4 Schritte zur Vorhersage von Fahrgeräuschen – ein Projekt mit der Hyundai Motor Group

Ohne Überlagerung durch Geräusche eines Verbrennungsmotors sind die Fahrgeräusche in Elektrofahrzeugen (EV) deutlicher wahrnehmbar und haben sich zur dominierenden Geräuschquelle für Fahrer und Insassen entwickelt. Fahrgeräusche sind in fast allen Fahrbedingungen vorhanden. Die Vorhersage von Fahrgeräuschen ist jedoch bekanntermaßen schwierig und hat sich zu einem der kritischen Themen entwickelt, mit denen sich Ingenieure bei der Entwicklung von Elektrofahrzeugen auseinandersetzen.
„Wie also lassen sich Fahrgeräusche unter verschiedensten Fahrbedingungen und Fahrzeugvarianten zu jedem Zeitpunkt der Entwicklung zuverlässig beurteilen?“
Diese Frage hat sich ein Forschungsteam der Hyundai Motor Group (HMG) gestellt. HMG ist für seine Pionierarbeit in der Automobiltechnik anerkannt und verfügt über eine solide Expertise im Bereich Fahrgeräusche, die es aber weiter ausbauen wollte.
Die HMG-Ingenieure hatten bereits damit begonnen, zu erforschen, wie Test- und Simulationstechnologien kombiniert werden können, um einen zuverlässigeren digitalen Zwilling zu schaffen. Insbesondere wollten sie ein Federungsmodell charakterisieren und konzentrierten sich daher auf die Erstellung von Testmodellen, die mit Simulationsmodellen kompatibel sind. Dabei stießen sie jedoch auf erhebliche Hindernisse.

Schritt 1: Die Grenzen der einzelnen Subsysteme verstehen
Wie Automobilkonstrukteure wissen, stellt die Messung des Beitrags einzelner Komponenten zu den Fahrgeräuschen eine Herausforderung dar. Ist das Rad, das Fahrwerk oder die Karosserie hauptsächlich für das Geräusch verantwortlich? Die erste Herausforderung bestand darin, die betrieblichen Randbedingungen jedes Subsystems als Teil einer größeren Baugruppe zu verstehen. Wir haben die Strukturprüfung in einem Free-Free-Setup durchgeführt. Es ist nicht einfach, eine korrekte Darstellung zu erhalten, da sich Subsysteme gegenseitig beeinflussen.
Hier bei Simcenter Engineering and Consulting Services sind wir bestrebt, unseren Kunden dabei zu helfen, ihre technologischen und geschäftlichen Ziele zu erreichen, indem wir komplexe Probleme lösen. Unsere Arbeit ist interessant, weil wir mit Hardware, Software und Menschen arbeiten und die Fähigkeiten und Ressourcen einsetzen, die zur Erfüllung eines Auftrags erforderlich sind. Logischerweise waren wir sehr daran interessiert, zu helfen, als Sangyoung Park, Senior Research Engineer bei HMG, anfragte, ob wir mit seinem Team zusammenarbeiten könnten.
Schritt 2: Aufhängung trennen
Wir begannen damit, uns auf die Beziehung zwischen dem Reifen (als Geräuschquelle) und der Karosserie zu konzentrieren, einschließlich der Aufhängung als Empfänger. Wir verwendeten die bauteilbasierte Transferpfadanalyse (bauteilbasierte TPA), um die Art der einzelnen Teilbereiche zu verstehen und die Belastung abzuschätzen. Wir haben diesen Ansatz der Schätzung unabhängiger Reifenlasten validiert, als die HMG-Konstrukteure bestätigten, dass die Verwendung dieser Lasten und der Reifendarstellung in einem anderen Auto ein genaues Fahrgeräusch vorhersagte.

