University of Tennessee – Innovative EcoCAR Team Enabled with Siemens Software (2022)
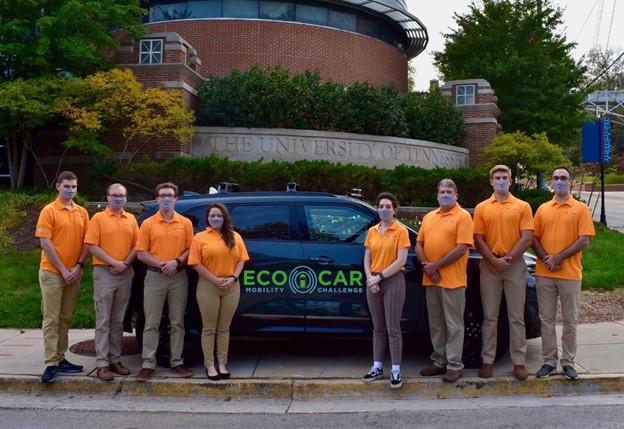
Written by: Lily Joy Crosby, (mentoring and minor edits by Leigh Anderson)
One of the best parts about EcoCAR was getting to work with our incredible sponsors. Working with them provides our team members the chance to use industry-best in class tools, giving our team members the training and skills needed to launch a stronger career in automotive engineering. We know that each of our EcoCAR sponsors was imperative to the work we accomplished as a team.
Our team won the Outstanding Communications Team & Sponsor Collaboration award for this article, earned 3rd place in Project Management and 2nd place in the Bosch Advanced Driver Assistance System (ADAS) Development Environment Award.
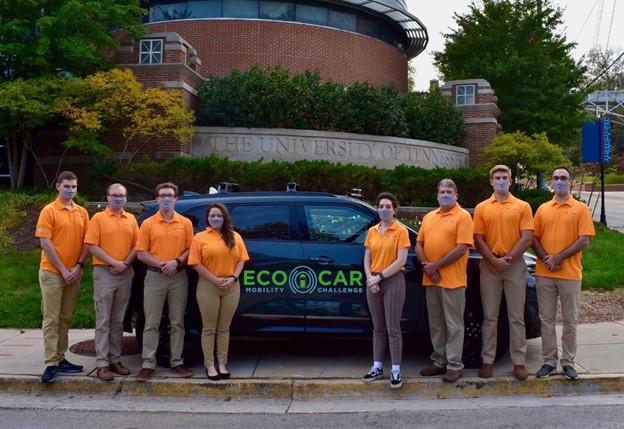
For the EcoCAR Communications mission, each team’s communications managers were partnered with one of the EcoCAR sponsors to highlight the partnering they do with the teams. Here at EcoCAR Team Tennessee, we partnered with Siemens. Throughout the collaboration, we worked with Siemens to write an article demonstrating the importance of our partnership and how Siemens’ generous resources helped us achieve success, (despite competing with teams having up to four times as many team members!)
The EcoCAR Mobility Challenge is a 4-year student competition (2018-2022), with a budget of over $25 million provided mostly by industry. EcoCAR is a U.S. Department of Energy (DoE) Advanced Vehicle Technology Competition (AVTC) program with the foundational industry sponsorship and vehicle donations by General Motors (GM). Students receive hands-on real-world experiences as they work towards creating the transportation technology of the future. Siemens Digital Industries Software is the principal engineering software supplier to the teams as well as a sponsor. GM provided a Chevrolet Blazer SUV for the students to modify from a gasoline-only vehicle to a hybrid-electric powertrain, as well as adding advanced driver assistance features (ADAS), (such as adaptive cruise control or lane-keeping). Siemens Digital Industries software is the primary engineering software sponsor for all the student teams. Siemens provides software at no-cost, along with free online training courses and technical support.
