Decarbonizing industry with digital solutions
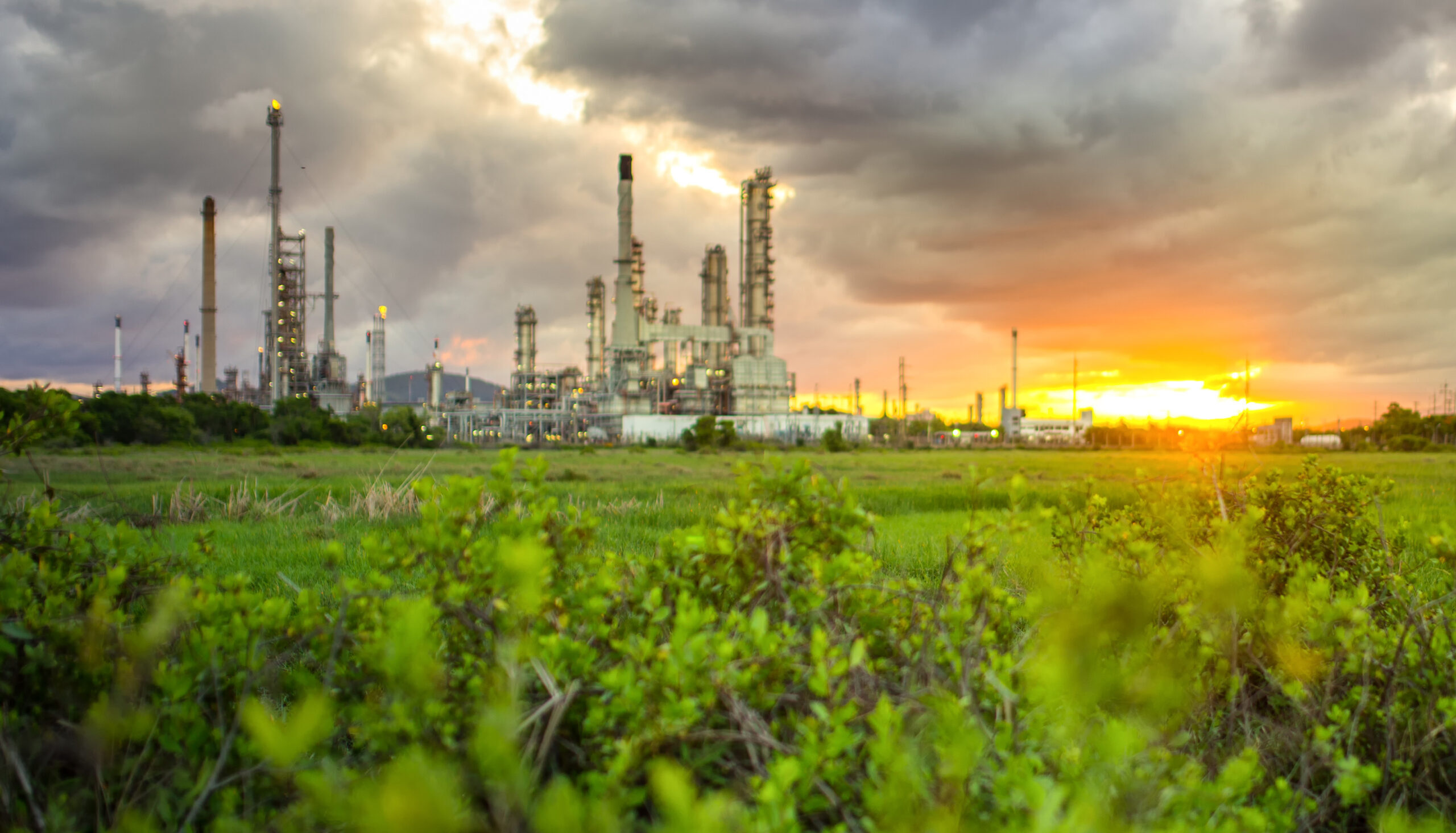
Removing carbon emissions from global economies is not only a matter of avoiding climate change. While decarbonization is highly prioritized because of the climate effects, the processes currently associated with carbon emissions have a fiscal incentive to reduce carbon emissions. Energy consumption within manufacturing and use of a product has a direct link to carbon releases, even fully electrified products require inputs during the manufacturing process. And making these products and processes more efficient on the way to net-zero is a great starting point for many businesses.
