Today’s tools building tomorrow’s heavy equipment
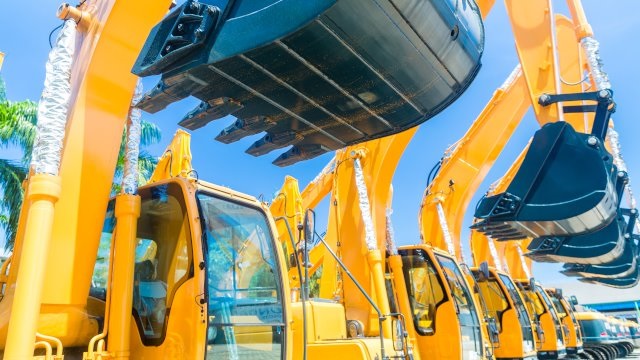
Where today meets tomorrow: rethinking the design process
In the previous blog, Building the heavy equipment machines of the future (Part II), we discussed solutions that heavy equipment manufacturers are using to build the next generation designs. We’ll continue exploring the advanced tools of today, such as the digital twin, that will innovate the heavy equipment machines of tomorrow.
In this blog, we’re going to go a little further and discuss how three design and production tools —generative design, additive manufacturing and virtual reality — are helping manufacturers create the complex products that drive the future of heavy equipment machinery.
1. Design optimization
Manmade designs tend to have a lot of straight lines and simple curves. Unfortunately, the designs are constrained by factors such as manufacturing techniques, materials, aesthetics and availability. But they’re not optimized. Engineers have long started to look at nature for inspiration of perfect functional design. Natural designs have been shaped by natural forces to conform and adapt to their environment. They may not look optimal to us, but they are optimized for their environments.
Digitalization can be used to optimize designs to match the environment where they will be included without the constraints of the past.
Take a look at the series of images in Figure 1 with the man-made designs on top and the natural ones below. This is the start of thinking today’s designs and thinking about how we get to tomorrow products with generative design.
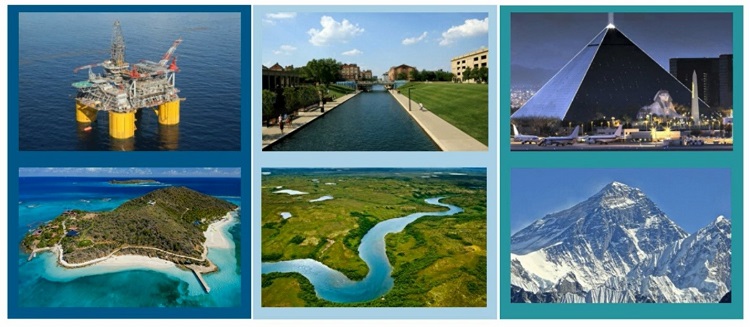
One key benefit to generative design is shedding excess weight, which helps reduce fuel use and emissions while still meeting performance and durability requirements.
It’s not easy to simulate heavy equipment because their use cases and conditions vary so much. That’s why simulation is critical, especially in areas such as noise, vibration and harshness (NVH), which helps minimize operator fatigue. To reduce time to market, it’s imperative to get the right design early and ensure quality from the very beginning.
Unfortunately, so many manufacturers operate systems for design and validation that are disconnected. They’re also relying far too much on physical part testing. This slows down the design process and is much more expensive than virtual testing.
What’s changing to the benefit of the design team is a convergence of technologies that are opening up new possibilities in design.
Designers can designate the important parameters and functions of a design and then automatically generate shapes that are optimized for material use, strength and other factors, instead of being constrained by them. Then there is massive potential for light-weighting and material savings while also ensuring strength. Weak spots and potential failure points are not just discovered during the simulation but are fixed as well.
Design optimization software makes it easier to explore multiple design alternatives to find the one that works best. When teams can bring feature parameter optimization, topology optimization, convergent modeling and additive manufacturing technologies together, they can produce a true generative design in a single environment.
A great example is AMAZONE which develops and produces innovative agricultural technology. They created a virtual test track using Siemens software to predict the performance of their machines, decrease their number of prototypes and testing, and are better able to find and address design flaws at an earlier stage. A combination of all of these allowed AMAZONE to reduce their concept to production time from one year to fewer than 4 months.