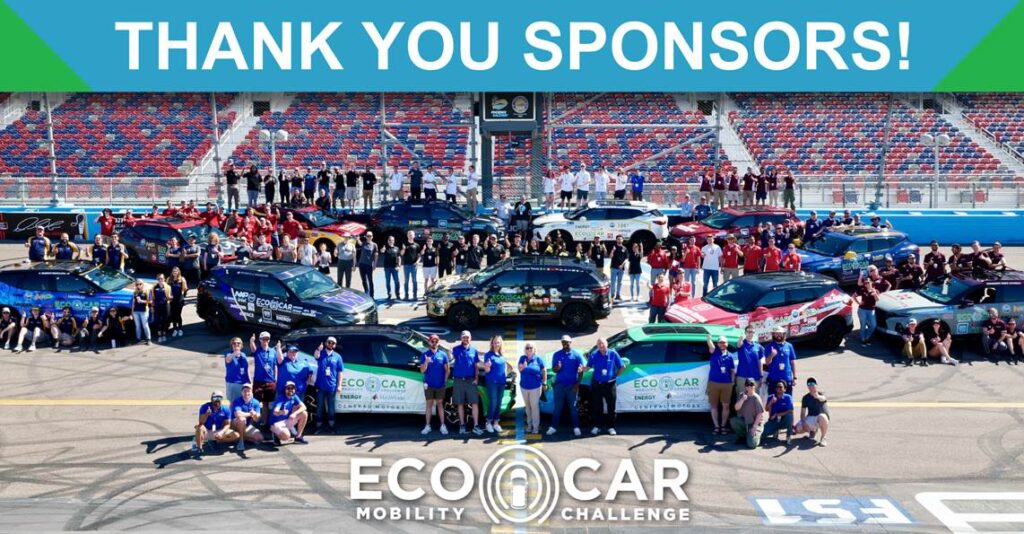
“Siemens is proud to be a longstanding sponsor* of the EcoCAR competitions series,” said Leigh Anderson, Manager of Siemens’ global student competitions program, “We had the opportunity to collaborate with the UT team on this article which showcases how the team used our Xcelerator software suite. It was great to see the relationship grow through this collaboration, and the stunning design-build work these UT students did. We will continue sponsoring this impressive talent-development competition, including the next series – the EcoCAR EV Challenge for 2022-2026, (as well as GM’s equally amazing AutoDrive Challenge II university competition operated by SAE’s capable organization.)”
For more than a dozen years of EcoCAR series, our Tennessee team has relied on Siemens’ software to advance the technology in our hybrid vehicles through their sponsorship and dedication to supporting EcoCAR teams. The resources they provided to our teams made them an essential partner of the EcoCAR Mobility Challenge. They provided us with training, software and tech support that empower our engineering functions to be carried out much more quickly and easily.
The most important, and difficult, part of creating such a complex vehicle system is integration. While designing and creating new ideas each have their own challenges, the integration phase holds the greatest risk and opportunity for error, due to tight tolerances and very complex fitment. Team Tennessee is currently operating with nine team leads, 12 undergraduate students, four volunteers, and four faculty advisors. With a limited number of students working on the project, having resources that cut down on time and cost are essential to our success.
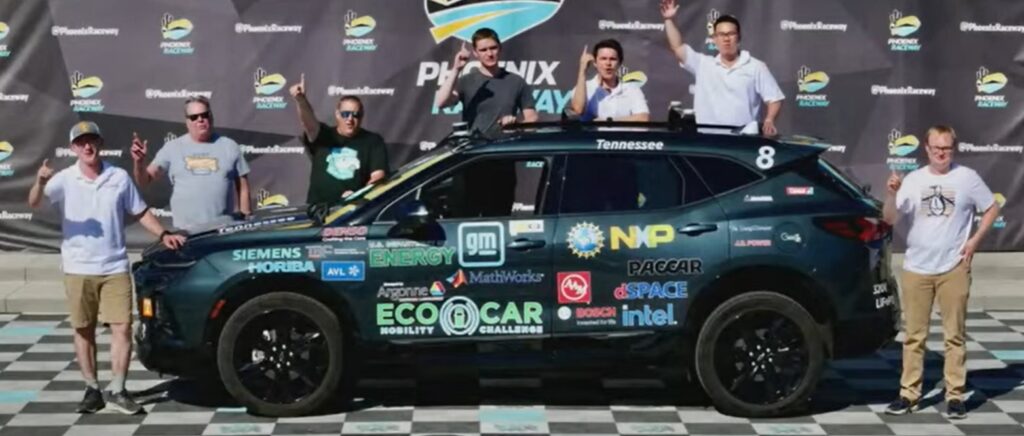
With the use of the NX software that Siemens provides to all EcoCAR teams, we were able to save a lot of time and money in the integration stage by testing out different aspects of our innovations virtually – before implementation into the vehicle.