Lesen Sie dieses White Paper, um mehr über die bauteilbasierte TPA-Methodik zu erfahren.
Mit Vertrauen in unsere Arbeit haben wir frequenzbasierte Substrukturierung (FBS) verwendet, um den Beitrag der Fahrzeugkarosserie, der Aufhängung und der Räder zu verstehen. Da es sich bei der Aufhängung um eine Kette verschiedener Bauteile unter einer bestimmten Vorspannung handelt, kann sie im freien Zustand nicht ohne weiteres gemessen werden. Stattdessen haben wir die neue Technik der FBS-Entkopplung verwendet, um das Schwingungsverhalten eines Bauteils zu charakterisieren, indem wir den Einfluss einer Stützstruktur oder eines Prüfstands beseitigen.

Im vergangenen Juni haben wir auf dem ISNVH-Kongress in Graz gemeinsam mit HMG einen Vortrag über die erste testbasierte Identifizierung einer Aufhängung einschließlich Vorspannung und Betriebsnichtlinearitäten vorgestellt. Folgen Sie diesem Link, um das technische Dokument zu lesen: FBS-Entkopplung auf Federungsebene für Fahrgeräuschanwendungen.
Schritt 3: Entwerfen, Bauen und Validieren des Prüfstands
Um die Technik der FBS-Entkopplung anzuwenden, arbeiteten wir an der Konstruktion, dem Bau und der Validierung eines kundenspezifischen Prüfstands, um das Aufhängungsmodell zu bewerten. Diese Bank musste so konzipiert werden, dass sie später von den HMG-Ingenieuren im eigenen Haus verwendet werden konnte, so dass an den Schnittstellen verschiedene Aufhängungen montiert werden konnten.
Unsere beiden Teams haben außergewöhnlich eng zusammengearbeitet. Das Engineering-Service-Team in Leuven, Belgien, erstellte CAD-Dateien, um Sensor- und Anregungsstandorte vorzuschlagen, die sie an HMG in Südkorea schickten. Dort verwendeten Testingenieure diese CAD-Modelle, um Instrumentierung herzustellen, die erforderlichen Übertragungsfunktionen zu messen und Belgien zur weiteren Validierung Rückmeldung zu geben.
Nachdem wir den idealen Testaufbau, die Positionierung der Sensoren und die Sicherstellung der Zugänglichkeit identifiziert hatten, verwendeten wir die Vorrichtung, um ein repräsentatives Modell der integrierten Vorderradaufhängung mit den richtigen Randbedingungen und unter der richtigen Vorspannung zu testen.

Wir haben das Verhalten der gesamten Baugruppe gemessen. Und als nächstes entfernte ich die Federung physisch aus der Gesamtsumme und maß nur die Bank neu. Durch einen intensiven Iterationsprozess haben wir die Ergebnisse nach und nach validiert. Wir erstellten ein virtuelles Modell der Aufhängung, das auf tatsächlichen Testdaten basierte, die durch Subtraktion der reinen Prüfstandsmessungen von der gesamten Baugruppe generiert wurden.
Schritt 4: Vorhersage der Leistung von NVH-Systemen
Der nächste Schritt im Prozess bestand darin, alle Komponenten zu kombinieren und die Reifenlasten auf die gesamte Fahrzeugbaugruppe oder den digitalen Zwilling aufzutragen, um das Fahrgeräusch zu hören und zu validieren.
Wenn Sie ein virtuelles Modell haben, das aus realen Messungen abgeleitet wurde, wissen Sie, dass es zuverlässig ist, und können es sich anhören. Wenn Ihnen das, was Sie hören, nicht gefällt, können Sie es ändern und erneut anhören. Sie können Ziele festlegen und Entscheidungen über den optimalen Klang treffen, die auf dem Beitrag der einzelnen Komponenten basieren. Für Konstrukteure bedeutet das deutlich mehr Flexibilität.