Getting there, however, requires a capable toolset for the task. Many of the products and processes that can most benefit from sustainability improvements are already complex systems relying on expansive supplier networks to bring them into the real world. Building sustainable industrial innovation necessitates a solution built on digitalization and automation. It requires the businesses start with a system of systems approach to design, manufacturing, use, and end-of-life to understand the product and processes. Businesses will rely on connected industrial ecosystems to design and built their product in a wider context. And every step of development needs to be understood with holistic sustainability indicators to continuously improve.
For a detailed description of decarbonization solutions for businesses, you may want to read our expert whitepaper on the topic. But for a condensed version continue below for the highlights.
Decarbonizing the product
One of the paths businesses will need to take in decarbonizing their business is to remove carbon emissions from the product itself and its usage life. And vehicle electrification is perhaps the best example case – by shifting the vehicle away from combustion as the energy source the carbon emissions over the lifetime of the product can be drastically reduced. But, the increased material needed to store and delivery energy increases the energy and material requirements at the beginning of its life. Balancing the improvements requires a comprehensive toolset, it requires a system of systems approach to understand the dynamics of such complex products.
How that happens can be just as varied as the products applying decarbonization practices. To continue the electric vehicle example, it could mean reducing the weight of structures and systems to increase the effective range of the vehicle per unit energy. Or it could be designing more aero-efficient body shapes to reduce skin friction. A cellphone or consumer electronic device might include a more energy efficient chip at a higher initial cost to reduce the long-term energy consumption of the device while providing similar performance. Digitalization creates that structure for these engineering decisions as a part of the digital twin and a system of systems approach helps define the cross-domain understandings.
Decarbonizing the process
A theoretically carbon-neutral product is great, but it is not the whole story. It still needs to be manufactured – requiring further energy inputs to the system. A highly-optimized component designed with topology optimization might deliver the most performance per gram in the final product, but without understanding the manufacturing process it can energy intensive, or even impossible, to bring into the real world. Whether using more traditional subtractive methods like machining or cutting edge additive processes, it is important to understand how much energy is being put into the system to create a product. Inefficiencies in manufacturing can completely negate decarbonization benefits from a more efficient product design.
But this also has a fairly direct financial impact on the manufacturer. Energy can be a hefty operational cost to manufacturing and minimizing how much is needed per unit produced can provide substantial savings. That might emerge as an optimized floor plan to reduce the travel distance of a product through the factory, tweaking the operating parameters of drive motors on machines to consume less electricity, or reprogramming when machines will go into a sleep state to reduce vampiric drains from a machine idling. These are just some of the solutions that can be deployed today with digitalization, but with some extra engineering work businesses can fully redesign processes during a refresh with decarbonization in mind.
Decarbonizing the enterprise
Building a sustainable business and decarbonizing does not stop at the factory door. There are still many variables that sit outside of the design and manufacturing phases. It starts at the very early concept designs to select the best material suppliers based on a variety of factors (travel distance, worker safety, carbon emissions, etc.). And it can continue well into the lifetime of the product to encapsulate the decommissioning of the product. Can it be recycled? What is the advantage of repairability vs. circularity? Should manufacturing be localized or centralized?
These decisions may not all be made on day one, in fact few of them will and instead develop over time and product revisions. But being able to collect data and validate decisions made across development is extremely valuable for long-term decarbonization efforts. For more information and maybe some ideas on how your business might start the path of decarbonization be sure to check out our whitepaper on the subject.
Siemens Xcelerator, the comprehensive and integrated portfolio of software and services from Siemens Digital Industries Software, helps companies of all sizes create and leverage a comprehensive digital twin that provides organizations with new insights, opportunities and levels of automation to drive innovation.
For more information on Siemens Digital Industries Software products and services, visit siemens.com/software or follow us on LinkedIn, Twitter, Facebook and Instagram. Siemens Digital Industries Software – where today meets tomorrow.
Stay up to date with the Siemens Software news you need the most.