Siemens’ NX with Simcenter is a comprehensive mechanical design software suite. Engineers use the NX software to do design, strength, aerodynamic, and weight analysis. NX saves time, money, and resources because engineers can do tests early in the digital twin world of NX rather physically testing parts. Engineers create and manipulate the vehicle model in NX in order to ensure their work is accurate and precise before implementing it into the actual vehicle. When moving to the actual vehicle, our team never had to worry about throwing away custom parts because all the parts are designed and proven to integrate exactly in advance using NX.
Christopher Lang, Propulsion Systems Integration Engineering Lead, said, “With Siemens’ NX software, there are unlimited opportunities for innovation. Pretty much anything you want or could want to do, you can do in NX.”
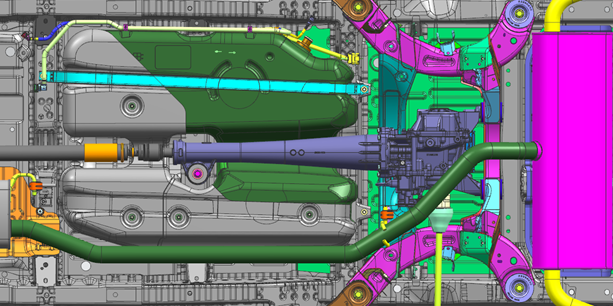
The electric power train integration consisted of the following main components:
- A123’s 4.5 kWh high voltage (HV) battery
- TM4 85 kW motor and inverter
- General Motors rear differential
- Fabricated custom driveshaft
- Motor coupler
- Custom fuel tank
To integrate these complex shaped components, new mounting structures were designed in NX as a “digital twin”. This model was used to create the necessary drawing files to build new parts and make modifications to the vehicle. In one of these modifications, the rear passenger compartment floor was cut, and a patch panel was installed to allow for the motor to sit higher in the vehicle to maintain ground clearance restrictions. By making the digital twin in NX before implementing these changes into the Blazer, the team was able to ensure the accuracy of all permanent vehicle modifications. Digital Twin model it once – cut once!
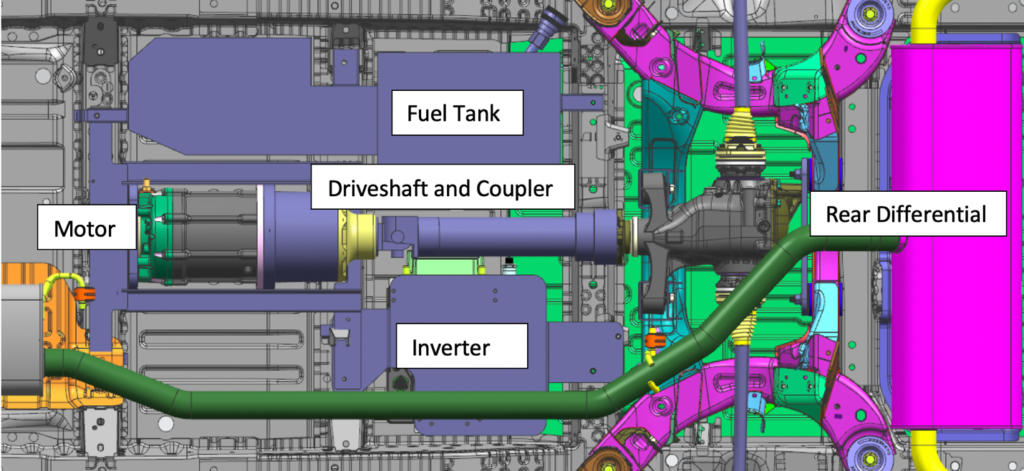
The above screenshot from NX demonstrates the various changes that have been made to the vehicle by the EcoCAR team to create the hybrid power integration. The engineers were able to create a new, smaller fuel tank, add the electric drive system (motor, driveshaft, coupler, and inverter), and transfer power from the rear differential to the wheels.