Der Prüfstand wurde an die HMG für den Einsatz vor Ort geliefert, um eine detaillierte Analyse des untersuchten Fahrwerks, die Messung anderer Fahrwerke, den Austausch von Fahrwerkskomponenten oder -lagern, Modifikationen usw. und die Untersuchung ihrer Auswirkungen auf das Fahrgeräusch zu ermöglichen. Dies ist ein Schritt nach vorn in der Fähigkeit des Unternehmens, die NVH-Leistung von Fahrzeugen virtuell vorherzusagen und zu einer modellbasierten virtuellen Fahrzeugentwicklung überzugehen.
In diesem Blog zur NVH-Vorhersage bei Fahrzeugen finden Sie weitere Informationen darüber, wie Sie die NVH-Leistung mit einem virtuellen Prototyp meistern können.
Teamwork macht den Traum wahr
Dieses mehrphasige Projekt hatte hohe Anforderungen und Erwartungen. Auf der einen Seite haben wir uns bei diesem Projekt um Innovation bemüht, während es eine außergewöhnliche Zusammenarbeit zwischen den Ingenieuren von Siemens und HMG gab. Wir glauben, dass dies die erste kommerzielle Anwendung des FBS-Entkopplungsansatzes ist, und wir sind alle stolz auf die ausgeklügelte Testvorrichtung, die wir produziert haben.
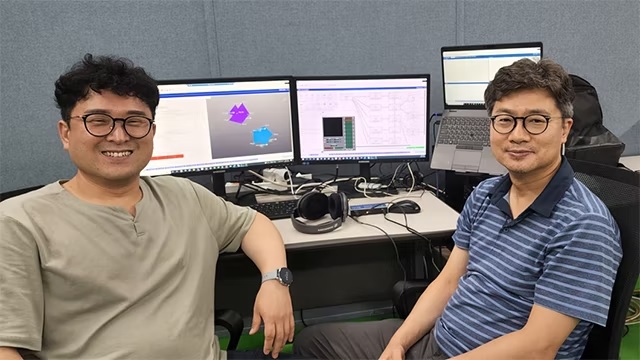
Die beiden Teams setzen ihre Zusammenarbeit fort. Unser Augenmerk liegt nun auf der Erstellung einer Datenbank mit Testergebnissen verschiedener Reifen und Aufhängungen, damit die HMG-Konstrukteure Ziele und Parameter eingeben, Optionen auswählen und einfach umschalten können, bis sie die optimale Kombination für das Fahrgeräusch gefunden haben.
In dieser Infografik erfahren Sie mehr über die Herausforderungen des Straßenlärms von Elektrofahrzeugen und wie Sie die Simulations- und Testlösungen von Simcenter nutzen können.
Vorhersage der Fahrgeräusche von Elektrofahrzeugen

Am 30. November ist Sangyoung Park Gastredner im Live-Webinar Fahrgeräuschvorhersage – ein MBSE-Ansatz für die virtuelle NVH-Entwicklung.
Er spricht dort über die Methoden, Ergebnisse und Errungenschaften des NVH-Fahrzeugmodellprojekts von HMG, die Zusammenarbeit mit Siemens und die Roadmap für die Verbesserung der Fahrgeräusche von Elektrofahrzeugen.
Ds Webinar befasst sich mit den Herausforderungen bei der Erstellung leistungsfähiger Fahrzeugmodelle erläutern und die Bauteile CAE- und testbasiert beschreiben. Zudem werden wir die Definition invarianter Lasten demonstrieren. Es wird erklärt, wie mit stark mit dem Fahrzeug gekoppelten Quellen, zum Beispiel den Reifen, umgegangen und modelliert wird. Es wird auch untersucht, mit welchen Tools eine Komponente oder ein Subsystem problemlos durch eine alternative Version ersetzt werden kann.
Interessante Links
- Anwenderbericht der Hyundai Motor Group – Modellbasiertes Systems Engineering für einen neuen Ansatz in der virtuellen NVH-Entwicklung
- White Paper: Fahrgeräusch-Engineering – Abschwächung der stärksten Geräuschquellen in Elektrofahrzeugen in einem frühen Entwicklungsprozess
- Anwenderbericht Renault – Fünffache Erweiterung der Anwendungen zur NVH-Vorhersage ohne physische Prototypen