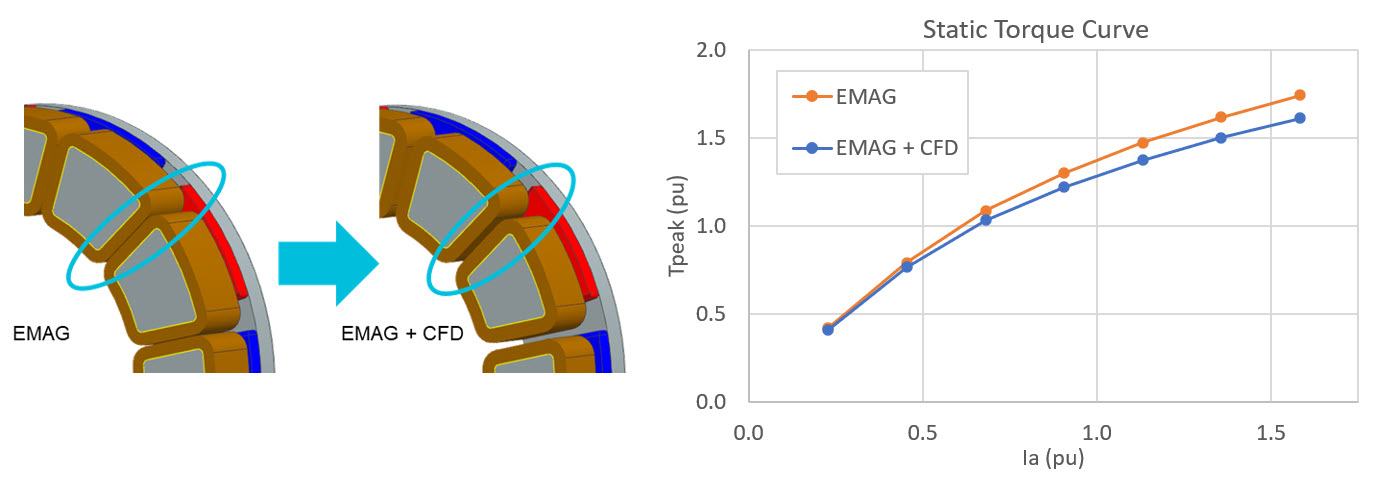
Ingenieure für Elektromagnetik (EMAG) und Elektrotechnik sind mit den schlanken EMAG-CAE-Paketen (Computer Aided Engineering) wie Simcenter SPEED, Simcenter Motorsolve und Simcenter MAGNET vertraut. Unsere Kollegen aus dem Bereich Functional Computer-Aided Design (CAD) generieren für uns eine feature-befreite Geometrie, die nur aus aktiven EMAG-Teilen besteht. Wenn wir auf CAD-Probleme stoßen, wie z. B. das Extrahieren der Geometrie aus einer Baugruppe oder Vernetzungsfehler, geben wir die Konstruktion automatisch an die CAD-Konstrukteure zurück, und die Uhr beginnt zu ticken.
Können wir so weitermachen?
Mit dem Wettlauf um die Elektrifizierung besteht ein Bedarf an mehr Zusammenarbeit zwischen verschiedenen Teams. Produktkonstrukteure verleihen dem Produkt „Aussehen und Haptik“ – seine äußere Gestalt. CAD-Konstrukteure vertreiben Immobilien. Die CAE-Konstrukteure arbeiten dann innerhalb der Randbedingungen, um die nötige Physik zur Produktoptimierung einzubinden.
Es wird als selbstverständlich erachtet, Zeit für Teamkommunikation und -abstimmung aufzuwenden. „So läuft das eben in großen Unternehmen“ ist eine gängige Klage. Suboptimale Abläufe waren vielleicht akzeptabel, als elektromagnetische Bauteile nur Zusatzkomponenten Ihres Produkts waren. Heutzutage ist jedoch ein elektrischer Antrieb das Herzstück vieler Produkte, und die Verschwendung von Zeit in Iterationen mit anderen Abteilungen kann Ihre Entwicklungszyklen verdoppeln und die F&E-Kosten in die Höhe treiben. Zudem machen der starke Wettbewerb und der Mangel an Konstrukteuren es unhaltbar, Zeit mit sinnlosen Wiederholungen zu vergeuden.