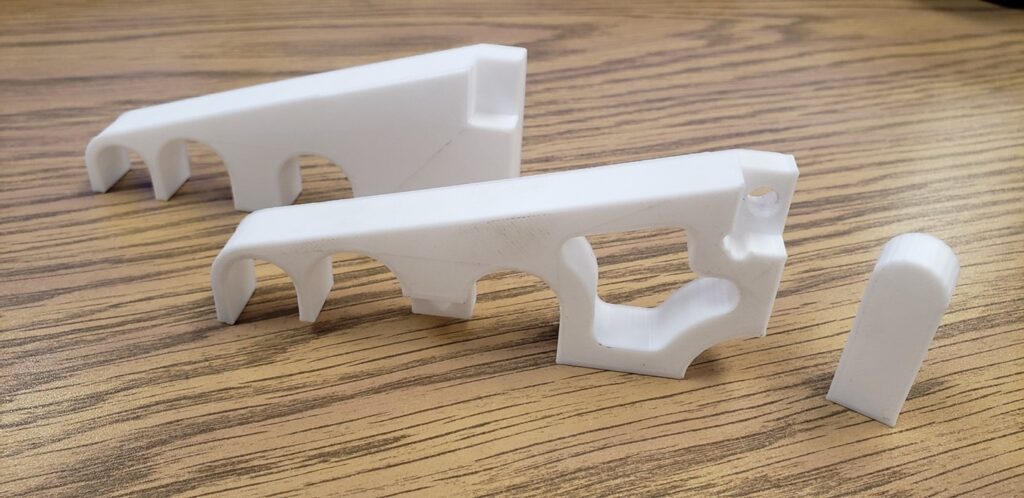
The design process progresses from the digital twin model in NX to the physical implementation, which are first 3D printed using the NX digital part files. Parts are 3D printed to quickly and inexpensively double check their fit on the vehicle, before being machined out of aluminum using NX CAM output.
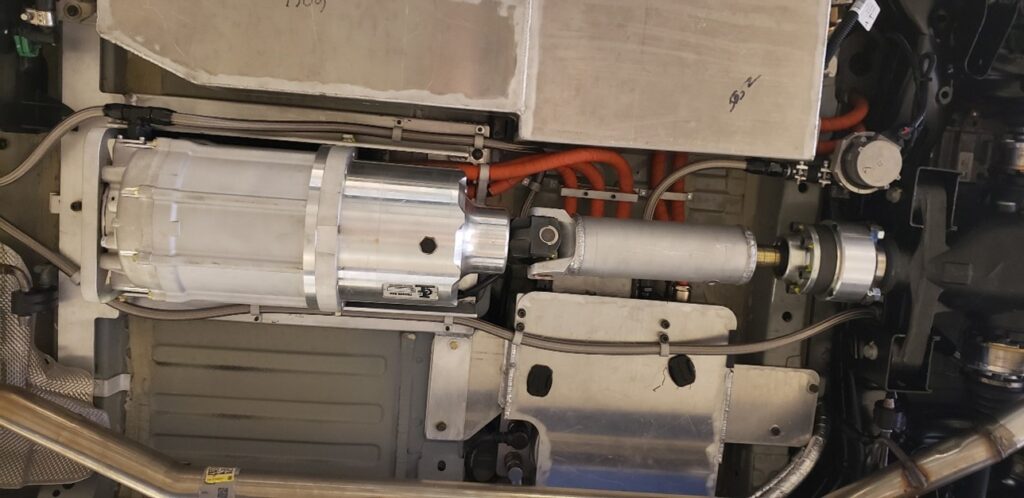
Once the digital twin has been created in NX, and part sizes have been double checked with 3D printed material, our team was ready to make the actual modifications to the vehicle and parts. The above image demonstrates the physical model of this system in the Blazer. Each part that has been implemented was successfully designed and machined without error, thanks to the precision of the NX digital twin.
