Hardware-in-the-loop and MBSE
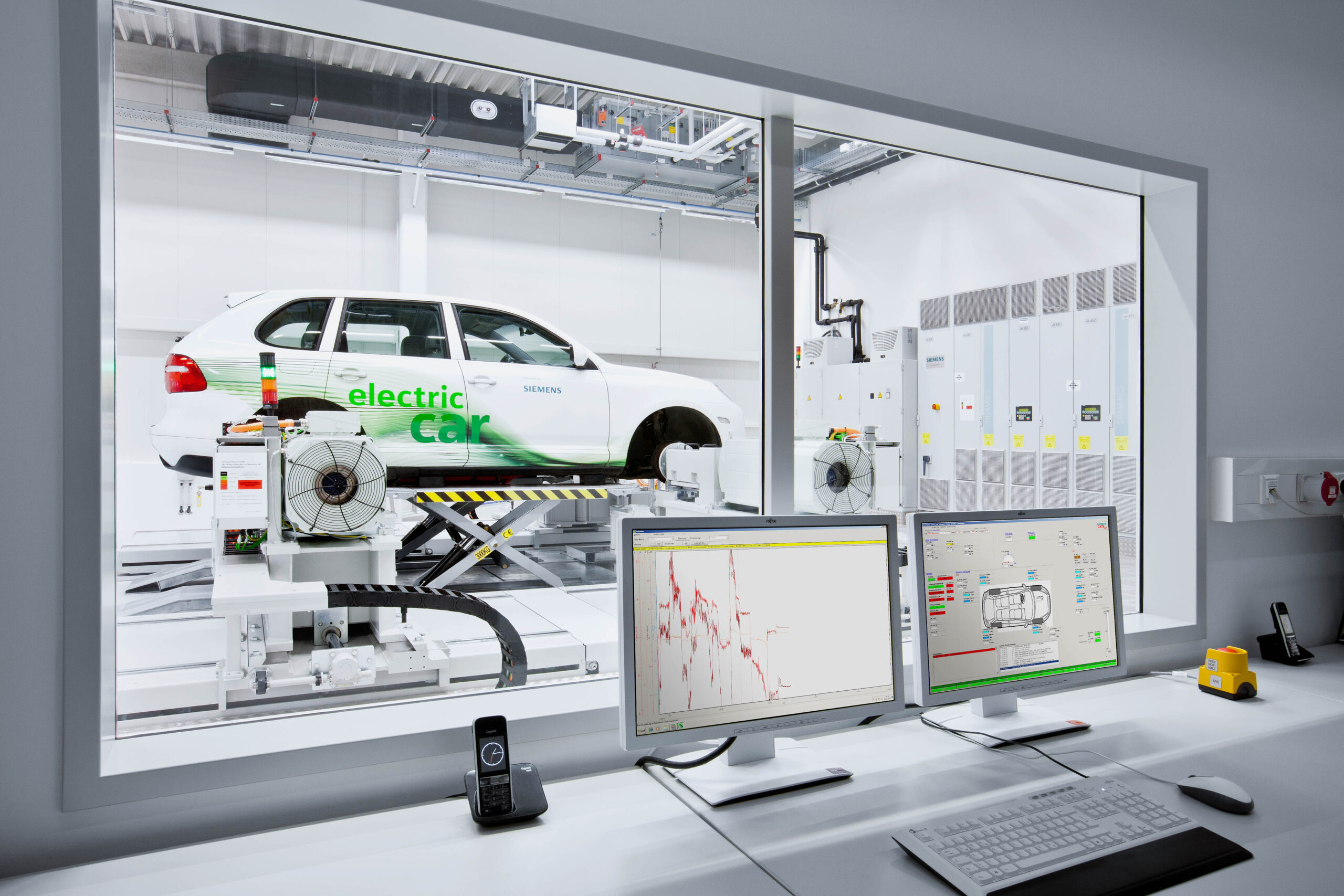
Often when discussing model-based systems engineering (MBSE) the focus is on the digital aspects of development, the role of requirements, and simulation. While it is a very important part of the methodology, it is not the whole story. The requirements and simulated estimations to development need to be validated in the real world to ensure they are grounded. That does not mean building the entire product and testing it in early stages of development, instead hardware-in-the-loop (HIL) testing combines the physical and the digital to remove variables from development. In episode seven of the Model Based Matters podcast, Tim Kinman and I continue our discussion with Michael Baloh and Jan Richter on the hardware and testing side of continuous verification. If you are interested in early analysis, I recommend episode six which also has some good definitional discussion of what continuous verification entails. But how does hardware play into MBSE?
As Tim and I have reiterated so many times before in our other episodes, development starts with concept design where the requirements of the system are defined, and an architecture begins to form through iteration in each of the relevant domains (mech., elec., soft., etc.). But ensuring these requirements are met means simulating and testing the systems. Often these tests can be conducted virtually, especially as a model is extended and resembles the physical world more accurately, but for edge cases or situations involving more subjective attributes physical tests are needed. For the automotive market, this can take shape with robust simulation rigs that can recreate the driver experience of any vehicle – with speakers for road noise, actuators for vehicle dynamics and complete virtual representations of the interior.
But complete vehicle or product simulators require quite powerful computer hardware to intake and calculate the data in real time. Another option for HIL validation is to test an individual system or component under artificial conditions. That might entail mounting a new braking system to a computer-controlled rotor to understand the braking times, thermal dynamics and forces experienced during compression. Rather than the subjective analysis of the whole-vehicle simulators, often called human-in-the-loop, these smaller test set-ups are to validate the physics models and provide concrete answers to possible variables in complex systems.
With the continued hardware advancements in computing however, it is increasingly possible to conduct virtual HIL testing. If data does not need to be calculated in real-time the computing power of the average engineering laptop can calculate test results overnight or in a few hours depending on granularity of the simulations. But you might ask, how can HIL be virtual? And your hesitation is warranted, because it can’t, not really. Virtual HIL is essentially testing the digital model of a physical system against artificial conditions or inputs to understand the behavior of the system. A common application today is for noise, vibration and harshness testing (NVH) to reduce noise and inefficiencies from gearing systems. This is especially important for electrification as there is no longer an internal combustion engine to drown out the other sounds from a system. Simpler tests like these empower engineering teams to get rough results quickly and validate later when the design has been iterated further. And earlier actionable information is a major goal of MBSE.
Our seventh episode of Model Based Matters was really my favorite discussion we’ve had so far, partially because it gave me an understandable reference with my background in mechanical systems, then bridging it into the digital world. I’d highly recommend giving it a listen if you haven’t and if the digital side is more your flavor episode six is a great introduction to continuous verification for model-based systems engineering. Tim and I are always talking with experts in different disciplines, so make sure to check out our other episodes and subscribe for future episodes on your favorite podcast platform.
Siemens Digital Industries Software is driving transformation to enable a digital enterprise where engineering, manufacturing and electronics design meet tomorrow. Xcelerator, the comprehensive and integrated portfolio of software and services from Siemens Digital Industries Software, helps companies of all sizes create and leverage a comprehensive digital twin that provides organizations with new insights, opportunities and levels of automation to drive innovation.
For more information on Siemens Digital Industries Software products and services, visit siemens.com/software or follow us on LinkedIn, Twitter, Facebook and Instagram. Siemens Digital Industries Software – Where today meets tomorrow