New machines: The only way to meet high-mix, low-volume demand?
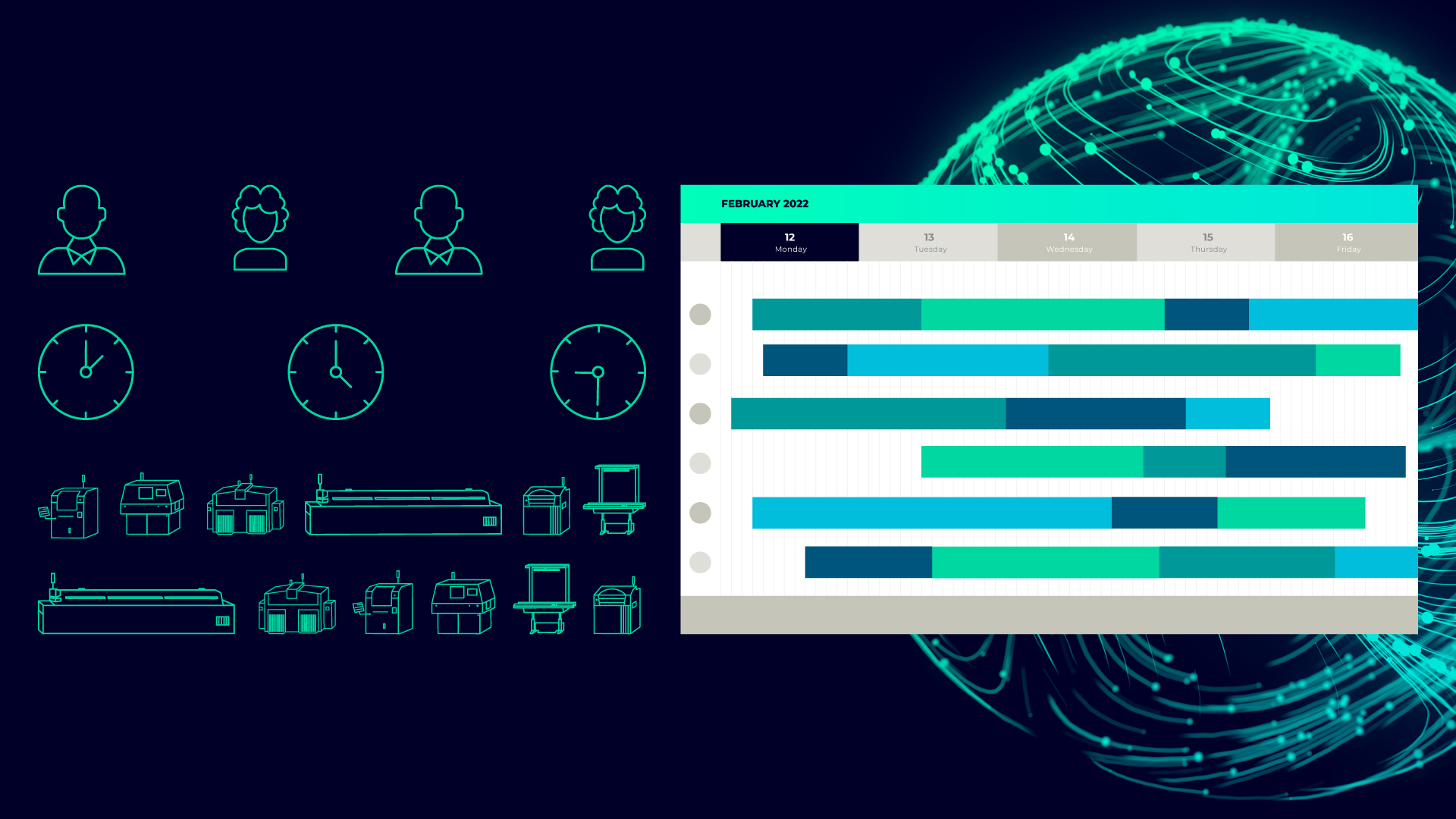
Our new whitepaper explains how to get the most out of your existing electronics manufacturing assets
Meeting current market demand for a high mix of products, with low volumes and costs and fast delivery, is a significant challenge for electronics manufacturers. Traditional planning tools like spreadsheets are simply not enough to effectively manage line planning in today’s complex manufacturing environment. Aiming to improve shop floor efficiency, manufacturers are often driven to invest in costly new production machines.
But new equipment isn’t always the best solution or the most cost-effective one. Before diving into new investments, it’s worth taking a fresh look at current resources and considering other ways to improve flexibility and yield.
A scheduling solution specifically developed for electronics manufacturing can have a huge impact – empowering improvements in resource use, reduced changeover times, and the elimination of unnecessary, manual error-prone processes, all without major investments in production infrastructure. It can also be a significant factor in the automation of factory processes.
Our new whitepaper breaks down the four key steps to better utilizing existing resources and improving product quality:
- Understand how your current scheduling process responds to changing variables
- Use a scheduling solution for electronics manufacturing to improve resource use
- Remove unnecessary, manual error-prone processes
- Reduce changeover times
Download the whitepaper now to learn how to achieve better product quality, reliability and stability without major investments in new equipment.
Test Siemens’ specialized tool for SMT assembly line planning
With our free online trial for Opcenter Scheduling SMT, you can test drive our solution and learn more about its unique dynamic scheduling capabilities. The trial environment includes exercises with detailed steps that will show you first-hand how to get optimal results in a challenging manufacturing environment.