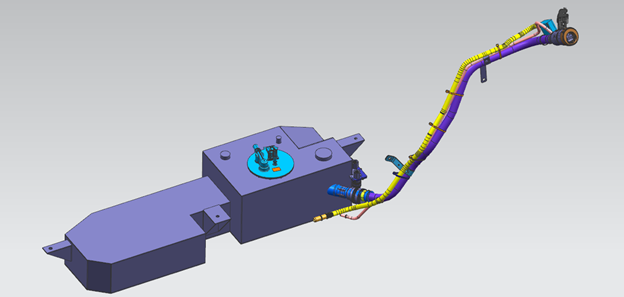
Using NX was also necessary for Team Tennessee’s fuel tank integration. The vehicle’s stock fuel tank had to be removed to make space for the electric propulsion system integration. The team manufactured and built a smaller fuel tank and placed it into the car using some of the stock mounting locations. Since the engineers were using NX software, the new fuel tank was designed and made to reuse the stock fuel filling components. The above photo demonstrates how the new fuel system was integrated into the stock fueling system.
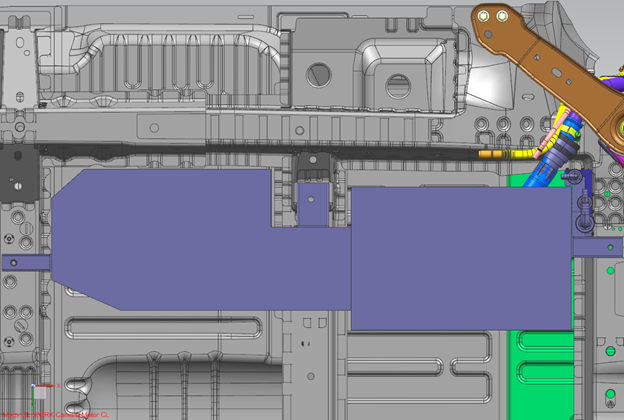

The smaller fuel tank designed, fabricated and installed in the physical vehicle – exactly as modeled in NX, with 1st time fit.
Again, the NX software allowed engineers to create all changes digitally before implementing them physically into the car. As is demonstrated in the images above, the digital twin captured the dimensions of the car and allowed engineers to successfully implement their designs on the first try.
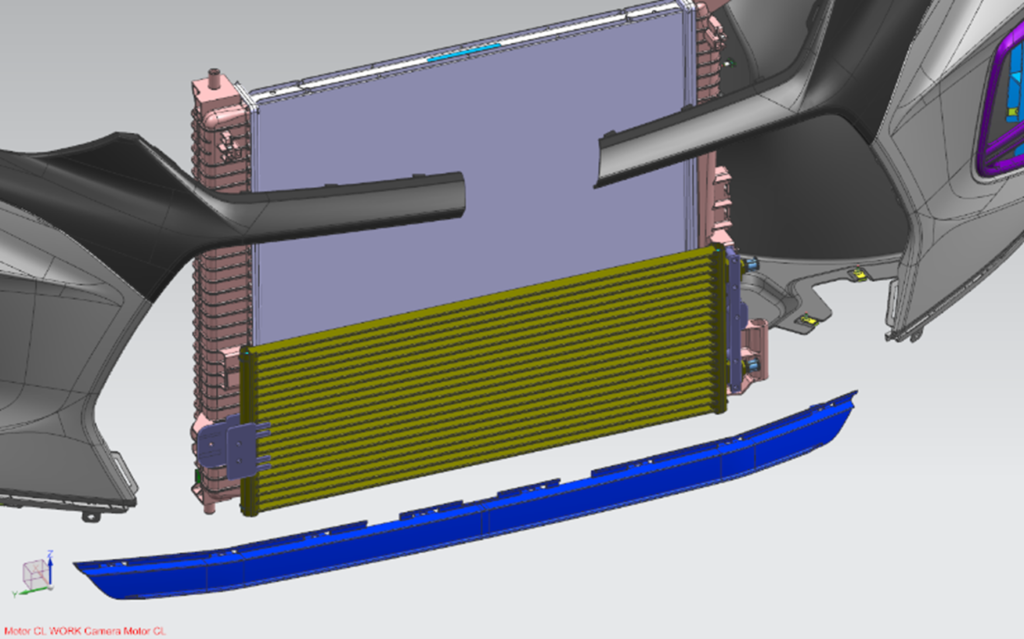
Another necessity in hybrid electric vehicles is a high voltage (HV) cooling system. In the Blazer, there are two stacked radiators. One is the stock vehicle system and the other is an additional HV cooling system that was added by our engineers to cool the electric HV components which are used in our hybrid vehicle. The motor, inverter, and battery are cooled with this independent cooling system. This cooling system was integrated in front of the stock radiator, and the cooling line routing was done in NX to allow the correct lengths to be used in the system. NX also allowed our engineers to add the mounting hardware needed to adequately retain the lines.