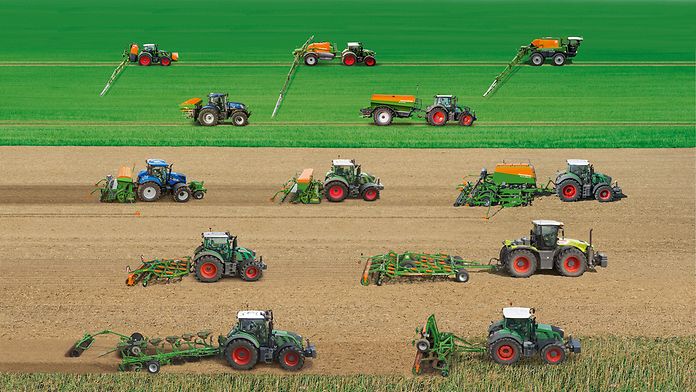
2. Industrialized additive manufacturing
As the heavy equipment market evolves toward customization, supplier replacement parts over the life of those machines becomes more difficult. At the same time, the lightweight designs necessary to reduce fuel consumption and emissions will take new manufacturing methods such as lattice design, which helps create strong, lightweight components.
The current approach to additive manufacturing makes it possible to print complex objects via a CAD simulation model, creating layer-by-layer using various types of materials with high precision and repeatable quality. It can be difficult to scale up from prototype to mass production with additive manufacturing because things like change management, translations and different data systems cause issues and creates bottlenecks.
There are new techniques and integrated solutions moving additive manufacturing beyond prototyping and into production. Additive manufacturing is becoming industrialized. This means manufacturers utilizing these digital tools can:
- Scale additive manufacturing from prototypes to mass production, all in one system
- Create strong, lightweight, optimized designs
- Avoid costly redesigns by ensuring part manufacturability early in the design stage
- Quality check tools and identify issues
Engineer can also update the build job with new part design in one system while monitoring the entire process and improving quality and efficiency.
3. Visualizing products with virtual reality
Let’s take a look at how technology like virtual reality (VR) and augmented reality (AR) will revolutionize how designers and manufacturing personnel will have better training and more automation so they can work smarter and more efficiently. Current solutions are limited to 2D displays and techniques, for example, the 2D screen you’re looking at right now. This also means collaboration issues, slow and expensive part checking, and safety concerns.
An immersive 3D virtual environment though offers a digital mock-up, the ability to design in-context with AR and VR, virtual design reviews, high end rendering and lightwork design.
The digital twin can help visualize innovative designs in a true 3D environment in many ways. Digital mock ups reduce or eliminate the need for physical prototypes by helping to visualize and analyze virtual prototypes early and often. These digital mock ups can also find and resolve form, fit and function design issues early in the design process with sophisticated spacial and analysis tools including clearance and interference analysis capabilities.
Amid distance, 3D virtual environments make it possible for entire teams to meet in an immersive 3D environment. Everyone on the team can view the same model and review, discuss and provide feedback in real time. With augmented reality and virtual reality, they can now interact with the digital twin and make sure the team works with the latest design.
Knowing how the product looks before production means decisions can be made early on about aesthetics or materials.
Virtual reality enables an immersive design review:
- Visualize designs at full scale
- Streamline and focus on the most important areas
- Measure, inspect and validate using simple tools to quickly find issues and improve designs
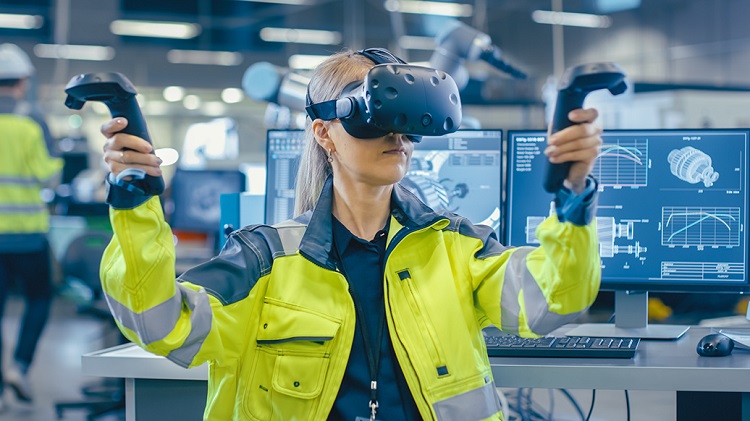
Meeting the demands of an evolving industry
The heavy equipment industry is transforming. Global trends and increased complexity are driving the need for digitalization to take the lead in advancing sustainable, traceable and reliable solutions. For those companies who want to remain competitive, it is critical to make digitalization a comprehensive part of designing, producing and manufacturing products.
With the Xcelerator Portfolio, Siemens enables a comprehensive digital twin. This includes software solutions to help design, simulate and validate all the configurations of a digital machine and produce it in a digital environment first. Using smart manufacturing technologies, teams can simulate the digital performance of their product virtually and collect the information in real time as manufacturing information or operational data.
Learn more how the Xcelerator Portfolio is revolutionizing the way heavy equipment manufacturers are designing, building and competing.
This concludes the third and final blog in our series. Check out the previous blogs:
Read Part 1: What will it take to build the heavy equipment machines of the future?
Read Part 2: Building the heavy equipment machines of the future Watch the full webinar: Heavy Machinery Industry Trends