Was ist mit vorgelagerten CAD-Änderungen, die sich auf die EMAG-Bauteile auswirken?
Es ist nicht ungewöhnlich, dass ein EMAG-Konstrukteur, der am E-Antriebsstrang arbeitet, eine detaillierte CAD-neutrale Datei erhält. Häufig sind diese Dateien, trotz Gehäuse und Getriebe, nicht-assoziativ (die Bedeutung davon erläutern wir später). Die Dateien enthalten keinen Rotor, Statorkern oder keines von beiden und dienen bei CAE eher der Visualisierung als der Funktionalität. Das löst einen Pingpong-Effekt zwischen EMAG- und CAD-Teams aus, die nun die Geometrie bereinigen und vereinfachen sowie die Materialien überprüfen müssen. Erst nach dieser Bereinigung kann ein Elektromagnetik-Konstrukteur mit der eigentlichen Arbeit beginnen: der Konzeptsuche und Validierung der vorgeschlagenen Konstruktion.
Aufgrund steigender Zinsen und Kosten stehen Projektmanager im E-Fahrzeugsektor seit 2018 unter zunehmendem Druck, Auslieferungstermine einzuhalten – bei drohenden Mehrkosten ohne Gegenmaßnahmen. Daher werden Sie Ihr Team vermutlich bitten, Komponenten in Gewicht und Größe zu optimieren. Als EMAG-Konstrukteur werden Sie Wege finden, die CAD-Konstrukteure zeitlich herauszufordern. Keine Sorge; du bist damit nicht allein. CAD-Konstrukteure müssen neue CAD-Updates berücksichtigen und CAE-Teams bei der Geometrie-Aktualisierung unterstützen. Wie Sie sich denken können, sind Mails, Anrufe und Meetings dafür zahlreich, mit enormen Auswirkungen auf die Markteinführungszeit.
Wie lässt sich Zeit einsparen?
Ein System, das dem Elektromagnetiker erlaubt, seine Modelle mit minimalem Aufwand des Konstrukteurs automatisch auf den aktuellen CAD-Stand zu bringen, steigert die Produktivität. Ein Beispiel für einen möglichen Prozess sehen Sie in diesem kurzen Video. Das Video zeigt, wie eine extrahierte 2D-E-Motorgeometrie aus einer Fahrzeugbaugruppe aufgrund von vorgelagerten Änderungen des Statoraußendurchmessers aktualisiert werden kann.
Das Video beginnt mit dem Fokus auf den elektrischen Antriebsstrang und isoliert nach und nach den Elektromotor vom Rest der Baugruppe. Weiter erfassen wir nicht nur die elektromagnetisch aktiven Körper, sondern verbinden sie auch mit der Baugruppe. Dann fügen wir alle für die Simulation erforderlichen Elemente hinzu: Luft- und Neuvernetzungsbereiche, 2D-Rotorgeometrien sowie das Finite-Elemente-Netz für eine vollständige Darstellung. Abschließend initiieren wir eine Anpassung des Statoraußendurchmessers, deren Auswirkungen im aktualisierten Netz ersichtlich sind. Die CAD-Schnittstelle der Simcenter-Umgebung erlaubt Ihnen, sich voll auf Ihre Kernaufgabe zu konzentrieren – die elektromagnetische Analyse.
Betrachten wir nun den globalen Trend zu Leichtbau und E-Antriebsintegration. Es gilt, Lärm zu reduzieren und Wärme bei stetig kleineren Elektromotoren abzuleiten. Diese benötigen eine komplexere Flüssigkühlung und Konstruktionen zum Schutz vor abfliegenden Magneten, was die elektromagnetische Struktur verändert.
Wie aktualisiert man das EM-Modell mit multiphysikalisch bedingten Geometrieänderungen?
In einem herkömmlichen Workflow müssten die von anderen Gruppen vorgenommenen, nicht zugeordneten Modellaktualisierungen den EMAG-Konstrukteur dazu zwingen, den Abstimmungsprozess mit dem Konstruktionsteam samt aller damit verbundenen E-Mails und Anrufe zu wiederholen. Sie fühlen sich verlegen ohne Assoziativität! Zudem verschärft sich das Problem mit steigender Anzahl berücksichtigter physikalischer Domänen.