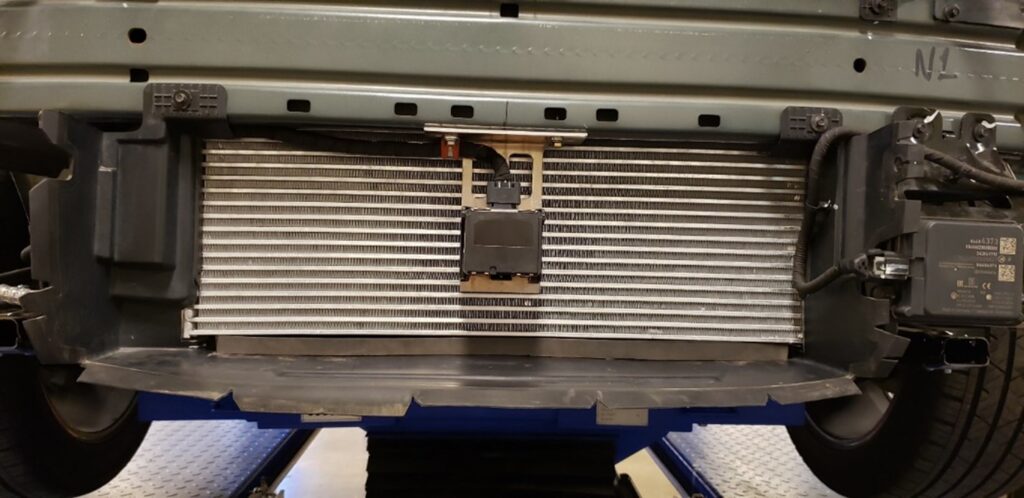
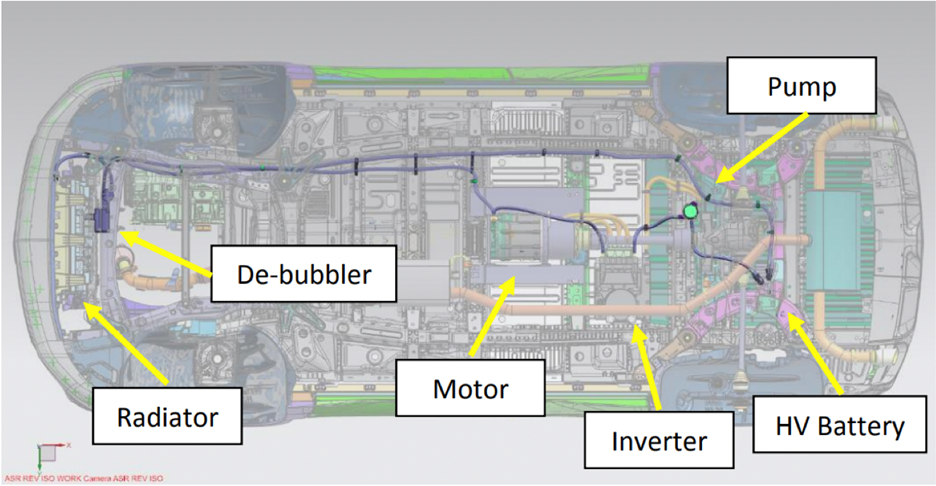
The above image captures the routing of the HV cooling system created in NX. Engineers digitally routed tubes to get the lengths of them so that they could integrate properly sized coolant lines into the system. This picture demonstrates the various fittings and mounting hardware and the locations of the various high voltage components and cooling loop components including the pump, de-bubbler, and radiator.
