The advantages of Comprehensive Digital Twin in managing complexity
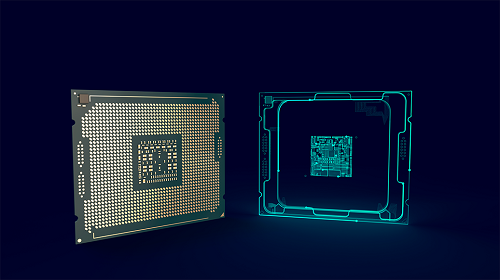
The Comprehensive Digital Twin is more than just a bridge between the digital and real worlds. It’s a way for progressive companies to stay ahead in a world where costs can skyrocket beyond scope and new product introduction windows are decreasing. It’s a way to build the factory virtually first and ensure its safety and efficiency before pouring the foundation or turn your current facility into a more sustainable manufacturing plant.
[Read our Siemens Xcelerator blog: What is the Comprehensive Digital Twin?]
How are the most progressive companies using the Comprehensive Digital Twin to collaborate better amongst their own design teams as well as external suppliers and customers?
These progressive companies can use their agility and the flexibility of digital solutions to meet the continuous uncertainty in the world.
In the 2022 Digital Twin Report, Lifecycle Insights reflects on how companies are using digital twin and digital thread and the differences between the most progressive and least progressive companies are using this technology.
Let’s take a closer look!
Developing better products, faster
In what ways are companies using the Comprehensive Digital Twin and digital thread? How does this impact their ability to develop better products faster?
During the product design process, engineers and other stakeholders are constantly working on various tasks simultaneously. They need a single source of truth to work from which includes everything from concept design and drawings to simulation results.
Finding specific, accurate information amongst the complexities of products presents challenges. However, integration between the digital twin and digital threads allows stakeholders to make well-informed decisions and accelerate the development process.
Progressive companies realize value in product design by connecting their digital twin and digital thread. They’re using PDM, PLM, or ALM solutions to find and access the right design-related data faster, such as models, drawings, simulation, and more, while executing their tasks.
Engineering better production
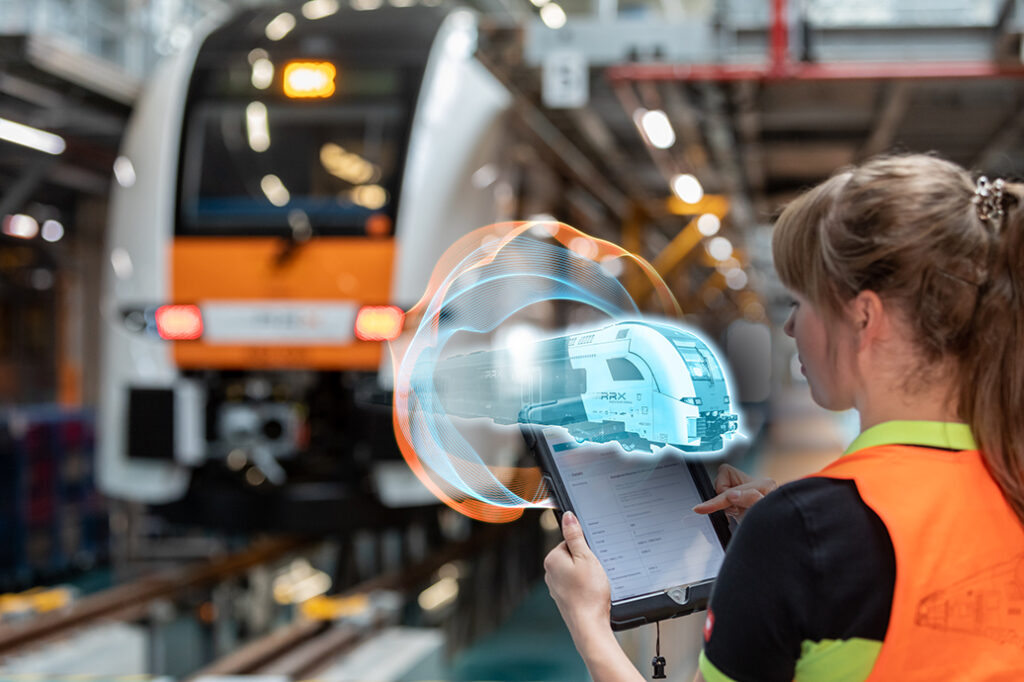
What could slow down or jeopardize the speed and efficiency with which a product is created? How much could be saved if delays and cost overruns could be solved before production?
Integration between the digital twin and digital threads is crucial to making well-informed decisions and accelerating the production engineering process. According to the 2022 Digital Twin Report, the most progressive companies are more than twice as likely as their least progressive counterparts to find production planning content using links from the process task in an advanced solution such as PDM, PLM, or ALM.
Connecting the digital twin and digital threads in the production engineering process ensures that stakeholders have the right information when they need it, make better decisions faster and have greater flexibility within their manufacturing environment.
Digital twin and digital thread adoption
Most of the least progressive companies surveyed in the 2022 Digital Twin Report had only a few digital transformation initiatives implemented at their companies. Recognizing the need to increase these initiatives to maintain competitiveness is the first step to becoming more progressive.
Companies don’t have to invest in an overwhelming amount of digitalization solutions at the forefront of their journey. In the short term, they should develop a digital transformation strategy based on business needs and start to adopt initiatives incrementally.
Looking further ahead, companies can create a plan that best meets their needs, anticipate what resources they need and ensure the culture of the company aligns with these efforts — an often-cited reason for lack of digitalization.
Digitalization to manage complexity
Product and process complexity is going through the roof. Amid this explosion of complexity, it has never been more apparent that engineering domains and functions must be integrated, co-designed, and require a single source of truth for engineering and manufacturing data.
The digital future is filled with technology to help businesses make better decisions faster. The Siemens Xcelerator portfolio provides the software, services and an application development platform to help companies embrace digitalization and create the innovative products of tomorrow with today’s best-in-class technology.
Learn more about Siemens Xcelerator.
Read the full 2022 Digital Twin Report here.