E-Antriebsstränge durchlaufen zahlreiche Multiphysik-Simulationen, bevor die Konstrukteure eine endgültige Konstruktion festlegen. Diese horizontalen Änderungen werden wechselseitig durch elektromagnetische, thermische und strukturelle Analysen sowie NVH-Untersuchungen beeinflusst. Mit Konstrukteuren aus allen Abteilungen, die simultan an einem nicht-assoziativen Tool arbeiten, ist die Gefahr beachtlich hoch, dass ein Konstrukteur an einer veralteten Version statt der aktuell besten Konstruktion arbeitet.
Wie verfolgen Sie Änderungen an der CAE-Geometrie?
Zum Glück gibt es einen Anhaltspunkt – wenn auch unauffällig in abgeschotteter Umgebung. Das Konstruktions-CAD bildet die einzige Brücke zwischen Physik und Produktanforderungen wie Kosten, die an Volumen und Masse gekoppelt sind. Wie Abbildung 2 zeigt, ermöglicht ein nahtlos aktualisiertes Konstruktions-CAD allen CAD- und CAE-Konstrukteuren den gleichzeitigen Zugriff auf dieselbe Geometrie. Natürlich erfolgen Aktualisierung und Zugriff in einer kontrollierten Umgebung. Das verhindert überholte Ergebnisse in Ihren Projektmeetings. Bei der Elektromagnetik bildet die Geometrie die jüngst genehmigten Upstream- und Horizontaländerungen ab.

In Abbildung 3 sehen wir beispielsweise die Entwicklung der EMAG-Statorteile von einer effizienten Konstruktion, die allein auf elektromagnetischer Leistung basiert, hin zu einer, die Kühlkanäle an den Spulen berücksichtigt. Wir beobachten ein vermindertes Drehmoment aufgrund des nun begrenzten Volumens. Das liegt daran, dass die erste Konstruktion mehr Stahl enthält und daher mehr magnetischen Fluss transportieren kann.
Wie im Video erkennbar, lassen sich die aktiven Komponenten des Elektromagneten mit der CAD-Konstruktion in Verbindung bringen. Nach einer Parameterstudie zur Ermittlung der optimalen Kanalbreite wurde diese geometrische Anpassung in die CAD-Konstruktion integriert. Und dank der assoziativen Geometrie für die EM-Simulation musste lediglich die Berechnung mit den Änderungen neu durchgeführt werden

Was bedeutet das wirklich?
- In einem Multiphysik-Konstruktionsprozess, wie er für eine E-Maschine nötig ist, kann ein optimierter Workflow Hunderte Konstrukteursstunden einsparen. Sie investieren nur einmal in die Ersteinrichtung! Der Rest ist lediglich die Weiterentwicklung der Konstruktion, basierend auf Produktanforderungen und physikalischen Änderungen.
- Der zugehörige Workflow ermöglicht es uns, isolierte Arbeitsweisen und die Fokussierung auf einzelne physikalische Aspekte bei der Entwicklung zu überwinden. Ein effizientes elektromagnetisches Gerät kann statisch instabil oder gar nicht produzierbar sein. Durch die Erfassung des Möglichen mittels geometrischer Randbedingungen und physikalischer Wechselwirkungen erreichen wir eine realistischere Konstruktion. Gleichzeitig hilft es uns, eigene physikalische Voreingenommenheit zu kontrollieren und gemeinsam eine ausgewogene Leistung anzustreben. Was wir für unsere Physik als passend erachten, ist nicht zwangsläufig förderlich für die Gesamtproduktperformance. Ein integrierter Konstruktionsprozess ermöglicht schnellere Iterationen und rascheres Zusammenführen der Ergebnisse!
Zusammengefasst verkürzt der hier beschriebene Prozess die Entwicklungszeit und ermöglicht eine schnellere Produktrealisierung. Dieser Prozess hilft Konstrukteuren, sich schneller auf ein Konzept zu einigen, indem alle am aktuellsten Modell arbeiten. Dabei wird verhindert, dass Nachteile wie Vorurteile zu bestimmten Physikmodellen oder Teamisolation entstehen. Konstruieren Sie Ihren nächsten E-Motor schneller, besser und kostengünstiger hinsichtlich der Entwicklungszeit.
