Has simulation become the great equalizer for the aviation industry?
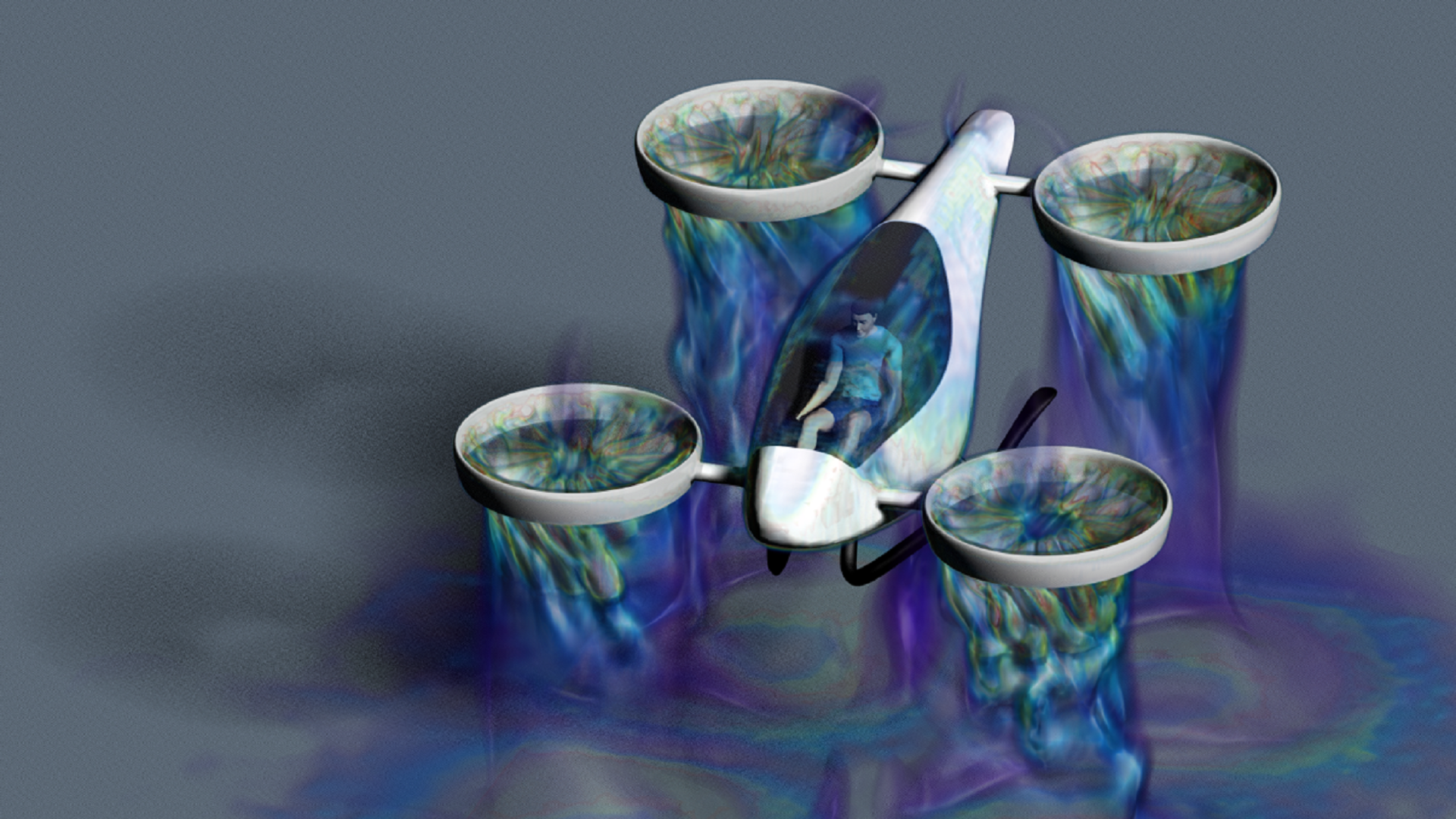
Last week I was fortunate enough to attend the annual AIAA SciTech technical conference which is normally held in Orlando, but this year it was virtual. I was struck by the number of attendees and papers given the unique format. There were more than 4,300 attendees and more than 2,100 papers at the conference.
In many ways, this conference continues to highlight the pace of innovation in the aerospace industry. I was struck by the number of papers on simulation related to urban air mobility (UAM), eVTOL/VTOL vehicles and drone development.
My appearance on the Siemens A&D podcast series Talking Aerospace Today perfectly coincides with the progress simulation is making in these new and emerging areas. In our current episode “eVTOL Aerodynamic Design through Digitalization” I talk about how the digital transformation through simulation is moving the industry forward.
… Listen to the podcast now!
The relationship between simulation and the development of UAM vehicles
It’s no surprise really that simulation and the development of novel vehicles for urban air mobility (UAM) are tightly coupled. Many of the new UAM vehicle designs do not follow traditional aircraft processes. If you look at the vehicle designs from Volocopter for example, with more than 18 rotors for VTOL and forward flight, or the work by Joby Aviation with their VTOL to cruise – it’s clear that innovation is tied to complexity.
What’s unique about these two examples is the fact that there is no existing analogue that can be used as a starting point for design. The only way to develop these new aircraft is to leverage highly digitalized technologies like simulation to quickly evaluate novel design concepts in advance of physical prototyping.
