The role of design verification in the electronics manufacturing process
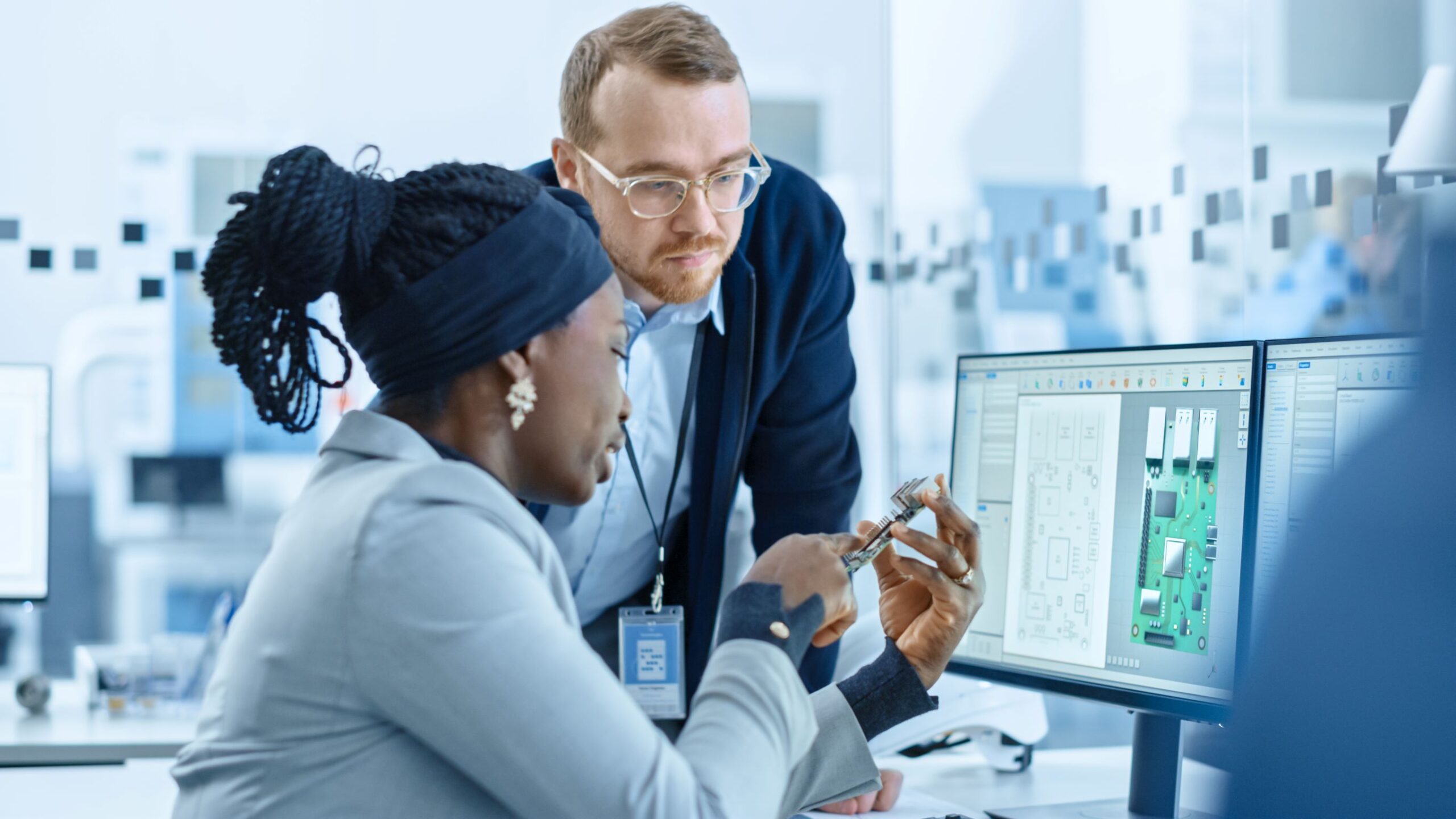
Blog #2 in a 12-part series covering the Digital Twin Best Practices in Electronics Manufacturing mini-webinar series by Jay Gorajia
Participants in the production of electronic products are frequently challenged by risks that affect the profitability of their projects. For example:
- Design specialists often lack insights into manufacturing processes, possibly resulting in design errors and the need for re-spins.
- Fabricators may not have all the information they need to initiate production, and may require frequent, lengthy communications with the designers, leading to time and cost overruns.
- Management, with an eye on the bottom line, risks delays, financial losses, and reputational damage.
There is a root cause for most of these concerns. Often, designs are not verified for manufacturability at an early stage of the process. As the project progresses, the discovery of design faults becomes increasingly costly, as design do-overs and even rejection of completed boards may be necessary.
So what is the role of design verification in electronics manufacturing, and how does it help improve bottom-line performance?
In the second session of our series of 12 mini-webinars on Implementing “Digital Twin” Best Practices From Design Through Manufacturing, we focus on verification of designs in order to avoid the costly pitfalls mentioned above. Design verification is an essential element of the digital-twin strategy that “left-shifts” crucial processes and decisions, thus helping organizations get it right the first time.
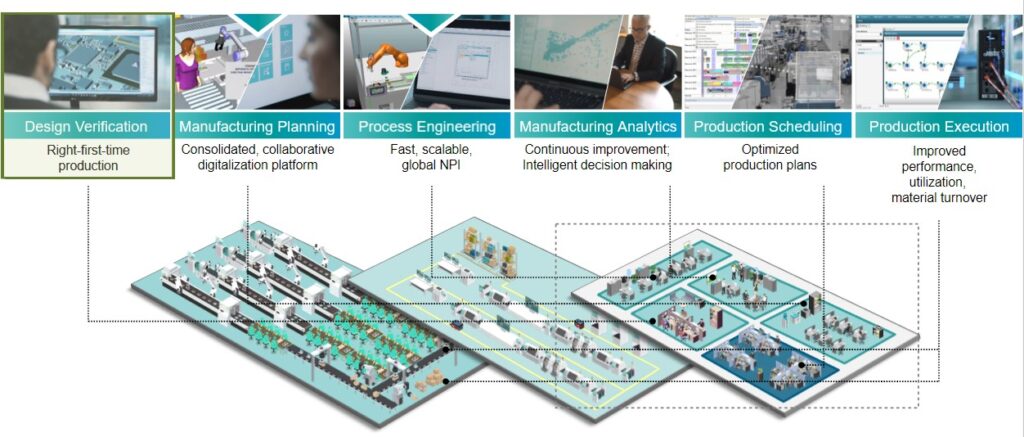
In this segment, we take a look at DFM (Design for Manufacturing) methodologies, and how they have become an essential part of the production process. We also introduce Valor® NPI – Siemens’ automated DFM design validation tool.
It’s a short, 7-minute session – watch it now!