Verwandte Ressourcen
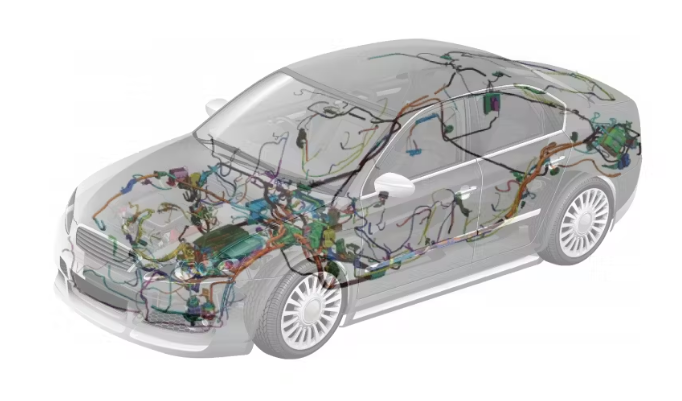
Webinar
Erreichen der EMV-Konformität für elektrifizierte Fahrzeuge durch elektromagnetische Simulation
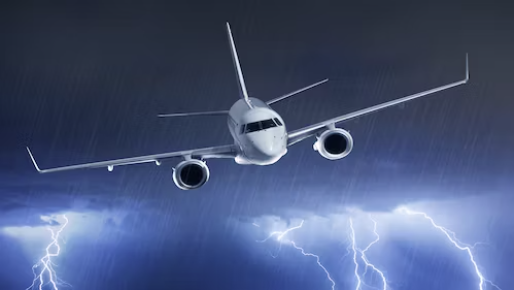
White Paper
Elektromagnetische Verträglichkeit von Flugzeugen
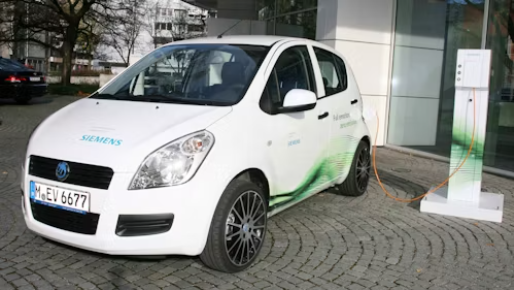
White Paper
EMC/EMI und thermische Herausforderungen bei der Entwicklung von Elektrofahrzeugen
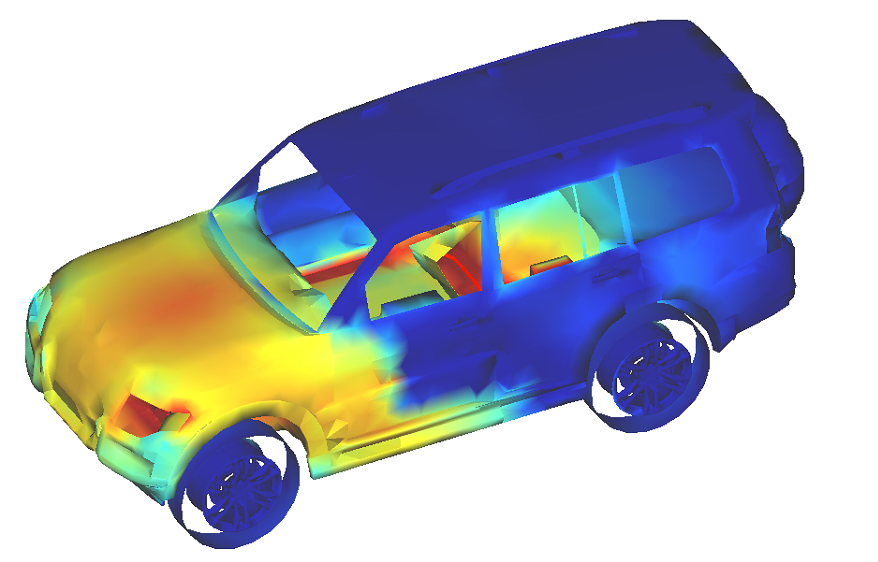
Blog
Das Unsichtbare sichtbar machen: Simulation der elektromagnetischen Leistung