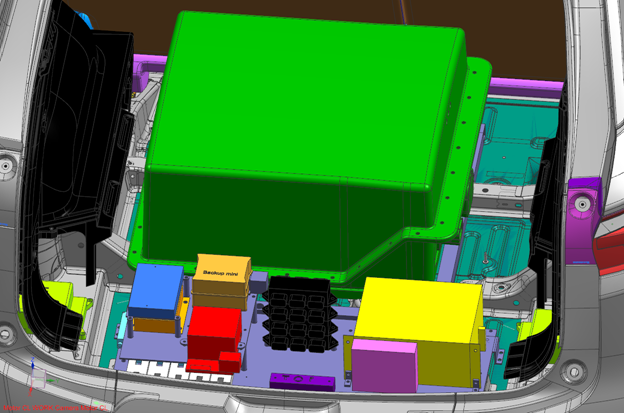
Engineers also use NX for the electrical system and for Connected & Autonomous Vehicle (CAV) purposes. The motor, inverter, battery, and power distribution boxes are all interconnected to provide propulsive power to the rear of the vehicle. The phase cable, HV cables, and mounting structure were modeled in NX to accurately represent their integration into the vehicle. The HV battery, energy storage system (ESS) and CAVs equipment must all be integrated into the rear of the vehicle. By creating the digital twin in NX, mounting structures were able to be implemented for each of the various components that allow them to be safely and securely integrated into the vehicle.
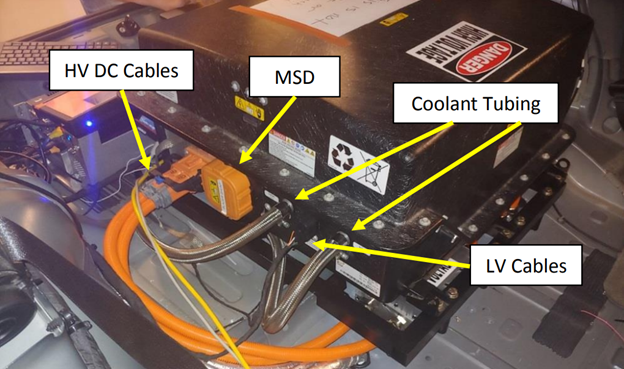
Since EcoCAR is dealing with such innovative and new technologies, sometimes competition rules are updated in order to ensure proper safety measure are taken. In this year’s EcoCAR challenge, there was an adaptation made to the rear vehicle systems integration for this reason. New specifications were made to mandate a crush zone for the rear of the vehicle in case of a rear-end collision. This was done so that if a rear-end collision occurs the CAVs equipment will not be pushed into the battery.
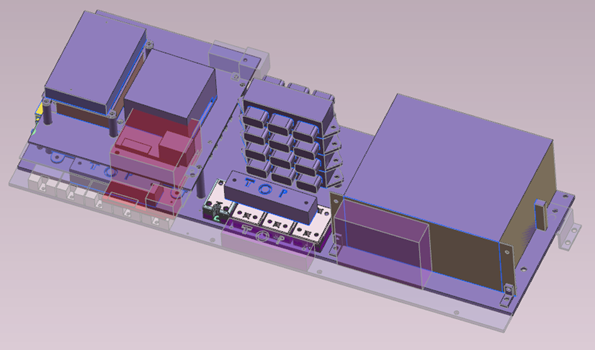
The NX software allowed our team to develop strategies to comply with the new rules without destructive testing. These strategies allowed our team to quickly change these components that were already integrated into the vehicle without causing major disruptions in testing. All changes were made in the digital twin and then implemented easily into the vehicle.
“NX is truly amazing.” UTK Project Manager J.P. Nelms, said, “You can test anything in a digital model before you make it. It is incredibly accurate, and it saves valuable time and money with first time fabrication success. NX makes it possible for us to compete on the same level as other EcoCAR teams that have far more resources and team members.”