Simulation – the great equalizer
What I’d like to convey most in this blog is how simulation has leveled the playing field for small companies to compete with larger, more established integrators. And exactly how is that happening? Well, there are two reasons. First, we’ve seen an improvement in the usability accuracy of simulation codes so that the types of engineering questions that can be addressed with simulation has expanded dramatically. And second, when coupled with cloud computational resources, simulation has opened up a new strategy for design where small companies can evaluate and characterize revolutionary designed aircraft at a fraction of the cost of just a few years ago.
It isn’t just the small companies that are seeing the value in this approach. The Amazon Prime Air program leveraged Siemens Simcenter technology and Siemens AWS cloud computing to develop a new delivery vehicle for last-mile delivery. What’s unique about Amazon’s strategy was the fact that they could characterize their vehicle leveraging simulation early in the design process to ensure they could meet their performance goals while leveraging a digital thread to aid them as they move to production.
So far I’ve talked about high-level objectives of UAM vehicle design and the role simulation and digitalization play as a core strategy, but what are some of the critical areas where simulation is used?
Here are four ways simulation is driving innovation for UAM programs. (I touch on some of these in the podcast.)
- Propulsion system design and performance characterization
- Battery packing and cooling design
- Cabin environment and comfort
- Vertical lift and cruise performance characterization
Propulsion system design
Perhaps in no other aspect of product design has innovation come faster than in propulsion. Several designs have evolved for UAM including multirotor VTOL, ducted fans, hybrid VTOL pusher design and blown wing tiltrotor combinations. The inherent complexity of power distribution has pushed the limits of historical design architectures. Successful programs are leveraging mixed-fidelity simulation where power distribution and control systems can be modeled at the same time to ensure successful operation under typical mission conditions. Coupling the power requirements and thermal loads during operation can be achieved through system modeling for virtual prototypes.
Battery packing and cooling
eVTOL aircraft are pushing the limits of existing battery technology. The power requirements of a modern vertical takeoff aircraft are orders of magnitude larger than an electric car. Battery systems need to provide power for the entire mission profile and that means that for takeoff and landing the battery system is going to generate a tremendous amount of heat. For terrestrial vehicles, dissipating this heat through liquid cooling and airflow is a viable option as weight requirements are more flexible. However for aircraft, every kilo of additional battery weight is reduced payload and range and therefore developing lightweight battery systems with adequate cooling capacity is fundamental to aircraft programs success. Simulation provides a framework to evaluate battery architectures, cooling strategies, safety systems, and projected weights.
Leveraging high fidelity multi-physics simulation allows integrators to evaluate hundreds of battery designs to the final physical prototype. Volocopter recently presented their work on novel battery cooling strategies for their current generation aircraft. They showed that lightweight phase-change materials can be used for cooling while maintaining or achieving lightweighting goals.
Cabin design
Most UAM vehicles in development today have between one and six passengers. Keeping those passengers safe and comfortable is the number one objective of cabin design. Simulation technology is being used to evaluate everything from acoustic signatures, thermal comfort and seat safety. Small aircraft are subject to atmospheric conditions like gusts which can sometimes lead to rapid movements. This may be perceived by some as exciting and for others terrifying which is why building the cabin environment to mitigate the effects of rapid maneuvers while ensuring safe transportation of passengers requires detailed analysis to achieve optimal design.
VTOL and cruise
Aerodynamic design of vehicles that operate both in VTOL and cruise flight can be a daunting task. While the requirements of thrust to achieve vertical flight are well understood for traditional rotorcraft design it is less understood for hybrid vehicles that operate in both flight regimes. Understanding rotor design, wake interaction and drag reduction for forward flight are difficult and often conflicting objectives. Fortunately, recent improvements to simulation accuracy and speed allow aerodynamicists to quickly evaluate multiple design candidates en route to the final design. This coupled with modern design space exploration strategies allows small engineering teams to evaluate large design spaces and identify better performing designs earlier in the process. It also allows engineering teams to characterize virtual prototypes and develop control systems that can be verified more quickly with physical testing.
Conclusion
Simulation has been an enabler for a number of markets, not just aerospace and defense, but in no other industry has innovation been so closely tied to this technology. Using simulation to tackle previously unsolved engineering problems often encountered in developing novel aircraft is fundamental to success. Siemens Simcenter along with the Xcelerator portfolio has been singularly focused on providing a framework of simulation and test tools to enable engineering groups to move projects forward faster with more confidence.
No question, urban air mobility will continue to be at the forefront of innovation for aircraft developers.
For more on simulation and UAM vehicles, I urge you to listen to my podcast now.
Durrell Rittenberg is the Industry Segment Lead for Aerospace and Defense for STAR-CCM+ and the Simcenter portfolio. Over the past 19 years, Durrell has helped engineering organizations leverage CFD and other computational methods to drive innovation in their design process. Over his career, Durrell has worked on critical aerospace and defense programs including projects with NASA, ONERA, Boeing, DLR and Lockheed Martin. He is currently a senior member of AIAA and a member of the Inlets, Nozzles, and Propulsion Systems Integration Technical Committee as well as a member of the CFD 2030 integration committee. Before joining Siemens PLM, Durrell was the Vice President of Product Management for Tecplot, Inc. in Bellevue, Washington, where he led the development numerical simulation analysis tools used by 50,000 users worldwide.