Accelerate automotive product development with performance engineering simulation software
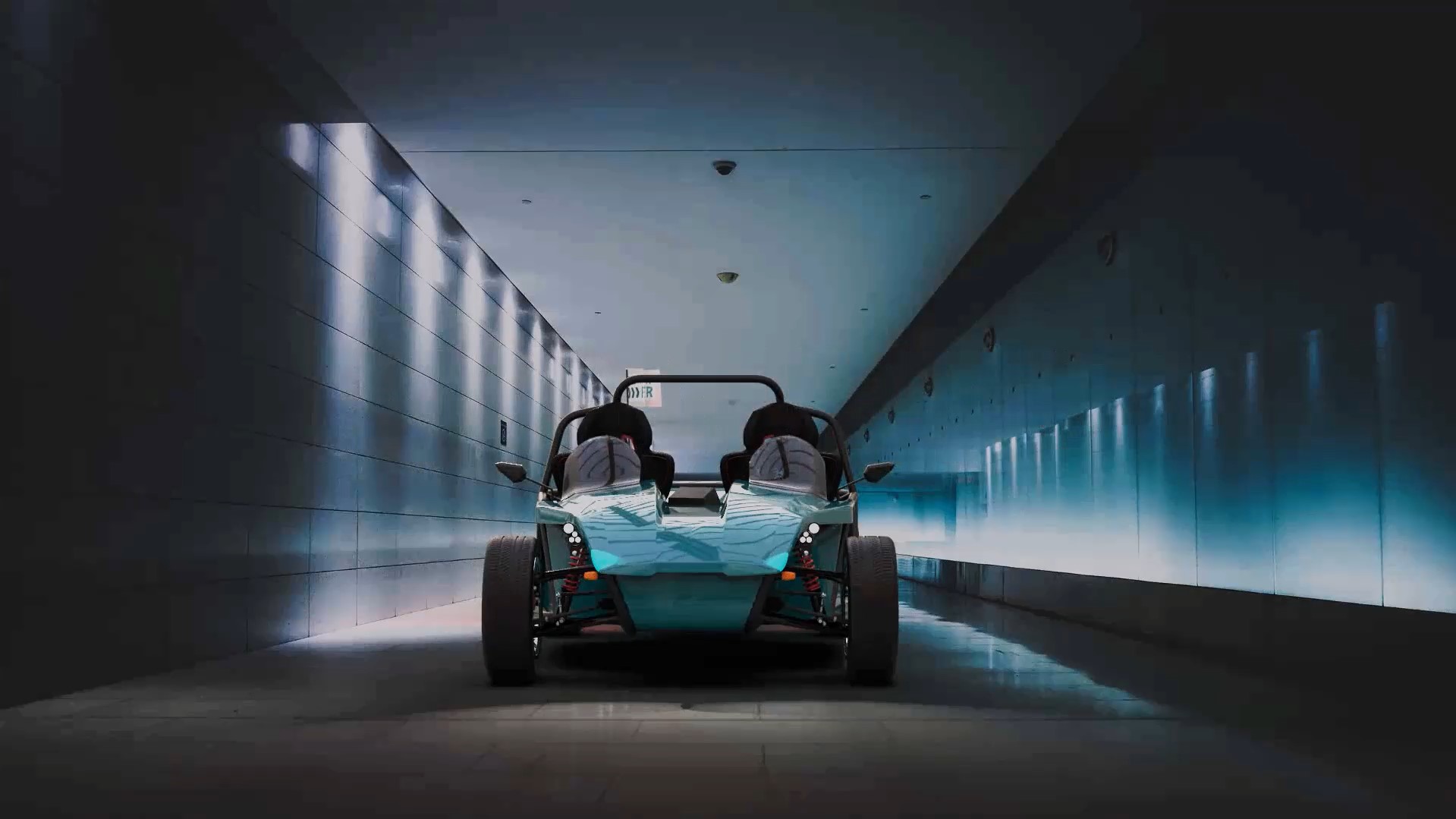
In the automotive industry, simulation and testing are key to building high-end and lightweight components. Now, instead of producing two or three models each year, many are looking to double this rate or more. Keeping up with an increased production schedule while maintaining profitability is a serious challenge, and simply cutting costs isn’t enough. Automotive manufacturers and suppliers need to streamline their development processes so they can improve vehicle performance and reduce development times.
Watch the videos below to learn how integrating Siemens powerful simulation capabilities with physical testing and correlation, as well as with the CAD application enables seamless development with full associativity.
Structural validation for automotive product development
- Generate associative CAE geometry model and simplify the geometry for simulation
- Build the model, apply boundary conditions and loads to simulate for deflection
- Add changes to the geometry to generate stiffer design
- Automatically update the simulation model, reevaluate and compare results
Benefits of structural validation for automotive product development:
- The simulation model is associatively attached to the CAD model and allows what-if studies through automatic updates of the simulation after a design change
- Simplified workflows and associative CAD/CAE models allow for rapid “what if” studies
- Reliable simulation results due to associative update after design changes
Design verification for automotive product development
- Easily replace a part in an assembly motion simulation with a new design and rerun
- Review and animate deflection and stress results with simplified templates
Benefits of design verification for automotive product development:
- Considering flexibility in the assembly gives a realistic representation of your product
- High quality digital twin results reduces the need for iterative physical prototype builds
CAD 2 CAE for automotive product development
- Generate an assembly CAE model of a vehicle substructure
- Utilize existing component meshes that are automatically positioned
- Easily develop bolt connections with automated universal connection technology
- Add lumped mass representation of the gearbox
- Run modal analysis and review animations of natural frequency modes
Benefits of CAD 2 CAE for automotive product development:
- Reusing existing CAE models speeds up the simulation setup and leads to high quality results
- Universal connections technology provides a simplified and automated method to define bolts, welds, and many other fasteners quickly
Physical testing and correlation analysis for automotive product development
- Visualize the deformation of the gearbox housing at resonance
- Perform a correlation analysis in the next step to compare with simulation results
- Import the test results from Testlab into Simcenter 3D
- Correlate the modal analysis and validate with the simulation model
Benefits of physical testing and correlation analysis for automotive product development:
- Builds the modal representation of the test results
- Generates the wireframe models to visualize the mode shapes of the gearbox housing
- Effortlessly imports the test results into Simcenter 3D and verifies the validity of the simulation
Want to learn more about how seamless integration of simulation into the design process avoids time-consuming updates and lets you improve your design performance faster?