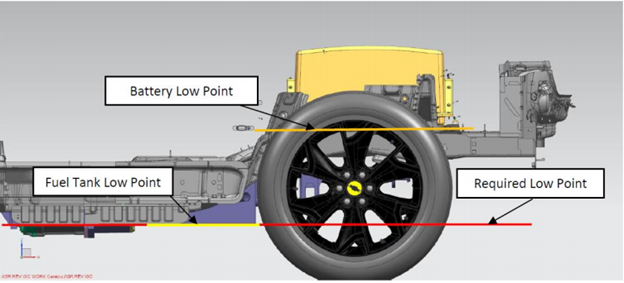
There are also other requirements that teams are required to abide by, such as ground clearance. There are specified low points for the fuel tank and battery. Since our team can do this in NX before it is implemented into the vehicle, we can ensure we pass all the criteria before actually building these structures and components. Without NX, it would be incredibly difficult to modify vehicles into hybrid-electric vehicles. This software makes it possible to precisely design components and put them in a digital twin model of the stock vehicle provided by GM in an NX CAD model.
Another helpful software Siemens provides teams is the Capital Essentials software (previously named VeSys). Capital Essentials is an electronics system design software package that enables teams to design and document the modifications that have been made to the vehicles stock wiring, electrical harness, and electrical systems. Our team uses Capital Essentials to track changes that have been made and to check the implemented wiring if problems arise. This schematic is very important to the safety of team members. It depicts the circuit which cuts power to the vehicle’s propulsion systems in case of an emergency. Capital Essentials provides a library of premade components to speed design, such as fuses, switches, wire, and relays. The symbol library and symbol editor allow the team to create various specific electrical components as needed. The most complex components are able to be drawn by the team using the pre-built parts such as fuses, switches, and other diagram components.
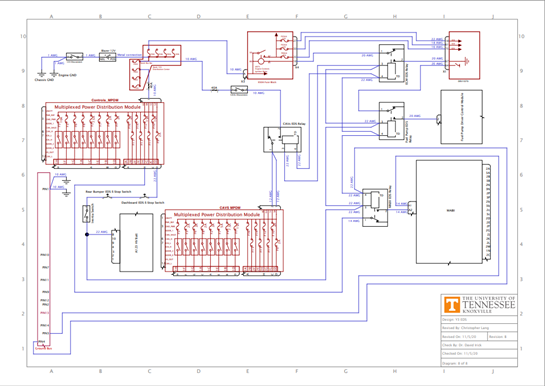
“With Capital Essentials software, we can easily organize diagrams and harnesses for the entire car in one project“. stated UT’s Undergraduate Research Assistant, Landon Harris, “Better yet, with the higher quality and new features of Capital’s documents and reports, our team has even started creating virtual wiring-harness diagrams before creating the physical wiring. Once you’ve used electrical system design like this, you don’t want to go back. I can’t imagine doing this work without the help of Siemens Capital software.”
We at Team Tennessee were glad to highlight this crucial partnership with Siemens through our sponsor collaboration deliverable. A bonus was winning first place for Communications & Sponsor Collaboration for this article! Implementing other challenges such as adaptive cruise control and refining the fully integrated propulsion system was easier with Siemens software. None of this could be achieved without our partnership with Siemens. The resources they provide are what make this level of innovation possible as we work toward the future of safer, more environmentally-friendly advanced vehicle technology.
Also see the blog article covering the 2018-2022 EcoCAR Mobility Challange series recently completed.
Want No-Cost Software for your Student Team?
Siemens software plays a crucial role in equipping and training student teams all over the world to enable success. Learn how to request a no-cost, full-featured commercial software licensing grant for your team here.
Useful Links for Student Teams:
Siemens’ Global Academic Partner Program Home
Student-Exclusive LinkedIn Group – Network with industry professionals, recruiters, educators and peers
Curriculum Hub – Free classroom downloads (great for virtual classrooms, too!)
Academic Certifications and Digital Badges – Get certified in NX, Solid Edge, Simcenter Amesim, MBSE and more, plus earn digital badges to show off your student competitions and software expertise on your resume.
Student Edition Software Downloads – Free software for students and educators!
<end>